Careful preparation before—and thorough inspection and testing after—are key to maintaining life safety systems in extreme weather
The scenes that emerged in the aftermath of Hurricane Dorian in the Bahamas are devastating. Choppy, coffee-colored floodwaters surge 20 feet high in the hardest-hit areas—reaching roof peaks and the tops of palm trees.
And unfortunately, hurricane season is far from over.
More hurricanes come ashore in the U.S. in September than any other month and the number of landfalls in October isn’t far behind. And in recent years, warmer-than-usual ocean waters are creating hurricanes that are stronger, intensify faster, and dump more rain on communities in their paths.
Rightly so, much of the focus after a catastrophic hurricane swirls around ravaged homes and displaced families. But facility managers at thousands of commercial buildings are also quietly struggling to get back to business after the storm. And one of the most critical tasks they face is ensuring life safety on their properties by restoring fire protection systems to service that were damaged during the hurricane.
In this blog, we will offer tips for preparing your fire protection system for a hurricane—and getting it back up and running when the storm passes to protect people and property from fire. While the risk of fire may be far from your mind in a facility that was just drenched in water, the reality is that the risk is higher than ever due to damage to electrical systems and devices caused by flooding.
If a hurricane has impacted your area and you need to make repairs, our selection of commercial fire sprinklers, installation tools, pipe components, valves, and more is in stock to help you restore your fire protection systems to service.
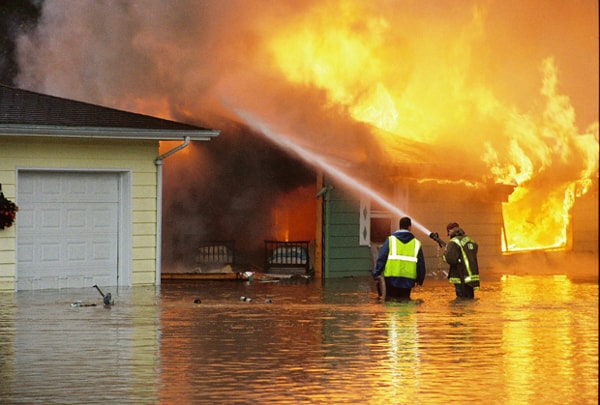
Don’t ignore fire protection systems in emergency preparedness plans
There’s an old saying among hurricane-hardened folks who live in coastal areas: hide from wind but run from water. While intense winds can certainly cause devastating damage during a hurricane, it’s the water that often wreaks the worst havoc. And don’t think just because your building is a little inland that you’re completely safe from a storm surge. Water pushed by strong winds can flow up rivers and streams as well, causing them and other bodies of water to overflow in catastrophic flooding.
Floodwaters now cause more damage than punishing winds during intense storms: Hurricane Katrina swamped 80 percent of New Orleans after storm surge breached 53 levees in 2005. Sixty percent of the losses reported from Superstorm Sandy in 2012 were attributed to water damage. Hurricane Harvey became the most extreme rainfall event in U.S. history in 2017, drenching Texas with a whopping 60.58 inches of rain and causing $125 billion in damage.
How fast facilities can recover from hurricane-induced destruction often comes down to preparation. NFPA 1600: Standard on Continuity, Emergency, and Crisis Management covers the key elements required for effective emergency management programs and business continuity during any type of emergency, from fires to hurricanes to acts of terrorism.
From the 2019 edition of NFPA 1600
5.4.1* The entity shall conduct a resource needs assessment based on the hazards identified in Section 5.2 and the business impact analysis in Section 5.3.
A.5.4.1 Scenarios developed during the risk assessment and BIA should be used to identify resources needed by the program. Resources for emergency operations/response to protect life safety, stabilize the incident, and protect property should be identified.
It’s critical that preparedness plans and checklists before a hurricane include fire protection systems. After all, these systems can be all that stands between the people and property you want to protect and dangerous fires when hurricane conditions make it impossible for emergency crews to arrive quickly. Keep this in mind as well: Many insurance carriers will require proof that property owners took reasonable measures to prevent fires during flooding before they will cover a claim.
And again, note that storms can increase the risk of fire. For example, more than 150 homes were destroyed by enormous fires that swept through the New York communities of Rockaway Beach and Breezy Point during Superstorm Sandy after rising seawater caused electrical systems to spark.
Watch this video of a house fire during Hurricane Harvey to understand the devastation that can result as intense winds spread flames despite torrential rains and flooding:
In the sample business preparedness guide offered in Annex C (Figure C.1), NFPA 1600 emphasizes the need for emergency management programs to include fire prevention programs and automatic sprinkler systems:
- Fire prevention program — Fire is the most common and significant threat to most businesses. Owner/operators can reduce the probability of fire by implementing fire safety programs, especially where flammable liquids or gasses are handled.
- Automatic sprinklers — Locating a business or operation in buildings that are fully protected by automatic sprinklers significantly reduces an entity’s exposure to a catastrophic incident. Many natural catastrophes are often compounded by fire.
Standard guidance before a storm includes making sure that fire protection systems are in working order and filling the fuel tanks on diesel fire pumps and emergency generators. In fact, it’s wise to take the extra step of asking a licensed fire protection contractor to evaluate fire protection equipment before the hurricane to ensure everything is in tiptop shape.
From the 2019 edition of NFPA 1600
A.5.4.3 All program equipment should be checked and tested on a regularly scheduled basis to ensure it will function properly when required.
If flooding seems likely, some risk management teams attempt to minimize the risk of electrical fires—or damage from arcing to expensive fire protection equipment like fire pumps—by cutting the system’s electrical power before a storm. A leading cause of electrical fires, arcing occurs when current jumps across a break in an electrical circuit, producing sparks and high heat.
But here’s the thing teams must carefully weigh: while shutting down power to fire protection systems may eliminate some risks, it significantly increases others—leaving the facility extremely vulnerable to fire.
Water-damaged electrical components can spark fires years after hurricane floodwaters recede
Once building personnel can safely re-enter a facility after the hurricane, it’s time to start assessing the damage and restoring fire protection systems to operating condition. Of course, the goal is to get systems up and running as quickly as possible. Fire risks run high after major flooding from live, water-damaged electrical circuits; gas or fuel leaks; accumulated debris that acts as kindling for fire; and puddles that contain spilled, flammable liquids like cleaning supplies that can cause fires to spread faster.
But in the rush to get systems back online, many facility managers may not consider potential long-term effects from hidden damage that can slowly rot system components. Water damage may not be immediately apparent—and submersion in corrosive saltwater from storm surge or “dirty” water filled with toxic substances that aren’t addressed can eat away at systems from within and lead to unexpected failures down the road.
Besides corrosive salt, floodwaters can contain an array of compounds harmful to fire protection systems (and other equipment throughout your facility), including fuel, solvents, industrial chemicals, sewage, cleaning chemicals, fertilizers, and pesticides. Floods also tend to carry mud that can deposit within equipment and cause overheating or mechanical failures.
Wire and wire connections damaged by Superstorm Sandy sparked the fire that decimated the Seaside Park boardwalk in 2013—nearly a year after the storm. Immersion in salt water during storm flooding caused wire connections to corrode, eventually generating so much excess heat that nearby building materials ignited. More than 50 businesses—many of which had just recently finished hurricane repairs—and a beloved amusement park were destroyed by the fire.
A quick post-hurricane fire protection system recovery checklist
To begin the recovery process of fire protection systems after a hurricane-induced flood, facility managers should immediately check water supplies, fire pumps, automatic sprinklers, fire alarms, and security systems, and report any outages to the proper authority.
The safest and most thorough way to assess the damage and ensure systems will function reliably after submersion in floodwaters is to hire a qualified fire protection professional to perform the annual system inspections—no matter how recently the last inspections were done.
It’s also a good idea to have systems inspected by an electrician to ensure that further damage won’t occur after they are re-energized. Along those lines, you may want to think twice about bringing non-critical systems back online after a lengthy power outage before permanent power is re-established, so you don’t render backup batteries unusable or risk additional damage from power surges.
A quick checklist for facility managers evaluating their fire protection systems might include:
- Testing fire sprinkler systems, including control valves
- Checking pipes for breaks, damage, or disconnections
- Testing fire pumps and inspecting fuel tanks for water intrusion
- Testing fire alarm systems, including external notification and alarms throughout the property
- Inspecting and testing fire alarm lights and control panels
- Checking emergency lights and exit lights for water damage and replacing shorted batteries
- Ensuring system valves, sprinkler heads, and control panels are free of mud, water, and other debris
- Checking fire extinguishers for damage, including the pull pin, pressure, tamper seal, and labeling
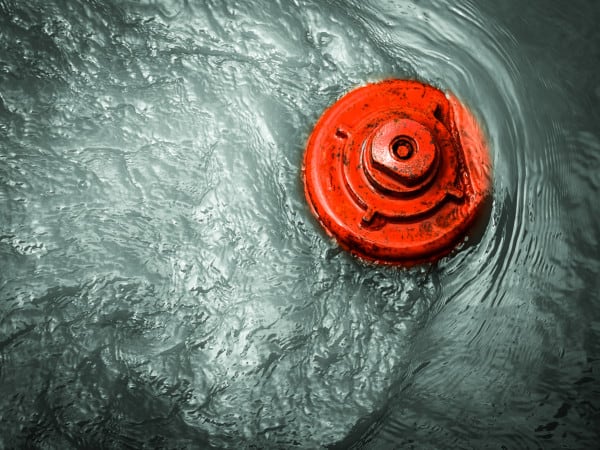
Repairs should be made urgently – and impairment procedures outlined in NFPA 25: Standard for the Inspection, Testing, and Maintenance of Water-Based Fire Protection Systems should be followed if the equipment is damaged so badly it cannot function properly and the building is occupied.
From the 2017 edition of NFPA 25
15.5.2 Before authorization is given, the impairment coordinator shall be responsible for verifying that the following procedures have been implemented:
(1) The extent and expected duration of the impairment have been determined.
(2) The areas or buildings involved have been inspected and the increased risks determined.
(3) Recommendations to mitigate any increased risks have been submitted to management or the property owner or designated representative.
(4) Where a fire protection system is out of service for more than 10 hours in a 24-hour period, the impairment coordinator shall arrange for one of the following:
(a) Evacuation of the building or portion of the building affected by the system out of service
(b)* An approved fire watch
(c)* Establishment of a temporary water supply
(d)* Establishment and implementation of an approved program to eliminate potential ignition sources and limit the amount of fuel available to the fire
(5) The fire department has been notified.
(6) The insurance carrier, the alarm company, property owner or designated representative, and other authorities having jurisdiction have been notified.
(7) The supervisors in the areas to be affected have been notified.
(8) A tag impairment system has been implemented. (See Section 15.3.)
(9) All necessary tools and materials have been assembled on the impairment site.
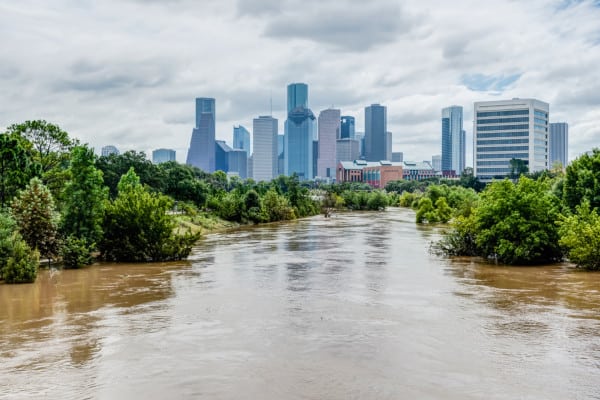
Should you repair or replace damaged equipment after a hurricane?
In the broadest strokes, the recommended course of action for any soaked electrical equipment is replacement—the fire hazard isn’t worth the risk, even if the equipment appears to be functioning for now. That includes any equipment with motors, switches, or wiring. In the fire protection industry, an easy rule of thumb to remember is that fire alarm panels and components that were submerged in a flood most likely need to be replaced, as well as fire pump controllers and components.
Fortunately, it’s also usually more cost-effective to replace equipment with smaller motors—think air compressors for dry sprinklers—then to go through the time-consuming process of removing them from service, sending them to a motor shop, having them cleaned, completing repairs, and getting them recertified by UL. Once products that bear a UL mark are rebuilt, UL requires confirmation that they continue to comply with appropriate safety requirements before they can return to service.
When it comes to larger, more expensive equipment like fire pump motors, however, repair and recertification may be a more cost-effective option than replacement—and, with the help of a qualified professional, can restore the integrity of a fire safety system.
But with water damage often elusive, how can facility managers confidently identify and restore every damaged fire protection system component after a flood?
A webinar from Fire Smarts featuring fire protection industry expert Tom Parrish, “Hurricane and Tropical Storm Recovery for Fire and Life Safety Systems,” aims to educate facility managers, building and fire officials, and service providers with guidance for reviewing and restoring fire and life safety systems after a natural disaster. For in-depth instruction, you can register to view the free webinar for a limited time. Fire Smarts is a nationally recognized fire education and training services provider.
Here’s a sampling of the webinar’s important tips for restoring fire protection equipment after a hurricane:
Floodwater elevation
If you returned to your building for the first time after floodwaters had already started to recede, critical to assessing the extent of the damage you face is determining how high the water reached. Floodwaters often leave a distinctive line on the walls that helps you easily identify what equipment was submerged. You can also look for standing water that remains on equipment with flat tops or ledges to judge flood elevation.
As a rule, if you aren’t sure exactly how high waters climbed, err on the side of the caution; the potential damage caused by an electrical fire down the road will cost more than repairing or replacing the equipment in question.
Fire alarm systems
Most likely, fire alarm control panels mounted within reach on the wall were impacted by floodwaters (water within the enclosure is a bad sign). Most jacketed fire alarm cables aren’t rated for wet locations, which means they need to be replaced if they were submerged in saltwater. But here, finally, is some good news: Wiring from these systems generally runs from the panel up—and notification and security devices are mounted high in the room. That means while the panel itself most likely needs to be replaced, you probably can avoid replacing the entire system.
Parts that didn’t come into direct contact with water may still be damp and require drying, but there’s a good chance they are otherwise undamaged. Before re-energizing this equipment, have a qualified electrician check the wiring and connections and ask an alarm professional to perform an annual inspection. That way, you can ensure that shorts or ground faults won’t cause more damage when you turn it back it on.
Batteries
NFPA 72: National Fire Alarm and Signaling Code mandates that fire alarm batteries must be replaced at periodic times recommended by the manufacturer or when a battery’s voltage falls below the manufacturer’s recommendations after charging for 48 hours.
Alarm battery back-ups are typically designed for a single discharge event—and many times, power outages that accompany intense hurricanes far exceed the 24-hour period they are designed to support. Once the battery is drained that much, replacement is recommended. At the very least, the battery must be charged for 48 hours and then load tested to see if it can maintain proper voltage.
Fire sprinkler systems
Visual inspections of sprinkler heads and pipes are necessary after a storm, checking for breaks, dislocations, and other damage. Cleaning the system by flushing it with fresh water is also recommended, especially if the system includes drainpipes, inspector’s test pipes, or auxiliary drains.
Dry sprinkler systems typically filled with pressurized air may be especially prone to accelerated corrosion after exposure to floodwaters, making system flushing even more important. But corrosion could be an issue for any system with metal components that were submerged in saltwater and should be monitored carefully in the coming years.
Backflow preventers that keep drinking water from becoming contaminated due to backflow should be inspected and serviced. It’s also a good idea to perform normal maintenance on valves that can be easily reached to ensure they are clean, lubricated, and opening and closing as expected.
Make sure water flow switches are clean and dry beneath the casing to mitigate the risk of corroded contacts causing problems down the road. Once again, contracting a fire safety professional to perform a thorough annual inspection is the best way to ensure sprinkler systems will perform reliably during future emergencies after a storm.
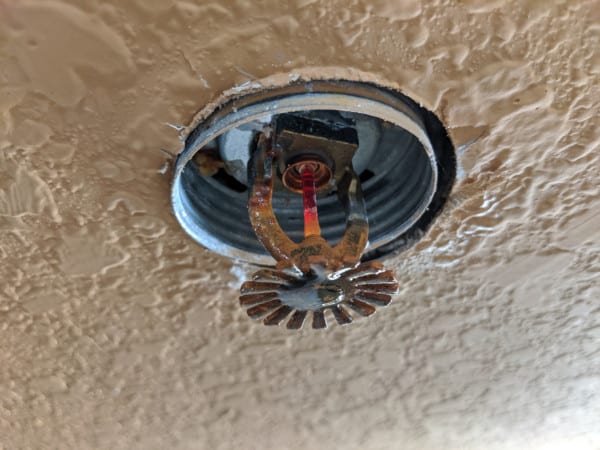
Fire pump controllers
Fire pump controllers are robust pieces of equipment that are built to withstand a little wetness—but not total submersion in brackish floodwaters. They are not watertight and should be opened and dried out as quickly as possible if they fill with water.
Equipment that was energized when floodwaters hit may have sustained substantial damage from arcing. Water damage to the computerized control circuits on the outside of the unit is another major issue that could prompt replacement, with real concerns about electrical fire. Corrosion of internal connections after exposure to saltwater is another significant risk that could cause issues within a few years of the storm. Some facility managers, however, may decide it’s more cost-effective to rebuild a larger, more expensive controller than replace it.
Electric-driven fire pumps
Fire pumps are made to be wet—although the water usually remains on the inside, not the outside. Even so, there are few moving parts on electric-driven pumps that should suffer significant impacts from saltwater and corrosion. After a flood, it’s usually enough to have the pump properly cleaned, tested, and serviced to catch any issues that arise.
Water-logged electric motors are more concerning, however, and facility managers may wind up weighing the difference between the availability and cost of replacing them vs. how long it will take shops in their area that were also impacted by the storm to perform repairs. Often in these situations, the fastest option for returning a system to service may be absorbing extra shipping costs and sending the motor to a repair shop in another state.
Water that saturated the motor windings is a major concern. It’s also generally wise to replace cables containing wires that got wet to guarantee there won’t be issues from corrosion down the road.
Diesel-driven fire pumps
Diesel-driven pumps have more moving parts, which also means more potential concerns after a flood. If a dipstick is pulled out of a diesel-driven pump and it looks like it’s covered in chocolate milk, that’s a strong indication that water mixed with the pump’s oil during the storm.
Diesel pumps also contain electronics that can be impacted by floodwaters and need to be assessed. Fuel filters, water separators, and fuel tanks should be carefully checked to ensure water didn’t mix with the pump’s fuel. Fuel tank lines should be flushed, and filters should be replaced.
The pump’s batteries should be checked to ensure they didn’t fill with water and the battery charger should be inspected for water damage. Contracting a service technician to perform the pump’s annual preventative maintenance or an after-storm service is imperative to ensure everything is in proper order.
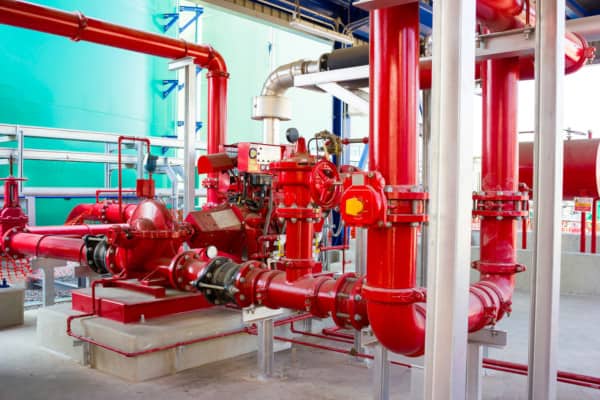
The final step: restoring fire protection systems to service
After damaged system components are repaired or replaced, NFPA standards outline the procedure for restoring fire protection systems to service. Restoration should be performed by a qualified fire safety contractor or otherwise-qualified personnel.
If extensive damage occurred to a water-based fire protection system, full hydrostatic testing in accordance with NFPA 25 is required to ensure system integrity was maintained. An obstruction investigation is also suggested to ensure the system is free of storm debris before it can be returned to service (NFPA 25 A.15.7).
From the 2017 edition of NFPA 25
15.7* Restoring Systems to Service. When all impaired equipment is restored to normal working order, the impairment coordinator shall verify that the following procedures have been implemented:
(1) Any necessary inspections and tests have been conducted to verify that affected systems are operational. The appropriate chapter of this standard shall be consulted for guidance on the type of inspection and test required.
(2) Supervisors have been advised that protection is restored.
(3) The fire department has been advised that protection is restored.
(4) The property owner or designated representative, insurance carrier, alarm company, and other authorities having jurisdiction have been advised that protection is restored.
(5) The impairment tag has been removed.
Make sure your fire protection systems are prepared for hurricanes—both before and after the storm
Major flooding caused by a hurricane can damage fire protection systems throughout a building – leaving your property alarmingly vulnerable to fire. Taking proper precautions before the storm arrives—and contracting a qualified professional to thoroughly inspect and test every system component afterward—is key to ensuring that corrosive floodwaters won’t pose a long-lasting threat to life safety.
If a hurricane has impacted in your area and you need to make repairs, our selection of commercial fire sprinklers, installation tools, pipe components, valves, and more is in stock to help you restore your fire protection systems to service.
For more information about QRFS products, call us at +1 (888) 361-6662 or email support@qrfs.com.
This blog was originally posted at blog.qrfs.com. Check us out at Facebook.com/QuickResponseFireSupply or on Twitter @QuickResponseFS.