Installation scenarios, the number of parts, and installer preferences determine which grooved pipe fitting is best for joining different-sized fire protection pipes
Grooved pipe systems make installing pipes in fire sprinkler systems and other applications easier and faster. The grooves allow quick, sure placement of couplings that create a water-tight seal without flanging or welding. Installers often need to join larger-diameter pipe to smaller-diameter pipe, of course, and there are several options to do it: reducing couplings, concentric reducers, and eccentric reducers. But which grooved pipe fitting is better suited for a specific job?
As with many things in fire protection, the answer is “it depends.” Here’s an explanation of when and why you might use each type of reduction (or expansion) device.
QRFS carries the equipment needed for your next project: check out our full selection of grooved fittings, including flexible and rigid couplings and adapters and reducers.
Both concentric reducers and reducing couplings keep pipes centered
These two devices for connecting different-sized pipes share a characteristic: both reducing couplings and concentric reducers (sometimes called “conical reducers”) maintain the center axis of the pipes they join and the water flowing through them.
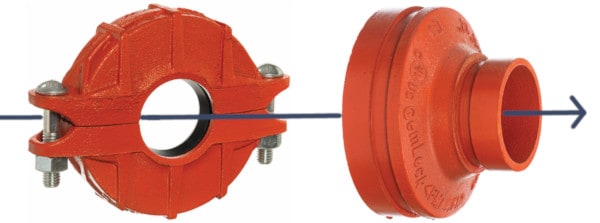
From there, they are a bit different: reducing couplings attach two different-sized pipes with less real estate in between them — the housing is 1.8”–2.4” wide, and the two pipe ends nearly touch —and only one coupling is required. In contrast, concentric reducers are “in-line reducers” that have a longer (2.5”–6”) funnel-like body that must be joined to the pipes on both sides by two standard, non-reducing couplings of appropriate sizes. So, using one part vs. three parts is a significant difference.
Both reducing couplings and concentric reducers enable transitions from a larger pipe to a smaller one (and vice versa). The main difference is that couplings are narrower, the transition is quicker, and fewer parts are involved. That said, concentric reducers may provide slightly better water flow than reducing couplings.
So, what about real-world use cases where one might be preferred over the other?
One possible consideration involves installing vertical pipe. To understand why, let’s review how installers join grooved pipes with couplings. They:
- Disassemble the coupling
- Apply lubricant to the inner gasket
- Place the gasket around the lower grooved pipe
- Align the pipes
- Place the metal coupling housing around the gasket, ensuring it engages with the pipe’s grooves
- Insert the nuts and bolts, followed by tightening the nuts to form a water-tight seal
This video from Victaulic demonstrates a horizontal installation of a reducing coupling:
The potential issue in vertical installations is gravity. First, one must hold a long section of the upper, smaller pipe in place, maintaining the centerline while placing the metal housing around the gasket and tightening the nuts. And because the pipe sizes differ and gravity is what it is, there might be a risk that a smaller pipe will telescope down into a larger one.
Thus, some installers say they use concentric reducers because it’s a foolproof way to avoid telescoping. That’s because after they attach the concentric reducer — a small part that’s very easy to handle — to the lower pipe with a coupling, there is no risk of telescoping when attaching the upper pipe because the holes are the same size. Further, the top of the reducer presents a stable surface area that makes it easy to center the pipe while attaching and tightening the upper coupling.
But that said, high-quality reducing couplings either have optional steel washers or steel washers integrated into their gasket to prevent telescoping. For example, GemLock reducing couplings sized 2” and above have an integrated washer. So, when an installer places and aligns the upper pipe, the washer blocks that smaller pipe from sliding down into the larger one. And again, installers who use reducing couplings for vertical installations need fewer parts: one reducing coupling instead of two couplings and a concentric reducer.
Larry Greenberg, an engineer with Core & Main, which manufactures GemLock® grooved pipe systems, doesn’t believe there is always a 100% clear use case for using one over the other.
“A concentric reducer may give a little better flow, and we typically see that engineering companies tend to only go with them,” he says. “But other pipe fitters go with reducing couplings because they involve using fewer parts.”
What about a concentric vs eccentric reducer?
The scenarios that call for using eccentric reducers instead of either a reducing coupling or a concentric reducer are more straightforward — and eccentric fittings are sometimes required. An eccentric reducer has a humped or angled shape that does not sustain the central axis of the pipe or water flow. Instead, the axis changes as these devices maintain the “BOP (bottom of pipe) elevation of the pipeline.”
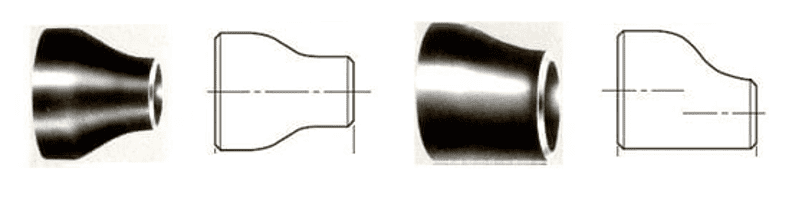
Thus, the primary use case for an eccentric reducer is an installation scenario where “one of the outside surfaces of the pipeline is to be maintained the same” (top, bottom, or side). These reducers are typically used in horizontal pipe joining and suction pipe applications. Like a grooved concentric reducer, grooved eccentric reducers attach to the pipes they join with two standard grooved couplings of the appropriate sizes.
Despite the benefits of maintaining the bottom-of-pipe elevation, installing an eccentric reducer flat side down may cause issues in some applications where horizontal pipes carry liquids. Specifically, air can get trapped using this orientation. An exception is using an eccentric reducer that feeds a control valve: “flat side down will give a more constant flow through the control valve rather than a concentric reducer or eccentric reducer with flat side up, which will give you more flow disruption.”
What do NFPA standards say about reducers and grooved pipe fitting?
There are few requirements in fire protection installation standards that govern which type of reducer to use. For example, NFPA 13: Standard for the Installation of Sprinkler Systems does not mention them under “groove joining methods.” It only references reducers in the section on welded fittings, and it’s not specific about their shape:
From the 2022 edition of NFPA 13
7.5.2.3.4 When the pipe size in a run of piping is reduced, a reducing fitting designed for that purpose shall be used in accordance with the requirements of 7.5.2.3.1.
Section 7.5.2.3.1 specifies the standards according to which various metal fittings must be listed.
But NFPA 20: Standard for the Installation of Stationary Pumps for Fire Protection has a requirement involving eccentric reducers. It mandates using them instead of concentric reducers to join the inlet of a suction pipe that connects the water supply to a fire pump:
From the 2022 edition of NFPA 20
4.16.6.4 Eccentric Tapered Reducer or Increaser.
Where the suction pipe and pump suction flange are not of the same size, they shall be connected with an eccentric tapered reducer or increaser installed in such a way as to avoid air pockets.
Commentary in the NFPA 20 Handbook (2016) specifies installing the eccentric reducer flat side up when “supplying the fire pump from below or the horizontal plane.” In contrast, “where supplied from above, the hydraulic institute recommends the flat portion of the reducer be installed on the bottom, with the actual reduction in pipe diameter taking place on the top of the fitting.”
Again, all these requirements — for using eccentric reducers on suction pipes and how to position them — aim to avoid trapped air, which is very bad news for fire pumps.
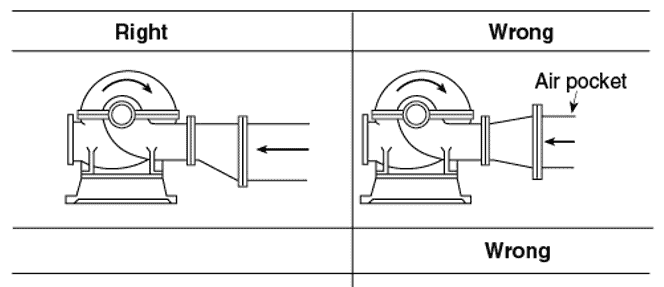
Other scenarios demanding eccentric vs. concentric fittings
Picking a concentric vs. eccentric fitting also comes into play regarding drain caps, a different type of reducing fitting used for auxiliary drainage of a fire protection system. Eccentric drain caps, which have an off-center hole, should be used when draining water from horizontal pipes, whereas either concentric or eccentric drain caps work for draining vertical pipes. Read more about grooved fire sprinkler drain caps, including all their potential uses.
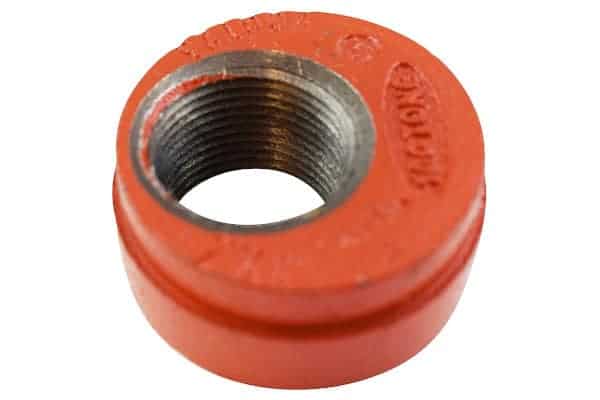
Use the grooved pipe fitting or coupling that’s right for your pipe-joining scenario and preferences
Aside from following the few NFPA rules, the ‘rules of thumb’ for using reducing couplings, concentric reducers, or eccentric reducers come down to:
- Whether you are doing horizontal, vertical, or suction-pipe installations.
- Whether you need to maintain the centerline of the pipe (reducing coupling or concentric reducer) or maintain the axis of one side of the pipe (eccentric reducer).
- Installer preferences, including ease of installation or use of fewer parts.
When it comes time to tackle your next project, check out QRFS’s grooved pipe fittings, including couplings, caps, and adapters and reducers.
All these grooved fittings are UL Listed and FM Approved, conform to ASTM A536 Grade 65-45-12, and are made by GemLock, a New York-based manufacturer of quality grooved pipe systems.
Have questions or need help finding a part? Contact QRFS at 888-361-6662 or support@qrfs.com.
This blog was originally posted at QRFS.com/blog. If this article helped you, check us out at Facebook.com/QuickResponseFireSupply or on Twitter @QuickResponseFS.