The biggest threat to fire sprinklers’ performance: the people they protect
More than 90 percent of the time, automatic fire sprinklers operate as expected when an emergency breaks out—controlling or extinguishing flames before they have devastating consequences. But when a fire sprinkler failure happens, human error is almost always the root of the problem.
In the first installment of our series on the most common mistakes that cause fire sprinkler failure, we examined simple-but-serious errors that involve shutting off the system or manually interfering with its operation. In this blog, we will shine a light on other frequent mistakes, including failing to perform simple maintenance and more complicated errors, like installing systems that can’t control the intensity of fires generated by a property’s hazards.
Looking to buy fire protection equipment? Feel free to browse our selection of fire sprinklers and accessories, including residential sprinkler heads, installation tools, shut-off tools that quickly stop triggered sprinkler heads, head guards that protect sprinklers from accidental damage or vandalism, and more.
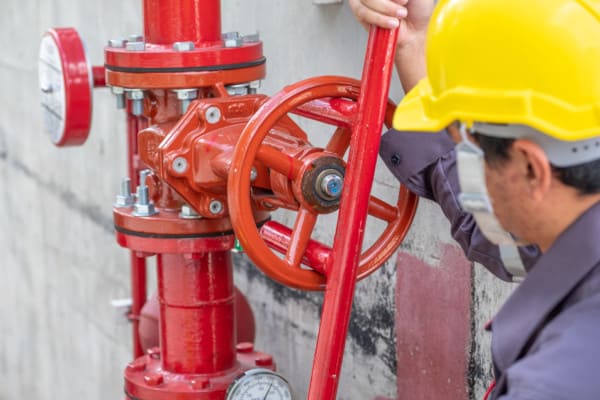
Lack of regular maintenance is a common mistake that causes fire sprinkler failure
A fire ravaged a Georgia textile recycling plant in 2007, killing one person and causing $7.5 million in damage. This happened even though a fire sprinkler system was installed and more than 75 sprinklers operated in an attempt to control the blaze. So, what went wrong?
According to the Society of Fire Protection Engineers (SFPE), a lack of maintenance triggered the tragedy. The plant’s sprinkler system had been neglected for years, with maintenance deficiencies including partially closed valves that restricted water flow, sprinkler risers modified to allow the use of garden hoses, and improper sprinkler clearances. With so many issues, the system was easily overwhelmed by the fire.
A properly functioning fire sprinkler system can be all that stands between the people and property you want to protect and an out-of-control blaze. Even just a few minutes of delay before sprinklers kick in can lead to devastating consequences.
Following the rules specified in NFPA 25: Standard for the Inspection, Testing, and Maintenance of Water-Based Fire Protection Systems is key to keeping sprinkler components in tip-top shape and catching problems before they lead to system failures. Known as the “wear and tear” document, NFPA 25 details minimum requirements for all inspection, testing, and maintenance (ITM) of fire sprinklers and other water-based systems. It also outlines the process that needs to be followed when problems are found, including proper fixes and reporting.
Fire sprinkler systems can suffer any number of service issues, including closed valves, worn-out parts, corroded pipes, and obstructions to the water supply. Most of these problems can be easily avoided or fixed. But without an ITM schedule, property owners are unlikely to realize they’re occurring until—like that Georgia recycling plant—it’s much too late.
Corrosion, for instance, is a serious concern in any sprinkler system that combines oxygen, water, and metal. More than 70 percent of studied dry sprinkler systems suffered significant corrosion issues within 12.5 years of installation, according to a Potter Corrosion Solutions report. Wet systems corrode slower, but they don’t escape unscathed: 35 percent experience significant issues after 25 years.
Corrosion quietly rots metal pipes from the inside out, making it nearly impossible to detect until the problem is so severe that the system suffers leaks, obstructions, or accidental sprinkler discharges. Regular inspection of sprinkler pipes helps catch corrosion at its earliest stages, while maintenance activities like system flushing mitigate damage, using a pressurized water source to remove potential blockages.
To learn more about mitigating corrosion in sprinkler pipes, check out our previous blog: “My Sprinkler Pipes are Corroded. Now What?”
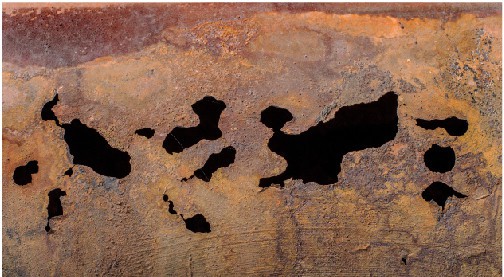
Corrosion is just one example of many things that need to be spotted early. Even far-less-difficult issues, like someone placing storage in a spot that blocks sprinklers’ spray patterns, can have serious consequences—ones that could be easily avoided by doing the annual visual inspection of sprinkler heads required by NFPA 25.
Documenting and exploring the root causes of any issues that are discovered while inspecting, testing, or maintaining sprinklers is key to reliable system performance. NFPA 25 categorizes components that aren’t up to code into three categories to help property owners prioritize repairs: impairments, critical deficiencies, and noncritical deficiencies.
Noncritical deficiencies don’t impact system performance but must be corrected to meet NFPA standards within a reasonable amount of time (2023 edition: 3.3.8.2). Critical deficiencies can have a “material impact” on system performance and should be corrected as soon as possible (3.3.8.1).
Impairments are the most serious, meaning all or part of the system is out of order and won’t function properly until it’s repaired (3.3.23). Impairments, which can be “preplanned” or “emergency,” are the highest priority and must be addressed immediately (emergency) or as soon as practicable and on schedule (preplanned).
NFPA 25 requires property owners to maintain careful records of ITM activities performed on their fire sprinkler systems (4.3). These documents must be kept for at least “1 year after the next inspection, test, or maintenance of that type required by the standard” is done, so deteriorating performance is easy to spot by comparing results (4.3.5).
From the 2023 edition of NFPA 25
4.3.2 Records shall indicate the following:
(1) The procedure/activity performed (e.g., inspection, test, or maintenance)
(2) The organization that performed the activity
(3) The required frequency of the activity
(4) The results and date of the activity
(5) The name and contact information of the qualified contractor or owner, including the qualified personnel performing the activity
How diligently these records are kept speaks volumes about the property owner or facility manager’s investment in maintaining fire protection. Missing, incomplete, or outdated records can make some testing or preventive maintenance virtually impossible—and increase the likelihood of system failures. Without consistent documentation, it may be impossible to know when gauges were last calibrated or changed, for example, if the fire pump is being run at regular intervals, or whether any past deficiency was ever corrected.
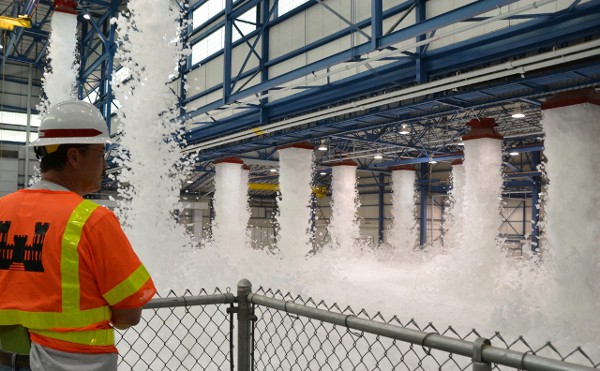
Choosing an inappropriate system for a property’s hazards offers inadequate protection from fire
One of the most important decisions in designing a sprinkler system is determining your property’s occupancy classification. NFPA 13 defines occupancy classifications based on usage and the type of materials a building contains, which impacts how hot fires will burn and how quickly they will spread. For example, fires develop slowly with lower levels of heat in light-hazard properties such as schools or offices but spread quickly and burn extremely hot in extra-hazard environments like steel manufacturing plants and textile factories.
A property’s occupancy classification determines the type and number of sprinklers it needs, and their orientation, water-discharge characteristics, and spacing within a building. Get these and other elements wrong and fire sprinklers may not be effective because the amount of water they provide (how fast and where) is no match for the hazard.
Hidden factors can influence a property’s classification, such as storing new products that can be explosive or burn quickly during a fire. It’s critical to enlist the help of a fire protection professional when determining the hazard level so such factors are discovered during a routine survey instead of an emergency event. When more than one occupancy hazard classification exists in a building, the most hazardous level should apply to the entire structure.
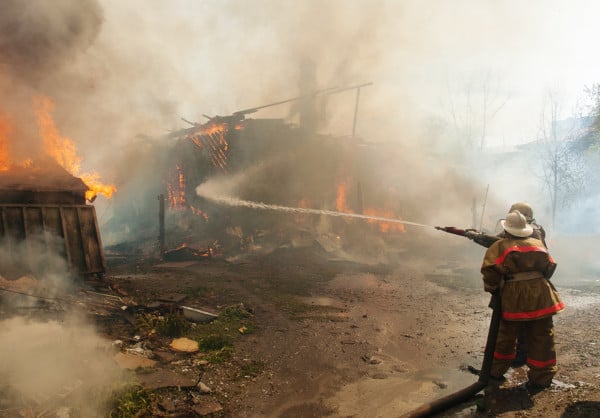
Now read this carefully: A sprinkler system’s effectiveness during a fire is limited by the design criteria of the original installation. Occupancy classification must be revisited any time the use of a building or space within it changes significantly to ensure the sprinkler system still provides sufficient protection.
A common mistake property owners make is failing to re-evaluate and make necessary modifications to sprinklers after modifications are made to a property’s space or use, even if they seem minor. For instance, if major renovations are completed without redesigning the sprinkler system layout, coverage is almost always inadequate. Even something as simple as a tenant change from a traditional office to a doctor’s office can change hazard levels and require different coverage.
Understanding the original system design and how a building has evolved over time is key to avoiding fire sprinkler failure. Annually reviewing a property’s occupancy classification is wise to ensure the system remains appropriate for the hazards and use of the building, as it ensures adequately protecting people and property from fires.
Minor mistakes can have a major impact on the fire sprinkler failure vs reliability
People pose the biggest threat to the effectiveness of fire sprinklers. Thus, understanding the biggest human errors that compromise these systems and cause fire sprinkler failure is your overwhelmingly best bet to ensure they work as intended.
Make sure to read part one of this series to round out your knowledge of common mistakes that cause fire sprinkler failure.
In the market for fire protection? Feel free to browse our selection of fire sprinklers and accessories, including residential sprinkler heads, installation tools, shut-off tools that quickly stop triggered sprinkler heads, head guards that protect sprinklers from accidental damage or vandalism, and more.
Questions about QRFS products or need a brand or item that’s not online? Just call us at +1 (888) 361-6662 or email support@qrfs.com.
This blog was originally posted at blog.qrfs.com. Check us out at Facebook.com/QuickResponseFireSupply or on Twitter @QuickResponseFS.