Samples of old fire sprinklers must pass laboratory tests or be replaced — usually (but not always) decades after installation
Fire sprinklers have been around for a long time, necessitating rules for ensuring that really old sprinkler heads still work. The National Fire Protection Association first published NFPA 13: Standard for the Installation of Sprinkler Systems in 1896 and most recently updated it in 2022. The “modern” spray sprinkler arrived on the scene in 1953, NFPA committees started exploring quick-response sprinklers in the ‘60s, and Grinnell manufactured the first listed residential fast-response model in 1981. Over all those years and evolutions, various fire sprinkler types have proven to be reliable and effective technology.
But think about the first spray sprinkler heads installed 70 years ago or the relatively newer quick response heads—can we simply trust that they work?
Despite fire sprinklers’ extensive track record, we must ensure they still function as they age. Fortunately, the need for testing starts decades after installation for many fire sprinklers, though this interval varies significantly for different types. This article explains:
- Why and when NFPA 25: Standard for the Inspection, Testing, and Maintenance of Water-Based Fire Protection Systems requires age-related testing (or replacement) of different fire sprinklers
- How sprinkler testing works and what the results mean
- How to pick a sample of sprinklers to send to the lab
Check out our previous blog posts to learn who can replace a fire sprinkler head and how to find replacements for obsolete sprinkler heads.
Pass or fail, you’ll need to replace a few sprinklers every time you conduct sprinkler head testing — or whenever sprinklers get damaged, corroded, painted, or activate. Check out QRFS’s inventory of fire sprinkler heads, escutcheons, cover plates, and installation tools.
When do you need to do fire sprinkler testing?
Removing fire sprinklers for a test isn’t convenient; you have to shut down and potentially drain the system or a portion of it. So, when testing be done? It depends on what type of sprinkler heads you have and the environments where they are installed.
Standard response sprinklers—test 50 years after installation, then every 10 years
Standard response sprinklers have been around much longer than their newer fast-response cousins, so they have the longest reliability track record and testing or replacement interval. Required testing starts at 50 years, with subsequent assessments every decade (5.3.1.1.1).
However, once sprinklers manufactured in 1920 or later hit 75 years after installation, you must increase the testing interval to every five years — or just replace the heads with new ones to start the clock again (5.3.1.1.1.4*). That said, the 50/10-year rule assumes that the sprinklers are installed in relatively favorable conditions. If they are exposed to harsher environments, different timelines may be required, as covered below.
Most fast response sprinklers (not ESFR and CMSA)—test 25 years after installation, then every 10 years
The latest 2023 edition of NFPA 25 stipulates that fast-response sprinklers should be tested 25 years after installation and retested every 10 years after the first test (5.3.1.1.1.1). “Fast response” refers to the thinner, more sensitive heat-response elements and quicker activation of quick response, residential, and some other sprinklers. The logic for more frequently testing fast response sprinklers is that they’ve been around less time and have a shorter reliability record—NFPA simply doesn’t have as much data on how long they last.
In addition, fast-response sprinklers are designed to be more sensitive to their specific activation temperatures, and testing determines whether this sensitivity is maintained sufficiently. That said, the 25-year testing or replacement requirement is up from 20 years in previous editions of NFPA 25, indicating that data has shown greater reliability of most fast-response sprinklers. There are two exceptions, however …
ESFR and CMSA sprinklers—test 20 years after installation, then every 10 years
Early suppression, fast response (ESFR) and control-mode special application (CMSA) sprinklers, both of which have large K-factors and the latter of which are sometimes fast response, must be tested (or replaced) 20 years after installation and at 10-year intervals afterward (5.3.1.1.1.2*).
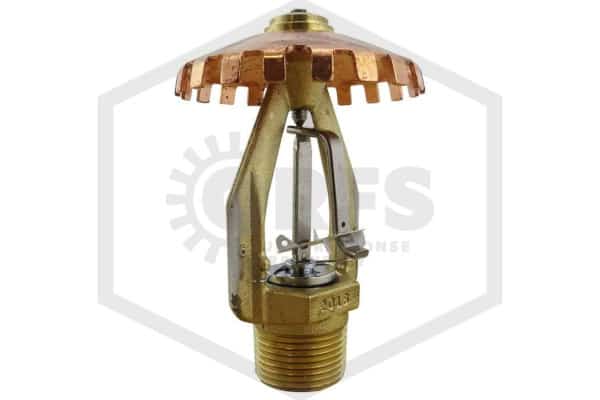
Dry sprinklers—test 20 years after installation, then every 10 years
Dry sprinklers should be tested 20 years after installation and then retested every 10 years after that (5.3.1.1.1.5). Why shorter intervals than most non-dry sprinklers? Dry sprinklers and entire dry systems are more prone to corrosion due to the greater mix of oxygen with residual water. And while dry sprinkler heads and systems have features explicitly designed to avoid freeze damage, components can experience it without proper maintenance due to leftover water.
Nevertheless, the 2023 edition of NFPA 13 marks two consecutive five-year increases in the latest editions; from 2002 to 2017, the initial testing or replacement interval was only 10 years. Here’s some context from NFPA 25 explaining why:
At the time [2002], not all of the conditions that cause failures were well understood, and the frequency of failures was higher for sprinklers that had been in service for more than 10 years. Design changes have been made to dry sprinklers where dynamic O-ring seals are no longer used. As a result, dry sprinklers are performing quite well and thus the requirement was modified […]
Extra-high, very extra-high, or ultra-high temperature, solder-type fire sprinklers exposed to very hot environments—test every 5 years
Some fire sprinkler environments, like industrial facilities, are extremely hot, and sprinklers with very high, very extra-high, and ultra-high temperature ratings are used above equipment like ovens, furnaces, and boilers. The ambient heat can cause the meltable solder to migrate in fusible-link fire sprinklers (the ones without glass bulbs), affecting their ability to activate. Where these models are in such environments for at least five years, fire sprinkler testing must be done every five years:
From the 2023 edition of NFPA 25 5.3.1.1.1.3* Where solder-type sprinklers with a temperature classification of extra high [325°F (163°C) or greater] are installed and exposed to semi-continuous to continuous maximum allowable ambient temperature conditions for 5 years, one of the following shall occur: (1) The sprinklers shall be replaced. (2) Representative samples of the sprinklers shall be tested and then retested every 5 years.
As most readers know, fire sprinklers activate at a particular temperature (the temperature rating). This rating is indicated by:
- The color of the liquid in the glass bulb indicates the temperature range for bulb-type sprinklers.
- In fusible link sprinklers, a small colored dot on the deflector and/or a colored finish or paint swipe on the frame indicates the temperature range.
- The precise activation temperature is usually imprinted on the deflector.
Each temperature rating also lists a maximum ambient ceiling temperature—the area around the sprinkler can get that hot without the risk of unnecessary activation. The below table combines tables 7.2.4.1 (a) and (b) in NFPA 13 (2022) to show the different temperature color codes for fusible link sprinklers and the bulb colors in bulb-type models. The relevant colors/temperatures/types that may need five-year testing are in bold:
Bulb Color | Fusible Link Color Code | Temperature Rating | Temperature Activation Range | Max Ceiling Temperature |
---|---|---|---|---|
Orange or Red | Uncolored or Black | Ordinary | 135-170F (57-77C) | 100F (38C) |
Yellow or Green | White | Intermediate | 175-225F (79-107C) | 150F (66C) |
Blue | Blue | High | 250-300F (121-149C) | 225F (107C) |
Purple | Red | Extra high | 325-375F (163-191C) | 300F (149C) |
Black | Green | Very extra high | 400-475F (204-246C) | 375F (191C) |
Black | Orange | Ultra high | 500-575F (260-302C) | 475F (246C) |
Black | Orange | Ultra high | 650F (343C) | 625F (329C) |
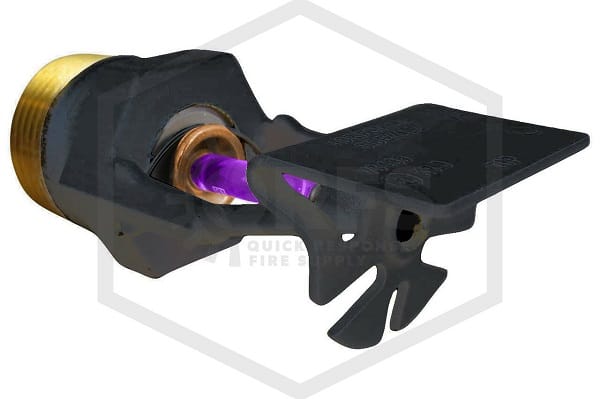
Sprinklers installed in harsh/corrosive environments—test every 5 years OR at 10 years and then every 5 years
Harsh conditions, especially corrosive atmospheres, can take their toll on fire sprinklers. NFPA 25 provides some examples of such environments (A.5.3.1.1.2):
- Paper mills
- Packing houses
- Tanneries
- Alkali plants
- Organic fertilizer plants
- Foundries
- Forge shops
- Fumigation areas
- Pickle and vinegar works
- Stables
- Storage battery rooms
- Electroplating rooms
- Galvanizing rooms
- Steam rooms
- Salt storage rooms
- Locomotive sheds
- Driveways
- Areas exposed to weather
- Around bleaching equipment in flour mills
Many sprinklers installed in these settings should be tested every five years or replaced (5.3.1.1.2*). But it’s possible to lengthen the initial five-year test requirement. Listed corrosion-resistant sprinklers can initially be tested at 10 years and retested every five years afterward (5.3.1.1.3). Corrosion-resistant sprinklers use stainless steel construction or specialized coatings (or both) to prevent oxidation.
You can read more about these technologies in our previous blog.
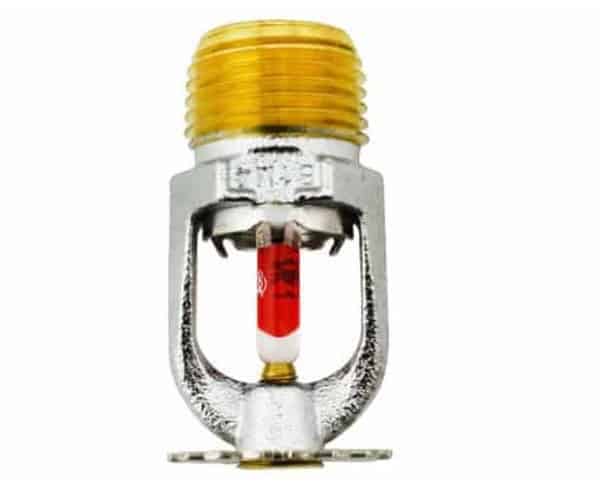
Sprinklers manufactured before 1920—replace them
Any sprinkler manufactured before 1920 must be replaced—no questions asked, samples taken, or testing (5.4.1.1). It’s over a century old, for Pete’s sake!
The “historical data” exception
There is one caveat to all of these testing intervals, as outlined here:
From the 2023 edition of NFPA 25
5.3.1.1.4 Where historical data indicate, longer intervals between testing shall be permitted.
Unfortunately, NFPA 25 provides no explanatory context about specific sprinkler types, historical data timelines, or how much the testing intervals can be lengthened. But according to one NFPA committee member consulted by QRFS, he believes that the exception, which first appeared in the 2002 edition, was likely intended for sprinklers in harsh/corrosive environments. Prior test reports indicating that sprinklers are not showing detrimental effects from exposure or other data that supports a longer range of exposure might spur reevaluating the testing or replacement interval, subject to approval by the authority having jurisdiction (AHJ).
Electrically operated sprinklers—according to manufacturers’ instructions
Electrically operated fire sprinklers are relatively new and don’t activate using a thermal-sensitive glass bulb or meltable solder link. NFPA Today notes they “are typically used in high challenge storage applications.” NFPA 25 began to issue rules for these devices in the 2020 edition and defines them as follows:
3.3.41.5 Electrically Operated Sprinklers. A sprinkler that is equipped with an integral means of activation using electricity.
They often use heat detectors to sense activation temperatures and are integrated with fire alarm control panels and systems. Since this technology is fairly new and doesn’t rely on traditional tech, NFPA 25 defers to the manufacturer for head testing rules and intervals, and none of the lab tests covered in our next section apply to them.
5.3.2.1 Electrically operated sprinklers shall be tested in accordance with the manufacturer’s requirements. 5.3.2.2 The testing of the electronic actuation and supervision shall be in accordance with the manufacturer’s requirements and NFPA 72 or the local fire alarm code.
Fire sprinkler testing procedures: a lab performs a visual assessment and the plunge test
When it’s time to test fire sprinklers, you or your fire protection contractor will submit a sample of them to a qualified laboratory. NFPA 25 (5.3.1.1) says this should be “a recognized testing laboratory acceptable to the authority having jurisdiction,” highlighting labs that meet ISO/IEC 17025, General Requirements for the Competence of Testing and Calibration Laboratories. The lab must be capable of conducting tests according to ANSI/UL 199: Standard for Safety of Automatic Sprinklers for Fire-Protection Service.
First, the lab visually inspects the sample to see if it fails section 5.2.1.1.1* of NFPA 25, which means sprinklers have obvious leaks or damage, significant corrosion, loss of fluid in the bulb, heavy loading (dust, dirt, or gunk), or any aftermarket paint. Then, following UL I99, the lab will perform the sensitivity oven heat test, often called the “plunge test.” The sprinkler is first lightly pressurized to about 7 psi or the distinct “minimum listed operating pressure for dry sprinklers” (A.5.3.1.1). Then, the pressurized sprinkler is quickly inserted (“plunged”) into a specialized oven that circulates hot air at a specific temperature and speed.
This video from Dyne USA, which does UL 199 sprinkler testing, demonstrates the plunge test:
The oven should cause the sprinkler to operate on time, which is assessed by calculating the sprinkler’s response time index (RTI). Labs use the following variables to calculate RTI:
- The time it takes the sprinkler to operate
- The sprinkler’s operating temperature
- The temperature in the oven
- The air speed in the test oven
- The sprinkler’s conductivity factor
RTI is measured in (meters-second)1/2, and new fire sprinklers are expected to have RTIs specific to their response type. However, NFPA 25 recognizes that older sprinklers will not perform to the same standard as new sprinklers (A.5.3.1.1).
So, for example, while a new fast response sprinkler should have an RTI of 50 (meters-second)1/2 or less, older fast-response sprinklers can have measured RTIs of up to 65 and still pass the test. Standard-response sprinklers can have RTI up to 350 and still pass. A sprinkler fails the plunge test if it doesn’t activate or does it too slowly—the RTI is higher than the acceptable value for the type of sprinkler. And if one sprinkler in a sample group fails, NFPA 25 requires replacing all of them installed in the area a sample represents (5.3.1.3).
Defining sample areas and sizes for fire sprinkler testing
As we said, the only definitive way to know if a sprinkler head works is by forcing it to activate. But fire sprinklers are single-use, and you must replace a sprinkler head whether it passes or fails. So instead of testing every fire sprinkler in the system, NFPA 25 basically compels an experiment—you remove a small number of your sprinklers and only assess those. Based on the results of that test, we can draw a conclusion about all the sprinklers in the area the sample represents.
NFPA 25 outlines some specific rules for setting up a test but also gives significant discretion. The standard (5.3.1.2) calls for a representative sample, which should include 1% of all sprinklers installed in an area or system or four sprinklers, whichever number is greater. In addition, you can test the entire system area with one sample or take multiple sample areas based on different conditions within the structure.
NFPA 25 doesn’t precisely define what makes a sample “representative” in fire sprinkler testing but offers some guidelines:
- The sample should cover a particular ambient environment (e.g., temperature, atmosphere, use/occupancy).
- “The sample should be somewhat random and […] representative of the sprinklers installed in the system. For example, sprinklers should be selected from different floors or areas of the building and not selected simply because they are more accessible than other sprinklers.” (3.1.2* — “enhanced content”)
- “Each sprinkler type and manufacturer in the sample area shall be represented in the sample.” (3.1.2.1*)
- “Sprinklers tested shall not include any sprinklers that were replaced at prior testing intervals.” (3.1.2.2)
Other than these rules, you have significant flexibility. According to the NFPA 25 Annex:
A.5.3.1.2 […] The sample sprinklers sent for testing can represent any group of sprinklers that is practical, keeping in mind that if one sprinkler in the sample set fails, then all sprinklers that the sample represents should be replaced.
An example should make these rules clearer. Consider a five-floor apartment building with 100 sprinklers per floor and an attached parking garage with 200 sprinklers. The apartments and the parking garage are drastically different environments, so you should probably test them separately. For the parking garage, you should take a sample of at least four sprinkler heads (the one percent option is 0.01 x 200 = 2, which is too few). There are two (obvious) ways to handle the apartments. First, you could sample the whole building at once (minus the separate garage sample) and send five sprinklers for testing (0.01 x 500 = 5; plus 4 from the garage = 9 sprinklers in 2 samples). It’s convenient, but if one sprinkler fails, you must replace all 500 sprinklers in the apartments.
An alternative is to treat each floor as a separate sample area. Because each floor has 100 sprinklers (0.01 x 100 = 1), you are required to send four sample sprinklers per floor (4 x 5 = 20 total). This scenario is more work and cost up-front, but it could prevent replacing every sprinkler within the building. If one sprinkler from one sample fails, you only have to replace 100.
The National Fire Sprinkler Association (NFSA) explains that exactly how you organize your samples is a judgment call. The sprinkler contractor should have a conversation with building management to make a decision based on financial concerns and the visual condition of the sprinkler heads. And as Dyne USA explains, it’s generally a good idea to take many smaller samples if you have sprinklers you are worried about or multiple harsh environments.
As heads age, fire sprinkler testing is essential
One great thing about fire sprinklers is that they’re incredibly reliable, typically lasting many years — usually decades — without replacement. But inspection, testing, and maintenance are still crucial for fire sprinkler systems, especially as they age. Be sure to review what type of fire sprinklers are installed — in what environments — within your building and follow the above NFPA 25 guidelines.
If you need replacement sprinklers, QRFS has you covered. Stock up on spare or replacement fire sprinkler heads, as well as escutcheons, cover plates, and installation tools, from our online catalog.
If you have questions or need help finding an item, contact us at (888) 361-6662 or support@qrfs.com.
This blog was originally posted at QRFS.com/blog. If this article helped you, check us out at Facebook.com/QuickResponseFireSupply or on Twitter @QuickResponseFS.
I live in a condo with 96 units. They recently did a dry sprinkler test on our system and it failed. Now, they tell us they have to tear out all the pipes in four buildings, displace all the people during the job, and it will be very intrusive. As I read everything, it would make more sense to replace ALL sprinker heads in the whole system. We have had some freezing problems in the past, especially in those units that face the east wind.
What are your thoughts? Thanks
Warren — Unfortunately, we can’t comment too helpfully without knowing what test failed. For example, if they are tearing out all the pipes, it may indicate that they found a corrosion problem that was causing leakages or blocking the water during a test. (Corrosion can be an issue in some dry systems, especially if the system uses pressurized air instead of nitrogen). In that case, it wouldn’t be the sprinkler heads that are the problem, it would be the pipe network itself. However, older dry sprinklers (circa pre-2003) have also had problems, so sprinkler heads could also fail an activation test. Regardless, it depends what the problem is, how the system is maintained, etc. You might want to ask exactly what the issue is and have the sprinkler pro/management company explain the rationale. Thanks!