Proper inspection, maintenance, and disposal of fire extinguishers can prevent potentially dangerous malfunctions
Some fire extinguishers wind up as inoperative duds, and a few of them can even become dangerous explosives—but what causes these problems with fire extinguishers? Will a unit that’s been in service for years do what it’s designed to do (safely)? A few recent incidents suggest that some worries are well-founded:
- The United States Consumer Product Safety Commission recalled a popular fire extinguisher after nearly 400 reports of “failed or limited activation.” A car accident in Pennsylvania proved fatal after one such extinguisher—used by first responders—failed to activate.
- A Mississippi man was killed when an “antique” fire extinguisher exploded as he unloaded it from a trailer. The base flew off and hit him in the face, causing blunt force trauma to his head.
Stories like these illustrate the need to identify and resolve problems with fire extinguishers before it’s too late. In this article, we show how attention to detail, regular inspections, removing very old models from service, and scheduled maintenance can help users stop potentially dangerous malfunctions.
If you need new fire extinguishers, check out our selection of ABC dry chemical and CO2 extinguishers in various sizes. Cabinets and covers can also help protect your investment in harsh environments.
Without immediate recharging and service, partial use can clog hoses or damage critical components
The National Fire Protection Association (NFPA) specifies that any time a fire extinguisher discharges—even for a short burst—it should be serviced or replaced. This maxim and other vital guidance are found in NFPA 10: Standard for Portable Fire Extinguishers:
From the 2022 edition of NFPA 10
7.8.1.1 All rechargeable-type fire extinguishers shall be recharged after any use or when the need is indicated by an inspection or servicing.
The gauge may still show that the extinguisher has enough pressure—but that doesn’t rule out the need for maintenance or replacement. Over time, extinguishers that have activated may continue to lose pressure. In addition, a build-up of the extinguishing agent inside hoses, gaskets, springs, and O-rings may prevent the extinguisher from working properly the next time it’s used.
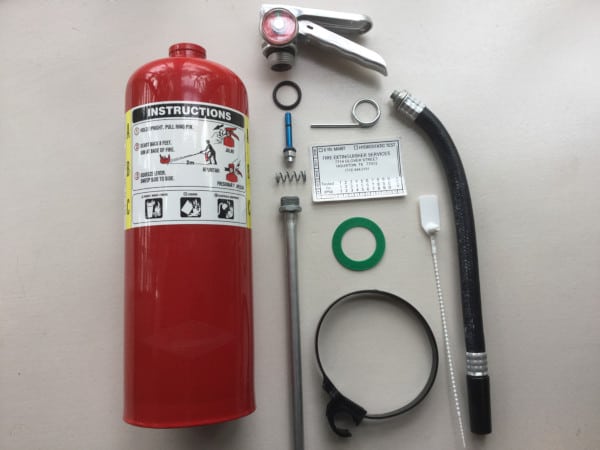
Alternately, if the fire extinguisher cannot be serviced—or if it’s not cost-effective to do so—it should be replaced. For a lot more detail on these issues, check out our article on fire extinguisher recharges.
Environmental forces and intentional acts may cause problems with extinguishers
Problems with fire extinguishers can be the result of a harsh environment. Although many extinguishers can withstand tough conditions, facility managers should read their manuals and labels to determine how best to protect these devices against the elements and other sources of wear. Some common sources of damage include:
- Low and high temperatures
- Exposure to ultraviolet rays
- Humidity, precipitation, and other forms of moisture
- Excessive vibration
Proper placement and protection can mitigate or eliminate these and other problems with fire extinguishers. That’s part of the reason why NFPA 10 requires that portable, non-wheeled extinguishers be installed properly on hangers, brackets, or “approved cabinets or wall recesses” (section 6.1.3.4). Section 6.1.3.6 adds that “approved strap-type brackets” must be used to secure fire extinguishers in vehicles or other areas where they might be dislodged.
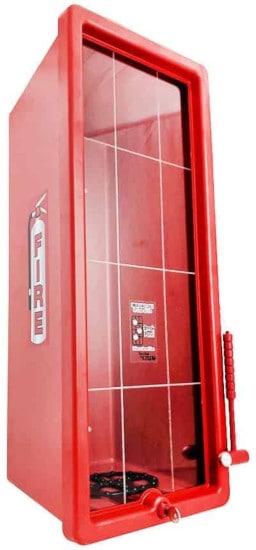
Further, sections 6.1.3.9.1, 6.1.3.9.2, and 6.1.3.9.3 of NFPA 10 guarantee that fire extinguishers aren’t placed so high that users struggle to remove them—or so low that they make contact with the floor. For more on placement requirements, see “When and Where Should Fire Extinguishers be Installed?”
Essentially, these rules ensure that it’s easy for users to remove an extinguisher from its housing. That’s a good thing: dropping an extinguisher can weaken the outer casing or damage operable parts, such as handles. In addition to accessibility issues, fire extinguishers placed on the floor may be more susceptible to corrosion. A standing extinguisher can be knocked over—and corrosion-resistant coatings may be removed if the extinguisher is inadvertently kicked or hit.
Responsible parties must ensure that extinguishers are protected in a way that doesn’t limit access in an emergency
The risk of damage, vandalism, and theft must be balanced against the need for a fire extinguisher’s availability in the event of an emergency.
From the 2022 edition of NFPA 10
6.1.3.11.1.1 Cabinets housing fire extinguishers shall not be locked, except where fire extinguishers are subject to malicious use and cabinets include a means of emergency access.
6.1.3.11.1.2 Cabinets housing fire extinguishers with break-front panels shall be provided with breaker bars or hammers, designed for accessing the extinguisher during a fire emergency.
Extinguisher cabinets provide some protection against the elements, discourage unauthorized handling, and make it more obvious when use has occurred, so that fire extinguishers can be re-inspected and serviced. Fire extinguisher covers do not provide the same degree of protection as cabinets. However, they do protect this equipment from hazards like dirt and UV light. That means that it’s easier to keep required tags and labels legible—an essential part of maintaining compliance with NFPA 10. While instructions or maintenance records aren’t, strictly speaking, a source of extinguisher failure, keeping them in order will extend the code-compliant life of a fire extinguisher.
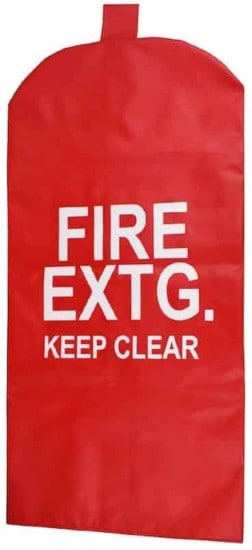
Obsolete extinguishers left in service can contribute to fire-related problems and deadly non-fire incidents
Numerous extinguisher types have no place in modern buildings, period
Fire safety technology has evolved since NFPA 10 was first adopted nearly a century ago. Many fire extinguishers that were once permitted—or even common—are no longer allowed in NFPA-compliant facilities.
From the 2022 edition of NFPA 10
4.4 Obsolete Fire Extinguishers. The following types of fire extinguishers are considered obsolete and shall be removed from service:
(1) Soda acid
(2) Chemical foam (excluding film-forming agents)
(3) Carbon tetrachloride, methyl bromide, and chlorobromomethane (CBM)
(4) Cartridge-operated water
(5) Cartridge-operated loaded stream
(6) Copper or brass shell (excluding pump tanks) joined by soft solder or rivets
(7) Carbon dioxide extinguishers with metal horns
(8) Solid charge–type AFFF extinguishers (paper cartridge)
(9) Pressurized water fire extinguishers manufactured prior to 1971
(10) Any extinguisher that needs to be inverted to operate
(11) Any extinguisher manufactured prior to 1955
(12) Any extinguishers with 4B, 6B, 8B, 12B, and 16B fire ratings
(13) Stored-pressure water extinguishers with fiberglass shells (pre-1976)4.4.1* Dry chemical stored-pressure extinguishers with an indicated manufacturing date of 1984 or prior shall be removed from service.
4.4.1.1 Subsection 4.4.1 shall not apply to wheeled-type dry chemical stored-pressure fire extinguishers.
Some of the older fire extinguisher types on this list are dangerous by modern standards. Most soda-acid fire extinguishers in the 20th century required the operator to tip them over before use, causing a potentially explosive chemical reaction. New York City banned them altogether back in 1983—following a lawsuit by an injured firefighter—and the Occupational Safety and Health Administration (OSHA) no longer allows their use in American workplaces.
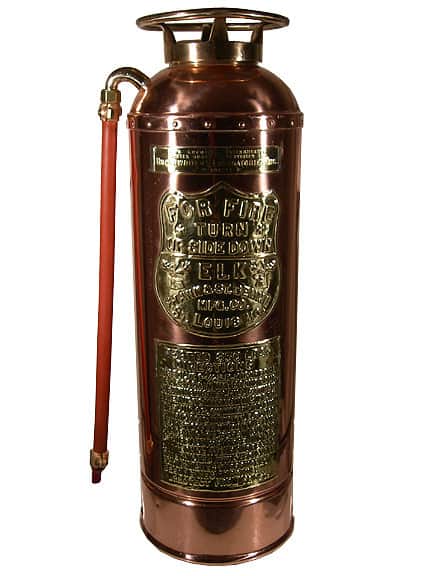
In fact, the safety organization UL (formerly known as Underwriters Laboratories) de-listed them way back in 1969, along with similar types of fire extinguishers that needed to be inverted (tipped upside down) before use. These extinguishers sometimes failed to operate in an emergency, and clogged hoses or elbows created dangerous build-ups of pressure that sometimes caused harm to users.
Note that NFPA 10 doesn’t allow facility managers to change existing extinguishers to meet these requirements. Section 7.10 stipulates that fire extinguishers should never be converted from one type to another—that is, filled with a different type of extinguishing agent—or in any way altered.
Old or unserviceable extinguishers must be removed and safely disposed of
Keeping old fire extinguishers around a facility puts occupants at risk. Along with the possibility of an explosion, somebody could attempt to use a non-working or malfunctioning extinguisher to fight a fire. The results could be catastrophic.
And these aren’t the only extinguishers that NFPA 10 won’t allow in service. In addition to the extinguishers listed in section 4.4, NFPA 10 requires the removal of:
- Non-rechargeable fire extinguishers more than 12 years old—from the date of manufacture (7.3.6.3).
- Any extinguisher that cannot be serviced in accordance with the manufacturer’s documentation. If the necessary parts or extinguishing agents aren’t available, the extinguisher must be replaced (4.4.2).
In short, some extinguishers fail due to known design flaws. There’s only one way to avoid problems with these extinguishers: remove and replace them—carefully. Placing old fire extinguishers in ordinary dumpsters or trash cans may expose sanitation workers and others to risks of exposure to toxic chemicals and/or explosive decompression.
According to a 2014 report by OSHA, a worker was killed when a fire extinguisher—improperly placed inside a dumpster—exploded during dumping operations. While disposal requirements vary by jurisdiction, every facility manager should consult with the local fire department or municipal recycling center to determine a safe and legal way to dispose of an obsolete fire extinguisher.
Problems with extinguishers may continue or worsen if responsible parties don’t conduct inspections and maintenance at recommended intervals
NFPA 10 requires regular inspections and service for all types of fire extinguishers. These procedures provide an idea of fire safety professionals’ top concerns regarding the devices’ operability and use—and allude to common problems with fire extinguishers.
Monthly inspections focus largely on basic issues like unexpected pressure loss
Whoever is responsible for maintaining the fire extinguishers—the “owner or designated agent or occupant of a property in which fire extinguishers are located,” according to NFPA 10 section 7.1.1—should inspect all fire extinguishers at least monthly, and more often when problems with fire extinguishers are found.
From the 2022 edition of NFPA 10
7.2.1.2* Fire extinguishers and Class D extinguishing agents shall be inspected either manually or by means of an electronic monitoring device/system at intervals not exceeding 31 days.
7.2.1.2.1 Fire extinguishers and Class D extinguishing agents shall be inspected at least once per calendar month.
7.2.1.3* Fire extinguishers and Class D extinguishing agents shall be manually inspected daily or weekly when conditions exist that indicate the need for more frequent inspections.
Those inspections focus largely on accessibility issues, but also include brief assessments of the extinguisher’s condition. According to NFPA 10 section 7.2.2, an extinguisher should always show a “pressure gauge reading or indicator in the operable range or position,” and appear to be full by “weighing or hefting.”
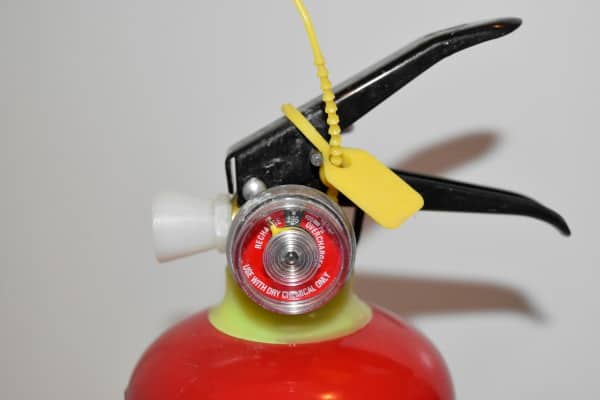
This section also requires an inspection of the hose and nozzle. For non-rechargeable fire extinguishers that only have “push-to-test” pressure indicators, those indicators should be pressed. If the extinguisher has lost pressure, the indicator will remain depressed; if it returns to its previous position, the device typically has enough pressure.
Risks to extinguishers may prompt more rigorous weekly or daily inspections focused on damage
What kind of conditions can cause more frequent and/or thorough inspections to be required?
In section 7.2.2.3, NFPA 10 lists “severe hazards,” a “high frequency” of past fires, extinguishers’ susceptibility to “mechanical injury or physical damage,” and “abnormal temperatures or corrosive atmospheres.” In addition, section A.7.2.1.3 recommends but doesn’t require more frequent inspections of extinguishers subject to leakage, tampering, or vandalism.
Those inspections focus on the issues listed in the previous section—including checks of pressure and hose conditions. In addition, inspectors verify the integrity of safety seals, tamper indicators, and the extinguisher itself, looking for “obvious physical damage, corrosion, leakage, or [a] clogged nozzle” (section 7.2.2.4).
Annual inspections include a look at long-term contributors to extinguisher failure, and may include professional testing
NFPA 10 offers guidelines for a more comprehensive annual examination in section 7.3.2, beginning with a look at an extinguisher’s overall condition.
From the 2022 edition of NFPA 10
7.3.2.1 Physical Condition. An annual external visual examination of all fire extinguishers shall be made to detect obvious physical damage, corrosion, or nozzle blockage to verify that the operating instructions are present, legible, and facing forward, and that the HMIS information is present and legible, and to determine if a 6-year interval examination or hydrostatic test is due.
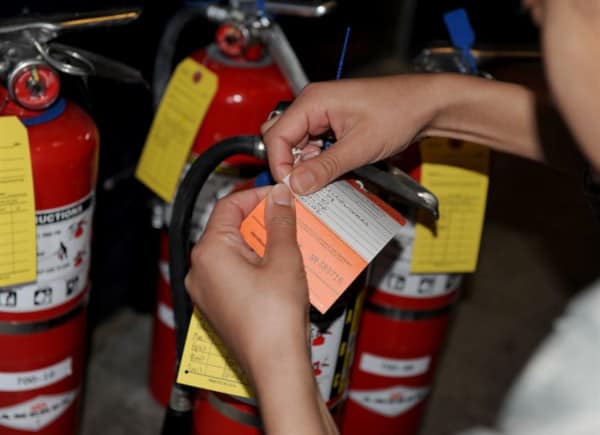
During this examination, the “pull pin or locking device” on a rechargeable fire extinguisher should be operated to ensure that it would work if needed (section 7.3.2.2). Note that the fire extinguisher is not discharged; only the locking device is tested. This requires removing the tamper seal, so a new tamper seal must be installed after this test (7.3.2.2.1). However, seals or tamper indicators on non-rechargeable extinguishers must be left in place (7.3.2.2.2).
Anything that can be removed from the cylinder—such as “boots, foot rings, and attachments”—must be removed, providing inspectors with a full view of the cylinder’s condition (7.3.2.3). In addition, hoses on CO2 (Carbon Dioxide) fire extinguishers must undergo a “conductivity test” (7.4). These devices can generate static electricity as gas passes through the hose and nozzle, causing an electrical surge powerful enough to create a debilitating shock. Extinguishers that pass this test will safely discharge static buildup in the hose assembly; if not, that assembly must be replaced (7.4.1).
All of these checks are critical because a fire extinguisher is a pressurized device. Age and exposure to temperature, moisture, dust, dirt, and UV rays can make seals, gaskets, and hoses brittle as well as eventually make metal corrode or rust. Under pressure, those damaged components may burst or leak, putting the user at risk.
While CO2 and halon gas extinguishers don’t promote corrosion, most fire extinguishers contain chemicals and/or water-based agents which can be caustic and damage metal if the protective coating or paint on an extinguisher wears off. Extinguishers in an office or retail environment may look “new” for years—even as these forces silently cause them to go bad.
Acting on inspections with subsequent maintenance can prevent or rectify problems with extinguishers
Only trained professionals should maintain or recharge extinguishers
Many of the inspection steps we’ve described so far can be performed by in-house personnel with no certification (although many companies contract out the more involved parts of the annual inspections). However, maintenance involving work on the pressurized internal parts of a fire extinguisher is a different story.
Section 7.1.2.1 of the 2022 edition of NFPA 10 stipulates that “persons performing maintenance and recharging of extinguishers shall be certified,” and the following maintenance steps should only be performed by certified professionals. Training and/or certification by an organization recognized by the local authority having jurisdiction (AHJ) is required. Although some large organizations may train in-house staff to the satisfaction of the AHJ, most facilities leave these tasks to professionals specializing in fire equipment.
Significant health, safety, and environmental risks can result if untrained personnel attempt to work on the pressurized internal components of a fire extinguisher. Mistakes are all too easy to make—even for professionals. For example, an employee of a fire protection company was severely injured in 2001 when a regulator (a device used to control the flow of pressurized gas into a cylinder) failed during an extinguisher recharge. As a result, “a pressure of 2500 lbs. of nitrogen was instantly put into the fire extinguisher,” according to an accident report from OSHA. The extinguisher, which “was designed for only 150 lbs of propellant pressure,” exploded.
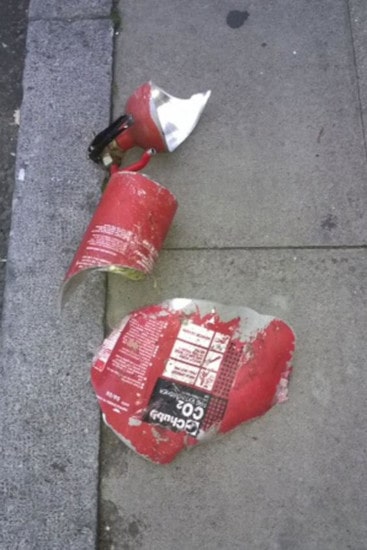
Each extinguisher type requires a slightly different form of maintenance
The exact steps performed during fire extinguisher maintenance vary depending on the type of fire extinguisher. In table 7.3.3.1, NFPA 10 provides maintenance intervals for wet-chemical, dry-chemical, CO2, and other extinguisher types:
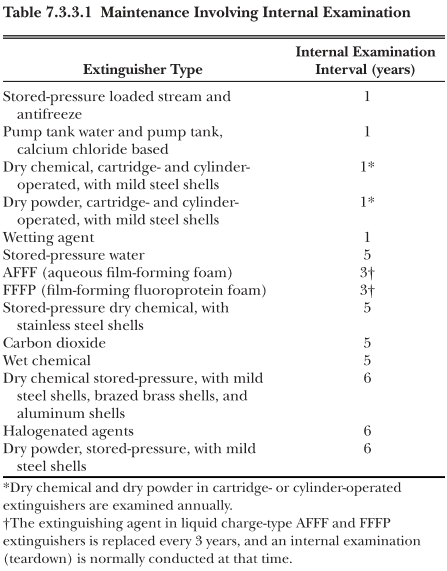
Some water-based fire extinguishers must be serviced very frequently—at one-year intervals—while carbon dioxide extinguishers can go up to five years. Dry chemical extinguishers, one of the most common types, can go up to six years before servicing.
During these internal examinations, the certified maintenance professional discharges the extinguisher and collects the fire extinguishing agent. The internal components, such as the valve and the discharge head, are cleaned and checked. Internal rubber components are replaced. While the valve head is off, sections 7.8.4.8.2, 7.11.4.1, 7.11.4.2, and 7.11.4.3 of NFPA 10 stipulate that a “verification-of-service collar” shall be placed around the neck of the fire extinguisher, where applicable.
This video shows a trained professional servicing a couple of common fire extinguisher types:
Afterward, the extinguisher is then reassembled, refilled, re-pressurized, and tested for leaks. The pull pin, tamper-evident seal, and all required labels and tags are placed on the extinguisher, leaving it ready for use.
Hydrostatic tests can determine when an extinguisher’s canister needs to be retired
Fire extinguishers must also be hydrostatically tested in accordance with chapter 8 of NFPA 10. This additional test is performed during the service procedures described above. The canister of the fire extinguisher is cleaned out and visually inspected—inside and out—for corrosion and damage. It is then filled with water and pressurized to the manufacturer’s test pressure, which is significantly higher than the normal operating pressure of the extinguisher. If the cylinder withstands this pressure without leaking or deforming, the extinguisher should be able to safely hold a supply of pressurized extinguishing agent.
Table 8.3.1 from NFPA 10, shown below, provides hydrostatic test intervals for various fire extinguisher types. For a CO2 extinguisher, it’s the same interval required for other servicing: 5 years. As such, it may be convenient to have normal maintenance and hydrostatic testing done at the same time. For most dry chemical ABC extinguishers, the 12-year interval is double that of the 6-year service requirement, so it should be tested during every other internal examination and maintenance procedure.
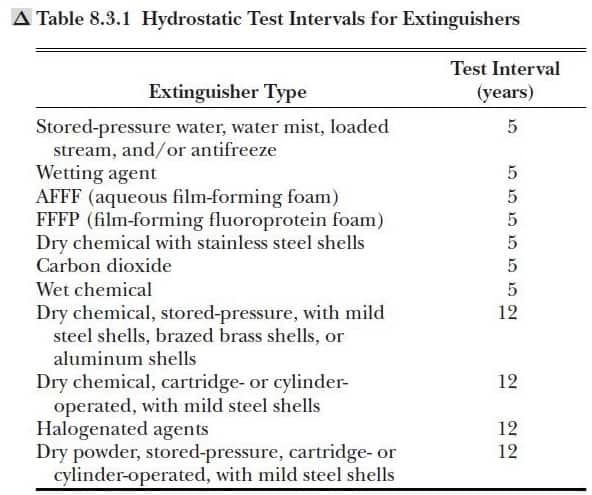
Problems with fire extinguishers can be minimized by staying on top of inspection, protection, maintenance, and replacement
Inspection of facility fire extinguishers can be a chore, but it’s imperative for maintaining the safety of workers, customers, and everyone else who works in and around a building. These inspections can be incorporated into other health and safety checks, as long as the recommended intervals are maintained.
It’s worth noting that caring for and refilling a rechargeable extinguisher may ultimately be cheaper than replacing disposable extinguishers on the timelines required by NFPA 10. However, maintenance costs for complete servicing can easily exceed replacement costs—especially for small fire extinguishers:
- Rechargeable 5 lb. Buckeye ABC fire extinguisher costs a little over $30 to replace. A low-end (and sometimes lower-quality) disposable extinguisher of the same size may cost as little as $20. If, as some surveys suggest, recharging and maintenance cost roughly $20 to $30 for small extinguishers, then consumers can buy a new extinguisher for about the price of a single recharge.
- A rechargeable 5 lb. ABC extinguisher costs just over $40—and an equivalent disposable extinguisher has a comparable price tag. Consumers may begin to see mild cost savings at this size, with maintenance ranging from $25 to $30. And as extinguishers get bigger (or have more specialized ratings and extinguishing agents), the scales tip more toward maintaining them vs. replacing them.
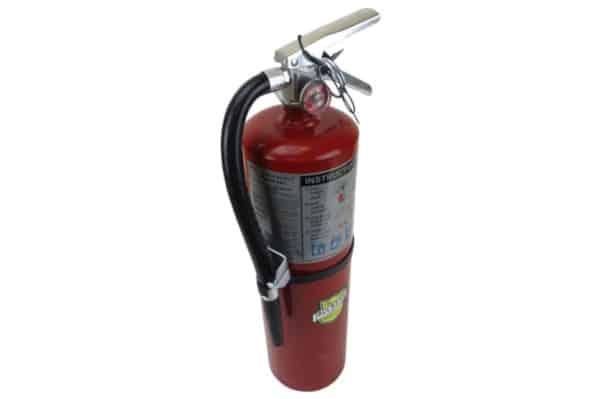
To that end, QRFS offers a wide selection of rechargeable fire extinguishers. Purchasing them in stages can help facility managers spread out expenses, with some reaching the five-year mark (CO2 extinguishers) and the six-year mark (most ABC dry chemical extinguishers) at different times.
QRFS also offers cabinets or covers to protect extinguishers when temperature, UV rays, the risk of theft and vandalism, and/or other factors require additional protection—and vehicle brackets and wall brackets to keep extinguishers in their approved places.
Browse our selection of rechargeable fire extinguishers and accessories.
For more information about our products or this article, call us at +1 (888) 361-6662 or email support@qrfs.com.
This blog was originally posted at blog.qrfs.com. Check us out at Facebook.com/QuickResponseFireSupply or on Twitter @QuickResponseFS.
A good & Informative Page for proffessionals and activist or Campaigner like me.
I shall be seeing more.
Thanks –
Thank you so much for this sharing knowledge. What happens if the fire extinguisher hose is not clamped on the fire extinguisher body?
Thank you for your comment! If the hose is not properly connected to the extinguisher, then it will not pass a fire marshall inspection (or work properly in the event of a fire!). You can attempt to attach the hose, contact the manufacturer for a replacement hose/straps/extinguisher, or can replace the extinguisher. QRFS has them in stock! https://blog.qrfs.comfire-extinguishers
I like your idea to incorporate fire extinguisher inspections with the other health and safety checks. Additionally, it’s a good idea to get detailed fire extinguisher inspection tags in order to keep an accurate record when maintenance is done. Using these tips together should be effective in preventing many causes of fire extinguisher failure.
This blog of one of the best I ever read in this arena. Thanks a lot for putting it together…
You are welcome, Mohammed. Thanks for reading!
great
Why would an extinguisher over its gross weight fail an inspection?
Brendan — We don’t have enough detail to say definitively why you (?) may have (?) failed an inspection due to this reason. However, extinguishers have placement rules based on weight. For example, this section is in the Illinois Building Code, which is based on the International Building Code:
“Hand-held portable fire extinguishers having a gross weight exceeding 40 pounds (18 kg) shall be installed so that their tops are not more than 3.5 feet (1067 mm) above the floor.”
It’s a great moment with you . I value your site.
Warm regards