The NFPA inspection requirements for fire pumps in commercial sprinklers
In the first two installments of QRFS’ series on the inspection of commercial fire sprinklers, we detailed the National Fire Protection Association (NFPA) requirements for the annual visual inspection of sprinkler heads, pipe, and fittings:
What Facility Managers Need to Inspect on a Fire Sprinkler System, Part 1
What Facility Managers Need to Inspect on a Fire Sprinkler System, Part 2
NFPA 25: Standard for the Inspection, Testing, and Maintenance of Water-Based Fire Protection Systems lists a number of other check-ups, some of which depend on the type of fire protection system and its components. In this piece, we go over the inspection schedule required for commercial fire sprinklers that use onsite fire pumps to pressurize water in the system.
Are you just looking for components for a fire sprinkler system? Check out our inventory of cover plates, escutcheons, fire sprinkler heads, and other components and tools, or just use the search bar to find what you’re looking for.
Fire pumps have complex inspection requirements
Many sprinkler systems require onsite fire pumps to ensure that the water pressure is adequate for the building’s needs. These often include:
- Any building that relies on a (non-gravity) water storage tank for the fire protection system’s water supply or uses a municipal supply with insufficient pressure.
- High-rise buildings: Fighting gravity to deliver adequate water pressure to upper floors requires the aid of a pump.
- Large industrial spaces and storage warehouses: The sheer size of these facilities plus the lack of separated interior rooms place a lot of pressure demand on a fire sprinkler system. In addition, many of these spaces have special fire protection systems that are different than run-of-the-mill sprinklers.
Fire pumps “and their associated equipment” can “cost from $20,000 to more than $1,000,000 when suction tanks are required.” And since they are complex pieces of machinery that are vital to the operation of these systems, they have varied and highly detailed inspection requirements.
Fire pumps are powered by a diesel, electric, or steam turbine engine, and each variety has different needs. Their installation specifications are covered in NFPA 20, Standard for the Installation of Stationary Pumps for Fire Protection, whereas inspection details are found in NFPA 25.
Given the intricacy of this equipment, there are generally two major categories of commercial inspection:
- Weekly inspections that can be completed by onsite facility personnel for the sake of convenience;
- and more complex monthly, quarterly, semiannual, annual, or biennial inspections – often coupled with testing and maintenance – that are done by a fire safety professional.
NFPA “does not mandate that a specific inspection form must be used” for weekly inspections, but says that “it is important to document that each item required to be inspected has been addressed at the proper frequency.” The organization also explicitly states that inspection should be done according to the fire pump manufacturer’s specifications, but provides an alternative schedule as well.
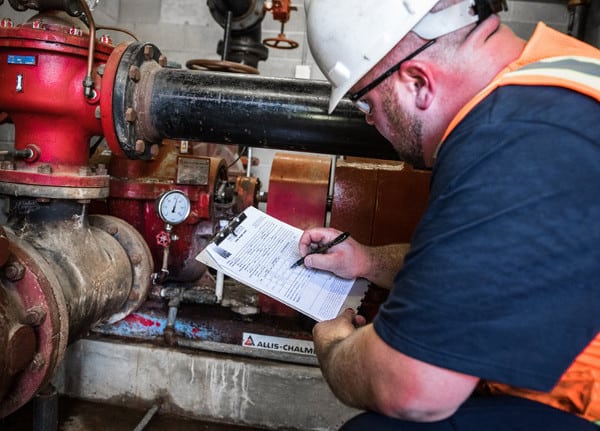
Weekly NFPA fire pump inspections
From the 2017 Edition of NFPA 25
8.2.2* The pertinent visual observations specified in the following checklists shall be performed weekly:
Weekly inspection of pump house conditions
NFPA first outlines what should be checked out in the space where the fire pump is located:
(1) Pump house conditions are determined as follows:
(a) Heat is adequate, not less than 40°F (4.0°C) for pump room with electric motor or diesel engine–driven pumps with engine heaters.
(b) Heat is adequate, not less than 70°F (21°C) for pump room with diesel engine–driven pumps without engine heaters.
These guidelines are intended to keep water from freezing in the pipes that safeguard the pump room. In addition, the higher temperature needs of diesel engines reflect the fact that cold temperatures can specifically impact their performance.
Diesel and electric engines are also affected by very high temperatures; diesel engines “are derated 1 percent for each 10°F (5.6°C) above 77°F (25°C) ambient temperature.” And many “controllers [in electric engines] have maximum operating temperatures of 104°F (40°C),” while this limit is “122°F (50°C)” in others. Thus, on a weekly basis, use the Goldilocks Rule to make sure that pump houses are climate controlled: not too cold and not too hot.
(c) Ventilating louvers are free to operate.
Diesel pumps require adequate air ventilation, and louvers help “maintain fresh air for proper diesel system combustion and room air temperature control.” Check to make sure the louvers are not broken, blocked, frozen, or otherwise out of operation.
(d) Excessive water does not collect on the floor.
(e) Coupling guard is in place.
Water could, of course, be a sign of a leak that needs to be corrected. And while commercial pumps typically sit pretty high off of the floor, deep standing water can interfere with the pump’s operation.
A coupling guard is a removable cover that protects people from the engine’s moving components, and the components from objects that could damage them. Make sure it’s good to go.
Weekly inspection of pump system conditions
From the 2017 Edition of NFPA 25
(2) Pump system conditions are determined as follows:
(a) Pump suction and discharge and bypass valves are fully open
A suction control valve is “used to prevent the fire pump from outdrawing the available [water] supply,” a discharge relief valve guards against pressure surges, and a bypass valve makes sure that the fire sprinklers have access to the onsite water supply if the pump isn’t functioning. NFPA says that all “valves directly associated with the fire pump (i.e., in the pump room) must be part of the weekly visual inspection,” and in these three cases, they must be in the open position.
(b) Piping is free of leaks.
NFPA states that “Piping leaks in suction and discharge piping, most frequently found at flanges or couplings … can be considered impairments or can lead to impaired systems, depending on the severity of the leak.” This video shows a leaking fire pump, plus what it looks like when the coupling guard is not in place:
(c) Suction line pressure gauge reading is within acceptable range.
Calculating the acceptable range on a suction line pressure gauge may a little tricky. NFPA specifies the following:
Where the water supply is taken from a tank, the gauge should be positive at a pressure approximately equal to the water height in the tank multiplied by 0.433 psi/ft. As an example, a pump attached to a tank that has 20 ft (6.1 m) of water above the point of the pipe connection should have approximately 8.5 psi (0.6 bar) on the suction gauge [0.433 psi/ft 3 20 ft 5 8.7 psi (0.6 bar)].
Where the supply is from a public source, the gauge should equal the public water supply pressure, adjusted for elevation changes.
A prudent step is to get the appropriate pressure range from a life safety professional and the manufacturer’s instructions, followed by verifying the gauge reading is appropriate every week.
(d) System line pressure gauge reading is within acceptable range.
When the pump is not running, this reading “should be the same as the suction pressure gauge.” (see above)
(e) Suction reservoir has the required water level.
If the system utilizes a tank, the water level of the supply the pump draws from is checked via an altitude float – whereas the water supplied from an underground well or reservoir involves reading a gauge. Consult the manufacturer’s instructions and/or the life safety professional who installed the system for specifics.
(f) Wet pit suction screens are unobstructed and in place.
Screens guard against debris that can enter the system from the water reservoir:
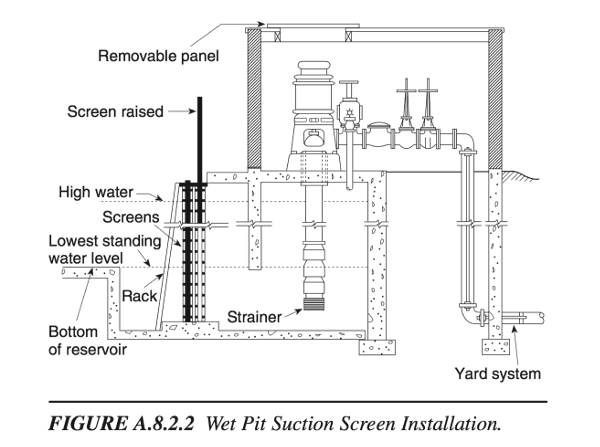
You must make sure:
- There is a trash rack; this is simply another name for the “primary” screen that blocks and collects debris while allowing water to flow freely.
- There are two sets of screens.
- And that the pump suction strainer is at the bottom of the submerged pump assembly. This is a “secondary” screen; to view its approximate placement, look at the diagram shown above (“strainer”).
Screens are necessary to protect the pump from objects that can impair the machinery or collect in and block system pipes.
(g) Waterflow test valves are in the closed position, the hose connection valve is closed, and the line to test valves is free of water.
Waterflow test valves, as the name specifies, are used to test the waterflow of the system. They should always be closed unless being used for this purpose. An open or even a leaking valve will/may cause the pump to activate. Further, water must be fully drained to protect valves and the pipes that feed them from freeze damage, if that is a possibility. The presence of leftover water mixed with air also causes corrosion in metallic components.
Weekly inspection of the electrical system and pump components
Electrical pumps have specific inspection needs; if you have a diesel pump, the actions specifically related to it in the section after this one apply. This video provides a good run-through of electrical pump components and the pump’s basic operation:
From the 2017 Edition of NFPA 25
3) Electrical system conditions are determined as follows:
(a) Controller pilot light (power on) is illuminated.
(b) Transfer switch normal pilot light is illuminated.
A transfer switch enables switching between alternate sources of power, such as between the municipal grid and a backup generator. It is only present on electric pumps that have this specific set-up. (c) Isolating switch is closed — standby (emergency) source.
An isolator switch “is used to ensure that an electrical circuit is completely de-energized for service or maintenance.” NFPA states that “isolation switches on each source of power to an electric motor drive must be closed when the pump is in the operating or standby condition.”
(d) Reverse phase alarm pilot light is off, or normal phase rotation pilot light is on.
Many pumps have multi-phase electric motors; if the “phase sequence” is set up incorrectly, the pump can run in the wrong direction. Proper installation means that this is unlikely to be a problem, so the “reverse phase alarm pilot light” should be off at all times, while a normal phase light should be lit.
(e) Oil level in vertical motor sight glass is within acceptable range.
(f) Power to pressure maintenance (jockey) pump is provided.
Make sure the maintenance pump (also known as a jockey pump) has a working power supply and check the manufacturer’s instructions to verify the correct oil level. This video illustrates how to shut off a main pump and then turn it back on after using a jockey pump for maintenance testing:
NFPA also instructs inspectors to evaluate and record “the general condition of the electrical components. … Potential problems that can be discovered include rodent nesting, plugged motor vents, broken parts, unlocked controller doors, and improperly labeled electrical panel boards. “If the pump room is equipped with electric heat, the thermostat should be checked to determine that it is operating in cold weather and that the temperature is set at normal room temperature. Any electric controls for ventilation should also be verified that they are fully operational.”
Weekly inspection of diesel system pump components
A specific set of weekly inspections is needed for a pump with a diesel engine:
From the 2017 Edition of NFPA 25
(4) Diesel engine system conditions are determined as follows:
(a) Fuel tank is at least two-thirds full.
The two-thirds-full rule is based on a standard calculation of demand based on the fact that tanks are “designed to hold an 8-hour supply of fuel for the diesel engine.” This rule could be adjusted in light of actual demand by your pump. Regardless of whether it is used, all fuel should be replaced at least yearly.
(b) Controller selector switch is in auto position.
Controller selector switches have auto, off, and manual positions. The “manual” setting enables manually starting the pump, and the “off” setting is one way of stopping a diesel engine.
The “auto” mode means that the pump is standing by and ready to engage when an emergency (activated by a drop in air or water pressure in the sprinkler system) calls for pressurized water. Auto is where you want it during an inspection.
(c) Batteries’ (2) voltage readings are within acceptable range.
(d) Batteries’ (2) charging current readings are within acceptable range.
(e) Batteries’ (2) pilot lights are on or battery failure (2) pilot lights are off.
(f) All alarm pilot lights are off.
(g) Engine running time meter is reading.
(h) Oil level in right angle gear drive is within acceptable range.
(i) Crankcase oil level is within acceptable range.
(j) Cooling water level is within acceptable range.
(l) Battery terminals are free from corrosion.
(m) Water-jacket heater is operating.
Water-jacket heaters heat water around an engine to keep it warm so it starts quickly, uses less fuel, and suffers less wear and tear. A running time meter enables you to track the life of the engine and perform maintenance at needed intervals. If you see a lit alarm pilot light, you know you have a problem. And all “acceptable ranges” for batteries and oil levels should be gleaned from the manufacturer’s instructions. This video from FM Global provides a brief run-through of the manual start of a diesel fire pump:
Weekly inspection of steam system pump components
They’re pretty rare these days, but steam turbine fire pumps are still around. They work when heated water is converted into high-pressure steam which rotates “the blades of a turbine to create mechanical or rotational energy.” NFPA 25 guidance on weekly inspection is pretty simple:
From the 2017 Edition of NFPA 25
(5) *Steam system conditions: Steam pressure gauge reading is within acceptable range
What about inspections at longer intervals than a week?
NFPA 25 outlines a host of inspections that must be done monthly, quarterly, semiannually, yearly, and biennially. Many of these checks line up with additional maintenance and testing requirements. Because of this complexity and the potential for dedicated testing and maintenance, a life safety professional is typically utilized for these inspections.
Again, NFPA explicitly instructs individuals who are responsible for inspection, testing, and maintenance of a fire pump to consult the manufacturer’s specific instructions. But the organization also provides a useful backup schedule; to see the complete, massive list of all inspection, testing, and maintenance requirements specified by NFPA, click on the preview image of the table below:
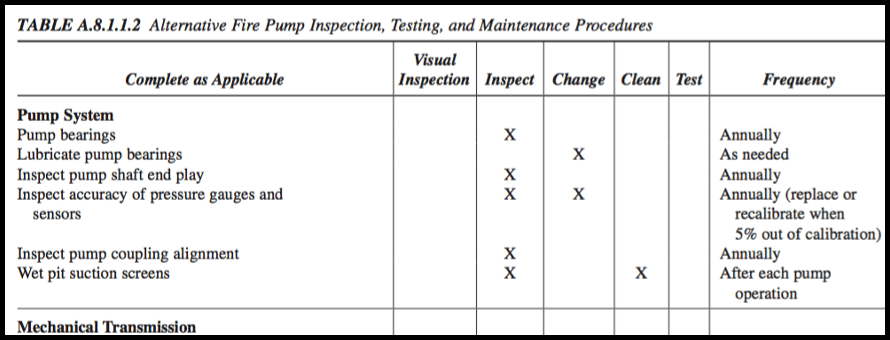
To be continued: What Facility Managers Need to Inspect on a Fire Sprinkler System
This concludes part three of QRFS’ series on the inspection of commercial fire sprinkler systems – but we’re not done yet. In the next and final installment of this series, we cover the inspection of waterflow alarms, signage, and other components.
If you need to buy items for a commercial fire sprinkler system, review our escutcheons, cover plates, commercial fire sprinkler heads, and other components and tools, or just use the search function at the top of the page.
If you have any questions regarding commercial fire sprinklers or need help finding something, give us a call at 888.361.6662, comment below, or fill out our contact form.
Nice Post! You have well explained NFPA inspection requirements for fire pumps in commercial sprinklers. Thanks for sharing.
I like how you mentioned that buildings rely on water storage tanks or a municipal supply with enough pressure. My cousin is thinking about constructing a facility for shoe companies to work out of and would need commercial facilities protection. It seems like a good investment to get a proper sprinkler system that can deploy water fast to put out fires.
Jesse, thanks for sharing! We definitely agree that a proper sprinkler system is a good investment! Make sure to check with your authority having jurisdiction (AHJ); if the facility is large enough and falls into a certain occupancy type, it may require automatic sprinkler protection by law.
In your video above that shows how to turn off the fire pump controller during “maintenance testing” the gentleman in the video states that he turns the fire pump off while testing the waterflow switches. Doesn’t that go against NFPA 25 4.4 stating that during inspection, testing, and maintenance, water supplies, INCLUDING FIRE PUMPS, shall remain in service unless under constant attendance by qualified personnel or unless impairment procedures in Chapter 15 are followed?
John — Since the video above presented by Sprinklermatic Fire Protection Systems is 25 minutes long and we would need to evaluate the context of what he is saying, would you please advise of the time-stamp? Thanks.
very useful topic as always, thanks a lot!