The steps to performing annual testing of individual fire pump parts
Fire pumps are needed when the existing pressure from a water supply isn’t enough for sprinkler systems to perform effectively. If a fire pump isn’t working properly, water from the sprinklers will simply trickle out, having little or no effect on a fire.
In our previous blog on fire pump annual testing, we took an in-depth look at the annual fire pump flow test requirements. In this blog, we examine the National Fire Protection Association (NFPA) requirements and best practices for annually testing fire pump components. These guidelines apply to fire pumps connected to every type of water-based sprinkler system, from wet to dry sprinklers.
Are you looking to buy parts for your building’s sprinkler system? Feel free to browse our selection of sprinkler system components and accessories, including commercial and residential sprinkler heads, installation tools, fire extinguishers, heavy-duty head guards that protect sprinklers from accidental damage or vandalism, and so much more.
Diesel-engine fire pumps require extra testing
As soon as fire sprinklers are activated, the pressure in a water-based system significantly drops. Fire pumps automatically kick into gear whenever the water pressure sinks below a certain threshold, maintaining enough pressure to keep the water flowing during a fire.
When they are functioning properly, fire pumps quickly deliver enough water to douse a fire before it has a chance to spread. They are often used in high-rise buildings, where pushing water to upper floors within seconds requires assistance, and big, low-rise structures like warehouses, where the exceedingly large coverage area makes it challenging to regulate water pressure. Many buildings that use water storage tanks as part of their sprinkler system also need fire pumps to generate the necessary pressure in the event of an emergency, as well as properties where the municipal supply can’t maintain enough pressure on its own.
Fire pumps are expensive and intricate machinery that require regular inspection and testing to ensure they function properly when they’re needed most. The 2017 edition of NFPA 25: Standard for the Inspection, Testing, and Maintenance of Water-Based Fire Protection Systems addresses minimum testing requirements for fire pumps. Additional requirements are outlined in NFPA 20: Standard for the Installation of Stationary Pumps for Fire Protection.
While the complexity of fire pump testing demands a qualified professional, property owners must maintain a complete written report of fire pump test results (8.4). Our previous blog on fire pump testing details what NFPA 25 requires for these reports.
Let’s take a look at the annual tests NFPA 25 requires for fire pump components, which are typically performed in conjunction with the annual fire pump flow test. While electric motor-driven and diesel engine-driven fire pumps are the most common fire pumps in use today, steam turbine engines are still found in rarer cases. There are more regulations for diesel drives than the other kinds of pumps due to their extra complexities such as fuel systems.
Annual fire pump tests
Testing diesel fuel
Commercial distillate fuel oils used in modern diesel engines can quickly degrade during storage. Many environmental or fuel-quality conditions have detrimental effects as fuel is handled and stored, including naturally-occurring gums, waxes, soluble metallic soaps, dirt, and temperature extremes. Water that finds its way into steel fuel storage tanks can also trigger corrosion, prompting microbiological growth where the fuel and water interface that reduces fuel quality.
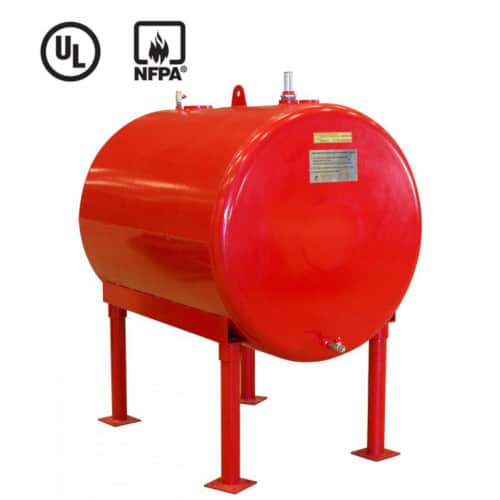
Poor fuel quality is a serious concern for diesel fire pumps, resulting in clogged filters and other damage that can eventually cause the entire system to fail. Fuel maintenance and testing that begins on the day of installation and the first fill is critical for the operation, efficiency, and longevity of a fire pump. Standards listed below by ASTM International, formerly the American Society for Testing and Materials, establish guidelines for testing fuel.
Fuel that is deemed compromised during testing must be reconditioned or replaced. The inside of the supply tank should also be cleaned, and the fire pump engine’s fuel filter should be changed.
From the 2017 edition of NFPA 25
8.3.4 Diesel Fuel Testing and Maintenance.
8.3.4.1 Diesel fuel shall be tested for degradation no less than annually.
8.3.4.1.1* Fuel degradation testing shall comply with ASTM D975, Standard Specification for Diesel Fuel Oils, or ASTM D6751, Standard Specification for Biodiesel Fuel Blend Stock (B100) for Middle Distillate Fuels, as approved by the engine manufacturer, using ASTM D7462, Standard Test Method for Oxidation Stability of Biodiesel (B100) and Blends of Biodiesel with Middle Distillate Petroleum Fuel (Accelerated Method).
8.3.4.2* If diesel fuel is found to be deficient in the testing required in 8.3.4.1.1, the fuel shall be reconditioned or replaced, the supply tank shall be cleaned internally, and the engine fuel filter(s) shall be changed.
8.3.4.2.1 After the restoration of the fuel and tank in 8.3.4.2, the fuel shall be retested every 6 months until experience indicates the fuel can be stored for a minimum of 1 year without degradation beyond that allowed in 8.3.4.1.1.
Testing electronic fuel management control systems
Fuel management systems are designed to effectively monitor and manage the use of fuel in diesel engine-driven fire pumps. To ensure consistent operation of a diesel fire pump during an emergency, NFPA requires two automatic electronic control modules (ECMs) to be installed with electronic fuel management systems in case the first one fails. Here’s how to test the backup ECM (NFPA 25: A.8.3.3.13):
To test the operation of the alternate electronic control module (ECM), move the ECM selector switch to the alternate ECM position. This should trigger an alarm on the fire pump controller. When the fire pump’s engine is started, it should operate normally with all functions. To complete the test, shut the engine down and switch back to the primary ECM. Restart it briefly to verify the primary ECM is selected.
To verify the operation of the redundant sensor, disconnect the wires from the primary sensor while the engine is running. There should be no change in the engine operation. Next, reconnect the wires to the primary sensor and disconnect them from the redundant sensor. There should still be no change in the engine operation. Reconnect the wires, and repeat the process for all primary and redundant sensors on the engines. ITM professionals should also test whether disconnecting and reconnecting wires to the sensors can be done while the engine isn’t running, and restart the engine after each disconnect/reconnect to verify engine operation.
From the 2017 edition of NFPA 25
8.3.3.13* Where engines utilize electronic fuel management control systems, the backup electronic control module (ECM) and the primary and redundant sensors for the ECM shall be tested annually.
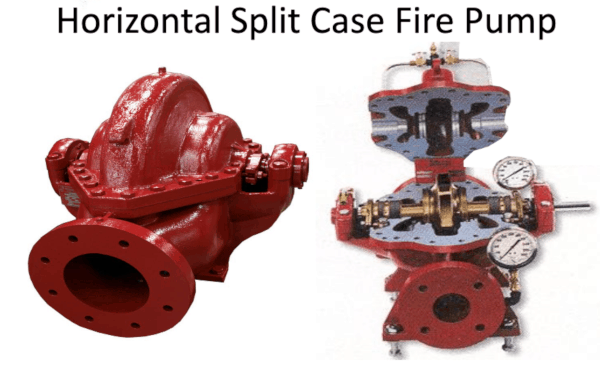
Testing positive displacement pumps
Centrifugal fire pumps—think familiar styles like vertical inline design, end suction, and horizontal split-case design—are commonly used in water-based fire sprinkler systems. By using a rotating impeller with curved blades to move water through centrifugal force, these pumps can move large quantities of liquids at high flow rates.
Positive displacement fire pumps move a fixed amount of fluid at regular intervals, trapping a certain amount of water before pushing it out through a discharge line. These pumps are generally more costly than centrifugal pumps and benefit high-pressure/low-flow-rate applications. They can also pump air, making them a popular choice for special hazard fire protection systems like foam and water-mist sprinklers.
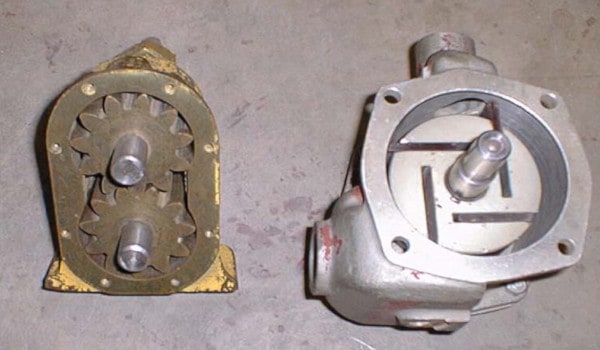
Annual testing of positive displacement pumps is generally performed by following the steps for flow testing from NFPA 25 (Section 8.3) that are explained in our previous blog on fire pump annual testing. But since positive displacement pumps operate differently from centrifugal pumps, the following guidelines are also offered:
From the 2017 edition of NFPA 25
8.3.5 Positive Displacement Pumps.
8.3.5.1 Except as provided in 8.3.5.1 through 8.3.5.7, positive displacement pumps shall be tested in accordance with 8.3.1 through 8.3.3.
8.3.5.2 The pump flow for positive displacement pumps shall be tested and determined to meet the specified rated performance criteria where only one performance point is required to establish positive displacement pump acceptability.
8.3.5.3 The pump flow test for positive displacement pumps shall be accomplished using a flowmeter or orifice plate installed in a test loop back to the supply tank, to the inlet side of a positive displacement water pump, or to drain.
8.3.5.4 The flowmeter reading or discharge pressure shall be recorded and shall be in accordance with the pump manufacturer’s flow performance data.
8.3.5.5 If orifice plates are used, the orifice size and corresponding discharge pressure to be maintained on the upstream side of the orifice plate shall be made available to the authority having jurisdiction.
8.3.5.6 Flow rates shall be as specified while operating at the system design pressure. Tests shall be performed in accordance with HI 3.6, Rotary Pump Tests.
8.3.5.7 Positive displacement pumps intended to pump liquids other than water shall be permitted to be tested with water; however, the pump performance will be affected, and manufacturer’s calculations shall be provided showing the difference in viscosity between water and the system liquid.
Testing alignment of the pump and driver
When fire pump couplings are misaligned, they are much more likely to fail. NFPA 25 requires inspectors to test the alignment of the pump and driver during annual fire pump testing.
Pumps and drivers shipped from the factory with both machines mounted on a common baseplate are usually aligned before shipment. But read this carefully: since all baseplates are somewhat flexible, they can’t be relied upon to maintain factory alignment. Realignment should be performed during installation and re-inspected periodically. There are many factors that can affect alignment, including thermal expansion and equipment maintenance.
From the 2017 edition of NFPA 25
8.3.6.4* Parallel and angular alignment of the pump and driver shall be inspected during the annual test, and any misalignment shall be corrected.
There are two common forms of misalignment between a fire pump’s pump and driver shafts: angular misalignment, when the shafts with axes are concentric but not parallel, and parallel misalignment, when they are parallel but not concentric. These are the steps to test the coupling alignment of the driver and pump shafts on a fire pump (NFPA 25: A.8.3.6.4):
- Angular alignment. Insert a taper gauge or feeler gauge at four points between the coupling faces of the two shafts. Compare the distance between the faces at four points spaced at 90-degree intervals around the coupling parts. The unit is in angular alignment when the measurements show that the coupling faces are the same distance apart at all points.
- Parallel alignment. Place a straight edge across both coupling rims at the top, bottom, and on both sides. Make sure the straight edge is parallel to the axes of the shafts. The unit is in parallel alignment when the straight edge rests evenly on the coupling rim at all positions.
When conducting these tests, allowances might be necessary for temperature changes and coupling parts that don’t have the same outside diameter. To fix misalignments, add shims under the motor mounting feet and recheck the alignment of the coupling halves after every change—adjustments in one direction might upset adjustments already made in a different direction. A small amount of misalignment is permitted but varies according to the type of pump and driver, as well as the coupling manufacturer, model, and size.
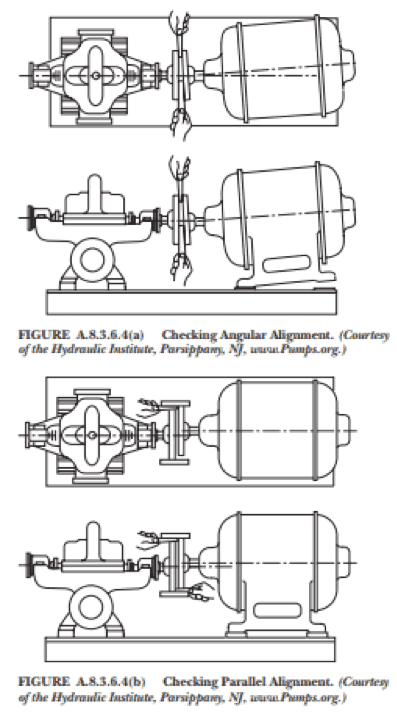
Other annual fire pump tests
Routine testing of standby generators that support fire pumps is also required during annual fire pump tests. NFPA 110: Standard for Emergency and Standby Power Systems sets detailed requirements for testing generators relied on by the fire pump. Environmental conditions in the fire pump room should also be tested annually to ensure they won’t impact pump performance, including heating, lighting, and ventilation.
From the 2017 edition of NFPA 25
8.3.6.1* Engine generator sets supplying emergency or standby power to fire pump assemblies shall be tested routinely in accordance with NFPA 110.
8.3.6.3 Tests of appropriate environmental pump room space conditions (e.g., heating, ventilation, illumination) shall be made to ensure proper manual or automatic operation of the associated equipment.
Cleaning suction screens after testing
Suction screens should be cleaned at the completion of annual fire pump testing. But it’s worth noting that suction screens should be inspected and cleared of any debris or obstructions that could impact fire pump performance as frequently as daily during periods of unusual water supply conditions like floods.
From the 2017 edition of NFPA 25
8.3.3.12* Suction Screens. After the waterflow portions of the annual test or fire protection system activations, the suction screens shall be inspected and cleared of any debris or obstructions.
What if the fire pump fails a test?
NFPA 25 (8.3.7.2.3) addresses conditions that must be achieved for a fire pump to pass its annual flow test, including the ability to meet full sprinkler system demand and test results that don’t deviate by more than five percent from the fire pump’s nameplate data or original unadjusted field test curve. But there are many other conditions that can cause fire pumps to fail their annual tests, including:
From the 2017 edition of NFPA 25
8.3.7.2.5 For electric motor-driven fire pumps operating at constant speed, the current at each flow rate test point and at each phase shall not exceed the product of the electric motor service factor and the full-load amperage rating of the motor.
8.3.7.2.6 Where the current at each flow rate test point and at each phase exceeds the product of the electric motor service factor and the full-load amperage rating of the motor, the source of the problem shall be identified and corrected.
8.3.7.2.7 For electric motor-driven fire pumps operating at varying voltage, the product of the test voltage and the current at each test point and on each phase shall not exceed the product of the voltage and the full-load current times the motor service factor.
8.3.7.2.8 Where the product of the test voltage and the current at each test point and on each phase exceeds the product of the voltage and the full-load current times the motor service factor, the source of the problem shall be identified and corrected.
8.3.7.2.9 Voltage readings at the motor within 5 percent below or 10 percent above the rated (i.e., nameplate) voltage shall be considered acceptable.
If a failure occurs, the fire pump’s owner must be notified, and the issue investigated and corrected. Once the repair is made, the fire pump should be retested for proper performance. The owner must create and maintain a report documenting all repairs and corrections.
8.3.7.2.4* Upon failure to meet the criteria in 8.3.7.2.3, the following actions shall occur:
(1) The owner shall be notified.
(2) An investigation shall be conducted to reveal the cause of the degraded performance.
(3) The deficiency shall be corrected.
8.3.7.2.10 A written or electronic record of the results of the investigation and the corrective action shall be prepared and maintained by the owner.
8.6.1 Whenever a component in a fire pump is adjusted, repaired, rebuilt, or replaced, the tests required to restore the system to service shall be performed in accordance with Table 8.6.1.
8.6.2 NFPA 20 shall be consulted for the minimum requirements for design, installation, and acceptance testing.
The table below provides examples for classifying conditions needing repair or correction that are identified by annual fire pump testing (click the caption below it to see a larger version):
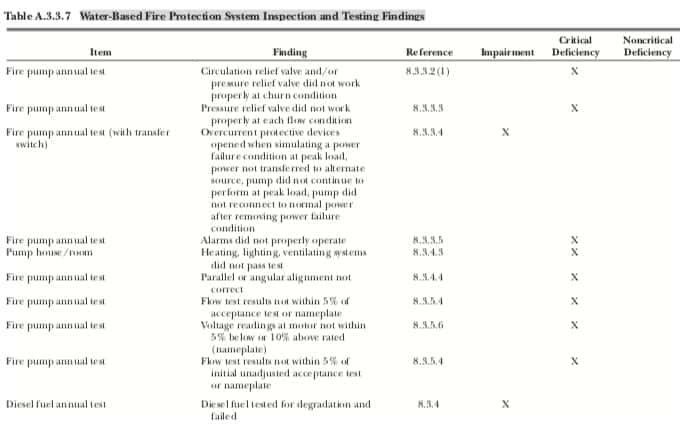
Keep sprinkler systems up and running in an emergency with annual fire pump tests in NFPA 25
With costs that start at $20,000 and can pass $1 million when suction tanks are required, fire pumps rank as the most expensive parts of water-based sprinkler systems. But their presence is essential at sites that need enhanced water pressure or don’t have a public water supply. Comprehensive annual testing ensures that the investment property owners make in fire pumps is repaid with reliable, automatic performance during a fire.
To keep the rest of a fire sprinkler system performing as intended, check out our selection of sprinkler system components and accessories, including commercial and residential sprinkler heads, installation tools, fire extinguishers, heavy-duty head guards that protect sprinklers from accidental damage or vandalism, and so much more.
If you have questions or you need help finding an item, call at 888.361.6662 or email support@qrfs.com.
This blog was originally posted at blog.qrfs.com. Check us out at Facebook.com/QuickResponseFireSupply or on Twitter @QuickResponseFS.
Is there anyway to check the alignment on a vertical fire pump? Just wondering if there is a special way and just don’t know about it.
Ed — Not that we are aware of off-hand. Best of luck!
I was asked this question on a steam turbine driven fire which tool is needed for proper testing?
bourodon tube tester; multimeter; tachometer; 3-valve differential tester.
Thinking it’s a tachometer due variable speeds can’t find solid answer for this question
Your Thoughts?
Unfortunately, your question is a bit technical and specific for this format. You can try our Ask a Fire Pro service and get the well-researched perspective of a pro, however. Thanks for reading!
If a fire pump is taken out of service for maintenance on the pump due to out of spec oil indications; is repaired; and then run at the facility without any issue; does it have to be retested to ensure it meets the annual test (<5% of mfg performance curves)?
Thanks,
Bob Sansone
860-916-1467
Bob — Unfortunately, we don’t typically provide definitive answers on an ITM compliance question in this forum, especially for very specific scenarios. We’d advise you to consult with a local fire protection pro or authority having jurisdiction. Thanks for reading.