Imprecise results and equipment failure can be avoided by choosing the right gauge range for pitot testing
Pitot gauge kits help inspectors accurately measure flows from fire hydrants, hoses, nozzles, and other outlets in water-based systems. Users hold these tools in front of a stream of water, guiding it through a smooth, narrow tube to a pressure gauge. But fire hydrants, fire pumps, and hose nozzles all flow water at different rates. To get proper readings at different outlets—and to prevent damage to testing equipment—the pressure gauge used needs the proper dial range.
Should users choose a gauge that covers a broad range like 0–300 pounds per square inch (PSI), or one that only goes from 0–60 PSI? Something in between? And why would some inspectors purchase one that goes down to negative 30 PSI? In this article, we look at gauge construction—and a few use cases in the fire protection industry—to help consumers choose the right dial range for their pitot gauge.
If you’d like, you can jump directly to our selection of pitot gauge kits and equipment, air and water pressure gauges, or our complete supply of testing and monitoring equipment.
Hydrant orifice sizes have a substantial impact on the PSI a pitot gauge measures
Firefighters can’t afford to get to the site of a fire only to discover they don’t have enough water to fight it. As such, fire hydrants must be periodically checked to confirm that they can deliver water at the rate needed. These flow rates are often measured in gallons per minute (GPM).
Pitot gauge kits are a time-tested way to estimate the GPM of water streams. Users place the blade of the pitot tube into the stream of water and read the pressure, in pounds per square inch (PSI), at an attached gauge. Using a conversion formula, inspectors can convert the measured PSI to GPM for a reasonably accurate estimation of actual flow rates.
The National Fire Protection Association (NFPA), a leading nonprofit organization in the fire protection industry, has compiled a list of best practices for hydrant testing in NFPA 291: Recommended Practice for Fire Flow Testing and Marking of Hydrants. NFPA 291’s color-coding scheme—with light blue, green, orange, and red bonnets indicating a GPM range for each hydrant—can be used to estimate expected pressures at similar hydrants.
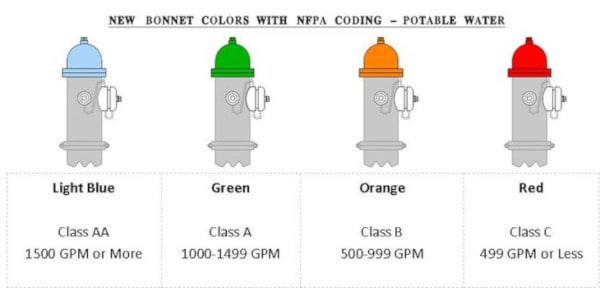
Pitot gauge readings may be less useful when testing at large outlets
To show how PSI varies depending on how the flow is measured, we’ll use the PSI to GPM calculator we developed in an earlier article. Without going into too much detail, we can use the shape of the hydrant’s orifice, the diameter of that orifice, and the hydrant’s expected GPM to estimate the pressures we’ll see at that hydrant. Note that these readings are theoretical. While they may be accurate enough to help users choose an appropriate dial range, actual flow rates will differ (particularly with large orifices).
Take a look at some likely readings for pitot gauges placed directly in front of a large orifice (pumper nozzle) on an open hydrant. For hydrants with a 4 1/2” square outlet that projects into the barrel, some rough PSI readings might be:
- 1 PSI or less—red (Class C) hydrants (499 GPM or less)
- 1 to 5.6 PSI—orange (Class B) hydrants (500 to 999 GPM)
- 6 to 12.6 PSI—green (Class A) hydrants (1,000 to 1,499 GPM)
- Above 12.6 PSI—light blue (Class AA) hydrants (1,500 GPM or more)
A problem emerges here: very slight changes in PSI represent especially large changes in our estimated flow rates. The accuracy of readings taken from the pumper nozzle—the largest orifice on a hydrant—may be questionable at best. In addition, large nozzles may not fill completely at pressures typically used with a pitot tube, raising additional questions about the validity of the results. As such, hydrants shouldn’t be directly tested from outlets this large.
Smaller outlets raise dynamic pressure, making results easier to read and more accurate
Rather than measuring hydrant flows at the pumper nozzle, NFPA 291 recommends measuring flows at smaller outlets. Many hydrants feature 2 1/2” nozzles with National Standard Thread (NST). And where water mains deliver especially low pressures, inspectors may attach a straight stream flow nozzle. With a smooth interior and a reduced outlet size, these devices straighten the stream and make pressure easier to measure.
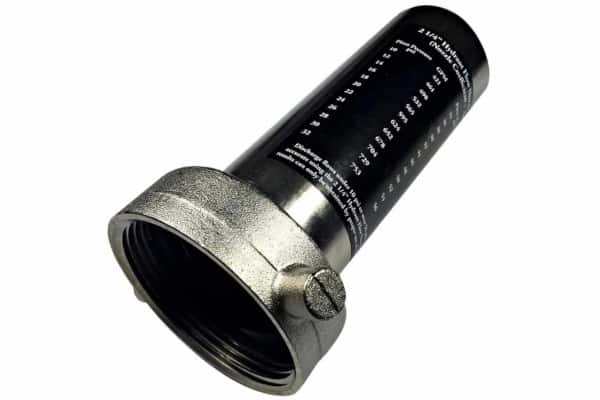
If, for example, you measure flows directly from a smooth, rounded 2 1/2” outlet, you might see PSI readings like these:
- 9 PSI or less—red (Class C) hydrants (499 GPM or less)
- 10 to 35 PSI—orange (Class B) hydrants (500 to 999 GPM)
- 36 to 80 PSI—green (Class A) hydrants (1,000 to 1,499 GPM)
- Above 80 PSI—light blue (Class AA) hydrants (1,500 GPM or more)
But if you use a smooth flow nozzle with a 2 1/4” outlet, you might see PSI readings like these:
- 14 PSI or less—red (Class C) hydrants (499 GPM or less)
- 15 to 56 PSI—orange (Class B) hydrants (500 to 999 GPM)
- 57 to 127 PSI—green (Class A) hydrants (1,000 to 1,499 GPM)
- Above 127 PSI—light blue (Class AA) hydrants (1,500 GPM or more)
Note that flow nozzles like these may be designed only for use at specified pressures. While these numbers are helpful in theory, it’s important to observe the manufacturer’s recommendations—and best flow-testing practices—when conducting actual tests.
As these numbers show, with a smaller outlet, PSI readings are larger (and further apart) for a given difference in GPM. This can make it much easier to read a gauge with a reasonable degree of accuracy. But why?
Water moves more quickly through narrower pipes. Somewhat confusingly, this increase in speed actually reduces the water’s pressure inside the pipe (known as static pressure). But pitot tubes are designed to measure the force water exerts on something that blocks its path. This dynamic or velocity pressure increases as water moves more quickly—as it does in narrower pipes. That’s partly why a 2 1/2” hydrant outlet, or a hydrant flow nozzle, produces higher and more easily measured pressures than a large pumper nozzle.
For easy reading and maximum durability, choose a pitot tube pressure gauge that places the pressures you expect to see in the middle of the dial
Ashcroft Inc., a globally recognized manufacturer of pressure gauges, recommends that the operating pressure of any gauge be kept to within 25 to 75 percent of the overall range of the dial. For example, a gauge with a 0-30 PSI dial range should usually operate between 7.5 and 22.5 PSI. A gauge with a 0–100 PSI dial range ideally operates between 25 and 75 PSI.
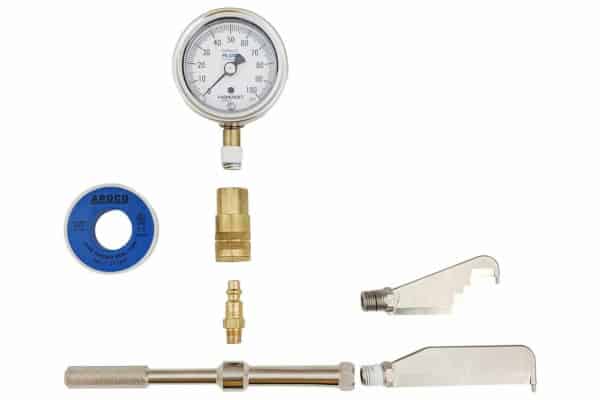
Not observing this rule can have unfortunate consequences for gauge life and the accuracy of your flow tests. If a pressure reading goes higher than the dial scale, it’s impossible to tell just how extreme that pressure actually is. It may not be possible to get a reading—and the gauge may be damaged in the process.
What about gauges with sub-zero readings? While there’s no such thing as negative pressure (a vacuum, after all, has 0 psi), a gauge dial that shows negative PSI reading may be useful when measuring low flows because:
- Gauges will last longer when measuring pressures in the middle of the dial’s range
- Some gauges may have greater accuracy within the mid-range
For example, a dial range of -30–0–100 would have its midrange starting a little under 3 PSI (25% of the way along the total dial range) and ending around 68 PSI (75% of the total dial range). This range can be more useful for users measuring especially low flows. It provides an even lower floor than a 0–60 PSI gauge, which isn’t in its recommended range until 15 PSI.
Another benefit of the negative range is that users can more readily see when the gauge is not fully calibrated. Pressure gauges measure relative pressure: in other words, when they read zero, they ignore the pressure of the earth’s atmosphere. But atmospheric pressure varies based on your altitude, meaning that each gauge must be appropriately calibrated for the location in which it’s used. A gauge that consistently starts below zero is not calibrated correctly—or it’s damaged. A sub-zero range can make problems like these apparent earlier, prompting recalibration or replacement.
Some pitot tube pressure gauges have limited accuracy above and below specified pressures, while others provide the same accuracy throughout the dial range
A gauge with 1% full-range accuracy and a broader dial scale will read less precisely than the same gauge with a narrower dial scale. For example, a gauge marked 0-60 PSI with 1% full-range accuracy will be accurate within +/- .6 PSI, but a similar gauge marked 0-300 will only be accurate within +/- 3 PSI.
This assumes that you can read the gauge precisely. The broader the range, the closer the numbers are together. And many hand-held pitot gauges will have dials less than 3” in diameter (regardless of range). Coupling small dials with wide ranges may make it difficult to take an exact reading.
Also, note that some gauges may be less accurate outside of a given range. For example, many gauges supplied with QRFS’s pitot gauge kits provide 1% accuracy only in their mid-range. In theory, this shouldn’t matter: consumers should stick to the mid-range to avoid wearing out their gauges prematurely. But when gauges don’t have full range accuracy, and when they may be used outside of their recommended range, it’s even more important to select the dial range carefully.
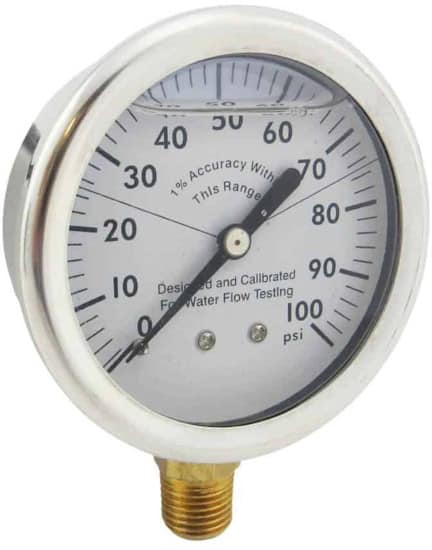
Choose pitot gauges with the right dial range for expected water flows
If all you do with your pitot tube pressure gauge is measure fire hydrant flow rates in one location, a single gauge may be fine. But nozzles, hydrants, pumps, and different water supply systems will all have different flow rates. To help inspectors choose a gauge that’s appropriate for the pressures and flows they expect, we offer the following recommendations:
- 0–60 PSI dials – test pressures from 15–45 PSI. This gauge is a good choice for hydrant testing in accordance with NFPA 291 section 4.8 (2016 edition), which recommends keeping PSI between 10 and 30 PSI—by opening multiple hydrants, if necessary.
- 0–100 PSI dials – test pressures from 25–75 PSI. Some water supply inspectors conduct tests at pressures exceeding 30 PSI. For example, Zurich Services, a risk management firm, suggests testing at pressures between 10 and 60 PSI. These gauges may be ideal when faced with moderate flows at a 2 1/2” hydrant orifice.
- 0–160 PSI dials – test pressures from 40–120 PSI. These gauges may be suitable when testing many class A or AA hydrants with a 2 1/2” outlet or a 2 1/4” flow nozzle.
- 0–200 PSI dials – test pressures from 50–150 PSI.
- 0–300 PSI dials – test pressures from 75–225 PSI.
- -30–0–100 dials – test pressures from 5–67.5 PSI. This gauge is also a suitable choice for hydrant testing in accordance with NFPA 291—particularly when pressures between 10 and 15 PSI are expected. Like other dials with a negative range, the -30-0-100 PSI gauge also provides an extra degree of assurance that the gauge is properly zeroed.
- -30–0–200 dials – test pressures from 5–142.5 PSI.
- -30–0–300 dials – test pressures from 5–217.5 PSI.
If you are doing more advanced testing of fire hoses and nozzles, test headers, pumps and other parts of your water delivery strategy, you may find that you need to invest in a few different gauges with different dial ranges. Civilians, firefighters, and property may someday depend on the accuracy of your testing.
If you’re looking for flow testing equipment, QRFS carries a supply of complete pitot gauge kits. Each comes with your choice of any gauge dial range listed above—and the included case has room for any extra gauges needed. Our round pitot gauge kit and standard pitot gauge kit are accurate to 1% in their mid-range, and our Inspector’s Choice kit provides a remarkable 1% accuracy across its entire range.
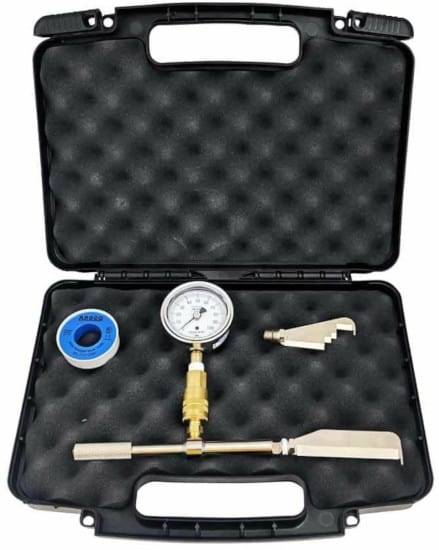
We’ve also got a number of testing and monitoring products, including replacement pitot blades, pitot handles, and standalone water pressure gauges compatible with any pitot tube that has a 1/4” gauge connection.
View our selection of pitot gauge kits and equipment.
Not sure what gauge(s) you need? Concerned about compatibility with your pitot tube? Call us at +1 (888) 361-6662 or email support@qrfs.com.
This blog was originally posted at blog.qrfs.com. If this article helped you, check us out at Facebook.com/QuickResponseFireSupply or on Twitter @QuickResponseFS.