There are many listed corrosion-resistant sprinklers—which one works best can depend on the environment
In harsh environments, corrosion can wreak havoc on the metals that make up most fire sprinklers, potentially leading to their impaired operation or structural failure. That’s why sprinkler manufacturers offer corrosion-resistant coatings and finishes that are listed for use in these environments. However, confusingly, there are many choices when it comes to corrosion-resistant fire sprinklers—so which is best?
To answer this complex question, we will examine how corrosion affects sprinklers and the types of environments that cause corrosion, before discussing the pros and cons of different sprinkler finishes or materials for various scenarios. Read on to learn:
- Choosing a corrosion-resistant sprinkler finish
- FM approval can be more rigorous than UL-listing
- Polyester paint is a good choice, especially for pool areas
- Wax finishes are protective but easy to damage
- Electroless nickel Teflon (ENT) is durable and effective
- Proprietary coatings are often good choices
- Stainless steel is often superior but expensive
As we explore this topic, we’ll draw on some official sources, namely:
- NFPA 25: Standard for the Inspection, Testing, and Maintenance of Water-Based Fire Protection Systems (2025 edition)
- UL 199: Standard for Safety for Automatic Sprinklers for Fire-Protection Service
- FM 2000: Examination Standard for Automatic Sprinklers for Fire Protection
QRFS has you covered with commercial and residential fire sprinklers for all applications. Browse sprinkler heads by manufacturer or type, or use our sprinkler-finder tool to find the right model. If you don’t see the corrosion-resistant finish you need or are having trouble choosing one, contact our customer service team.
How corrosion harms fire sprinklers
Most guides to corrosion prevention in fire sprinkler systems focus on the degradation of metal pipes, usually black steel, that eats away at pipe walls (eventually leading to leaks) and creates debris that can clog pipes and sprinkler heads. But in contrast to the vast majority of pipes, sprinklers are typically made of brass, which is an alloy of copper, zinc, and (usually) lead. While brass can also corrode, it has unique mechanisms and issues.
For clarity’s sake, we’ll break down the effects of sprinkler corrosion into two primary issues: performance problems and structural problems.
When we say “performance,” we’re alluding to the annual visual inspection of fire sprinklers required by NFPA 25. If any sprinkler shows corrosion “detrimental to sprinkler performance,” it should be replaced (5.2.1.1.1). As we discussed in a previous blog entry, the phrase “detrimental to sprinkler performance” has been phased into items in that section of NFPA 25 over multiple editions, and it requires an inspector to make a judgment call. Ultimately, corrosion is detrimental to sprinkler performance if:
- A buildup of corrosion insulates the thermal element, delaying activation
- It seals the cap in place, preventing dislodgement and water flow
- Corrosion disrupts the sprinkler spray pattern on the deflector
Structural problems (which, of course, also cause performance issues) refer to the metal’s ability to stand up to the forces it will encounter while in service within a fire sprinkler system. These forces include working water pressure, the high pressures used during a hydrostatic test, and the forceful water flow that can occur during a sprinkler activation. Corrosion can weaken the metal of a sprinkler’s body, causing it to fail.
Just as there are different types of problems caused by the corrosion of sprinkler brass, the degredation itself happens in different ways. In general, brass corrodes by:
- Surface oxidation of copper, forming a patina
- Dezincification, where zinc leaches out of the alloy over time
- Stress corrosion cracking, where microscopic cracks form in the metal
Below, we examine how these three types of corrosion can lead to performance and structural issues in fire sprinklers.
Surface oxidation forms a patina
Although brass does not rust exactly like iron or steel, it does oxidize. The compounds formed by the reaction of copper, oxygen, and water can be different colors, including pink, black, and a classic green patina. This type of oxidation happens on the surface of brass and is typically not a structural problem. Brass patina, unlike iron or steel rust, does not flake off and expose the inner metal to oxidation. Thus, it does not weaken the integrity of the material and can even be considered protective.
While surface discoloration and oxidation don’t pose a structural problem, they can still cause performance issues. A buildup of copper oxide deposits might insulate the heat-sensitive element, prevent a sprinkler’s plug from dislodging, or disrupt the spray pattern. This is why UL 199: Standard for Safety for Automatic Sprinklers for Fire-Protection Service and FM 2000: Examination Standard for Automatic Sprinklers for Fire Protection both evaluate sprinklers for operability and heat sensitivity after they are exposed to corrosive atmospheres.
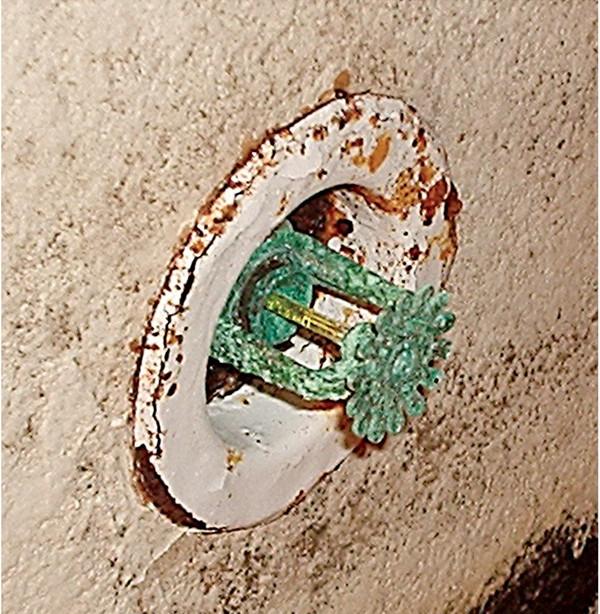
Dezincification makes brass brittle
As we mentioned, brass is an alloy of copper, zinc, and often lead. One type of corrosion that affects brass (especially brass with more than 15% zinc) is dezincification. Zinc is more reactive than copper—so, it can leach out of the brass alloy in some corrosive atmospheres. Dezincified brass becomes brittle, and the chemical change can sometimes be seen in a color change from yellowish brass to a pinkish hue of purer copper. Dezincified brass might not even look “corroded” in the way we usually think of that word while still being structurally compromised.
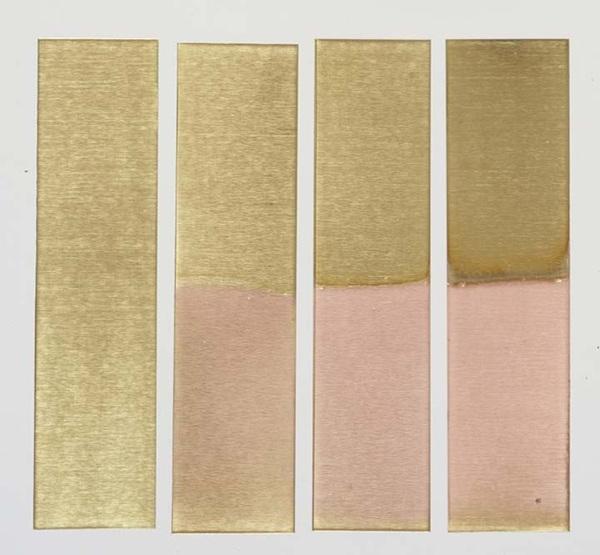
Many types of conditions cause dezincification, including slightly acidic, slightly alkaline, and salty environments. Chloride ions, such as those found in hydrochloric acid or salt air, especially promote zinc leaching. Because UL found that dezincification was a particular problem in some sprinklers installed in the field, UL 199 requires all brass sprinklers with more than 15% zinc to undergo a dezincification test, which involves exposure to copper chloride.
Some sprinkler manufacturers have also begun producing corrosion-resistant fire sprinklers with dezincification-resistant (DZR) brass, which contains a higher proportion of copper, less zinc, and additives—such as arsenic, tin, or phosphorus—that reduce zinc loss.
Stress corrosion cracking
Stress corrosion cracking (SCC) is the formation of small, sometimes microscopic, cracks in an alloy that form due to a combination of physical stress (such as tension) and corrosion. In brass, ammonia is the major cause of stress corrosion cracking. The formation of these cracks can lead to structural failure in sprinklers.
Dezincification and stress corrosion cracking are often synergistic; one exacerbates the other, and vice versa. Both UL 199 and FM 2000 evaluate brass sprinklers in moist ammonia atmospheres, testing for evidence of cracking and structural failure, as well as assessing heat sensitivity and consistent operation.
Types of harsh, corrosive environments
Corrosion can occur anywhere, but it happens most rapidly in certain types of harsh, chemically reactive atmospheres. That’s why NFPA 25 says that sprinklers “exposed to harsh environments, including corrosive atmospheres” should be tested for functionality or replaced every five years (5.3.1.1.2). That said, sprinklers placed in harsh environments that are listed as corrosion-resistant can initially be tested at 10 years instead of five, and retested every five years afterward (5.3.1.1.3).
There are many types of harsh, corrosive environments, and they affect sprinklers differently. Between UL 199, FM 2000, and the sprinkler manufacturers’ literature, we can highlight a few major types of corrosive atmospheres, including salt air, chloride atmospheres, carbon dioxide/sulfur dioxide atmospheres, hydrogen sulfide atmospheres, and ammonia atmospheres. That isn’t a comprehensive list, and NFPA 25 details many more specific examples of harsh environments. However, these are very significant categories:
Salt air
Both UL 199 and FM 2000 test sprinklers after exposure to moist, salty atmospheres similar to those found near the ocean. These environments are particularly corrosive to brass, so corrosion-resistant fire sprinklers can be essential.
Chloride atmospheres
Although salt contains chloride ions, we can treat chloride-heavy atmospheres as a distinct problem for brass sprinklers. Swimming pools use chlorine as an antimicrobial agent and other compounds as stabilizers. The atmospheres around swimming pools, especially indoor pools with poor ventilation, can be particularly challenging to sprinklers. Some manufacturers say that sprinkler finishes suitable for salt air should not be used in chlorine atmospheres—more on that soon.
Carbon dioxide/sulfur dioxide atmospheres
Both UL 199 and FM 2000 evaluate sprinklers against carbon dioxide/sulfur dioxide atmospheres. This mixture of gases comes from the combustion of fossil fuels—think power plants, commercial boilers and furnaces, and heavy industrial processes. Diesel-burning vehicles and construction equipment are also significant sources. Diesel fuel is typically higher in sulfur content than standard gasoline, although its sulfur levels have been reduced in recent years due to regulatory requirements.
Hydrogen sulfide
Hydrogen sulfide is a corrosive chemical used in industrial settings such as paper mills, coke plants, and tanneries. It is also a byproduct of crude oil refining and produced from wastewater and landfills.
Ammonia atmospheres
As mentioned earlier, ammonia can cause stress corrosion cracking in brass. Thus, ammonia atmospheres are highly challenging environments. Ammonia can be used as a fertilizer, as a refrigerant in cold-storage areas, as a cleaning agent, and in textile plants.
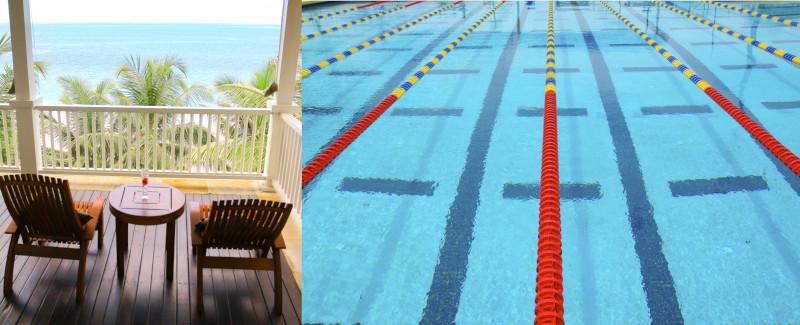
Choosing corrosion-resistant fire sprinklers
As mentioned earlier, sprinklers in harsh environments with listed corrosion-resistant finishes have extended timelines in NFPA 25 testing requirements. But beyond the testing rules that may spur buying them, there are practical benefits for many situations. A sprinkler finish or material that has earned a corrosion-resistant listing means it has been tested to withstand harsh environments, so it should last significantly longer in a variety of environments. That’s a major plus.
Types of corrosion-resistant finishes
There are many different UL-listed or FM-approved corrosion-resistant sprinkler finishes, including polyester paint, electroless nickel PTFE, wax, and more. In addition, some companies have proprietary coatings. Finally, some sprinklers are also available in all-stainless-steel construction. So, which should you choose for what environment?
From one significant perspective, it doesn’t matter. NFPA 25 does not say anything about which type of corrosion-resistant sprinkler you must use to get the benefit of an extended testing timeline. If you only care about compliance, any sprinkler that’s UL-listed or FM-approved as corrosion-resistant will do. That said, there’s more to life than basic compliance!
Unfortunately, sprinkler manufacturers don’t make it easy to make a choice. For liability reasons, they say that picking the right coating is your responsibility, not theirs. For example, this Viking data sheet states, “Appropriate finish and parts choice for an environment is the responsibility of the customer.” A Tyco representative also stressed to us that “it is the end-user’s responsibility to verify the materials that compose the sprinkler are compatible with the environment.”
Fortunately, representatives from Tyco, Victaulic, and especially Viking were also able to provide us with some very helpful information that can guide making a choice among finishes, coatings, or materials. Between this feedback, some published data, and an understanding of how corrosion-resistant listings work, we can offer some general conclusions:
- An FM Approval is slightly more rigorous than a UL Listing alone
- Polyester paint is a generally good choice, and ideal for indoor chlorine pools
- Wax is protective but requires careful handling to ensure it does not strip off
- An electroless nickel PTFE (ENT) coating is durable and effective—but not for chlorine environments
- Proprietary coatings are often good choices
- A sprinkler with complete stainless-steel construction is generally superior, but the most expensive option
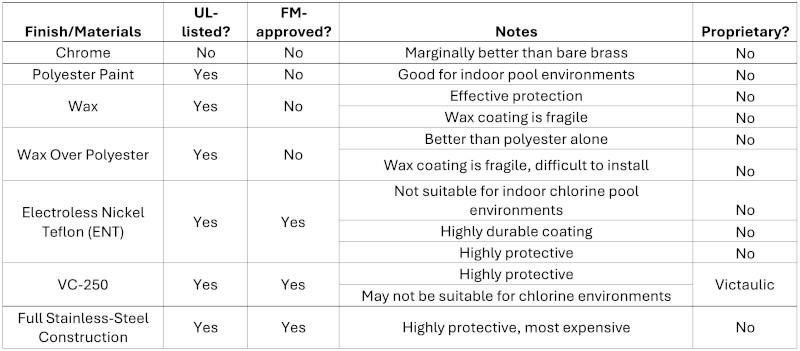
Let’s go over each of these considerations:
FM Approved can be more rigorous than UL Listed
All listed fire sprinklers, regardless of finish, undergo a baseline corrosion-resistance test, as seen in UL 199 and FM 2000. However, achieving a specific corrosion-resistant listing requires going beyond the baseline test; instead of standing up to a 10-day exposure assessment, corrosion-resistant sprinklers must withstand a 30-day exposure test under both UL and FM standards. If this seems like a short period compared to how long a sprinkler stays in service, know that the corrosive atmospheres used in these tests are much more intense than those typically found in the field.
It’s useful to know that FM Approval is slightly more rigorous than UL Listing in terms of corrosion resistance. These portions of FM 2000 require more tests of sprinklers against hydrostatic pressure and high-pressure water flow (e.g., tests of structural integrity) than the tests specified in UL 199. This is why all corrosion-resistant coatings are UL Listed, but only some are FM Approved.
Polyester paint is a good choice, especially for pool areas
Although typically only UL Listed and not FM Approved, a polyester paint coating remains a solid choice for corrosion resistance. Data published by Tyco showed that polyester-coated sprinklers only evidenced corrosion in hydrochloric acid, hydrofluoric acid, and nitric acid atmospheres—even faring better than some more “advanced” coatings on corrosion-resistant fire sprinklers. That result is only reflective of a specific type of test in a particular scenario, but it remains impressive, nonetheless.
Viking also informed us that polyester is a good choice for pool environments: “Polyester (white/black) is most often used in chlorine pool areas as this finish tends to hold up the best to the chemicals used to balance the water when chlorine is used.”
Wax finishes are very protective but easy to damage
Some manufacturers offer different variations of wax coatings, including wax-over-brass and wax-over polyester. Wax-over-lead (and plain lead coatings) also appear on some data sheets, though a Tyco representative told us that these lead coatings are being phased out. In general, wax is an effective choice among corrosion-resistant fire sprinklers, though it’s typically not FM Approved. This Viking whitepaper ranks wax and especially wax-over-polyester as superior to polyester alone.
Unfortunately, the downside of a wax coating is the care required when transporting or handling it. The coating can be damaged by tools or improper handling.
Electroless nickel PTFE (ENT) is durable and effective
ENT-coated sprinklers are often an excellent choice for corrosion resistance. This coating is typically both UL Listed and FM Approved, Viking cites it as ideal for use in industrial wash areas, chemical processing facilities, and parking garages. A Viking representative told us that ENT is also their recommendation for handling salt air, and GW Sprinkler concurs. ENT is also an extremely physically durable coating.
The downside of ENT-coated sprinklers is that they fare poorly in chlorine environments such as indoor pools. As mentioned earlier, Viking suggests polyester for these areas.
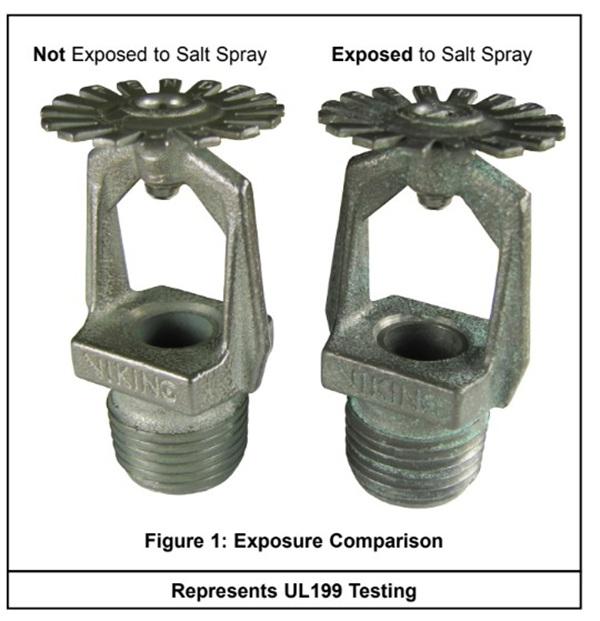
Proprietary coatings are often good choices
Some sprinkler companies offer proprietary coatings. Most notably, Victaulic offers UL-listed and FM-approved VC-250, which (based on one testing protocol) outperformed ENT and only showed corrosion signs under hydrofluoric acid, phosphoric acid, and sulfuric acid conditions. A Victaulic representative informed us that VC-250 has stood up well in chlorine environments. However, he did express reservations about a mix of high chlorine concentration, humidity, and temperature, citing chlorine pool pump rooms as one place where he might not use the coating.
Tyco has sprinklers with a proprietary polyester-stainless steel coating that performs well in tests. The company’s representatives stated that this coating can serve as a middle ground between a polyester coating and full stainless-steel construction. They offered no specifics about how poly-stainless sprinklers fare particularly well or poorly in different environments, however.
Stainless steel construction instead of a coating or finish
Some sprinklers are available in full stainless-steel construction. It is the most expensive option, but it is generally a superior choice for highly corrosive environments. However, Viking states these sprinklers may not be suitable for chlorine exposure.
The right materials keep your equipment protected in harsh environments
Corrosion is an enemy of fire sprinklers, compromising their structural integrity and creating buildup that can prevent them from operating properly. Fortunately, corrosion-resistant fire sprinklers protect sprinklers from degrading in harsh environments. Choosing the right option is a matter of understanding how corrosion affects the underlying metal and the type of environment these parts will face.
QRFS is your sprinkler partner for every application. We stock a wide range of sprinkler heads in various protective and decorative finishes. Explore our online selection today and contact our team with questions or to request assistance locating a sprinkler or finish that isn’t listed on our website.
This blog was originally posted at blog.qrfs.com. If this article helped you, check us out on X @QuickResponseFS.