An appropriate response helps prevent catastrophic outcomes after problems are discovered during fire protection inspections
A monstrous 16-alarm fire ravaged Bernat Mill in Massachusetts in 2007, burning out 65 business and leaving 500 people out of work. A full-coverage, combination wet pipe and dry pipe sprinkler system was installed to protect the property, including the basement where the fire started. So, what went wrong? Something that a proper fire sprinkler inspection could have prevented.
A control valve that enabled water to reach the sprinkler heads at the fire’s point of origin was closed and padlocked. With the water supply blocked off, the fire spread quickly across the mill’s wooden floors and overwhelmed the rest of the sprinkler system. A permit was required for the sprinkler system to be shut off, but none had been requested.
“If the sprinkler system had been properly maintained and operational, the fire would have been controlled and contained until the Fire Department arrived,” the local fire chief concluded in his report.
Fire protection system deficiencies and impairments can be catastrophic during an emergency, and the National Fire Protection Association (NFPA) and local authorities having jurisdiction (AHJs) have detailed rules in place to ensure they are handled properly. But there is some latitude for professional judgment—and if inspection, testing, and maintenance (ITM) professionals and property owners don’t accurately gauge the severity of an issue, it’s difficult to determine the right course of corrective action.
In this blog, we review NFPA requirements for classifying deficiencies and impairments discovered in water-based fire protection systems so that appropriate responses are taken. We also explain guidelines for tagging issues uncovered during system inspection and testing, as well as what each color-coded tag means.
Need to correct deficiencies or impairments discovered in a water-based fire protection system? Our selection of commercial fire sprinklers, installation tools, pipe components, valves, and more is in stock to help you restore your fire protection systems to service.
You can also read this blog to learn how fire protection ITM software can make the process of correcting deficiencies more effective and efficient.
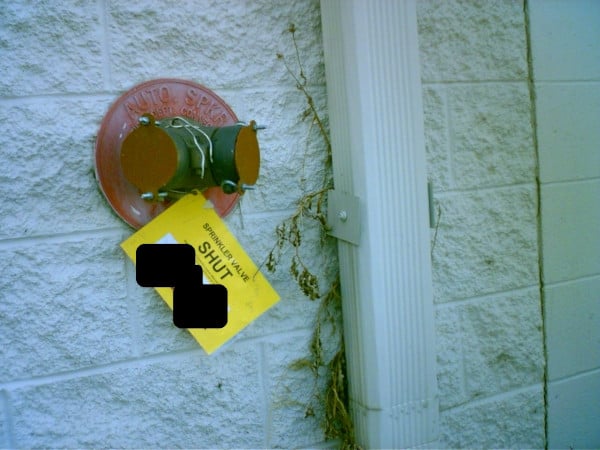
Deficiencies and impairments: why they shouldn’t be treated the same
Experiencing at least a few deficiencies and impairments is unavoidable over the lifecycle of a water-based fire protection system. How fast these issues are identified and corrected is key to maintaining life safety on the property. Failing to correct problems in a timely manner also exposes property owners to potentially hefty financial consequences, including fines, a building shut-down, legal liabilities, increased insurance rates, and unpaid insurance claims.
NFPA 25: Standard for the Inspection, Testing, and Maintenance of Water-Based Fire Protection Systems details the minimum requirements for maintaining these systems. It also outlines the process that needs to be followed when problems are found, including proper fixes and reporting. Local governments often build upon these guidelines with specific requirements for their areas. AHJs also enforce repairs, and many have their own specific mandates for timely corrections.
Before 2011, water-based fire protection systems basically either passed or failed NFPA 25’s ITM requirements. There was no official option for identifying different nuances of system status.
Thus, many AHJs basically lumped any issue under the umbrella of an “impairment,” currently defined as something that creates an emergency situation because it could cause systems to fail during a fire. Property owners interpreted this as having to follow the robust impairment process laid out in chapter 15 of NFPA 25: immediately correct even the most minor deficiency, like a missing hydraulic nameplate.
Understandably, many protested that implementing NFPA 25’s impairment procedure for issues that didn’t impact system performance—and potentially suffering consequences for not doing so—was onerous. The standard also requires detailed steps for restoring systems to service after impairments are corrected (15.7).
From the 2017 edition of NFPA 25
15.5.2 The impairment coordinator shall be responsible for verifying that the following procedures have been implemented:
(1) The extent and expected duration of the impairment have been determined.
(2) The areas or buildings involved have been inspected and the increased risks determined.
(3) Recommendations to mitigate any increased risks have been submitted to management or the property owner or designated representative.
(4) Where a fire protection system is out of service for more than 10 hours in a 24-hour period, the impairment coordinator shall arrange for one of the following:
(a) Evacuation of the building or portion of the building affected by the system out of service
(b)* An approved fire watch
(c)* Establishment of a temporary water supply
(d)* Establishment and implementation of an approved program to eliminate potential ignition sources and limit the amount of fuel available to the fire
(5) The fire department has been notified.
(6) The insurance carrier, the alarm company, property owner or designated representative, and other authorities having jurisdiction have been notified.
(7) The supervisors in the areas to be affected have been notified.
(8) A tag impairment system has been implemented. (See Section 15.3.)
(9) All necessary tools and materials have been assembled on the impairment site.
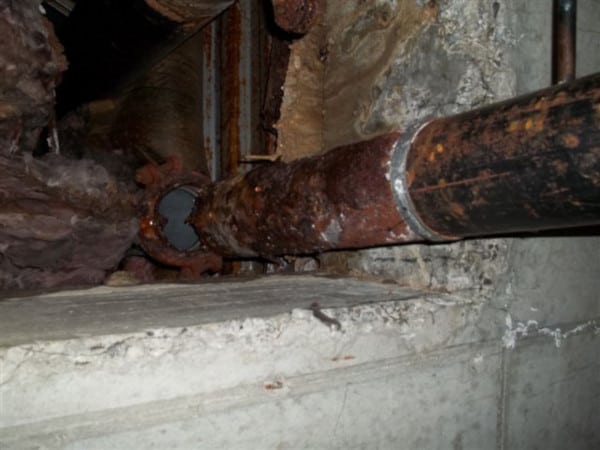
In 2011, NFPA 25 expanded its definition of a system problem to include two new levels along with impairments: critical deficiency and non-critical deficiency. By doing so, NFPA aimed to provide clearer guidance to inspectors and AHJs about the severity of system violations and subsequent corrective actions that are needed.
While it is still abundantly clear in the standard that every deficiency needs to be fixed in a timely manner, NFPA also recognizes that every issue isn’t an emergency. Since less-serious problems don’t stop systems from providing a reasonable degree of protection, NFPA agrees it’s not practical to treat every system issue the same.
NFPA does not intend for noncritical and critical deficiencies to involve impairment procedures such as fire watches, building evacuation, or standby fire protection unless the corrective action that’s required creates an impairment, like shutting off the water supply to replace a sprinkler.
Here’s how components that aren’t up to code are categorized in the 2017 edition of NFPA 25 to prioritize repairs:
- Noncritical deficiencies don’t impact system performance but must be corrected to meet NFPA standards within a reasonable amount of time (3.7.2). They might include missing signs or an inadequate number of spare sprinklers.
- Critical deficiencies—perhaps painted sprinklers or inaccessible fire hydrants—can have a “material impact” on system performance and should be corrected as soon possible (3.7.1). In other words, the deficiency does not prevent a system from functioning properly right now, but—if not corrected—it could lead to an impairment. For instance, a pipe that is showing some corrosion will still function during a fire, but if the condition is allowed to get worse, an impairment will result.
- Impairments are the most serious issues, meaning that all or part of the system is out of order and won’t function properly until it’s repaired (3.3.21). These are the highest priority and must be addressed immediately. Many believe that an impaired system is a system that has been shut off, but the definition is actually much broader. Any system or portion of a system that can’t function as designed during a fire would qualify as an impairment.
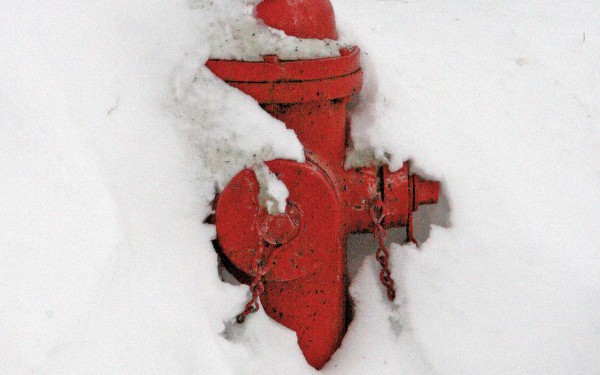
Impairments can be preplanned during scheduled maintenance, repairs, or building renovations, giving property owners plenty of time to implement temporary provisions or additional safeguards. Preplanned impairments can also be delayed until necessary equipment and personnel are available to make their duration as short as possible.
But impairments can also be unplanned emergencies, meaning the system is out-of-service due to damage or malfunction like a leak or frozen pipes. These repairs must often be accomplished under less-than-ideal conditions with the needed supplies and personnel not readily available—leading to a potentially lengthy interruption to critical fire protection equipment.
From the 2017 edition of NFPA 25
4.1.5.1* The property owner or designated representative shall correct or repair deficiencies or impairments.
A.3.3.7 An impairment should be addressed promptly by either immediately correcting the condition or implementing the impairment procedures found in Chapter 15. Critical and noncritical deficiencies should be corrected as soon as practicable after considering the nature and severity of the risk.
How to determine the right classification for system issues without black-and-white guidelines
Of course, with life safety on the line, introducing different classifications that determine the urgency of corrective actions has made assigning the appropriate deficiency or impairment level one of the most critical steps in the ITM process. Many inspectors say it is also now the most difficult part because it is so subjective.
The chart below from NFPA 25 Handbook: ITM of Water-Based Fire Protection Systems provides an overview of how common deficiencies are typically classified. Table A.3.3.7 in NFPA 25 offers a much more comprehensive list, including deficiency and impairment classifications for sprinkler systems, standpipes, fire pumps, fire service mains, water storage tanks, and more.
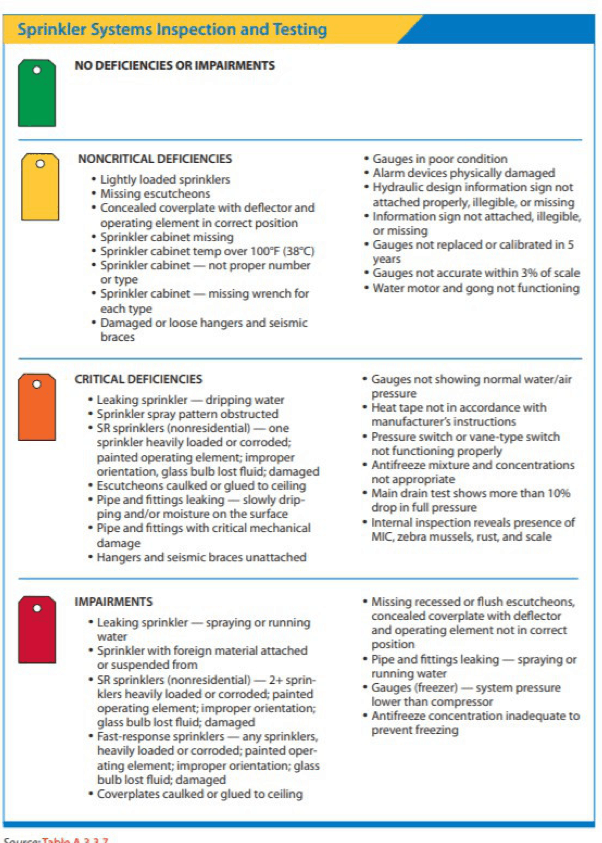
Neither source is meant to be all-inclusive or serve as a definitive guide, however, because different factors such as the nature of the hazard and the building’s occupancy classification could cause a deficiency that’s noncritical at one location to be much more serious at another. For instance, NFPA 25 (A.3.3.7) notes that the risk posed by a lightly painted sprinkler in a large warehouse might be noncritical, but a painted sprinkler could be critical or even an impairment in a high-hazard battery-charging station.
NFPA 25 (A.4.1.5.1) also urges inspectors to pay extra attention to deficiencies not explained by normal wear and tear. Unexplained deficiencies—such as banging noises in the sprinkler piping or perplexing leakage at closed nipples—could be symptoms of a greater problem that “could lead to catastrophic failure,” the standard warns.
Still, there is no single “correct” classification for most deficiencies, which is why Table A.3.3.7 was inserted into NFPA 25’s advisory annex instead of its main body of requirements. At the end of the day, NFPA 25 (A.3.3.7) instructs ITM professionals to use “good judgment” and cautions that they “could require input” from the local AHJ to appropriately assess problems.
The NFPA 25 Handbook attempts to help property owners, facility managers, and fire safety professionals better understand what defines an impairment, critical deficiency, or noncritical deficiency. The 2017 edition examines dozens of field conditions that could impact a water-based fire protection system and offers a glimpse into the thought process that was used to determine the severity of the issues and how they were classified.
But the handbook emphasizes that, once again, the case studies are only meant to help fire safety professionals understand the thought process behind determining ITM classifications. It cannot serve as instructions for classifying similar problems in the field, which must ultimately be determined by the unique combination of conditions at the site.
Since classifying issues has so many shades of gray, many inspectors opt to simply record deficiencies and leave classification to a qualified individual or team. Severe impairments such as inoperable fire pumps, of course, are immediately reported.
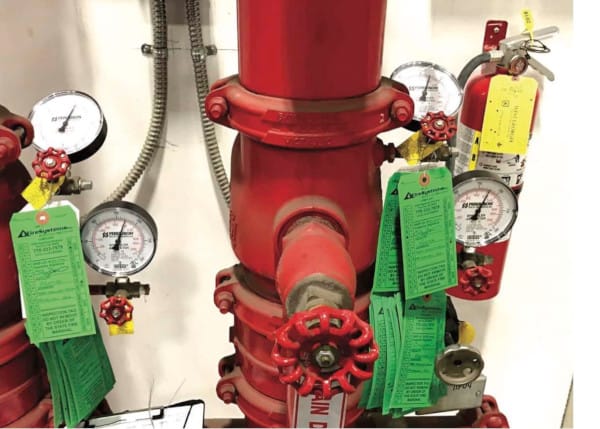
Tag, you’re it: what’s behind NFPA’s rainbow of color-coded ITM tags for standpipe and fire sprinkler inspections
Once a deficiency or impairment is discovered, color-coded tagging is often used to make abnormal conditions and completed inspections instantly apparent. But read this carefully: while NFPA 25 requires tagging to indicate that an impairment has been discovered on a water-based fire protection system, it does not specifically define a tagging structure for identifying all deficiency levels in its code.
From the 2017 edition of NFPA 25
15.3.1* A tag shall be used to indicate that a system, or part thereof, has been removed from service.
15.3.2* The tag shall be posted at each fire department connection and the system control valve, and other locations required by the authority having jurisdiction, indicating which system, or part thereof, has been removed from service.
A.15.3.1 explains that impairment tags should be weather-resistant, clearly visible, and sufficiently sized (typically 4 inches x 6 inches) to instantly alert building occupants and the fire department that all or part of the system is out of service. Tags should include information about which system is impaired, the date and time the impairment began, and the person responsible. Tags are required on the fire department connection as well as the system’s control valve so firefighters unable to gain access to the sprinkler control room don’t overlook abnormal conditions with the fire protection system the building relies on.
But many state, local, and private jurisdictions have developed a series of color-coded tags that are placed on a water-based fire protection system during a standpipe or fire sprinkler inspection. These tags identify the significance of any field conditions that are discovered and use anywhere from two to five tags and an array of color schemes.
For instance, the state of Louisiana requires green tags for system certifications, blue tags for service, yellow tags for partial impairments, red tags for full impairments, and white tags for installation. The state of Florida requires green tags for compliant systems, yellow tags for noncritical deficiencies, and red tags for critical deficiencies and impairments.
NFPA offers mixed reviews of color-coded tagging programs. It acknowledges that they foster fast, easy recognition of abnormal systems and tend to trigger a more in-depth review of ITM records by inspectors. However, NFPA 25 Annex G also raises concerns that compliance tags might provide a false sense of security if inspections are not done thoroughly; tags are not filled out completely, accurately, or consistently; or multiple contractors are hired to complete repairs noted on a single noncompliance tag but only one has completed work.
In 2017, NFPA 25 added Annex G to offer AHJs some basic guidance for addressing these concerns, and to help move the ITM industry toward a consistent system status tagging program. Its guidelines are presented as being advisory, not mandated. The annex suggests four different-colored tags should be assigned to indicate compliance, noncritical deficiencies, critical deficiencies, and impairments to water-based fire protection systems.
Here’s the color-coding system NFPA 25’s Annex G recommends for ITM tagging:
- Green tag – No deficiencies or impairments were found when inspections and tests performed at the required frequency were completed. Compliant system status was reported to the property owner.
- Yellow tag – Noncritical deficiencies were found and recorded on the ITM report.
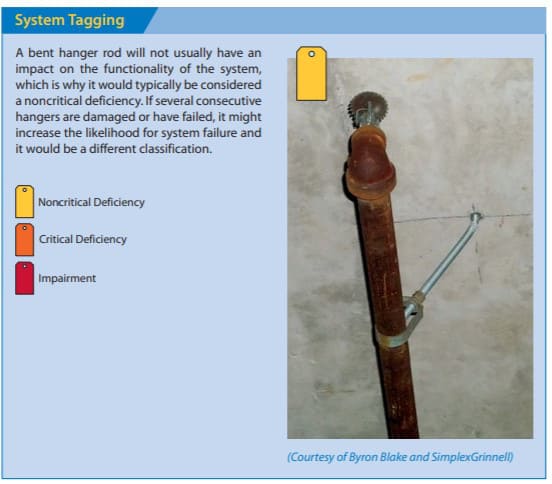
- Orange tag – Critical deficiencies were found and recorded on the ITM report.
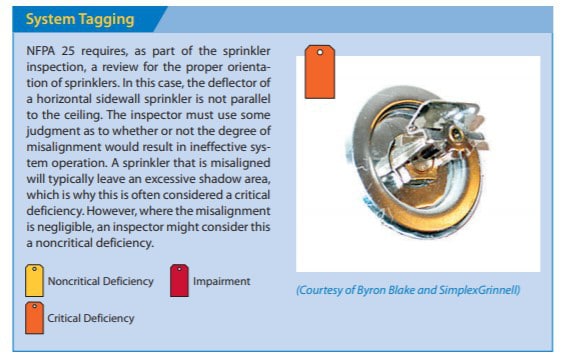
- Red tag – Impairments were found and recorded on the ITM report. NFPA 25 adds that the color-coded tagging program should be separate from the requirements outlined in Chapter 15.

The standard recommends that color-coded tags be constructed of durable, weatherproof, colorfast materials and securely attached to the main control valve of each system. If the main valve isn’t accessible—such as on underground piping, for instance—tags should be attached as close as possible to the main control valve in a place that is still highly visible and accessible, such as on a system pressure gauge. Annex G recommends that tags should at least include the following information:
- Identification of the system that the information on the tag represents
- The employer of the ITM technician, as well as any license certification information required by the AHJ
- The date ITM was performed
- ITM type and frequency
NFPA’s guidelines also include a fifth white tag that is only attached after deficiencies or impairments are repaired or corrected. The white tag is placed alongside the yellow, orange, or red tag that indicated the problem, and includes a brief description of what was done to address it. NFPA 25 emphasizes that white tags shouldn’t be attached until all appropriate inspections and tests mandated by the nature of the deficiency or impairment are completed.
This system eliminates confusion over the meaning of green compliance tags, which can then solely be used to indicate that no deficiencies or impairments were discovered during required inspections and tests, and have nothing to do with compliance after repairs.
Annex G suggests that the length of time tags remain in place should mirror NFPA 25 requirements for ITM record retention, which mandates that records be maintained for another year after the next round of the same inspection, testing, or maintenance is performed (4.3.5). The annex also suggests that only qualified ITM professionals should be able to place or remove tags on water-based fire protection systems.
But despite NFPA’s detailed tagging guidance, a consistent national system has yet to emerge and tagging requirements can still vary among individual jurisdictions. Fire safety professionals must check for locally applicable code before conducting ITM work.
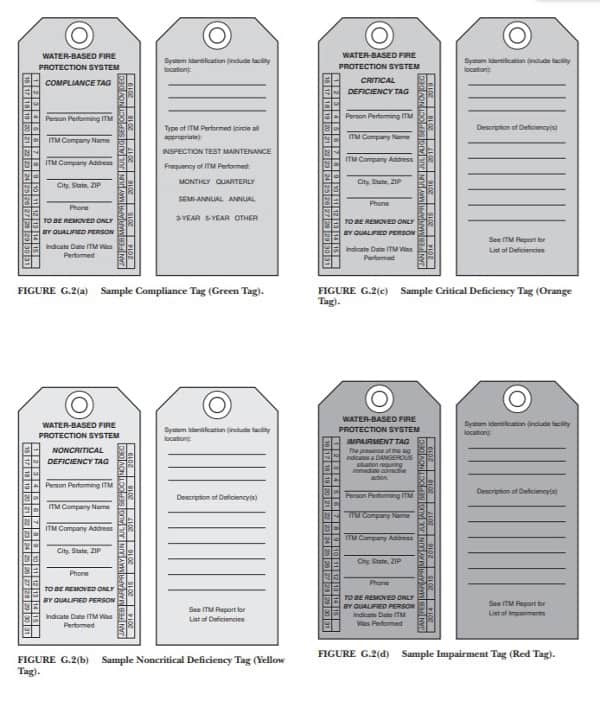
Proper classification of deficiencies and impairments ensures emergent issues will be prioritized after standpipe and fire sprinkler inspections
Water-based fire protection systems can be the difference between a catastrophic event and a controlled or quickly extinguished fire—but only if the system can function properly during an emergency. Understanding how to determine the proper classification for problems that are discovered ensures that the most emergent issues will be prioritized and properly addressed before life safety is compromised.
Need to correct deficiencies or impairments discovered in a water-based fire protection system? Our selection of commercial fire sprinklers, installation tools, pipe components, valves, and more is in stock to help you restore your fire protection systems to service.
We also encourage you to check out the benefits of software for standpipe and fire sprinkler inspections—as well as various other fire protection components. To learn exactly how it improves compliance and makes performing ITM more efficient, sign up for a free demo of Inspect Point’s fire protection ITM software.
For more information about QRFS products, call us at +1 (888) 361-6662 or email support@qrfs.com.
This blog was originally posted at blog.qrfs.com. Check us out at Facebook.com/QuickResponseFireSupply or on Twitter @QuickResponseFS. Source for the image at the top of this post: U.S. Fire Administration.