Dry standpipes, both automatic and semiautomatic, require maintenance tests of priming water, essential valves, and other components
In the previous installments of our standpipe series, we’ve detailed the different types and components of standpipes and the acceptance and maintenance testing requirements for most systems. This article will break down additional maintenance testing requirements specifically required for automatic and semiautomatic dry standpipes defined in NFPA 25: Standard for the Inspection, Testing, and Maintenance of Water-Based Fire Protection Systems.
This post is part 6 of a 7 part series on standpipe systems:
Part 1: Fire Protection Standpipe System Overview and Introduction to NFPA 14
Part 2: Standpipe System Components and How to Maintain Them
Part 3: More Standpipe System Components and How to Maintain Them
Part 4: Acceptance Testing and Ongoing System Maintenance
Part 5: Maintenance Testing of Standpipes (Continued)
Part 6: Maintenance Testing for Automatic and Semiautomatic Dry Standpipes
Part 7: Standpipe Signs and Markings
Are you looking to buy components or accessories for your building’s standpipe system? If so, feel free to skip directly to our selection of gauges, hose valves and accessories, pin rack items, fire hose reels, butterfly valves, check valves, and hydrostatic test pumps.
A summary of the unique maintenance testing requirements for these dry standpipe systems
Automatic and semiautomatic standpipe systems are unique in several regards. Because they are dry systems, water does not sit in the piping leading to the hose outlets. In its place, pressurized air or nitrogen fills essentially all (automatic) or most (semiautomatic) of the piping, with water only flooding the system in an emergency. Both types of standpipe require an onsite fire pump and additional, specific components – such as a differential dry-pipe valve (automatic) or a deluge valve tied to an alarm panel and an initiating device (semiautomatic) – to make them work.
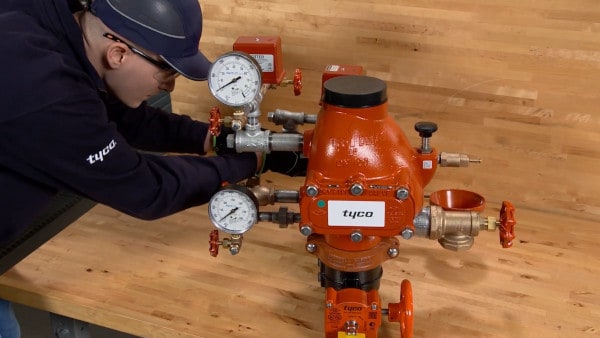
This design is a trade-off: The set-up of these systems mitigates the risk of water damage due to accidental discharge (semiautomatic) or damaging the pipes when there are freezing temperatures (automatic and semiautomatic), but their complexity demands additional maintenance and testing, it is harder to identify leaks in dry pipe, and the design slightly delays access to water during a fire. Nevertheless, with proper inspection, maintenance, and testing, dry standpipes can be very reliable and effective fire protection systems.
Please note: this guide covers additional maintenance tests that are specific to automatic and semiautomatic dry standpipes; individuals responsible for maintaining these types of standpipes will also need to conduct the regular testing covered in Part 5 of this series, “Maintenance Testing of Standpipes.”
Dry standpipe maintenance: priming water level tests
The term “priming water” means different things in different standpipe systems or components of systems. For example, in manual wet standpipes, priming water is defined as the water that constantly sits in the pipes, reducing “the time it takes to get water to the hose station outlets.” But in the context of dry standpipe maintenance testing, priming water serves a different purpose.
Automatic dry standpipe systems (as well as automatic dry sprinkler systems) have differential dry pipe valves that separate the pressurized air contained in most of the piping from the pressurized water supply. The pressurized air holds the clapper on the dry pipe valve shut until a hose valve or other orifice is opened farther down the system. Once air begins to escape from this hose connection and the air pressure drops in the piping, the pressurized water pushes the dry pipe valve open and quickly floods the system.
Many of these valves are filled with priming water between the water source/connection and the clapper that separates the water from the pressurized air. The purpose of this priming water is to “assist in providing a positive seal at the air seat ring to prevent air from escaping into the intermediate chamber and on to the atmosphere.” Of course, if air were to escape then the air pressure may drop, meaning there is no guarantee that the clapper would remain closed and prevent water from entering the pipes. Thus, the priming water level must be tested on a quarterly basis to ensure that a proper seal is in place within the valve.
From the 2017 Edition of NFPA 25 (brackets ours)
13.4.3.2.1* [Preaction Valves] The priming water level in supervised preaction systems shall be tested quarterly for compliance with the manufacturer’s instructions.
13.4.5.2.1* [Dry Pipe Valves/Quick-Opening Devices] The priming water level shall be tested quarterly.
Most valves have a “priming water test port;” the test merely consists of opening it and noting whether water or air is emitted. If it’s water, the system passes the test; if it’s air, water needs to be added to achieve the appropriate water level.
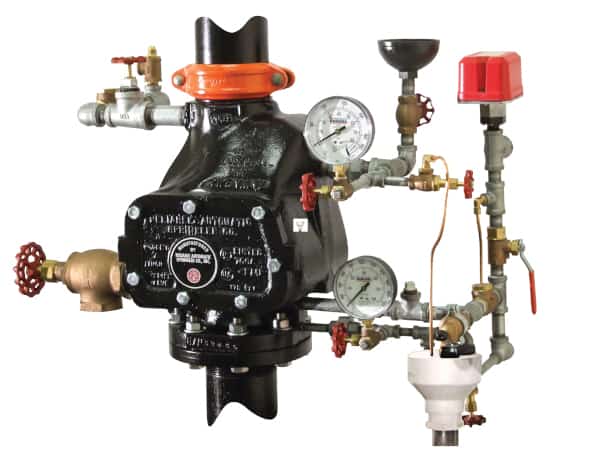
Note: some valves require that all of the pressurized air is bled from the system before filling the valve through a priming water fill connection, whereas other valves are more conveniently designed to allow a fill without depressurizing the system. In all cases, be sure to consult the manufacturer’s instructions to determine the necessary steps for your specific valves.
Trip testing of preaction and dry pipe valves
NFPA 25 outlines different requirements for “trip testing” – testing to make sure that the preaction system springs into action in an emergency – that depend on set intervals plus whether a freezer is part of the protected space.
From the 2017 Edition of NFPA 25
13.4.3.2.2 Except for preaction systems covered by 13.4.3.2.4, every 3 years the preaction valve shall be trip tested with the control valve fully open.
13.4.5.2.2.2* Every 3 years and whenever the system is altered, the dry pipe valve shall be trip tested with the control valve fully open and the quick-opening device, if provided, in service.
13.4.3.2.3 During those years when full flow testing in accordance with 13.4.3.2.2 is not required, the preaction valve shall be trip tested with the control valve partially open.
13.4.5.2.2* Each dry pipe valve shall be trip tested annually during warm weather.
13.4.5.2.2.3* During those years when full flow testing in accordance with 13.4.5.2.2.2 is not required, each dry pipe valve shall be trip tested with the control valve partially open.
13.4.3.2.4 Preaction valves protecting freezers shall be trip tested in a manner that does not introduce moisture into the piping in the freezer.
13.4.5.2.2.1 Dry pipe valves protecting freezers shall be trip tested in a manner that does not introduce moisture into the piping in the freezers.
13.4.3.2.6* Manual Operation. Manual actuation devices shall be operated annually.
13.4.3.2.7 Return to Service. After the annual trip test, the preaction system shall be returned to service in accordance with the manufacturer’s instructions.
13.4.3.2.9* Records indicating the date the preaction valve was last tripped and the tripping time, as well as the individual and organization conducting the test, shall be maintained at a location or in a manner readily available for review by the authority having jurisdiction.
13.4.5.2.2.4 When refilling a dry system, the air supply shall be capable of restoring normal air pressure in the system within 30 minutes.
13.4.5.2.2.5 The requirements of 13.4.5.2.2.4 shall not apply in refrigerated spaces maintained below 5°F (–15°C), where normal system air pressure shall be permitted to be restored within 60 minutes.
For the freezer exception noted in 13.4.3.2.4 and 13.4.5.2.2.1, a control valve that feeds the freezer area simply needs to be shut so that water does not reach and/or bypasses that space. The remainder of the trip testing is the same for all systems. Since dry standpipe systems are usually deployed in areas subject to freezing temperatures, both the three-year full flow trip test and the partial flow trip test done in the other two years should be completed at warmer times of the year.
Before conducting either test, the water supply line first needs to be flushed – the main drain should be opened and “water at full pressure should be discharged long enough to clear the pipe of any accumulation of scale or foreign material.”
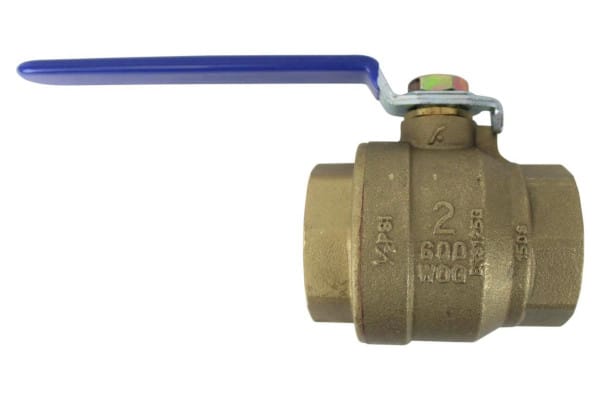
To conduct the three-year, full flow trip test: After flushing is complete, measure the pre-test air pressure in the dry section of the pipes and the water pressure in the piping near the water supply.
Once these measurements are recorded, a test connection, which can be a dedicated trip test connection or just the most remote hose connection in the system, is opened. Simply opening this valve trips the system in the case of an automatic dry standpipe; the air pressure drops and the differential dry pipe valve opens to flood the system. To trip a semiautomatic standpipe, the tester must engage an initiator, usually a manual pull station or button. Note that the full flow trip test requires two people – one at the downstream test connection and one at the valve where the system is tripped. This pair must remotely communicate exactly when each event occurs to achieve the timing required for the test.
Once the system is tripped:
- Record how long it takes for the dry pipe valve to trip after the test connection is opened when testing an automatic dry system. In the case of a semiautomatic dry system, simply determine whether the deluge valve opens (trips) when the initiator is engaged.
- Record how long it takes for the water to travel through the piping and pour out of the test connection.
- Record the air pressure reading when the valve trips.
- After the water flows out of the test connection for a few minutes, shut the control valve, drain the water via the main drain and auxiliary drains, reset the dry pipe/deluge valve, close all drains, and refill the dry portion of the pipe with pressurized air or nitrogen.
There are no pass/fail criteria for the trip test outlined in NFPA 25, but there is some guidance in the standpipe acceptance trip testing required in NFPA 14. The latter code “allows systems with a total volume in the piping up to 750 gallons to pass the test with no specific time for water delivery [to the test connection],” though the time it takes should be compared to previous tests; any significant slowdown could indicate a leak or blockage in the piping. Any system with over 750 gallons in total volume should deliver water to the test connection within three minutes of being tripped.
Be sure to record the results of each full flow trip test to create a history:
- Air and water pressure (before the test)
- Air pressure at trip
- Elapsed time at trip
- Water delivery time
The partial flow trip test conducted in off years between full-flow tests is much easier. Simply initiate the test with the main control valve only partially open. Once the system successfully trips, close the valve, drain the small amount of water that made its way into the piping, and otherwise reset the system, making sure the air is sufficiently pressurized.
In both full flow and partial flow trip tests of dry pipe valves, the valve must trip within 60 seconds of the action designed to trip it, and water should take at least 60 seconds to discharge from the test connection after the system is tripped.
Dry standpipe maintenance: air leakage tests
Dry and preaction systems require a test for air/nitrogen leakage every three years. While the pressurized gas in dry standpipe systems has traditionally been air, many owners and contractors now use nitrogen because it causes less corrosion in the pipes. There are two methods of conducting the test; one adds pressure for two hours and looks for a certain loss, whereas the other test simply shuts off the air source and sees if the low air pressure alarm goes off due to a leak.
From the 2017 Edition of NFPA 25
13.4.3.2.5 Preaction systems shall be tested once every 3 years for air leakage, using one of the following test methods:
(1) Perform a pressure test at 40 psi (3.2 bar) for 2 hours. The system shall be permitted to lose up to 3 psi (0.2 bar) during the duration of the test. Air leaks shall be addressed if the system loses more than 3 psi (0.2 bar) during this test.
(2) With the system at normal system pressure, shut off the air source (compressor or shop air) for 4 hours. If the low air pressure alarm goes off within this period, the air leaks shall be addressed.
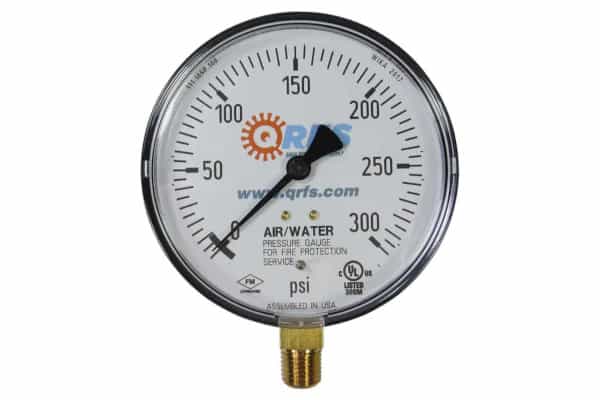
Dry standpipe maintenance: low-pressure alarm, low-temperature alarm, and air pressure maintenance tests
The low air pressure alarm itself also needs to be tested quarterly, whereas low-temperature alarms installed in valve enclosures and automatic pressure maintenance devices must be tested annually:
From the 2017 Edition of NFPA 25
13.4.3.2.10 Low air pressure alarms, if provided, shall be tested quarterly in accordance with the manufacturer’s instructions.
13.4.3.2.11 Low temperature alarms, if installed in valve enclosures, shall be tested annually at the beginning of the heating season.
13.4.3.2.12 Automatic air pressure maintenance devices, if provided, shall be tested yearly at the time of the annual preaction valve trip test, in accordance with the manufacturer’s instructions.
Low-pressure alarms and pressure maintenance devices should be tested according to the manufacturer’s instructions, with the latter done at the same time as the annual trip test. Annual low-temperature alarm tests are conducted by simply lowering the temperature enough to trip the alarm below its warning threshold. In freezing weather, this may be accomplished by simply turning off the heat in the room where the sensor is located; otherwise, the test can be completed by spraying the alarm with a refrigerant.
To be continued: The Complete Guide to Standpipe Systems
This concludes part six of our review of standpipe systems, a look at the maintenance testing specific to automatic and semiautomatic dry existing systems. In the next and final installment of this series, we’ll outline the NFPA signage requirements for all standpipe systems.
If you’re looking to buy components for your standpipe system, QRFS offers a range of gauges, hose valves and accessories, pin rack items, fire hose reels, butterfly valves, check valves, and hydrostatic test pumps. And if you have any questions about standpipes systems – or need help finding an item – give us a call at 888.361.6662 or contact us at support@qrfs.com.
Browse our selection of components for standpipe systems or our entire fire protection catalog
This blog was originally posted at blog.qrfs.com. Check us out at facebook.com/QuickResponseFireSupply or on Twitter @QuickResponseFS.
View Other Posts in this Series on Standpipe Systems
Part 1: Fire Protection Standpipe System Overview and Introduction to NFPA 14
Part 2: Standpipe System Components and How to Maintain Them
Part 3: More Standpipe System Components and How to Maintain Them
Part 4: Acceptance Testing of Standpipes
Part 5: Maintenance Testing of Standpipes (Continued)
Part 6: Maintenance Testing for Automatic and Semiautomatic Dry Standpipes
Part 7: Standpipe Signs and Marking
Additional Sources:
1.NFPA 25: Standard for the Inspection, Testing, and Maintenance of Water-Based Fire Protection Systems (2017)
2.Isman, Kenneth E. Standpipe Systems for Fire Protection. Springer International Publishing.
3.“THE BEGINNER’S GUIDE TO FIRE SPRINKLER TESTS.” Capitol Fire Blog. https://capitolfire.com/the-beginners-guide-to-fire-sprinkler-tests/
4.“Fire Sprinkler Systems Inspections.” Complete Fire Protection, Inc. https://www.completefire.com/inspections/16-fire-sprinkler-systems-inspections.html
5.Victor, Terry. “Best Practices for Performing Less Frequent Tests Required by NFPA 25-2014.” 2014 NFPA Conference & Expo. https://www.nfpa.org/~/media/7C38270782D74787812EEA298932DEAE.pdf