Obstruction investigations are critical for uncovering blockages that can cause fire sprinklers to fail
Fire sprinklers and their network of piping have one job: to automatically deliver water when they sense the heat of a fire. They are highly effective, but an undiscovered blockage in fire sprinkler pipes can sabotage a system’s ability to distribute water, possibly leading to loss of property and life.
Although many commercial structures rely on sprinkler systems, the majority are not yet equipped with them. In its “U.S. Experience with Sprinklers” report, the National Fire Protection Association (NFPA) states that fire sprinklers were present in only 10 percent of reported structure fires between 2010 and 2014. Less than 30% of warehouses, offices, stores, or public assembly buildings were covered by sprinklers when fires broke out. The coverage rate approached and even exceeded 50%, however, in reported fires at educational, manufacturing, and care institutions such as hospitals and prisons.
When sprinkler systems are installed, NFPA asserts that they operate as intended 96% of the time, effectively extinguishing or controlling fires. Yet inspecting sprinkler pipes in commercial buildings is not always done to standards.
At a minimum, NFPA recommends that system pipes receive internal inspections every five years—so without any sign of obstruction, pipes can hide issues that may lead to failure. The complexity of large networks of pipe adds an additional hindrance, requiring a systematic approach to inspection that includes pre-tests, identification of a problem, appropriate responses, and documentation.
Conducting an investigation into a pipe obstruction is thus a proactive endeavor shaped by several factors: scheduled examination, noting when conditions merit it, and sampling different areas of the system.
In this first installment of our two-part series on fire sprinkler obstruction investigations, we describe when to investigate and some common sources of obstructions. Read part two next, where we discuss how inspections should be carried out and the standard flushing remedies to unblock sprinkler pipes.
Looking to repair or replace obstructed pipes? Browse our selection of pipe and accessories, including CPVC pipe components, pipe hangers, and seismic bracing.
When to be concerned about fire sprinkler pipe
Pipes often don’t give visual or other obvious clues that they are blocked. Therefore, NFPA 25: Standard for the Inspection, Testing, and Maintenance of Water-Based Fire Protection Systems has outlined specific conditions associated with pipe obstruction. Performing an obstruction investigation when these conditions are present is critical since NFPA’s routine inspection period for periodic assessment of potential pipe blockages is at least five years.
Since so much time can stretch between routine investigations, knowledge of the specific piping environment, tell-tale signs, and the specific history of usage (or non-usage) of the system are critical.
The 2020 edition of NFPA 25 breaks down 15 conditions that warrant pipe obstruction investigations. We will review each of those as a framework for performing an investigation. In addition, NFPA 25 notes four system elements (valves, risers, cross mains, and branch lines) that must be inspected.
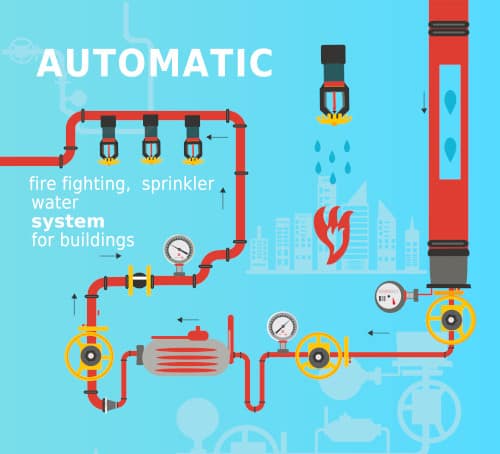
When it comes to sprinkler obstructions, small pipes equal bigger problems
Sprinkler systems in commercial buildings form a network, much like arteries, blood vessels, and capillaries in the human body. Water moves from larger diameter pipes to a branching system of smaller pipes, the “capillaries.” The analogy is incomplete, however, because not all sprinkler systems have a pump (the human heart); some are kept under pressure by the pressure inherent to the water supply.
NFPA 13: Standard for the Installation of Sprinkler Systems permits sprinkler pipes to have relatively small diameters, as low as ¾ inch in commercial systems. That means it doesn’t take a great deal of blockage to effectively prevent adequate water flow, thus incapacitating the sprinkler from automatic activation.
Less-common dry pipe systems are more prone to blockage due to corrosion from traces of water in metal pipes. Their normally dry environment periodically fills with water during testing or a fire, and moisture is often left behind. Any pooling of water makes the once bone-dry piping interior highly susceptible to corrosion, and pipe corrosion is a major source of blockages.
Visually inspecting hundreds of feet of pipe (of any size) is daunting and time-consuming given that a significant blockage can appear in any part of the system. Thus, obstruction investigators must focus on three facets:
- When to inspect, by doing assessments
- What known or observable conditions trigger an inspection
- What parts of the system are most vulnerable, and most easily accessible for assessment
Whether the sprinkler system is wet pipe, dry pipe, pre-action, or deluge style—sources of blockages must be ferreted out by looking for conditions associated with sprinkler obstruction, which include knowledge of system components and the individual history of the sprinkler system. Even new metal pipes can quickly corrode when leaks develop or foreign materials enter.
Some installations opt for CPVC piping over metal, as they are more corrosion-resistant and can be easier to install and repair, and are less expensive with an array of adapters. Even this type of piping can become blocked, however, and does not preclude a strategy for obstruction inspection. It’s also important to keep in mind that CPVC pipe is only listed for light-hazard occupancies since it can start to soften at temperatures slightly higher than 200°F. The upper service temperature limit of currently listed CPVC sprinkler pipe is 150°F (65.5°C) at 175 psi (12.1 bar).
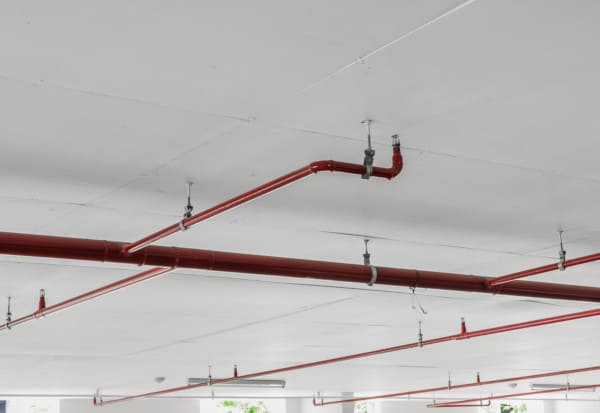
NFPA requirements for assessing sprinkler pipes
NFPA 25 addresses monitoring interior piping conditions and conducting obstruction investigations in Chapter 14, and this guidance pertains to all four types of water-based fire sprinkler systems, as well as foam-water systems. (NFPA specifically comments, however, that the more corrosion-resistant varieties of non-metallic pipe are not required to follow the recommendations in section 14.2 regarding the frequency of inspection).
From the 2020 edition of NFPA 25
14.1* General. This chapter shall provide the minimum requirements for conducting investigations of fire protection system piping for possible sources of materials that could cause pipe blockage or internal corrosion of system components.
In 2014, NFPA 25 changed the requirements of Chapter 14 to require an assessment instead of an inspection to determine the condition of system piping. Broadening the requirement gave the property owner the ability to choose among several different methods for checking their pipes, hopefully making the burden as small as possible.
The traditional method for conducting the required internal assessment involves draining the system piping, opening it up, and looking inside—taking samples of any organic growth that’s found. To save on costs, NFPA 25 recommends timing these assessments to coincide with other actions that require drained pipes such as internal inspections of system valves, renovations, and maintenance.
Even so, this approach can be expensive and intrusive. It requires property owners to take the system offline for a period of time and may cause unacceptable business interruptions in facilities like hospitals or power plants. So, NFPA 25 (A.14.2.1) specifies other noninvasive methods of conducting an assessment, such as the use of ultrasound technology or laboratory analysis of water samples and the inspection of solid material discharged at the main drain and inspector’s test connection.
From the 2020 edition of NFPA 25
A.14.2.1 It is the intent of this requirement to provide a reasonable assurance that corrosion and obstruction issues within fire protection systems are identified. It is not the intent to require verification that every piece of pipe in the system is free from corrosion and obstructions. An assessment of the internal condition of piping can be accomplished by several methods that meet the intent of this section.
In determining the best time to examine piping, the maximum period between assessments in any sprinkler pipe should be five years, as established by a specific risk analysis performed by a qualified entity or person. The authority having jurisdiction (AHJ; often the fire marshal) must approve any recommended frequencies longer than five years.
From the 2020 edition of NFPA 25
14.2.1* An assessment of the internal condition of piping shall be conducted on a frequency determined by 14.2.1.1 or 14.2.1.2 for the purpose of inspecting for the presence of foreign organic and inorganic material.
14.2.1.1 An assessment of the internal condition of piping shall be conducted at a minimum of every 5 years or in accordance with 14.2.1.2 for the purpose of inspecting for the presence of foreign organic and inorganic material.
14.2.1.2* Where an assessment frequency has been established by an approved risk analysis, the assessment shall be performed at a frequency determined by the approved risk analysis.
Section 14.2 specifies that when buildings have multiple wet pipe systems, they all must receive the same frequency of evaluation, either within a given five-year period or based on a specific risk analysis.
If any sprinkler or piping element within a building shows the presence of foreign inorganic and/or organic materials in the pipes, the entire network needs to be assessed (14.2.2.2). Supporting material from A.14.2.2 indicates that a reasonable approach to assessment in a large building is to evaluate half the system and, if no foreign organic and/or inorganic material is found, conclude that the piping is unobstructed. In the next inspection cycle, the alternate half of the building’s sprinkler system can be assessed.
The NFPA 25 Handbook discusses how to begin the timing of routine testing:
From the 2017 edition of the NFPA 25 Handbook
The sprinkler testing provisions in NFPA 25, like most of its requirements, are frequency based. For this concept to work, there has to be a starting point. For each of the frequencies in this section, the basis for this starting point is the date of installation.
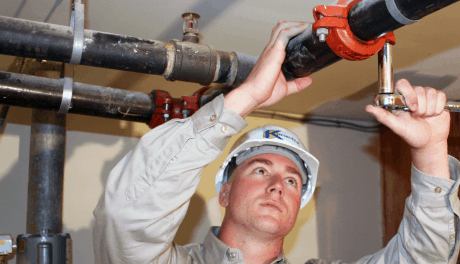
The land of red flags: what triggers an obstruction investigation
While obstruction investigations are vastly different from the assessments required by 14.2.1, it is not unusual for assessments to raise a red flag that a deeper look into pipe conditions is warranted. Internal assessments are largely designed to determine pipe corrosion, but they can also uncover the presence of material that could cause a dangerous obstruction.
Obstruction investigations are more extensive than assessments and do not have a specified frequency. They are triggered by specific events or conditions that can occur either within the system itself or within the water supply infrastructure for the system.
Since blockages can occur anywhere within the pipe to potentially restrict water flow, a non-routine inspection must use a systematic approach that considers a variety of potential sources of obstruction.
NFPA 25 lists conditions that should always raise red flags and result in further investigation. The NFPA 25 Handbook also recommends forms and checklists to track the frequency of checks and the scope of system components assessed.
From the 2020 edition of NFPA 25
14.3.1* An obstruction investigation shall be conducted for system or yard main piping wherever any of the following conditions exist:
(1) Defective intake for fire pumps taking suction from open bodies of water
(2) The discharge of obstructive material during routine water tests
(3) Foreign materials in fire pumps, in dry pipe valves, or in check valves
(4) Foreign material in water during drain tests or plugging of inspector’s test connection(s)
(5) Unknown materials are heard in the system piping during draining, refilling, or otherwise flowing water through the system
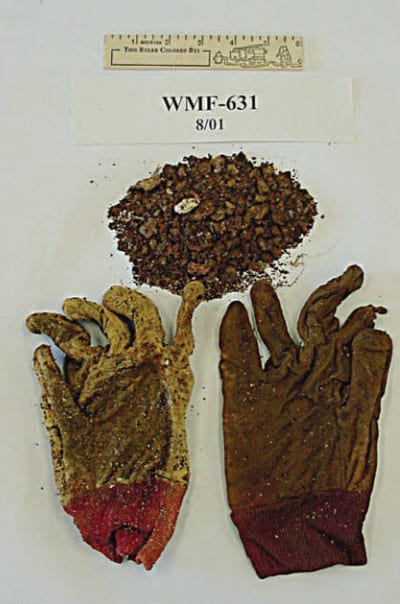
(6) Plugged sprinklers
(7) The presence of sufficient foreign organic or inorganic material is found in the pipe
(8) Failure to flush yard piping or surrounding public mains following new installations or repairs
(9) A record of broken public mains in the vicinity
The NFPA 25 Handbook explains that the intent of trigger (9) is to ensure that obstructive material like gravel doesn’t enter the system after a break repair. A certain level of judgment is necessary, as the requirement for “in the vicinity” is not defined.
(10) Abnormally frequent false tripping of a dry pipe valve(s)
(11) A system that is returned to service after an extended shutdown (greater than 1 year)
(12) There is reason to believe that the sprinkler system contains sodium silicate or highly corrosive fluxes in copper systems
(13) A system has been supplied with raw water via the fire department connection
(14) Pinhole leaks
(15) A 50 percent increase in the time it takes water to travel to the inspector’s test connection from the time the valve trips during a full flow trip test of a dry pipe sprinkler system when compared to the original system acceptance test
In some instances, such as zebra mussel infestations, the cause of the obstruction is difficult to control. Zebra mussels are small, freshwater bivalve mollusks with zigzag markings on their shells. They can invade sprinkler piping that’s supplied by a natural source of water, such as a river or lake. Most enter the piping as larvae or young adults and then grow into obstructions.
When obstructions are hard to correct, NFPA 25 (14.3.2.1) requires obstruction investigations to be repeated every five years to ensure the pipe will work as expected during a fire. In all other instances, obstruction investigations are not meant to become routinely scheduled activities and are only required when one of the above 16 conditions listed in 14.3.1 is found.
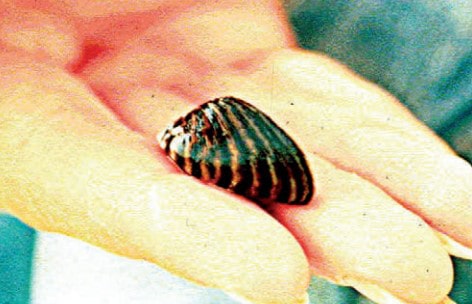
The main sources of fire sprinkler pipe system obstructions
Sprinkler system pipes have yielded a cornucopia of strange objects; welding materials and even intact work gloves have been dug out of clogged sprinkler pipes. Let’s look at some common issues that cause obstructions:
Pipe scale
NFPA 25 (D.2.1) asserts that dry sprinkler systems account for most fire losses resulting from obstructed sprinklers—and pipe scale is the leading obstructing material in those cases. Pipe scale is a mineral coating that can form in pipes when water flows through it.
Dry pipe systems that have been maintained as alternately wet and then dry over a period of years are particularly prone to an accumulation of pipe scale. In systems that were always dry, condensation from moisture in the air supply or traces of water left in the pipes sets the stage for hard scale, microbiological materials, and corrosion products to form along the bottom of pipes. When sprinklers open, the scale can break loose and flow down the pipe, plugging sprinkler heads or causing obstructions at fittings.
Careless installation or repair
Many obstructions can be traced back to workers who are careless during the installation or repair of yard or public mains and sprinkler systems. Wood, paint brushes, buckets, gravel, sand, and gloves are just a few of the materials that have been discovered clogging sprinkler systems. In other cases, cutout discs created when holes are drilled for quick-connect fittings are left in the piping, blocking water flow.

Raw water sources
Foreign materials can be sucked up from the bottoms of rivers, ponds, or open reservoirs and forced into sprinkler systems by fire pumps with poorly arranged or inadequately screened intakes. These obstructions may range from fine, compacted materials like mud or sand to coarser materials like stones, sticks, or wood chips.
Biological growth
Asiatic clams and zebra mussels are common examples of biological growth that can work its way into fire protection systems supplied by raw river or lake water to cause blockages. The Asiatic clam, for instance, typically enters systems as small larvae but can grow larger than 2 1∕8 inches (54 mm) by attaching itself to piping and feeding on bacteria or algae that passes through the system. Originally brought to Washington from Asia, these clams have been discovered in at least 33 U.S. states.
Calcium carbonate deposits
Natural freshwaters contain dissolved calcium and magnesium salts in varying degrees. When the concentration of these salts is high, the water is considered hard. When hard water flows through pipes made of more-noble metals like copper, a thin film composed largely of calcium carbonate tends to form that can offer some protection against corrosion.
But there’s also an unfortunate consequence: this scale formation also naturally occurs on sprinklers—often plugging the orifice even when the piping itself is relatively clear. This type of sprinkler obstruction can’t be detected or corrected by normal flushing procedures. It is usually discovered by inspecting sprinklers in suspected areas.
Most public water utilities in hard water areas soften their water supplies to minimize consumer complaints about scale buildup in water heaters. Thus, this type of obstruction is most often found in sprinkler systems directly supplied without treatment from wells or surface water in areas where water supplies are known to be hard.
Ice
NFPA 25 (14.4) requires property owners to perform annual internal inspections for ice obstructions in dry or preaction systems that pass through refrigerated spaces maintained at temperatures below 32°F (0°C). The inspection should be conducted at the point where the piping enters the refrigerated area. All penetrations into the refrigerated space must be inspected. If ice obstructions are found, 14.4.2 requires the inspection of additional pipe to ensure that no other ice blockages exist.
Pipe corrosion as a factor in sprinkler obstruction
Most piping systems contain some evidence of foreign material or corrosion, but not enough to trigger an obstruction investigation. During the initial assessment, the presence of tubercles or slime requires an additional step in the inspection process. NFPA 25 (A.14.2.1) recommends that black-colored water and rust should always be further investigated, as well as any smell of sulfur.
If signs of microbiologically influenced corrosion (MIC) are present, the damage can affect any part of the pipe system. Slime refers to a microbiological colony of either fungi or bacteria, sometimes referred to as bio-film.
The surfaces of pipes with bio-film steadily and rapidly collect salts or metals (or both), which can lead to nodules, tubercles, and carbuncles. Their presence, in turn, may lead to obstruction by either blocking the entire pipe diameter through the build-up, or loosening during flow and forming a blockage downstream.
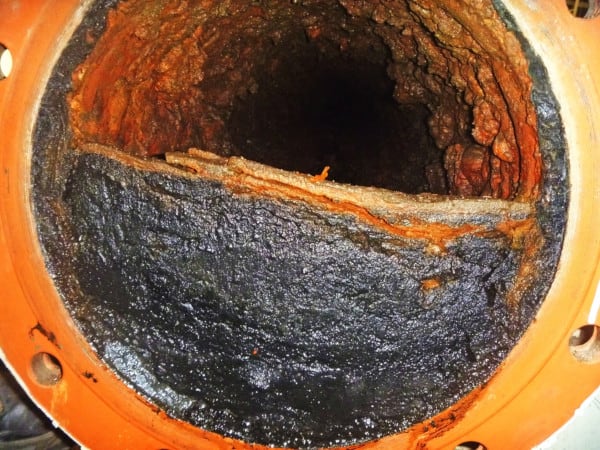
Corrosion is identified in NFPA 25 (Appendix D) as having eight primary varieties. It is defined as a chemical or electrochemical reaction—although MICs are considered a “ninth form of corrosion” (D.2.6). Corrosion is a term that describes reactions primarily between metal (or multiple types of metal) and another element or elements that can result in a buildup of material or loss of metal. We cover the topic of corrosion in greater detail, explaining the degree to which its sources are detectable and destructive.
Spotting conditions that should trigger an obstruction investigation helps protect people and property from fire
Fire sprinkler protection is an essential component of fire and life safety on a property. But over time, these systems can accumulate organic or inorganic materials that not only prematurely deteriorate system parts but can create obstructions that lead to system failure. Recognizing the conditions that should trigger an obstruction investigation goes a long way toward avoiding the potentially devastating consequences that can occur when water is prevented from reaching sprinkler heads.
Be sure to read the next installment of our series on obstruction investigations, where we reveal how these important investigations are conducted.
Looking to repair or replace obstructed pipes? Browse our selection of pipe and accessories, including CPVC pipe components, pipe hangers, and seismic bracing.
For more information about QRFS products, call us at +1 (888) 361-6662 or email support@qrfs.com.
This blog was originally posted at blog.qrfs.com. Check us out at Facebook.com/QuickResponseFireSupply or on Twitter @QuickResponseFS.
Do fire sprinkler systems that are constructed of the orange plastic pipe and are filled with glycerine, need to be obstruction inspected every five years too?
Bob – thermoplastic CPVC pipe (orange pipe) are less subject to corrosion and things like microbiological buildup, which can be major factors in obstructions. But NFPA 25 does not specify a pipe material when mandating a 5-year “assessment of the internal condition of piping” (14.2.1.1). It does, however, recognize that different materials, systems, and scenarios are more subject to these issues than others, so it also says that an alternative schedule can be set if an “approved risk analysis” is completed:
Thus, it is a conversation that should be conducted with a qualified fire protection ITM professional and the authority having jurisdiction.
Hi and thanks for all the great pictures and excellent details regarding why we do these types of inspections.
I’m the owner of a Vancouver BC, Canada based fire equipment service company. I’m trying to get a clear idea of how long I need to leave a dry pipe system “WET” to be able to loosen up scale that builds up in some of the systems we service? After we soak it the system will be completely flushed using main branch line end caps or other flushing connections.
I’m specifically searching advice from those in the Pacific Northwest that are familiar with our water and its biology.
Regards Russ
Russell — Thanks for reading and the kind words—and you’re welcome. For specific system application questions like yours, you can try our Ask a Fire Pro service. Click the link to submit your question with some information about your building, and a fire protection professional will provide an answer based on best practices, standards, and codes. Our pros include AHJs, contractors, engineers, and code experts with 150+ years of combined experience!