How to assess fire sprinkler corrosion and determine the right strategy for fixing it
Corrosion threatens the reliability of automatic fire sprinklers—and unfortunately, the presence of water, iron, and other metal in systems makes it nearly impossible to avoid. Fire sprinkler corrosion eats away at pipes from the inside out, often escaping notice until it’s already caused extensive and costly damage.
In this blog, we will examine what to do if you’ve uncovered corrosion in fire sprinkler pipes. We will also explore the steps you can take to prevent corrosion from causing a need for costly repairs or system replacements in the future.
Looking to repair or replace corrosion-damaged parts? Browse our selection of fire sprinkler heads, installation tools, and other system components.
What causes fire sprinkler corrosion?
If a sprinkler system is corroding, oxygen is most likely to blame. Since the first fire sprinklers, the fire protection industry has struggled with the effects of the “corrosion triangle”—oxygen, water, and metal—that forms the ultimate breeding ground for electrochemical corrosion. And the problem can start as soon as fire sprinklers are installed.
Orangey-red rust eats holes the size of pinholes or pennies into metal sprinkler pipes. At the right temperatures, the corrosive elements also contribute to microbiologically induced corrosion (MIC), allowing bacteria to colonize the internal surfaces of sprinkler systems.
A Potter Corrosion Solutions report found that as much as 90 percent of fire sprinkler corrosion is “generalized,” meaning it’s an electrochemical reaction triggered by the presence of oxygen. Between 10 and 30 percent is caused by MIC.
Corrosion causes costly service calls to fix pipes obstructed with a crust of tubercules, repair leaky holes, and remove loose scale or rust clogging sprinklers and valves and degrading the system’s flow characteristics.
Left untreated, it’s only a matter of time until corrosion triggers leaks or accidental sprinkler discharges that can cause tens of thousands of dollars in water damage to the property the system was meant to protect. Even worse, it can cause fire sprinklers to fail during a fire, putting lives at risk.
The problem is most alarming for dry sprinkler systems, which typically rely on pressurized air to keep pipes from freezing in cold temperatures by holding back the water supply. But although water isn’t supposed to infiltrate dry systems until sprinkler heads activate, it’s nearly impossible to prevent it from pooling at low points in the pipes due to condensation or after the annual trip test required by the 2017 edition of NFPA 25: Standard for the Inspection, Testing, and Maintenance of Water-Based Fire Protection Systems.
More than 70 percent of dry sprinkler systems suffer significant corrosion issues within 12.5 years of installation, the Potter report states. But while corrosion may take longer to wreak havoc in wet systems, they don’t escape unscathed: 35 percent experience significant issues after 25 years.
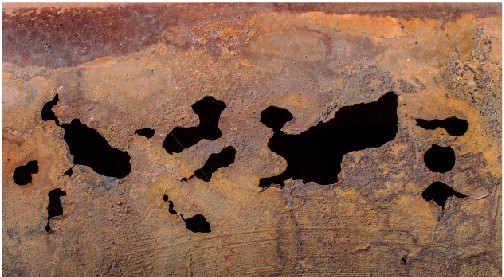
NFPA takes a proactive stance against corroded pipes
With so much at stake, it’s no surprise that the National Fire Protection Agency (NFPA) is taking a proactive approach to fire sprinkler corrosion.
The 2019 edition of NFPA 13: Standard for the Installation of Sprinkler Systems (4.2) requires property owners to share “special knowledge” with sprinkler system installers of water supply or environmental conditions that could cause corrosion to flourish. Air vents are now required on wet systems with metal pipes to release any trapped air pockets, which serve as their main catalyst for corrosion (8.1.5).
NFPA 25 requires regular inspection and testing to catch fire sprinkler corrosion at its earliest stages. (Read more about NFPA inspection requirements for sprinkler pipes.) 5.2.2 minces no words by requiring that sprinkler pipes remain “free” of leakage and corrosion.
Any tubercules or slime found in sprinkler pipes must be immediately tested for MIC (NFPA 25 14.2.1.3). NFPA 13 takes that requirement a step further, spelling out the specific steps that must occur if conditions are ripe for MIC to flourish:
From the 2019 edition of NFPA 13
5.1.5.1 Water supplies and environmental conditions shall be evaluated for the existence of microbes and conditions that contribute to microbiologically influenced corrosion (MIC). Where conditions are found that contribute to MIC, the owner(s) shall notify the sprinkler system installer and a plan shall be developed to treat the system:
(1) Install a water pipe that will not be affected by the MIC microbes
(2) Treat all water that enters the system using an approved bacterial inhibitor
(3) Implement an approved plan for monitoring the interior conditions of the pipe established time intervals and locations
(4) Install corrosion-monitoring station and monitor at established intervals
Watch this video to learn what causes MIC to form in sprinkler systems:
NFPA 13 also addresses what property owners must do if sprinkler pipes are installed under unusually corrosive conditions. Sometimes, water supplies fit for human consumption can have chemical features such as dissolved oxygen or pH levels that speed corrosion in pipes.
From the 2019 edition of NFPA 13
5.1.5.2 Water supplies and environmental conditions shall be evaluated for conditions that contribute to unusual corrosive properties. Where conditions are found that contribute to unusual corrosive properties, the owner(s) shall notify the sprinkler system installer and a plan shall be developed to treat the system using one of the following methods:
(1) Install a water pipe that is corrosion resistant
(2) Treat water that enters the system using a listed corrosion inhibitor
(3) Implement an approved plan for monitoring the interior conditions of the pipe at established intervals and locations
(4) Install corrosion monitoring station and monitor at established intervals
(5) Fill dry-pipe or preaction systems with nitrogen as a supervisory gas to mitigate against corrosion
(6) When using a generator, use an approved nitrogen generator
Should you repair or replace corroded sprinkler pipes?
Historically, the standard approach to fighting fire sprinkler corrosion has been replacement of the offending pipes. Repairs can patch smaller issues such as pinhole leaks, but sometimes they simply stick a band-aid on a bigger problem that’s quietly rotting within ceilings or behind walls.
NFPA 25 (A.5.2.2) asserts that sprinkler pipes must be kept free of corrosion that can have “a detrimental effect” on their lifespan and performance. But NFPA 25 (A.5.2.2.1) also permits “a degree of judgment” in determining whether corroded pipes should be repaired or replaced. It goes on to explain that surface corrosion “not impacting the integrity of the piping strength or raising concern of potential leakage should not warrant the replacement of piping.”
NFPA 25 (14.2) requires internal inspections of sprinkler piping every five years or as needed to monitor corrosion levels. Tests such as video-scoping the internal conditions of system piping, laboratory-testing water samples, and ultrasonic testing of pipe samples to quantify metal loss can help building owners make informed decisions about the best approach to mitigate corrosion damage. Obstruction investigations are triggered if there is sufficient evidence of foreign materials blocking sprinkler pipes (NFPA 25 14.2.1.4).
A Potter Corrosion Solution report promoted by NFPA offers guidelines for fixing corroded sprinkler pipes:
- Class I: Little damage is found; the pipe array should simply be flushed, which involves using a pressurized water source to clear sprinkler systems of potential blockages. However, NFPA 25 (5.2) asserts that piping should be thoroughly cleaned and hydrostatic testing should be performed to ensure that corrosion didn’t seriously weaken the pipe’s walls after flushing.
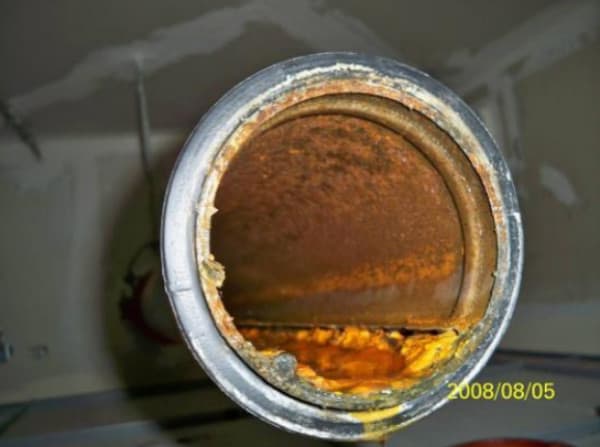
- Class II: Medium damage is found, meaning some but not all pipes show increased damage. Those specific pipes should be replaced.
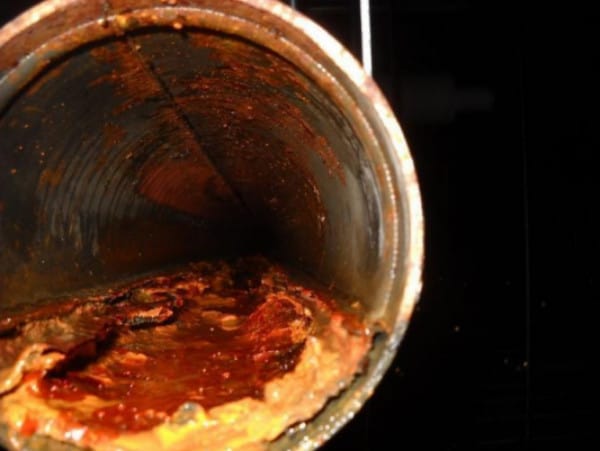
- Class III: Considerable corrosion and deposits are present; the complete pipe array or significant parts of it should be replaced.
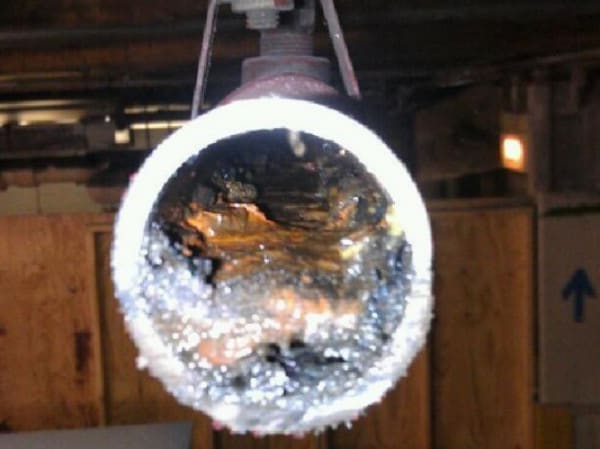
Replacing sprinkler pipes that stretch throughout a property is no small task, incurring high costs and potential business interruptions. Many property owners opt to simply repair fire sprinkler leaks until they become enough of a nuisance or expense that it requires a better solution.
Sprinkler contractors can use chemical corrosion inhibitors to treat water in the pipes and kill MIC-causing bacteria. Some also use chemical corrosion inhibitors as a barrier between the water and the metal to slow or stop corrosion.
But some industry sources have raised concerns about injecting chemical corrosion inhibitors into water-based fire sprinklers, wondering about the effects of the chemicals on sprinkler components, risks to emergency response personnel when the water sprays during a fire, and the effectiveness of these inhibitors in stagnant environments like sprinkler pipes, where the corrosion triangle is so prevalent.
Sometimes corrosion becomes so invasive that a full system replacement is the only option, but it’s important to note that localized corrosion doesn’t generally warrant such extensive measures. Surgical replacement of the failing piping can often fix the problem, followed by the implementation of a corrosion-control strategy.
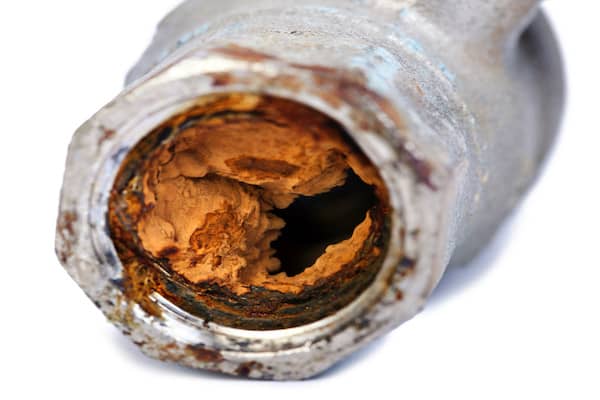
Let’s consider four main factors that can impact a property owner’s decision to make a quick repair or fully replace corroded sprinkler pipes:
- Cost. Potter Corrosion Solutions puts the average cost of repairing small leaks between $800 and $1,200. Full pipe replacements average between $6 and $8 per square foot, including labor, material, and equipment, according to Engineered Corrosion Solutions. But both those averages can surge upward based on location, the current price of steel, and whether emergency repairs are needed during off-hours. Facilities with hard-to-reach areas or high ceilings that require lift equipment may experience higher labor costs as well. Properties in remote areas may also incur higher costs for contractors’ travel time, making the risk of ongoing repairs cost-prohibitive.
- History of problems. The repair or replacement record of the sprinkler system should also weigh into the decision. Property owners who are repairing corrosion-related leaks on a frequent basis will ultimately save money by replacing the pipes and eliminating the source of the problem. Along the same lines, business owners who are suffering repeated business disruptions due to leaky sprinklers might also lean toward a solution that ensures a lower likelihood of future problems. Environments where water leaks could cause expensive or irreparable damage, such as museums, might also consider moving forward with pipe replacements instead of repairs if corrosion is revealed.
- System age. The remaining useful life of the sprinkler system is a significant factor when evaluating whether repair or replacement is more cost-effective. It’s also important to consider whether advancements in fire sprinkler technology since an older system was installed could dramatically change the outcome of a disastrous fire. Finally, new and older systems can sometimes be problematic to hook together, making a repair a more viable alternative if the damage is centralized to a small area.
- The extent of the damage. The extent of corrosion in the pipes impacts whether repair or replacement makes sense. Corrosion located in a spot that makes it difficult to just replace a section of a system matters as well. Dry systems that rely on pressurized air have copious amounts of oxygen in their pipes, which can speed the spread of corrosion and increase the likelihood that repairs won’t avoid replacement a few short years down the road. Severe corrosion in wet sprinkler pipes is often localized to places air is trapped, such as system high-points. When corrosion occurs on such a small scale, a repair service may be enough to fix the damage.
4 strategies for preventing future pipe corrosion
Corrosion remains one of the biggest challenges facing the fire protection industry—and unfortunately, no fire sprinkler system is completely immune to it. But many property owners fail to take proactive measures to mitigate the problem until significant damage is detected. A corrosion control strategy is key to avoiding expensive repairs and replacements in the future.
These four tips can help control corrosion in metal sprinkler pipes:
Replace pressurized air with nitrogen in dry and preaction sprinkler systems
Removing oxygen from sprinkler systems and replacing it with pure nitrogen cuts a critical leg off the corrosion triangle. Nitrogen is an inert gas, meaning it doesn’t react with water or metal to cause electrochemical corrosion—or create the perfect conditions for MIC to grow. Nitrogen has been proven to extend the life of dry sprinkler systems 5.3 times longer, according to Potter’s research. It also makes a dramatic difference in long-term maintenance and repair/replacement costs over the life of a building. Want to learn more about replacing oxygen with nitrogen in dry systems? Read our previous blog on the trend toward nitrogen in fire sprinklers.
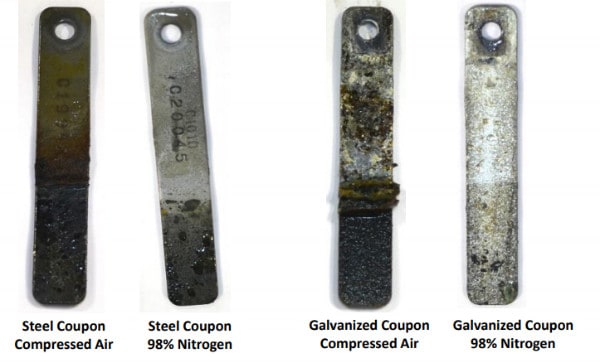
Be wary of galvanized steel piping
Galvanized steel pipes feature walls coated with zinc. Since zinc is more reactive than steel, it was intended to serve as a sacrificial material to corrosion, creating a protective layer of scale build-up while protecting the pipe underneath. But concentrated corrosion action around small holes in the zinc may actually cause galvanized pipes to fail faster than black steel.
Studies have shown pinhole leaks developing in dry systems with galvanized steel pipes within two years of installation—and ruptures within four years, according to Potter Corrosion Solutions. In 2016, the U.S. Department of Defense banned the use of galvanized steel piping in the majority of its fire protection systems. It also required black steel to replace galvanized steel when additions, replacements, or relocations are made.
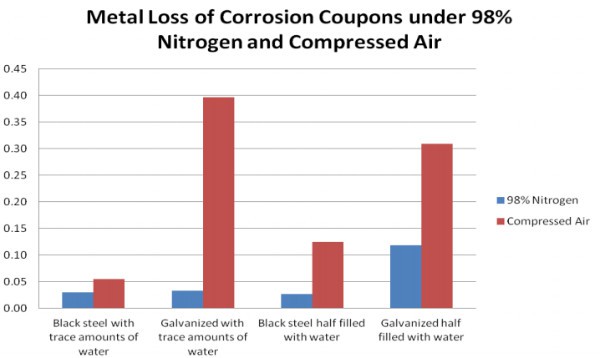
Install air vents in wet systems
Venting valves are a simple, cost-effective solution for reducing oxygen corrosion, releasing air that would otherwise be trapped in wet sprinkler pipes. NFPA 13 (16.7) requires air vents to be located near a high-point in the system, enabling corrosive oxygen to escape through a manual valve that’s at least a ½-inch in size, an automatic air vent, a remote inspector’s test valve, or other approved means. Vents may be automatic—shutting off when water reaches the vent—or manual, requiring the valve to be closed after excess air is removed.
Consider corrosion monitoring
Required by NFPA 13 (5.1.5.1 and 5.1.5.2) when environmental or water supply conditions create a higher risk of corrosive activity, corrosion monitoring equipment is designed to catch corrosion at its earliest stages—before it leads to expensive repairs, property damaged by leaking water, or system failures that can cause catastrophic losses during a fire. Monitoring solutions can keep a watchful eye on metal loss or gas composition in wet or dry systems, automatically sending an alert if corrosive activity begins. They are typically installed throughout the system where corrosion is most likely to form.
Minor fire sprinkler corrosion can become a major catastrophe if it’s not caught early and properly fixed
Over time, fire sprinkler corrosion is inevitable in nearly every system—especially those using metal pipe. And minor issues can turn into major catastrophes if they aren’t caught early and properly fixed. Taking time to understand the extent of the damage and other relevant factors can help property owners make an informed decision about the best path for mitigating corrosion in sprinkler pipes.
Looking to repair or replace corrosion-damaged parts? Browse our selection of fire sprinkler heads, installation tools, and other system components. We also sell CPVC pipe fittings that have little chance of corrosion and are appropriate for new installations or system replacements in light-hazard environments.
Questions about QRFS products? Call us at +1 (888) 361-6662 or email support@qrfs.com.
This blog was originally posted at blog.qrfs.com. If this article helped you learn how to avoid and shut down accidental sprinkler discharges, check us out at Facebook.com/QuickResponseFireSupply or on Twitter @QuickResponseFS.
Thank you very much for sharing your thoughts with us.