Image source: PHCP Pros
Heat tracing, also known as heat tape, is an option to protect fire sprinkler pipe from freezing
Wet fire sprinkler systems have many advantages; since the pipes are always filled with water, they are ready to release it instantly against any fire hazard. They are also less complex to install and maintain than preaction or dry pipe sprinkler systems, where the delivery of water in a fire can be delayed up to 60 seconds.
However, like any other pipe carrying water, there is a danger of breakage or blockage when it freezes, causing costly damage and preventing the system from working in an emergency.
To ensure fire sprinklers are protected against freezing, the National Fire Protection Association (NFPA) requires that water-filled sprinkler systems be maintained at a minimum temperature of 40°F (4°C), unless an approved antifreeze solution is used. Antifreeze has traditionally been the preferred way of handling this problem, but its flammability has caused serious concerns about its safety – and it was due to be phased out entirely before the recent listing of a new, safer solution. Regardless, the additional maintenance and testing requirements make antifreeze complicated to use.
So, if antifreeze isn’t an option in a particular wet system, what can be used?
Heat tracing (also known as heat tape), typically employed in commercial applications, is one way of providing freeze protection for fire sprinkler systems. Electrical heating cables – either wrapped along or taped to the pipes – keep the network warm, preventing freezing.
In this QRFS blog, we look at heat-tracing systems, the different types, their pros and cons, installation and maintenance requirements, and major manufacturers. Let’s begin by looking at when heat-tracing is needed and the NFPA standards that govern this technology.
When to use heat-tracing: 40 degrees is the magic number
NFPA 13: Standard for the Installation of Sprinkler Systems requires pipes located in areas that can reach temperatures below 40 degrees to be maintained above 40 (but below 120) degrees by a listed heat-tracing system or another approved method. Listing means that the technology has been tested and listed for that specific application by the safety organizations UL or FM Global. NFPA 25: Standard for the Inspection, Testing, and Maintenance of Water-Based Fire Protection Systems outlines the ongoing requirements to keep heat tracing working.
Areas that pose the highest risk for pipe freezing are open areas, entryways, stairwells, attics, skylights, and under floors.
From the 2016 edition of NFPA 25
4.1.2.2 Aboveground water-filled pipes that pass through open areas, cold rooms, passageways, or other areas exposed to temperatures below 40°F (4.0°C), protected against freezing by insulating coverings, frost-proof casings, listed heat tracing systems, or other reliable means, shall be maintained at temperatures between 40°F (4.0°C) and 120°F (48.9°C).
Another component of heat-tracing systems that helps maintain these temperatures – in addition to the electric cable described in the introduction – is thermal insulation. Without it, heat losses are generally too high to be countered by the current produced by a heat tracing system. A protective barrier is recommended around the insulation to protect it from moisture intrusion, physical damage, and to ensure proper performance of the system.
Other components of a heat tracing system are the control and monitoring systems which, depending on the size and importance of the system, can be very simple or very complex. These can sometimes even be linked to the computer-controlled building management system. However, generally, heating is controlled using a combination of time-clock switches, thermostats, and frost-stats:
- The time-clock switch allows the site owner or manager to schedule a time for the system to be turned on; for example, after-work hours when the building is vacant and the heating system might be turned off.
- A frost-stat is a thermostat used to override any time-clock switch and turn on the heating system in the event that the air temperature falls to near freezing; this thermostat is usually positioned outside or in the coldest part of the building to turn on the heating as soon as possible.
- Once the heating has been turned on, it will often be controlled locally by a separate thermostat, normally triggered by ambient air sensors.
Heat tape can’t be used on every component of a fire sprinkler system. Heat-tracing equipment is only intended for use on:
- The supply piping for a sprinkler or standpipe system
- Branch lines within a sprinkler system (using heat-tracing specifically listed for branch lines)
NFPA 13 states that listed heat-tracing can also be used on private fire service mains when heat tracing has been listed for underground use, while unlisted heat-tracing can be used when the underground piping extends through the wall or slab by no more than 24” (6.4.2.1.7, 6.4.2.1.7.1, and 6.1.4).
However, if your wet sprinkler system supplies an auxiliary dry pipe or preaction system, NFPA rules do not permit heat tracing in place of heated valve exposures that protect the dry pipe or preaction valve or to safeguard supply pipe from freezing.
3 different types of heat tracing provide installation options
Heat-tracing can be powered by either electricity or steam; however, due to the cost of installation, steam heat-tracing is most likely to be used when steam is already available on site or is generated as a byproduct of condensation. Otherwise, electricity is more commonly used because it’s easier to install, provides better temperature control, and uses energy much more efficiently. Electric’s downsides compared to steam power are a lack of available voltage and the potential unreliability of the electricity source, including the consequences of electrical outages.
There are three different types of electrically-heated cables commonly used in fire-sprinkler freeze-protection: series circuit heating, parallel circuit heating (constant wattage), and self-regulating heating. Each method has its own advantages and application, including the level of difficulty of installation, reliability, and flexibility. Three common criteria used for selection are the cables’ 1) output, 2) the ability to cut to length, and 3) temperature limits. Energy efficiency can also be an important factor when choosing a system.
Series circuit heating (often supplied as a mineral-insulated cable)
The simplest type of heat-tracing, a series circuit system is made up of a high-resistance wire which is insulated and often enclosed in a protective jacket. It is powered at a specific voltage which, along with the length of the circuit, determines the heat output.
Advantages:
- Extremely long circuit lengths are possible, up to 4,000 ft.
- Relatively low cost per foot
- Voltage up to 600VAC
- Suitable for high temperatures and harsh environments
- Provides uniform power along the entire length
Disadvantages:
- Cannot be used on plastic pipes
- Relatively inflexible – difficult to install
- Can overheat and burn out if they are crossed over themselves
- Available in standard lengths and cannot be shortened in the field
- A break anywhere along the line will result in a failure of the entire cable
- Caution must be taken when using these in hazardous areas
Parallel-circuit constant-wattage
A constant wattage cable is composed of multiple electric power zones and is made by wrapping a fine heating element around two insulated parallel wires. Every zone of the cable has a fixed resistance circuit supplied by a fixed voltage, meaning there is a constant wattage along its entire length.
Advantages:
- If one small element of the system should fail, the rest of the system will continue to operate
- Can be cut-to-length in the field, which simplifies installation
- Is always installed with a thermostat to control the power output of the cable, making it a very reliable heating source
Disadvantages:
- Cannot be used on plastic pipes
- Has to be installed slightly beyond the end of the pipework
- Overlapping or touching the cable to itself can cause overheating and burnout
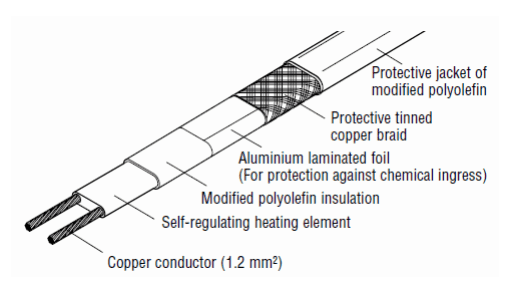
Self-regulating heat-tracing
Self-regulating heat-tracing systems are the go-to for very low temperatures and they are the leading type of heat-tracer. Self-regulating heat tapes automatically adjust heat output based on temperature changes, using only the amount of electricity that is needed.
Advantages:
- More rugged in comparison to series and constant wattage cable
- Can be used on metal and non-metallic pipes
- Can be cut-to-length in the field, making it easy to install
- It’s flexible and can be overlapped without burnout
- Can be used in a wide range of applications, including on nonmetallic piping and equipment
- Particularly suited for hazardous environments
- Do not create significant heat
- Energy efficient
Disadvantages:
- Subject to high inrush currents on starting
- Cannot be used on 480V
- Precise temperature control is difficult because the wattage output is always changing
- Harder to bend
- Not nearly as reliable as series or constant wattage cables
- If subject to high temperatures beyond their maximum, the tape can be damaged beyond repair
Installation of the cable can be handled with little expertise, but an electrician is needed for hook-up to an electric power source
Installation of heat-tracing cable is fairly straightforward but can vary depending on the type of heat-tracing cable, some of which is more flexible than others and/or has the ability to be cut in the field. An example of heat-tracing that is easy to install is the self-regulating cable, which known for being easy to tee and splice, thus facilitating installation.
One of the key steps before installation is to decide how many watts per foot are required for a specific application. Tables like the one below can help users find the appropriate wattage by judging the size of the pipe and the difference between the expected pipe and ambient temperature.
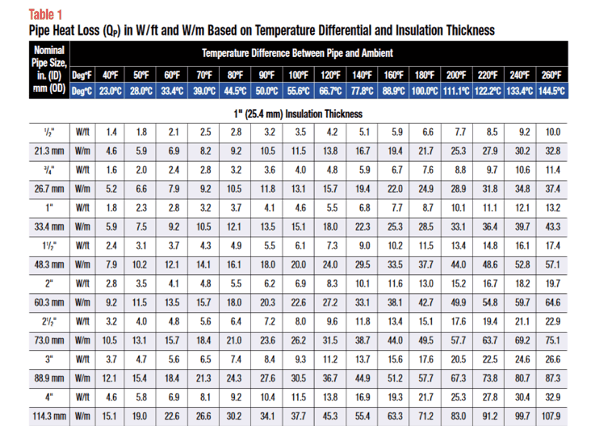
After choosing an appropriate heat-tracing cable, users without electrical expertise can attach the trace heating cable and then place the insulation and covering on piping. Installers will also have to be aware of information related to a heat tracing system design, specific application limitations, as well as the ambient environmental limitations for the installation of the heat tracing cable controls. The video below shows the installation steps:
Steps that require a qualified electrician are the attachment to a power supply; trace heat cables may be connected to single-phase or three-phase power supplies. Although single phase heaters can generally operate on either 120 or 240-V, the latter are preferred because they can support circuit lengths approximately twice as long as 120-V heaters can.
In addition, electricians can oversee the installation of electrical supervision to ensure power is being delivered to the portion of the pipe that is being protected by heat-tracing, as required by NFPA standards. This supervision can consist of “controllers with alarm relays connected to the fire control panel.”
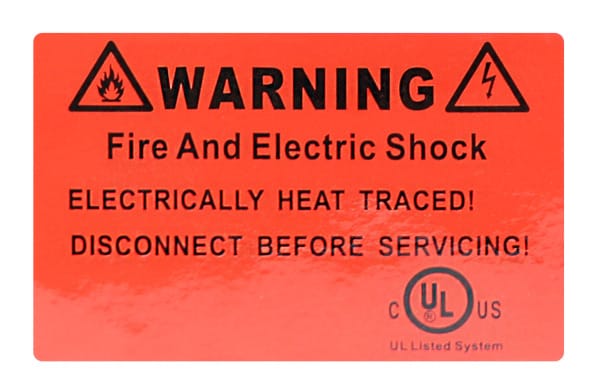
Signage with information about your heat-tracing system can help preserve your property
The sturdy signage required by NFPA 25 ensures that critical information about fire systems components and their location – including heat tape – is securely maintained and provides vital details to someone unfamiliar with maintaining the system. If this information is not known, the system can be damaged due to freezing water in trapped sections of pipe that are unprotected.
From the 2016 edition of NFPA 25
4.1.9.1 A permanently marked metal or rigid plastic information sign shall be placed at the system control riser supplying an antifreeze loop, dry system, preaction system, or auxiliary
system control valve.4.1.9.2 Each sign shall be secured with a corrosion-resistant wire, chain, or other approved means and shall indicate at least the following information: (1) Location of the area served by the system (2) Location of auxiliary drains and low-point drains for dry pipe and preaction systems (3) The presence and location of antifreeze or other auxiliary systems (4) The presence and location(s) of heat tape
Fire protection heat tracing manufacturers and cost
Heat-tracing cable is typically sold by the foot or the meter. In 2019, one vendor stated that the cost of a 5-watt per foot self-regulating cable was $7.33/foot, while the cost of constant wattage heat tracing-cable was $10/foot. Higher wattage cables come with a higher price tag: 20-watt per foot heat-tracing cable can run $15/ft. In addition to the cost of the cable, several accessories typically need to be purchased, like a thermostat which can run upwards of $350.
The heat-tracing industry is a large and growing one, especially in the U.S. Major players in this country and abroad are Pentair (UK), Thermon (US), BARTEC (Germany), Chromalox (US), Emerson (US), Danfoss (Denmark), BriskHeat (US), eltherm (Germany), Parker-Hannifin (US), and Warmup (UK). Other companies operating in the electric heat tracing market are Parker-Hannifin (US), Heat Trace Products (UK), and Warmup (UK).
Maintenance is straightforward: NFPA requires users to follow the manufacturer’s instructions
NFPA standards provide a lot of guidance on many subjects but they defer to manufacturers when it comes to heat tracing maintenance. Users are instructed to follow the specific manufacturer’s requirements. According to Thermon and Nelson heat tracing system manuals, heat-tracing systems should be inspected and tested regularly – at least once a year, ideally at the beginning of the freeze season.
A few of the components that should be reviewed during an annual evaluation:
- Thermal insulation should be reviewed for damage, missing seals, cracks or gaps in caulking and mastic coatings, and damaged or missing lagging. If there is damage, the insulation should be replaced or repaired and then resealed, and the heater cable should be inspected for damaged sections that may need to be replaced.
- Junction boxes, connection boxes, and thermostats should be checked for corrosion, moisture or foreign matter.
- The tightness of electrical connections, the proper electrical insulation of heater cable wires, and the adequacy of moisture seal on electrical connections should all be reviewed.
- Thermostats or sensor capillary leads should be checked to ensure they are tied back and shielded from physical damage.
- All enclosures, the connection box, etc., should be reviewed to ensure that their covers are properly closed, and that the thermostat is switching off and on by measuring current flow in the circuit when the unit switches on.
Heat tracing is a viable freeze-protection solution for some wet sprinkler systems
Heat tracing installed within NFPA parameters can protect sections of pipe in wet fire sprinklers from freezing, providing a viable alternative to antifreeze or installing or retrofitting more complex and expensive dry pipe or preaction systems. That said, it does have its limitations, in both how much heat tracing can be applied and where, plus the additional supervisory, maintenance, and inspection requirements.
Since a new antifreeze has been listed that addresses the flammability concerns of previous products, it will be interesting to see which freeze-protection option becomes more common in wet systems in the coming years.
If you’re looking to buy components for your wet sprinkler system, check out our selection of commercial sprinkler heads, as well as our sprinkler gauges, valves, switches, and other accessories.
If you have questions or need help finding a component, give us a call at 888.361.6662 or email support@qrfs.com.
hi
thanks a lot for this post about heat tracing systems
i hope the best for you and your team
have a good day
Thank you, and you as well!
Only one manufacturer mentioned in the paragraph “manufacturers and costs”, actually meets the finer points of the NFPA 13 2016 standard. That manufacturer is Chromalox. Chromalox is the only UL listed manufacturer in the of freeze protection heat cable/systems, specifically listed for use on fire sprinkler pipe. No other manufacturer meets the NFPA 13 2016 (and forward standards) requirements with their heat cable/system.
That is not true. Various manufactures meet the code and have fully listed systems.
Great post, thanks for sharing this article. I am really interested in your blog.
Great post, I wish it had been a bit more specific about type of heat traced sprinkler systems being approved by FMG/UL and NFPA considering ESFR, CMSA and CMDA, if it is not a general ok for all three.
The firemarshall in my town requires the fire suppression system to have glass sensors outside on the decks of houses. This creates a high likelihood of freezing, breakage and water damage. Can heat tape be used on the glass sensor to prevent freeze up?
Frederick — We’re unsure of what you mean by “glass sensors.” If you mean the heat-sensitive glass bulbs in the middle of fire sprinklers that cause them to activate, the answer is a definite “no” to using heat tape. Otherwise, your best bet is to contact a local fire protection professional, have them evaluate your system, and run any possible heat tape application by them for safety and code-compliance. Thanks for reading and commenting!