NFPA acceptance testing requirements of standpipe systems
In the previous posts in this series, we covered standpipe systems, required maintenance, and the components of standpipe systems. Some of the major components we covered were pipes, water flow alarms, fire department connections, hoses, hose connections, and system valves. As we continue through our series, this installment covers required testing for standpipe systems and the NFPA codes that correspond with the different types of testing.
This post is part 4 of a 7 part series on standpipe systems:
Part 1: Fire Protection Standpipe System Overview and Introduction to NFPA 14
Part 2: Standpipe System Components and How to Maintain Them
Part 3: More Standpipe System Components and How to Maintain Them
Part 4: Acceptance Testing of Standpipes
Part 5: Maintenance Testing of Standpipes (Continued)
Part 6: Maintenance Testing for Automatic and Semiautomatic Dry Standpipes
Part 7: Standpipe Signs and Markings
The testing required for certification of new and altered standpipe systems
The complexity of standpipe systems demands diligent action to make sure all portions of the system work in an emergency. And just as system components have detailed maintenance and inspection requirements, the National Fire Protection Association (NFPA) also outlines a series of tests that must be conducted in a specific order and at exact intervals. There are two major categories of tests that must be run:
Acceptance testing is done when a standpipe system or a portion of a system is installed. In the vast majority of cases, this process coincides with the construction of a new building. It’s also required when significant modifications are made on an existing standpipe system, such as an expansion of the piping or a retrofit of the standpipe with a sprinkler system.
Ongoing testing consists of all the maintenance tests that must be completed at regular intervals after installation.
These testing requirements are primarily outlined in NFPA 14: Standard for the Installation of Standpipe and Hose Systems and NFPA 25: Standard for the Inspection, Testing, and Maintenance of Water-Based Fire Protection Systems. Additional testing procedures and requirements are also outlined in NFPA 24: Standard for the Installation of Private Fire Service Mains and Their Appurtenances and NFPA 72: National Fire Alarm and Signaling Code.
In the previous installments of our standpipe series, we’ve introduced standpipe systems and reviewed the function, inspection, and maintenance of major system components. This article will break down the acceptance testing requirements for standpipe systems in an effort to clarify NFPA code for contractors and building owners.
Are you looking to buy components or accessories for your building’s standpipe system? If so, feel free to skip directly to our selection of gauges, hose valves and accessories, pin rack items, fire hose reels, butterfly valves, and check valves, or just use the search bar at the top of the page to find what you’re looking for. If you’re looking for a test pump to conduct a hydrostatic, flush, or flow test, view our selection here.
In sequence: Underground and above-ground testing
The acceptance tests of a standpipe are done sequentially, starting with several that are run on the underground sections of the system followed by tests of the above ground components. The reason for this order is simple: Underground sections will only be exposed during an early phase of new construction, enabling contractors to spot and more easily fix deficiencies like leaks, damage, or obstructions. In addition, tests on aboveground piping could be compromised if the underground pipes haven’t been thoroughly checked first.
An important note about this sequence: If different contractors are used for the underground and above ground testing, make sure the latter contractor is present to verify the results of the underground tests.
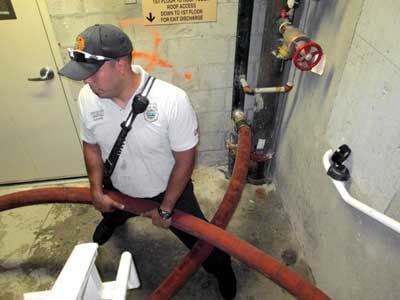
Underground testing of standpipe components
The two main tests that need to be run on underground piping are a flush test and a hydrostatic test.
Underground standpipe acceptance: Flush test
A flush test is intended to clear the underground pipes of any dirt or debris before they are hooked up to the above-ground piping.
From the 2016 Edition of NFPA 14
11.2.1 Underground piping supplying the system shall be flushed in accordance with NFPA 24.
From the 2016 Edition of NFPA 24
10.10.2.1.1 Underground piping, from the water supply to the system riser, and lead-in connections to the system riser, including all hydrants, shall be completely flushed before connection is made to downstream fire protection system piping.
A flush test involves either pumping water through the piping at a specific, elevated rate (pumping enough gallons per minute to achieve a velocity of 10ft/s) or by simply flushing the pipes with the maximum flow of the system’s water supply. Using elevated pressure is more likely to clear out the pipes, but it’s difficult to measure the velocity of the water. In either case, the test consists of running the water through the underground pipe and out of an orifice aboveground. The water is run until it comes out clear, and contractors sometimes use a strainer to collect any debris that emerges. The flush test should be completed prior to a hydrostatic test, as any obstructions left in the pipe will throw off the pressure readings of the latter test.
Underground standpipe acceptance: Hydrostatic test
A hydrostatic test must be run after the flush test to ensure that the underground piping is put together correctly, unblocked, and undamaged. The test consists of capping all outlets, running pressurized water through the system for two hours, and inspecting the pipe for leaks while monitoring gauges for any pressure loss that would indicate a leak. The water should be pumped and the pressure monitored from the lowest possible point in the system.
From the 2016 Edition of NFPA 14
11.4.1* General. All new systems, including yard piping and fire department connection piping, shall be tested hydrostatically at not less than 200 psi (13.8 bar) or 50 psi (3.5 bar) in excess of the system working pressure, whichever is greater for 2 hours.
11.4.2 The hydrostatic test pressure shall be measured at the low elevation point of the individual system or zone being tested.
11.4.3 The standpipe system piping shall show no leakage other than as permitted by 11.4.4.
11.4.4 Underground pipe shall be tested in accordance with NFPA 24.
Unlike hydrostatic tests that are done on aboveground piping, NFPA 24 permits some pressure loss in the underground pipe. This is because a small amount of leakage through fire hydrant drains is inevitable on underground mains connected to hydrants, plus it’s difficult to tighten the joints on underground piping to the point where there will be no small leaks. A loss of 5 psi is permitted during the test. Anything greater than that indicates a problem that needs to be found and fixed.
Underground standpipe acceptance: Additional testing
Prior to testing aboveground piping, three more areas of the system should be tested. Private fire hydrants that are attached to the underground main should be opened and water pumped through to flush out the barrel, followed by being closed to make sure they seal properly under system pressure (25: 7.3.2.1). In addition, control valves must be opened and closed to make sure they work under system water pressure (which may require a test pump; 14: 11.6.1). Finally, the backflow preventer must be forward flow tested (14: 11.5.3.1). The backflow preventer is the essential check valve that prevents stagnant water in the standpipe system from pushing back into and contaminating the city water supply. To test it, simply flow water (at system demand) through the backflow preventer assembly to an open orifice.
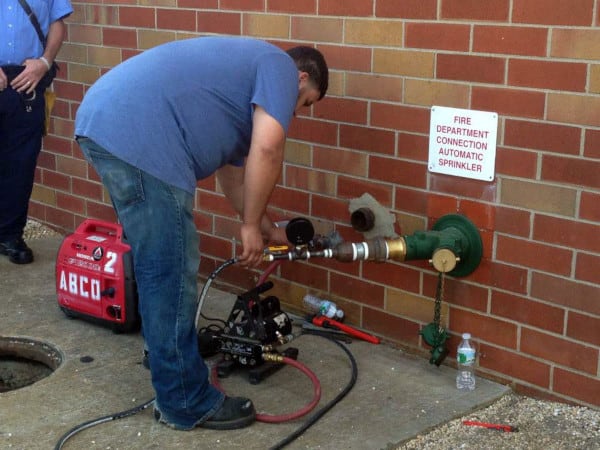
Above-ground Testing of Standpipe Systems
The aboveground pipe and equipment are ready for acceptance testing after the underground components are verified. These tests include:
Above-ground standpipe acceptance: Flush test
Just like the underground pipes, the fire department connection piping also needs to be flushed to “remove any construction debris and trash.”
From the 2016 Edition of NFPA 14
11.2.2 Piping between the fire department connection and the check valve in the inlet pipe shall be flushed with a sufficient volume of water in order to remove any construction debris and trash accumulated in the piping prior to the completion of the system and prior to the installation of the fire department connection.
Above-ground standpipe acceptance: Hydrostatic test
Above-ground piping also needs to be hydrostatically tested for two hours at 200 psi or 50 psi more than system working pressure, whichever is greater. During this period, the piping should be visually inspected for leaks, and gauges must be monitored for any drop in pressure that indicates a leak. Much like the hydrostatic test of the underground piping, the test pressure should be read from the lowest point in the system or, since standpipe systems can have multiple vertical zones depending on the size of the building, the lowest point in each zone.
From the 2016 Edition of NFPA 14
11.4.1* General. All new systems, including yard piping and fire department connection piping, shall be tested hydrostatically at not less than 200 psi (13.8 bar) or 50 psi (3.5 bar) in excess of the system working pressure, whichever is greater for 2 hours.
11.4.2 The hydrostatic test pressure shall be measured at the low elevation point of the individual system or zone being tested.
While some drop in pressure (and some corresponding degree of leakage) is permitted when hydrostatically testing underground piping, ostensibly no drop in pressure at the lowest system or zone gauge is permitted in above-ground pipe. There is an exception to this strict standard, however: If the temperature dropped significantly during the two-hour test, water could have contracted relative to air trapped in the system, causing a slight loss of pressure. What is deemed an acceptable pressure loss is a judgment call based on the temperature change, the size of the system, and whether there is any other possible reason for the loss (e.g., the presence of a visible leak in the piping). In addition, some pressure loss is naturally permitted at gauges read on higher portions of the system to account for gravity and friction.
Important note: An air pressure test can be temporarily substituted for a hydrostatic test if freezing temperatures make the latter impossible at the time:
From the 2016 Edition of NFPA 14
11.4.5 Where cold weather prevents testing with water, an interim air test shall be permitted to be conducted prior to the standard hydrostatic test.
11.4.5.1 An air pressure leakage test at 40 psi (2.8 bar) shall be conducted for 24 hours.
11.4.5.2 Any leakage that results in a loss of pressure in excess of 11/2 psi (0.1 bar) during a continuous 24-hour period shall be corrected.
This is only an interim measure; a full hydrostatic test will need to be conducted when weather permits.
In addition, acceptance hydrostatic testing is required of any existing standpipe system that is modified with new piping, though “modifications that cannot be isolated, such as new valves or the point of connection for new piping, shall not require testing in excess of system static pressure.” (14: 11.4.7.2)
Above-ground standpipe acceptance: Hose threads
Remember, different fire departments can use different size hoses (such as the use of 3” inlets in San Francisco and New York), as well as different types of threads or couplings (such as non-threaded, 5” Storz connections). Thus, one of the most basic acceptance tests for a new standpipe system is to make sure the connections are compatible with the equipment used by local authorities.
From the 2016 Edition of NFPA 14
11.3.1 All hose connection and fire department connection threads shall be tested to verify their compatibility with threads used by the local fire department.
11.3.1.1 The test shall consist of threading coupling samples, caps, or plugs onto the installed devices.
Above-ground standpipe acceptance: Flow test
A flow test must be run to verify that enough pressure can be achieved at the most remote hose connection when the standpipe operates at system demand. The design pressure that must be achieved at the most remote connection for Class I and Class III systems is usually 100 psi, whereas Class II systems must usually achieve at least 65 psi. These values can be measured using either a flow meter or by interpreting the difference in pressure at individual gauges placed at the fire department connection and the most remote hose outlet. In automatic standpipes, the test can be done using the readily-accessible water in the system, whereas manual systems require a pump that pressurizes water sourced from a hydrant or tank.
From the 2016 Edition of NFPA 14
11.5.1* The standpipe system shall be tested to verify system demand.
11.5.1.1 The test required by 11.5.1 shall be permitted to be waived where acceptable to the AHJ.
11.5.1.2 This test shall be conducted by flowing water simultaneously from the outlet(s) indicated in the approved hydraulic calculations of each standpipe as required by Sections 7.8 and 7.10.
11.5.1.2.1 For each additional standpipe, the required flow shall be permitted to be taken from any hose connection on that standpipe.
11.5.2* For a manual standpipe, a fire department pumper, portable pump of a capacity to provide the required flow and pressure, or other approved means shall be used to verify the system design by pumping into the fire department connection.
11.5.2.1 Where allowed by the authority having jurisdiction, the test required by 11.5.2 shall be permitted to be waived.
Above-ground standpipe acceptance: Pressure-reducing devices
All pressure-reducing valves must be tested to ensure that they work as designed:
The test is conducted by flowing 250 gpm through the Class I or Class III outlet with a pressure gauge on the upstream side and a pressure gauge on the downstream side of the device. The difference between the readings on the pressure gauges will indicate whether the device is working properly.
In addition, valves that are arranged in a series must also be tested in a series.
From the 2016 Edition of NFPA 14
11.5.5.1* Each pressure-regulating device shall be tested to verify that the installation is correct, that the device is operating, and that the inlet and outlet pressures and flow at the device are in accordance with design.
11.5.5.1.1 Where pressure-reducing valves are arranged in series, the downstream pressure-reducing valve shall be tested at both the discharge pressure from the upstream pressure-reducing valve and with the upstream pressure-reducing valve bypass open.
11.5.5.2 Static and residual inlet pressure and static and residual outlet pressure and flow shall be recorded on the contractor’s test certificate.
The 1991 fire at the Meridian high-rise in Philadelphia is a stark example of the consequences of failing to test pressure-regulating devices. Numerous pressure-reducing valves that had been installed at hose connections on upper floors weren’t properly calibrated, and thus wound up “supplying only between 40 to 50 psi at the nozzle tip” during the emergency. This crucial component failure contributed to the death of 3 firefighters and the injury of 24 others, as well as the complete loss of nine floors and millions of dollars in damage.
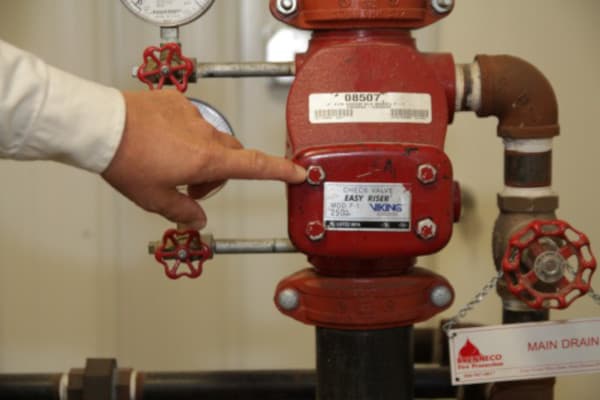
Above-ground standpipe acceptance: Main drain flow test
Automatic and semiautomatic standpipes with a connection to a water supply require a main drain test. This test verifies that valves between the water supply and the drains are open, plus sets a benchmark pressure reading for future maintenance testing.
From the 2016 Edition of NFPA 14
11.5.6.1 The main drain valve shall be opened and shall remain open until the system pressure stabilizes.
11.5.6.2 The static and residual pressure shall be recorded on the contractor’s test certificate.
If there is hesitation in the system pressure returning to static pressure after shutting the drain, there may be a blockage, partially-closed valve, or other issue.
Above-ground standpipe acceptance: Additional tests
A few more acceptance tests are required, though some only apply to certain types of systems:
- All alarm and supervisory devices must be tested in accordance with NFPA 72. (14: 11.7)
- If a backflow preventer is a part of the aboveground system, it must be flow tested as previously described for underground piping. (14: 11.5.3)
- Control valves and hose valves must be manually tested as follows:
From the 2016 Edition of NFPA 14
11.6.1 Each valve intended to be manually opened or closed shall be operated by turning the handwheel crank or wrench for its full range and returning it to its normal position.
11.6.2 Hose valve caps shall be tightened sufficiently to avoid leaking during the test and removed after the test to drain water and relieve pressure.
Specific additional acceptance tests must be run for automatic dry and semiautomatic dry systems:
From the 2016 Edition of NFPA 14
11.5.7.1 Automatic dry and semiautomatic systems shall be tested by initiating a flow of water from the hydraulically most remote hose connection. [In systems with pumps, the pump may be activated during this test]
11.5.7.2 The system shall deliver a minimum of 250 gpm (946 L/min) at the hose connection within 3 minutes of opening the hose valve if the system capacity exceeds 750 gal (2480 L).
11.5.7.3 Each remote control activation device for operating a semiautomatic system shall be tested in accordance with the manufacturer’s specifications and instructions.
11.5.7.4 In addition to the standard hydrostatic test, an air pressure leakage test at 40 psi (2.7 bar) shall be conducted for 24 hours. Any leakage that results in a loss of pressure in excess of 1.5 psi (0.1 bar) for the 24 hours shall be corrected. [13:25.2.2.1]
An important note on acceptance testing: In addition to all of the above tests, any automatic or semiautomatic standpipe system requires acceptance testing of the onsite fire pump. Because of the mechanical complexity of a pump, these testing requirements are extensive and specifically outlined in NFPA 20: Standard for the Installation of Stationary Pumps for Fire Protection.
To be continued: The Complete Guide to Standpipe Systems
This concludes part four of our review of standpipe systems, a look at the acceptance testing required for new and altered systems. In the next installment of this series, we review the regular NFPA testing requirements for existing systems.
If you’re looking to buy components for your standpipe system, QRFS offers a range of gauges, hose valves and accessories, pin rack items, fire hose reels, butterfly valves, and check valves, or just use the search bar at the top of the page to find what you’re looking for. If you’re looking for a test pump to conduct a hydrostatic, flush, or flow test, view our pumps here.
See the Full Selection of Standpipe System Components Here
If you have any other questions about standpipes or need help finding an item, give us a call at 888.361.6662 or fill out our contact form and we’d be happy to assist.
Check us out on Facebook and Twitter!
View Other Posts in this Series on Standpipe Systems
Part 1: Fire Protection Standpipe System Overview and Introduction to NFPA 14
Part 2: Standpipe System Components and How to Maintain Them
Part 3: More Standpipe System Components and How to Maintain Them
Part 4: Acceptance Testing of Standpipes
Part 5: Maintenance Testing of Standpipes (Continued)
Part 6: Maintenance Testing for Automatic and Semiautomatic Dry Standpipes
Part 7: Standpipe Signs and Markings
Additional Sources:
- Isman, Kenneth E. Standpipe Systems for Fire Protection. Springer International Publishing.
- NFPA 14: Standard for the Installation of Standpipe and Hose Systems (2016)
- NFPA 24: Standard for the Installation of Private Fire Service Mains and Their Appurtenances (2016)
- NFPA 25: Standard for the Inspection, Testing, and Maintenance of Water-Based Fire Protection Systems (2017)