An explosion-proof flow switch, pressure switch, and other devices can help prevent explosions in hazardous environments
Electronics like flow switches, pressure switches, and valve tamper switches are essential components of modern fire sprinkler systems, spurring crucial notifications. Most of these devices only carry and need the typical listings for use in fire protection. However, some environments are so hazardous that ordinary electric components just aren’t safe, and they require special explosion-proof equipment.
In an industrial setting with high concentrations of volatile substances in the atmosphere, sparks from electronics can create dangerous explosions or fires. Therefore, some devices (including fire sprinkler monitoring switches) are designed to be “explosion-proof.” But that’s just one safety rating—there are other types of hazards and corresponding safety features.
Read on for explanations of:
- How NFPA 70: National Electrical Code classifies different environmental dangers from gas, vapors, dust, and fibers
- The design features that make electronics safer in classified environments
- Listings and approvals for explosion-proof equipment and other hazards
QRFS stocks the standard flow switches, pressure switches, and supervisory switches you need for most fire sprinkler systems. If you require explosion-proof devices or switches rated for other hazards, contact our support team for assistance.
Gas, vapors, dust, and fibers: classified hazards for electrical equipment
Some industrial environments are inherently flammable because gas, vapors, dust, particles, or fibers are present in the air and easily ignitable. In these settings, a tiny spark (such as from an electronic device) could ignite a massive fire, creating the need for explosion-proofing and other safety measures.
But not all environments and risks are the same, and designers must understand each to build a safe device. Chapter 5 of the National Fire Protection Association’s NFPA 70: National Electric Code (NEC; 2023 edition) categorizes different hazards on three levels: Class, Division, and Group. Briefly:
- Class tells you what kind of hazard it is—gas, dust, or fiber
- Division indicates the severity of the hazard
- Group gets more specific about the exact material involved
Settings that fall into these categories are sometimes called “classified environments.”
Class I, Class II, or Class III
NEC groups these hazardous environments into three classes (NEC 500.5A-D) based on what creates the hazard: gas, dust, or fibers:
- Class I has flammable gasses, vapors, or aerosols. Examples include refineries, chemical plants, or distilleries.
- Class II has flammable powders. Grain elevators are an example.
- Class III has flammable fibers. For example, consider a textile mill.
The distinction between these three groups is essential for equipment design. “Explosion-proof” is one design, but it isn’t appropriate for all hazards. There are other risks—and remedies—that we’ll explain shortly.
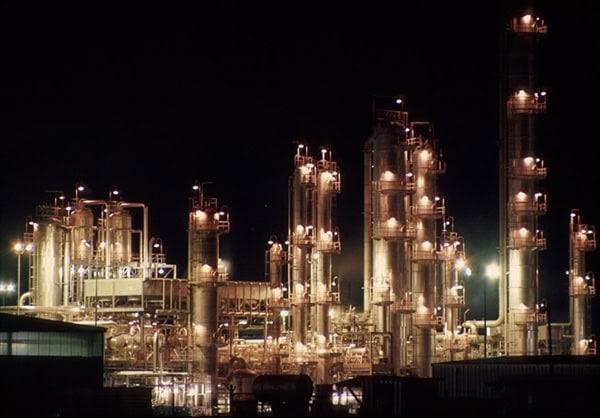
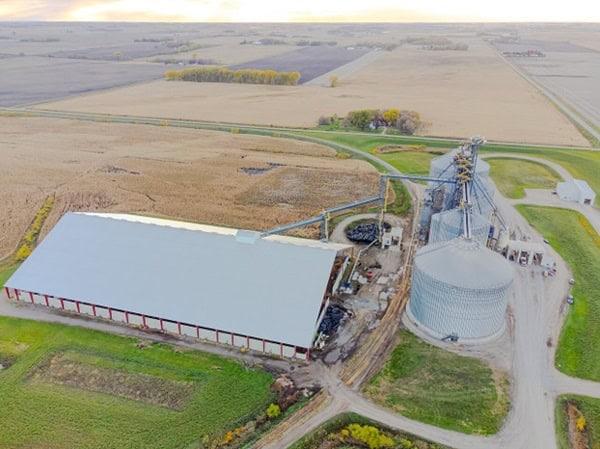
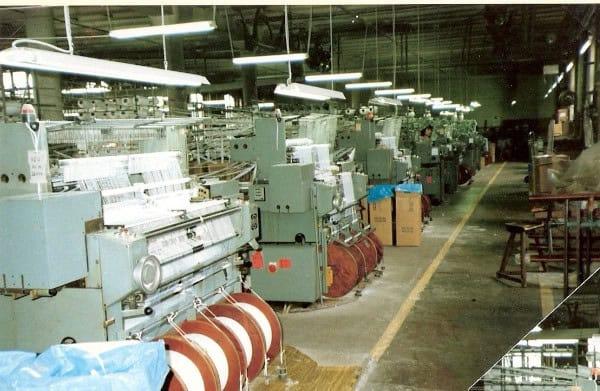
Divisions distinguish between hazard levels
Each class is broken down into Division 1 and Division 2, with the former being more hazardous than the latter. Classes I, II, and III each use slightly different rules with very fine distinctions to separate into divisions. For now, just know that Division 1 environments generally have normally ignitable atmospheres, while Division 2 environments generally have ignitable atmospheres in abnormal situations, such as when ventilation equipment fails.
Some gases and dusts ignite and explode more easily than others. So, NEC distinguishes between them based on their hazard level with a concept called Groups. Class I gas, vapor, and aerosol hazards are split into Groups A through D (500.6(A)), while Class II dusts are divided into Groups E through G (500.6(B)). Class III fibers are not split into materials groups.
To understand Class I groups, we need to understand a few materials-science concepts. First, the maximum experimental safe gap (MESG) is the biggest opening in a metal container that can still hold an explosion of gas inside the container. This essentially measures how tight a seal is needed on an electronic enclosure to stop an explosion from spreading. The other concept is the minimum igniting current ratio (MIC ratio), which measures how much electric current in a spark is needed to ignite a gas. Gasses with smaller MESG or MIC ratio values are harder to contain and easier to ignite.
This table summarizes the specs for each material group:
Protection techniques for electronics in hazardous environments: explosion-proof equipment and other risk-reduction designs
The point of all these categories—Class, Division, Group—is to help us understand the safety measures needed to prevent electronics from causing a fire. These aren’t the same in every environment!
On the surface, it may seem like explosion-proof equipment should be safe to use everywhere, or something designed for Class I environments should also be safe for Class II. However, NEC explains why this isn’t necessarily true, as the threats are different:
From the 2023 edition of NFPA 70
502.5, Enhanced Content
The electrical equipment required in Class II locations is different from that required for Class I locations. Class II equipment is designed to prevent the ignition of layers of dust, which can also cause an increase in equipment operating temperature, while Class I equipment does not address this concern. […] Grain dust […] ignites at a temperature lower than that of most flammable vapors.
In other words, what’s safe for Class I is not necessarily safe for Class II, and “explosion proof” isn’t the only possible necessary safety feature.
Section 500.7 of NEC lists many different protection techniques. Some, such as “explosion-proof” and “dust-ignition proof,” are about enclosure design. Enclosures house and protect electrical wiring; they can be smaller than junction boxes or larger than breaker boxes. Specifically, an explosion-proof enclosure is heavy-duty and has thread-sealable wiring ports (NEC 501.10A(3)).
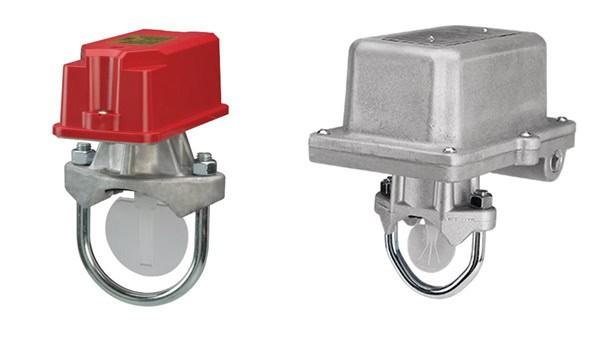
Other types of designs—such as “non-incendive” components, circuits, or equipment—focus on wiring methods determined not to create sparks or arcs. Finally, some techniques use non-flammable substances like oils, inert gas, or resins to shield electrical components from anything they could ignite.
We’ve summarized some of the different protection techniques in the table below. The explanations are summaries of the definitions found in Chapter 1 of NEC. The use case for each method comes from section 500.7 of NEC:
Listings and approvals for electric devices in special-hazard environments
Many fire protection devices must be listed, carrying the marks of an organization such as UL or FM Global indicating they have been tested to appropriate standards by a nationally recognized testing laboratory (NRTL).
But in the hazardous environments we’ve discussed—Class I, Class II, and Class III—equipment needs additional layers of safety beyond a standard fire-service rating. For example, a water flow switch used in certain environments might be separately listed for fire service and listed as explosion-proof equipment. Distinct standards exist for classified environments. There are many of them, but here’s a short list of some of the main standards used in the US:
- FM 3600: Electrical Equipment for Use in Hazardous (Classified) Locations—General Requirements
- FM 3610: Intrinsically Safe Apparatus and Associated Apparatus for Use in Class I, II & III, Division 1, Hazardous (Classified) Locations
- FM 3611: Nonincendive Electrical Equipment for Use in Class I and II, Division 2 and Class III, Divisions 1 and 2 Hazardous (Classified) Locations
- FM 3615: Explosionproof Electrical Equipment General Requirements
- UL 60079-0: Explosive Atmospheres—Part 0: Equipment – General Requirements
- UL 60079-1: Explosive Atmospheres—Part 1: Equipment Protection by Flameproof Enclosures
- UL 1203: ExplosionProof and Dust-IgnitionProof Electrical Equipment for Use in Hazardous (Classified) Locations
When you purchase equipment for classified hazardous environments, the manufacturer typically won’t enumerate which specific standards a device complies with. Instead, they indicate significant ratings like “explosion proof” or “dust-ignition proof” and list which NEC Classes, Divisions, and Groups the device is rated for.
For example, this VSR-FEX Series flow switch from Potter Signal is described as explosion-proof, and its data sheet says, “For use in hazardous locations, classified as: Class I: Div. 1 & Div. 2, Groups C, D Class II: Div. 1 & Div. 2, Groups E, F, G, Class III: Div. 1 & Div. 2.”
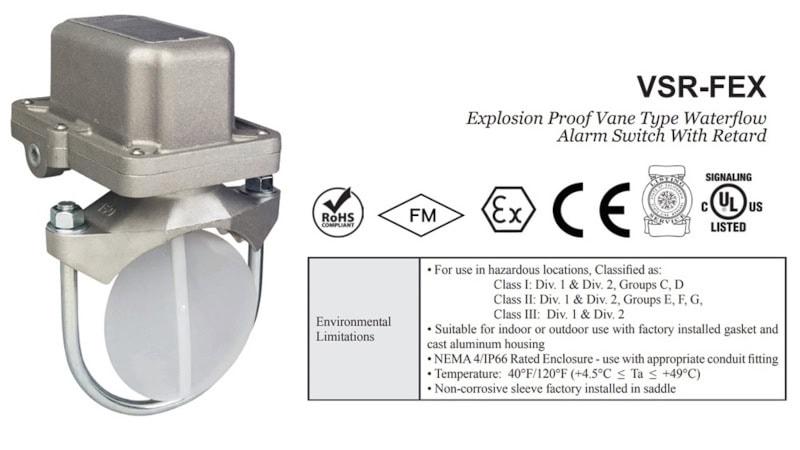
If you know what protection a specific environment requires, as specified by a fire protection engineer or authority having jurisdiction, you can figure out the right equipment. When it comes to fire protection switches, the hardware labeled “explosion proof” meets most needs.
Stay protected in hazardous environments with the proper explosion-proof equipment
While electric monitoring devices are essential in modern fire protection systems, electricity is a source of sparks and heat. Your average fire sprinkler flow switch or valve tamper switch won’t cause a fire in, say, a grocery store. But standard electronics can be dangerous in NEC-classified environments where the air is filled with flammable dust, gas, vapor, or fiber.
In these settings, electronic devices should have special designations to prevent causing a fire or explosion, each tested and listed for specific Classes, Divisions, and material Groups. You can find this safety info on an item’s manufacturer data sheet. When it comes to fire protection equipment like flow switches, pressure switches, or valve tamper switches, look for an explosion-proof rating. Trusted manufacturers like Potter and Safe Signal offer explosion-proof equipment listed for Class I, Class II, and Class III environments.
For help purchasing explosion-proof switches, contact the QRFS sales team directly. For standard supervisory devices, check out our website.
If you need something you don’t see in our catalog or have additional questions, email us at support@qrfs.com or call 888-361-6662.
This blog was originally posted at blog.qrfs.com. If this article helped you, check us out on X @QuickResponseFS.