Backflow preventers offer the best protection against contamination of city water supplies
A check valve provides a basic form of backflow prevention, preventing water from flowing in the wrong direction. National Fire Protection Association (NFPA) model codes and standards require them in various places on fire protection systems, and check valves are essential components of backflow preventers. But they are not adequate on their own to protect potable city water supplies from backflow contamination. “Potable” supplies contain treated, drinking-quality water.
In this blog, we explain the key differences between backflow preventers vs. check valves. And we clear up a misconception that’s often inquired about in online forums: while check valves have other important applications, they cannot be considered a safe substitute for backflow preventers when it comes to protecting the purity of drinking water.
In the market for check valves or check key tools for backflow preventers? Be sure to check out our selection of check valves. QRFS also carries backflow check key tools and toolsets, which quickly remove or install cam checks found in Ames and Watts backflow prevention assemblies.
Check valves vs. backflow preventers: why they aren’t interchangeable devices
Backflow occurs when pressure changes in pipes cause the flow of liquids, gas, or semisolids to reverse in the wrong direction. Check valves are designed to ensure substances in a pipe only flow one way, automatically closing to prevent unwanted backflow if the direction is reversed. They are used successfully in a wide variety of applications: protecting equipment such as pumps and filters from backflow damage, stopping drainage in a fire sprinkler system with elevation changes, providing pressure relief in liquid or pneumatic applications, and more.
Because of their simple design, check valves generally operate without automation or human interaction—continuing to work even if the power goes out or people can’t manually cycle them. Instead, they are flow-sensitive; when water flows through a pipe, check valves rely on the water’s flow velocity to open or close. The cracking pressure, or minimum upstream pressure needed to operate a check valve, generally falls between 1 and 5 pound-force per square inch (PSI).
Many check valves feature a hinged clapper with a spring that keeps the valve closed until it’s opened by water flowing from a source. If the pressure downstream exceeds upstream pressure, the spring presses the clapper against a rubber seat, forming a watertight seal and preventing flow from reversing.
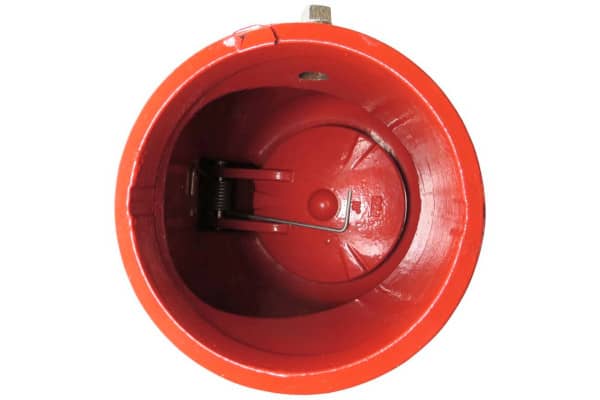
But here’s the thing: a check valve can serve as an important means of backflow prevention in low-risk scenarios, such as when equipment damage stands out as the biggest risk. But when the stakes are as high as the purity of the water people drink, local plumbing codes require the more reliable protection of backflow preventers.
While check valves function reliably most of the time, failures can occur for many reasons. Since a check valve’s clapper is always in the flow path, clapper movement will happen even if there isn’t enough flow. Parts that rub against each other cause wear, which can eventually lead to check valve failures. In extreme cases, damaged components can even escape into the line, causing other valves or equipment to malfunction.
Worn seat seals are another common cause of check valve failures, as well as lodged debris that causes the valve to remain stuck in the open or close position. Damage can also be caused by water hammer, in which flow reversal downstream causes the valve to abruptly close—resulting in a pressure wave that propagates throughout and damages the pipe. Improper maintenance, installation, or assembly can also lead to failures.

Backflow preventers take backflow protection to the next level
Backflow can be dangerous when pressure changes in water pipes cause water from building systems like sprinklers, irrigation, or plumbing to seep back into the main city supply line. When this happens, the public drinking water can be polluted with contaminants like fertilizers, pesticides, human waste, and harmful chemicals.
Backflow can also be extremely expensive to remediate: the Environmental Protection Agency (EPA) states that the average backflow incident takes nearly 500 hours to fix at a cost of $14,800.
Like a check valve, a backflow preventer is a device that ensures water only travels in one direction. Its sole job is to keep water flowing from the water main to a building’s pipes. However, it takes backflow protection to the next level with extra fail-safes designed to keep drinking water pure by preventing the non-potable water in a building’s systems from backing up and contaminating it.
Our previous blog, “How Does a Backflow Preventer Work?” offers great detail on the different types of backflow preventers and how they work. It also explains when they’re required to protect city water supplies connected to fire protection systems.
Local plumbing codes set forth requirements for backflow preventers in building systems, such as fire protection equipment. They also typically require backflow preventers to be tested regularly and maintained by certified professionals to ensure they are reliable and functioning properly.
Be sure to check with your local water authority to understand specific requirements for backflow preventers in your area.
Fire protection systems: How does a backflow preventer work?
Two main types of backflow preventers are utilized in fire protection systems. Double Check Valve (DCV) backflow preventers are common in low-hazard situations, where cross-contamination might create a nuisance or be aesthetically objectionable but wouldn’t create a health hazard.
These backflow preventers are specifically designed to prevent reverse flow in fire sprinkler systems, using two check valves assembled in a series to prevent water from backing up into the supply line.
This redundancy ensures that one check valve will continue to protect the city water supply even if the other fails. The assembly also enables the closure of one valve to reduce the pressure differential across the other, creating a more reliable seal and avoiding even minor backflow leakage.
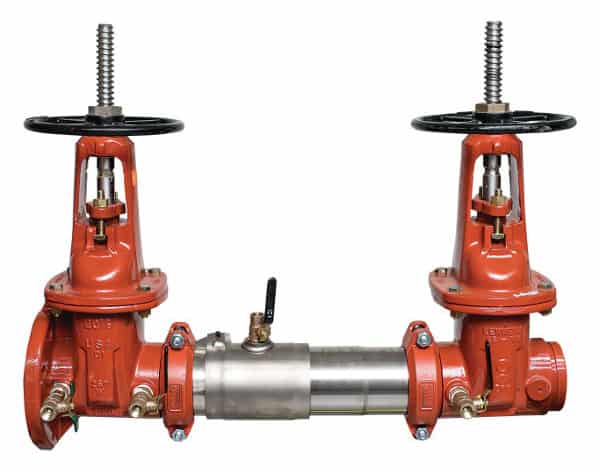
A Reduced Pressure Zone (RPZ) backflow preventer ups the protection of redundant check valves even more. The addition of a hydraulically operated differential relief valve makes this device essentially fail-safe.
During normal operation of an RPZ backflow preventer, the pressure between the two check valves—referred to as the zone of reduced pressure—is maintained at a lower pressure than the supply pressure. If either check valve should leak, the relief valve is designed to open and discharge water to the outside, ensuring that backflow never occurs.
On fire protection systems, plumbing codes generally require RPZ backflow preventers in high-hazard cross-connections, where hazardous chemicals like antifreeze or corrosion inhibitors could threaten public health if they are introduced into a city’s water supply. Some local water authorities, however, require them on all fire protection applications.
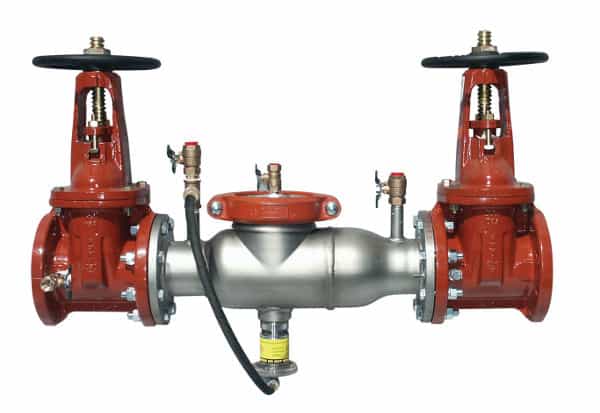
Backflow preventers vs. check valves: greater protection is needed for potable water supplies
Check valves are relied on to prevent backflow in a variety of applications, from HVAC systems to sump pumps to fire sprinkler systems with elevation changes. But when it comes to public health and safety, many water authorities and municipalities demand the more reliable protection of backflow preventers to keep drinking water safe.
Knowing key differences between backflow preventers vs. check valves helps property owners and facility managers understand why the added cost and complexity makes sense.
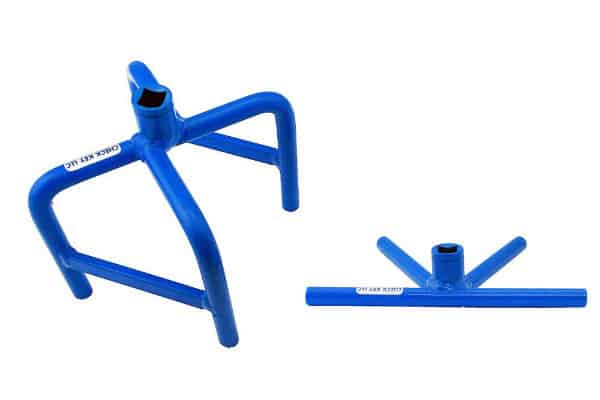
QRFS has a selection of check valves for fire protection and other applications. We also carry backflow check key tools and toolsets, which quickly remove or install cam checks found in Ames and Watts backflow prevention assemblies.
This blog was originally posted at blog.qrfs.com. Check us out at Facebook.com/QuickResponseFireSupply or on Twitter @QuickResponseFS.
When using a SDCV in a vertical position, do I need to use an isolating valve on either side of the SDCV? There are two landing valves positioned above the SDCV with a gear operated butterfly valve (isolator) below the SDCV.
Derek, thanks for reaching out. For code questions like this, we recommend submitting your question through QRFS Ask A Pro. Click the link to submit your question with some information about your building or system, and a fire protection professional will provide a detailed answer based on standards and codes. Our pros include AHJs, contractors, engineers, and code experts with 150+ years of combined experience!
I live in a house that is 300′ from the water supply main, connected by 1″ PE pipe, thus containing more than 12 gallons of water. The road is entirely uphill from the house. I’m installing a combo-boiler with an autofeed inlet to be sure the heating loop has adequate water. The heating loop has a 12PSI 2-gallon expansion tank, and the loop includes about 240′ of 1/2″ PEX tubing and hydronic baseboards. Thus the loop includes about 2.4 gallons and the other components about another gallon. I’m an experience professional mechanical engineer and am trying to figure out any way that my system needs an approved back flow preventer for the heating loop feed line. As soon as city pressure would drop, a little back flow from my supply pipe would occur, until my system pressure dropped to the street pressure. This equalization would let out at most a gallon. And the process couldn’t happen again until the city re-pressurized to refi;;/re-pressure my heating loop. This would have to push water back from my supply line to the heating system. No siphoning could occur because the city water line is well above my system.
Can anyone suggest a way that my small heating loop could endanger the public water supply in this circumstance?
Sir, thanks for reaching out. For complex system application questions like this, we recommend submitting your question through QRFS Ask A Fire Pro. Click the link to submit your question with some information about your building or system, and a fire protection professional will provide a detailed answer based on standards and codes. Our pros include AHJs, contractors, engineers, and code experts with 150+ years of combined experience!
Great article QRFS! I appreciate how you went into detail with these apparatuses used to prevent backflow. Most people have the common misconception that these two are interchangeable but do not know that one part is essential to the other. These components are essential for general safety and health and are used in many places, for HVAC systems, fire protection etc. Knowing the ins and outs of your water systems allows for better planning and decision making.
Thanks, Eleonor!