Digital pressure gauges have made a mark on how inspectors and manufacturers take measurements
Mechanical pressure instruments have supported the efforts of scientists, technicians, and fire professionals for more than a century. But do electronic (digital) pressure gauges perform better than traditional gauges—or are they just a new and more-expensive spin on an old device?
The short answer is this: digital pressure gauges haven’t ushered in any sort of revolution—particularly in fire protection (where analog gauges still reign). But the way they’re built is radically different. And for contractors looking to replace several measuring instruments with an alternative that’s tough, long-lasting, easily used with a variety of formulas, and surprisingly convenient, these devices are worth a glance or, in this case, a read.
Readers familiar with the benefits of digital pressure gauges are invited to skip to our premiere Ashcroft DG25 digital gauge and a selection of products, like bleeder valves, designed to prolong their life.
The fusion of long-lasting materials with a handful of electronic components eliminates traditional sources of gauge failure
Digital pressure gauges eliminate a number of mechanical parts found in other gauges (although which specific parts they use vary from model to model). In general, these devices combine a transducer, which transforms pressure into an electronic signal, and a microprocessor that converts those signals into readable values.
Engineers have devised a number of innovations to get information from liquid-or-gas-filled systems into gauge displays, including:
- Mechanical deflection: pressure against a flexible component causes movement, which registers as an electronic signal
- Thin films that respond to changes in pressure
- Pistons that move up and down, conducting an electric signal
Compare that scheme to the inner workings of an analog pressure gauge—modern or antique—and the differences are stark. Those traditional gauges resemble a clock or old-school speedometer, and rely on a dial and pointer to represent changes in pressure. But behind those visible components are a range of mechanical parts, including:
- The Bourdon tube: the primary pressure-sensing element, this tube flexes in response to pressure
- Link and tip: responsible for transferring motion from the Bourdon tube to the gauge’s gears
- Pinion, hairspring, and rotary movement mechanisms (gears): these rotate the pointer while minimizing vibration to ensure readability
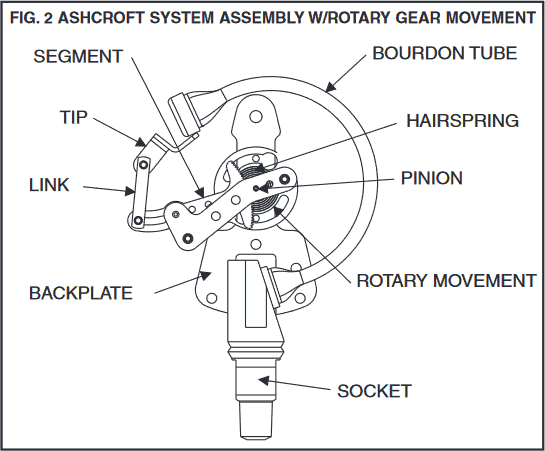
Complex arrangements of mechanical parts in non-digital, analog gauges make field calibration more difficult and contribute to gauge failure
In a guide to gauge installation and maintenance, gauge maker Ashcroft outlines a range of behaviors or considerations that may merit analog gauge repairs, including:
- Substantial inaccuracy
- Damage to pointers
- Broken windows
- Leakage of liquid from the gauge face
- Leaks at the gauge connection
- Discolored liquid in the gauge window
If the dial doesn’t show zero PSI with no pressure (but is error-free, otherwise), a quick adjustment can typically fix the problem. But if a more substantial error is detected, recalibration of an analog gauge requires taking several measurements with a well-regulated pressure supply—followed by a more thorough internal inspection, along with some repetitive adjustments and tests with the manufacturer’s prescribed tools. Calibration and trouble correction may involve an entire toolkit, cleaning, adjusting, rotating, and reassembly of fine parts.
Analog gauges that show non-zero readings with errors in excess of 10%—or “zeroes” that are 25% or more away the gauge’s zero—may have irreparable damage. These and other indicators can point to excessive gauge use or subjection to extreme conditions, such as temperatures between 250 and 750 degrees Fahrenheit.
Compare all of this with the field calibration process for the DG25, a digital gauge developed by the Connecticut-based Ashcroft, Incorporated (spoiler alert: it’s easier and possible to recalibrate):
Ashcroft’s manual for a digital test gauge lists only two steps for recalibrating their handhold digital pressure gauge:
- Access the calibration feature through the gauge’s menu—and with the gauge under no pressure, press “ENTER”
- Attach the gauge to a pressure source and pressurize to 100% of the gauge’s range (ensuring the accuracy of that pressure with a device that’s at least four times as accurate). Press enter again.
Rigorous construction and testing are hallmarks of handheld digital pressure gauges
Not all electronic measuring devices are created equal—so, to simplify things, we’ll focus for now on Ashcroft’s DG25, a handheld digital pressure gauges favored by manufacturers, building and construction inspectors, and contractors relying on precise measurements.
In the DG25, only a few parts make direct contact with the liquids or gases under pressure—namely, the socket and the sensor, which are both typically made from stainless steel. Those components are protected by a laser-welded stainless steel body, which in turn is surrounded by a polycarbonate case, back, and window.
These exterior components work together to provide an IP67 enclosure rating, which classifies objects according to the level of protection they provide against dust and moisture. The first digit of this code represents how well the encasement resists penetration by fine solids, with a 0 representing no protection against ingress and a 6 representing “complete protection.” The second digit represents liquids, and ranges from 0 (not protected) to an 8 (suitable for continuous submersion in water deeper than one meter). An IP67 enclosure, then, is one that is completely dust-tight and suitable for immersion in water less than one meter deep.
But while filth and moisture can slowly corrode or destroy gauges, vibration and shock pose the most recognizable threat—and digital gauges can withstand both. The DG25, for example, meets two standards developed by the US Department of Defense:
- MIL-STD-202G (Method 201A): Vibration resistance
- MIL-STD-202G (Method 213B, Test Condition K): Shock resistance
Vibration can gradually loosen or reposition critical components within gauges, both analog and digital. Eventually, the accuracy of gauges decreases (or they stop working entirely). The first set of tests subjects gauges to increasing levels of harmonic vibration—applied from several different directions—to assess how the instrument performs after intense wear.
Similarly, shock tests under the Department of Defense’s standard simulate rough handling using pulses. They’re placed in machines that rise and fall at specified rates and heights, with the height of the platform changing at nearly 9 feet per second under “Test Condition K.” Take a look at the machinery used in these tests in the video below:
Electronic measuring devices leverage modern technology to deliver greater accuracy and ease of use
Handheld digital pressure gauges do an excellent job of resisting dust, moisture, shock, vibration, and other forms of wear. But the same can be said for some high-end analog pressure gauges—so what really sets them apart?
Interchangeable units of measurement make formula work easier
An electronic pressure gauge’s most notable advantage is its adaptability, enabling one gauge to meet the needs of a variety of industries with an assortment of units. The DG25 comes with nine different engineering units of measure, including:
- PSI (pounds per square inch)
- Bar
- kPa / mPA (pascals)
- inHg / cmHG / mmHG (units of mercury)
- kg/cm2 (kilogram per square centimeter)
It’s possible, say, to calculate PSI from bar, or kPa from inHg. But that requires doing some math. So, while a digital gauge isn’t necessary, strictly speaking, it’s handy—and can reduce the likelihood of error—in industries where multiple gauges or multiple units of measurement are regularly used.
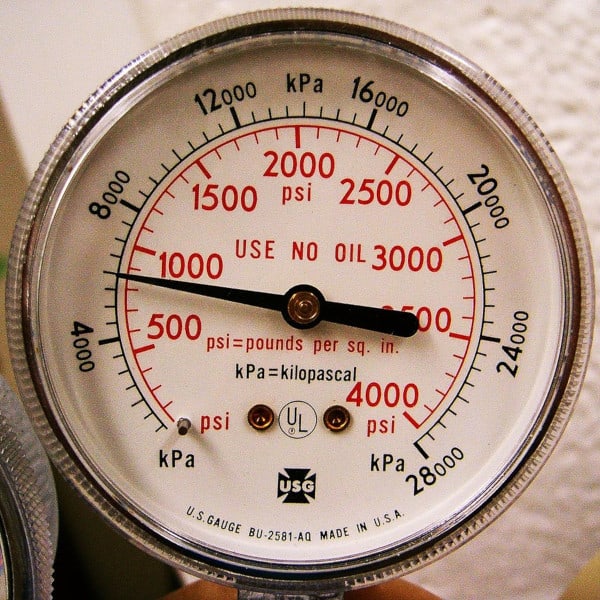
Unlike traditional analog gauges, which usually feature just one or two units of measure, a digital pressure gauge can replace a variety of traditional gauges. As an example, people testing a fire engine use measurements taken in PSI and inHg (inches of Mercury), with the latter measurement used to evaluate vacuum pressures found in a priming system. A multi-unit gauge allows testing professionals to rely on just one gauge to fulfill a range of testing and inspection tasks.
Storing measurements in memory prevents accidental loss of readings
Many digital pressure gauges come with the added benefit of storing and accessing previous measurements. Some gauges offer a range of measurements over a period of time, some keep track of pressure as temperature changes, and others record maximum and minimum values until cleared by the user. That’s a handy feature in environments where pen and paper might get wet—or where attention to especially high or low values is critical.
Modern electronic measuring devices nearly eliminate worries over battery life
Battery life remains one key concern for consumers switching from analog to digital gauges. Some specialty electronics rely on hard-to-find batteries; others exhaust the power they have far too quickly. But other gauges rely only on AA batteries—an easy-to-replace component, when the time comes—and can deliver in excess of 2,000 hours of measurements. These can last for 10,000 cycles (where pressure fluctuates, causing gauge readings to change). And handheld digital pressure gauges can extend that battery life with built-in timers that stop taking readings—or dim the backlight—after a user-determined period of time.
Simplicity in design and use make digital pressure gauges a powerful ally in a range of industries
Digital pressure gauges—for scientists, fire protection professionals, and manufacturers—have arrived. They’re forging a new approach in how we take pressure, vacuum, and compound measurements, and reshaping consumers’ expectations for precision in measuring instruments and the devices they help maintain.
QRFS is proud to stock the Ashcroft DG25, a handheld digital pressure gauge that rounds out our complete selection of gauges for system risers, fire pumps, fire protection piping, and more. With an IP67 enclosure, stainless steel components, shock and vibration resistant construction, and listings from a variety of agencies, this gauge is designed to deliver accurate readings over one million cycles.
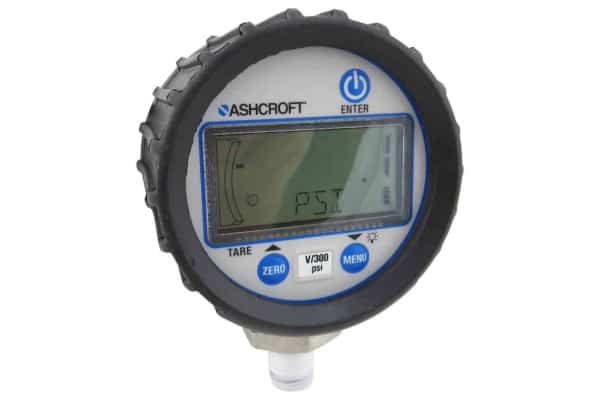
Each of these gauges is NIST-certified. That means it’s been tested against a properly-calibrated reference (and has the paper trail to prove it). NIST certification is popular among facilities that brand themselves as ISO-compliant—meaning that they meet rigorous manufacturing standards—and is demanded for some contractors providing fire protection services to the American government.
View Ashcroft’s DG25 handheld digital pressure gauge.
As a parting word of advice: to ensure your gauge works flawlessly, never hand-tighten it into a fitting. Improper installation can adversely impact the gauge’s circuitry. To be safe, always use a wrench for proper tightening, and protect the gauge from excess pressure with a bleeder valve.
Questions? Comments on this article? Call us at +1 (888) 361-6662 or email support@qrfs.com.
This blog was originally posted by Jason Hugo and Cameron Sharp at blog.qrfs.com on April 18, 2016 and updated on October 18, 2019. If you like what you’ve read, check us out atFacebook.com/QuickResponseFireSupply or on Twitter @QuickResponseFS.
like!! I always blog and I sincerely thank you for your knowledge. The blog really increased my curiosity.