CPVC solvent cement (mistakenly called CPVC glue) requires little time to set, but cure times vary from mere minutes to days depending on climate and pipe size
Pipes made from CPVC, or chlorinated polyvinyl chloride, have become a popular choice in residential fire sprinkler systems as well as other light hazard settings. Low costs, corrosion resistance, and a heat-resistant design have caused CPVC to expand from a favored choice for hot-water plumbing to a mainstay in fire protection for homes, apartments, and other living spaces. But for installers, CPVC poses one big challenge: not all CPVC pipe consists of the same chemical compounds. Consequently, contractors must choose their joining method—CPVC solvent cement—in accordance with manufacturers’ guidelines.
In this article, we explain the chemical makeup of CPVC and provide a few important guidelines for installers choosing CPVC glues. We then provide a list of drying times—bot to set and cure—for so-called “glues” used with leading CPVC brands like BlazeMaster®, FlameGuard®, and ThermaFit Industries.
If you’d like, you can view our selection of one-step solvent cement for CPVC now, or browse our entire catalog of CPVC pipe and accessories.
CPVC solvent cement, or “CPVC glue,” forms a chemical bond between pipes and fittings
What contractors and retailers often refer to as CPVC “glue” isn’t glue at all. Glue sticks materials together intact. Pipes or fittings joined this way connect only to the adhesive material—not each other directly. Typically, these substances consist of chemicals that aren’t at all like the pieces they hold together. Those differences in chemical composition mean that glued joints may fail when faced with stresses the pipes themselves can withstand.
Unlike glue, CPVC solvent cement functions as a chemical weld. The molecules of pipes and fittings joined with these compounds unite to create a single plastic part. Initially, solvents in this cement break down the outer membrane of pipes and fittings, preparing them to combine chemically. As the process continues, CPVC within the adhesive—or CPVC resin—fills in empty spaces. Stabilizers and fillers increase the strength, durability, and appearance of the weld. The result: a single piece of thermoplastic with the exact dimensions and shape needed.
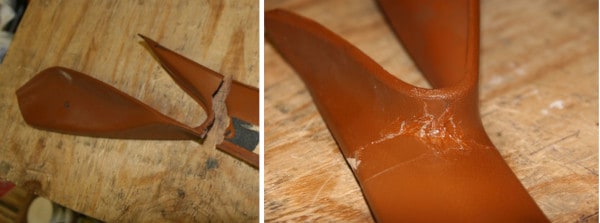
Listings and product documentation specify acceptable choices for CPVC cement
There’s no universal CPVC solvent cement. The “glue” that holds fittings together consists of chemical bonds between CPVC molecules. But different brand-name CPVC parts vary at the molecular level, impacting performance and chemical resistance. As such, it’s up to manufacturers to determine which cements work with their CPVC products—particularly when those products are part of a fire sprinkler system.
Many U.S. states and cities have rules for CPVC pipe based on codes from the National Fire Protection Association (NFPA), including:
- NFPA 13: Standard for the Installation of Sprinkler Systems
- NFPA 13D: Standard for the Installation of Sprinkler Systems in One- and Two-Family Dwellings and Manufactured Homes
- NFPA 13R: Standard for the Installation of Sprinkler Systems in Low-Rise Residential Occupancies
All three of these standards allow for the use of CPVC pipe in a fire sprinkler system only in accordance with the product’s listings (a form of product evaluation, testing, and certification) and the manufacturer’s instructions.
From the 2016 edition of NFPA 13R
5.2 Aboveground Piping and Equipment.
5.2.3.1.1 Listed nonmetallic pipe shall be installed in accordance with its listing limitations, including installation instructions.
A nearly Identical provision can be found in the 2019 edition of NFPA 13 (section 7.4.3) and the 2016 edition of NFPA 13D (5.2.3.1). These listings and installation instructions specify the choice of CPVC cement, restricting contractors’ choices to one of a handful of options. Take, for example, these guidelines from ThermaFit Industries (TFI), a California-based manufacturer of CPVC pipe and fittings:
Thermalfit [sic] CPVC fittings are for assembly using one step solvent cement manufactured by IPS Corporation identified as Victaulic FireLock 899, IPEX BM-5, TYCO TFP-500, Central CSC-500, Spears FS-5, and Nibco FP-1000.
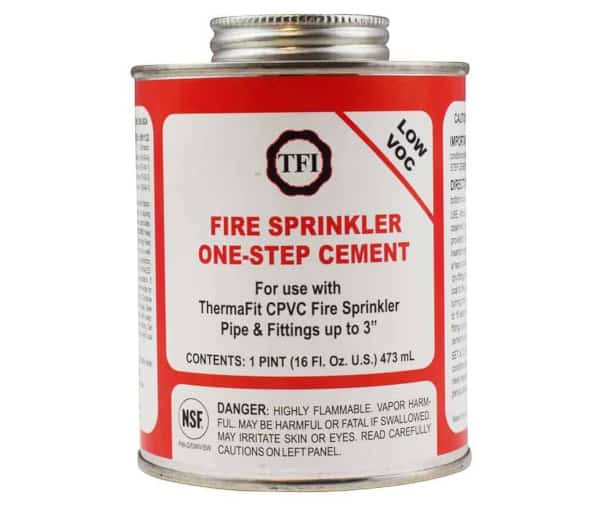
How long it takes for CPVC glue to set or cure depends on the climate, pipe size, and other factors
A joint formed with CPVC cement dries in two ways: it sets (at which point the joint may be handled or placed under limited stress) and cures (bonds enough for use). The three biggest factors in these drying times for CPVC cement are:
- The size of the pipe, tee, elbow, coupling, or other parts being joined
- Ambient temperature
- Humidity
- Test pressures
Curing and drying times for “CPVC glue” increase with pipe size
Small pipes and fittings can fuse faster and at lower temperatures than their larger counterparts. At the lowest test pressure described in ThermaFit’s documentation—100 pounds per square inch (PSI)—a 3/4” pipe cures in as little as 15 minutes, while a 2 1/2” pipe can take 32 times as long (8 hours).
Especially high or low temperatures can make bonding impractical or impossible
CPVC joints set and cure quickly at temperatures between 60- and 120-degrees Fahrenheit. A 1” pipe may set in as little as 15 minutes at 60 degrees but will take 30 minutes at lower temperatures. At temperatures under 40 degrees, a 3/4” pipe may take as long as two days to fully cure. In short, when temperatures drop, curing times grow (and at a dramatic pace for pipe sizes exceeding 1”). In fact, ThermaFit’s guidelines state that 2”, 2 1/2”, and 3” sizes may never be dried at temperatures under 40 degrees.
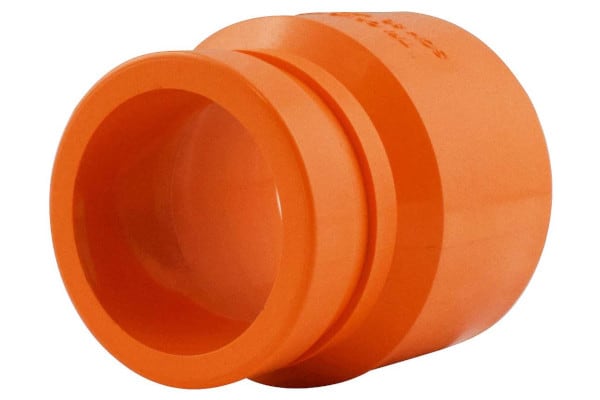
However, high temperatures—even those between 60 and 120 degrees—can be a source of trouble for installers. When temperatures exceed 90 degrees in direct sunlight, solvent cement may become too thin to work with or dry too quickly. At best, excess cement will be squandered as it falls from the applicator and, at worst, it may run off of pipes and fittings, leaving too little on the pipe.
Humidity substantially increases curing times
While it’s rarely specified, highly humid environments can prevent the solvent in CPVC cement from evaporating—which prevents the chemical weld from forming. In humid environments, curing times may grow by 50%.
Expected test pressures can make the difference between hours and days of drying
Contractors conduct acceptance tests when fire sprinkler systems are first installed. During these tests, pumps force pressurized water into the piping system to ensure that pipes are sufficiently leak-proof. The pressure applied varies with the system’s working pressure, defined as the maximum pressure expected for the system under normal circumstances (NFPA 13, section 3.3.216).
As required test pressures grow, drying times increase. At 100 PSI and temperatures under 40 degrees Fahrenheit, a 1 1/4” CPVC pipe can cure in 2 hours. At 200 PSI, that figure becomes 120 hours, and at 225 PSI, curing takes 10 days.
CPVC pipes and fittings made by FlameGuard, BlazeMaster, and ThermaFit Industries have nearly identical curing times and choices for CPVC cement
There are differences between brand-name CPVC products—in terms of long-term strength, durability at high temperatures, and composition—but, for the most part, curing isn’t one of them. Documentation from Viking Plastics, Spears Manufacturing, and ThermaFit Industries (TFI) provide similar lists of compatible cements and pre-test curing times. Those times are compiled in the table below, along with manufacturer-recommended drying or “set” times and listed cements.
BlazeMaster (Viking Plastics) CPVC
Viking BlazeMaster-compatible CPVC solvent cements include:
- Spears FS-5 One-Step Low VOC Solvent Cement
- NIBCO FP-1000 One-Step Cement
- IPEX BM5 One-Step Cement
- Hershey HVC-500 Cement
- Victaulic Style #899 FireLock One-Step Solvent Cement
- Tyco TFP-500 One-Step Solvent Cement
How long the CPVC “glue” takes to set: 1-5 minutes
FlameGuard (Spears Manufacturing) CPVC
Spears-compatible CPVC solvent cements include:
- Spears FS-5 One-Step Low VOC Solvent Cement
- IPEX BM5 One-Step Cement
- Central Sprinkler CSC-500 Cement
- Tyco TFP-500 One-Step Solvent Cement
Initial dry time (set time) for CPVC “glue”: At least 5 minutes
ThermaFit Industries (TFI) CPVC
ThermaFit-compatible CPVC solvent cements include:
- TFI Fire Sprinkler One-Step Cement
- Spears FS-5 One-Step Low VOC Solvent Cement
- NIBCO FP-1000 One-Step Cement
- IPEX BM5 One-Step Cement
- Central Sprinkler CSC-500 Cement
- Victaulic Style #899 FireLock One-Step Solvent Cement
- NIBCO FP-1000 One-Step Cement
Time required for CPVC “glue” to set/dry: At least 5 minutes
Curing Times for Selected ThermaFit Industries, FlameGuard, and BlazeMaster-type CPVC Pipes and Fittings
|
|||||||||
Test Pressure (Max) |
Nominal Pipe Size (Metric) |
Ambient Temperature | |||||||
60F to 120F (16C to 49C) |
40F to Less Than 60F (4.4C to <16C) | 0F to Less Than 40F (-17.8C to <4.4C) |
|||||||
225 PSI / 15.5 BAR |
3/4″ (DN20) |
1 hour | 4 hours | 2 days | |||||
1″ (DN25) |
1 1/2 hours | 4 hours | 2 days | ||||||
1 1/4″ & 1 1/2″ (DN32 & DN40) |
3 hours | 1 1/3 days (32 hours) | 10 days | ||||||
2″ (DN50) |
8 hours | 2 days | Raise temperature to cure | ||||||
2 1/2″ & 3″ (DN65 & DN80) |
1 day | 4 days | Raise temperature to cure | ||||||
200 PSI / 13.8 BAR |
3/4″ (DN20) |
45 minutes | 1 1/2 hours | 1 day | |||||
1″ (DN25) |
45 minutes | 1 1/2 hours | 1 day | ||||||
1 1/4″ & 1 1/2″ (DN32 & DN40) |
1 1/2 hours | 16 hours | 5 days | ||||||
2″ (DN50) |
6 hours | 1 1/2 days | Raise temperature to cure | ||||||
2 1/2″ & 3″ (DN65 & DN80) |
8 hours | 3 days | Raise temperature to cure | ||||||
100 PSI / 6.9 BAR |
3/4″ (DN20) |
15 minutes | 15 minutes | 30 minutes | |||||
1″ (DN25) |
15 minutes | 30 minutes | 30 minutes | ||||||
1 1/4″ (DN32) |
15 minutes | 30 minutes | 2 hours | ||||||
*1 1/2″ (DN40) |
*1 1/2 hours | *16 hours | *120 hours | ||||||
*2″ (DN50) | *6 hours | *1 1/2 days | *Raise temperature to cure | ||||||
*2 1/2″ & 3″ (DN65 & DN80) |
*8 hours | *3 days | *Raise temperature to cure | ||||||
Viking BlazeMaster CPVC and Spears FlameGuard CPVC products at 1 1/2″, 2″, 2 1/2″, and 3″ sizes may not be tested at 100 PSI. Instead, test at either 200 PSI or 225 PSI. |
While it doesn’t always dry quickly, CPVC solvent cement makes forming joints simple
Since the 1980s, CPVC’s presence in water-based systems has rapidly increased, displacing metal pipe in plumbing and residential fire protection systems alike. Ease of installation is one of the driving forces behind that growth—and CPVC cement plays an important part in making that process easy. While the curing process can be slow in some situations, joining two pipes this way creates a durable bond with few tools and little installation time.
If you’re in the market for CPVC cement, couplings, or other fittings, QRFS carries a supply of American-made CPVC products from ThermaFit Industries. With elbows, caps, tees, and adapters for fire sprinkler heads, our selection makes it easy to install a code-compliant residential fire sprinkler system.

View our selection of CPVC fittings or purchase TFI’s CPVC cement by the pint.
Have questions about cure times for CPVC “glue”? Call us at +1 (888) 361-6662 or email support@qrfs.com.
This blog was originally posted at blog.qrfs.com. If this article helped you, check us out at Facebook.com/QuickResponseFireSupply or on Twitter @QuickResponseFS.
BlazeMaster® and FlameGuard® are trademarks of the Lubrizol Advanced Materials, Inc. and Spears Manufacturing Co. respectively.