Close inspections and sophisticated tools can quickly put underground pipes in working order
In the first installment of QRFS’s two-part series on underground standpipe leaks, we looked at how installers use flow and pressure tests to find problems in private fire service mains. When an issue is found, rather than tearing apart all the underground pipe—or needlessly replacing very large sections—savvy contractors can use specialized detection and repair tools to limit their scope of work.
In this article, we explain how inspectors use a variety of tools to precisely locate leaks and what contractors can do to fix them with minimal disruption.
If you’re looking for flow or hydrostatic testing equipment to detect underground leaks, feel free to browse our selection of hydrostatic test pumps, flow test accessories, or flow-testing pitot gauges.
After flow tests, inspectors take a closer look at the cause and extent of pipe problems
When a flow test points to a problem in the underground pipes serving standpipe systems, those pipes must be inspected to the satisfaction of local fire authorities. Some of these inspection procedures are outlined in NFPA 25: Standard for the Inspection, Testing, and Maintenance of Water-Based Fire Protection Systems.
NFPA 25 outlines some ways that contractors may assess the internal condition of pipes in chapter 14. If fire officials suspect that living organisms or outside debris have entered the system, contractors may need to assess the condition of pipes with cameras, ultrasonic technology, or lab tests—or even open one end of the main and look inside.
One type of leak—the pinhole leak—triggers an even closer look at underground pipes serving standpipe systems. Pinhole leaks may point to bacterial growth and pitting, a concentrated form of corrosion that destroys pipes from the inside out. The tiny organisms that drive this form of corrosion could cause as much of 30 percent of corrosion in piping systems throughout the United States.
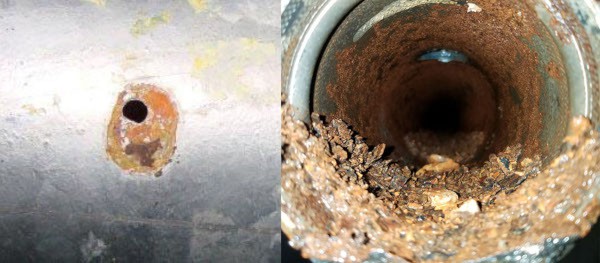
When microbiologically influenced corrosion (MIC) causes a leak, inspectors must look closely at pipes throughout the system, either directly or using specialized tools. The network must be flushed and sometimes chemically treated if this investigation confirms that MIC has blocked pipes.
From the 2017 edition of NFPA 25
14.3.2.2* Internal examination shall be performed at the following minimum four points:
(1) System valve
(2) Riser
(3) Cross main
(4) Branch line14.3.2.3* Alternative nondestructive examination methods shall be permitted.
14.3.3* If an obstruction investigation indicates the presence of sufficient material to obstruct pipe or sprinklers, a complete flushing program shall be conducted by qualified personnel.
Acoustic and radar-based tools help users find concealed underground leaks in standpipe systems
Because some standpipe systems may feature hundreds of feet of underground pipe, narrowing the scope of the investigation can vastly reduce the labor required and speed up repairs. Contractors turn to specialized tools to assess the extent of damage and to find these leaks in the first place.
One such tool relies on the sounds that pipes make when they leak. Leaking pipes hiss, whoosh, splash, thump, or clink. The volume and range of these sounds depend on all kinds of factors. Loose and wet soils transmit sound poorly, while compacted soil carries sound well. Metal pipes can transmit sounds clearly over hundreds of feet, while some cement and plastic pipes have less range.
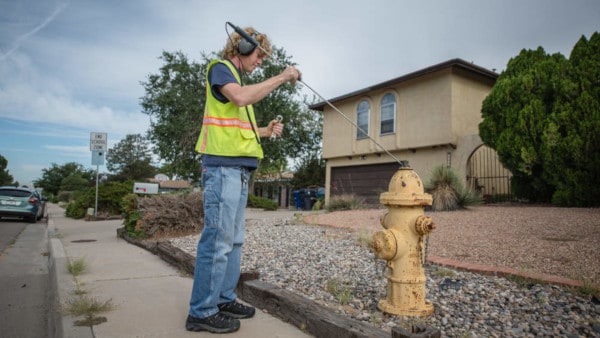
Acoustic tools can prove helpful in pinpointing a leak when the pipe isn’t buried too deeply and when pipes or outlets are accessible for listening. By placing a microphone on the ground directly over the water main or on devices connected to those pipes, listeners can search for where the sound is loudest.
Another tool uses ground-penetrating radar (GPR) to create images of the ground below. GPR helps archaeologists decide where (and where not) to dig. Police use it to find murder victims buried underground. And in fire protection, GPR makes pinpointing the location of a leak possible without unearthing pipe.

Normally, ground layers below the surface appear as straight lines, while pipes appear as ripples. Leaking pipes create distortions in these lines and waves, helping to pinpoint the location of a leak. However, GPR has limitations: clay and salt-contaminated soils can make imaging difficult, and too much moisture in the soil can also make GPR ineffective.
Cameras can locate leaks and provide an inside look at damage to underground fire protection piping
If the underground pipes connected to a standpipe system lie under concrete or other hard surfaces, thermal imaging may narrow the scope of the investigation. Water resists changes in temperature, but concrete and pavement heat and cool at a faster pace. Infrared (IR) cameras often render these slight contrasts in surface temperature caused by leaks.
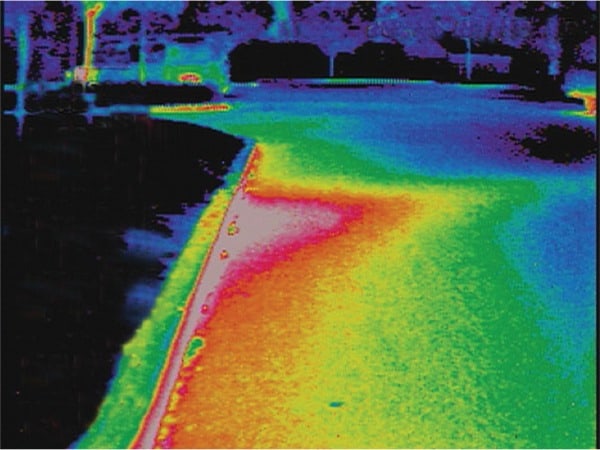
Like GPR and acoustic tools, IR cameras have limits. While IR can be used at any time, late-night inspections eliminate distortions caused by sunlight. Very high and very low surface temperatures make imaging difficult. Thus, while IR cameras have successfully located water main leaks in fall and spring, they may fail to detect leaks in summer and winter, when temperatures are most extreme.
Other types of cameras can do far more than simply detect leaks. Video inspection equipment, which often consists of a camera with a lighting system and a push cable, can record footage or send a feed of a standpipe’s underground pipes to a view screen. Inspection cameras may provide the most thorough look at the problems facing fire protection piping, allowing inspectors to find leaks and assess the problems contributing to them—all without breaking ground.
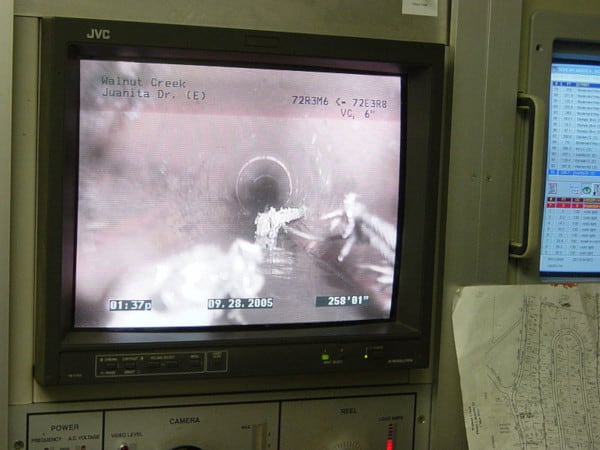
Repairs or replacements can fix underground leaks in standpipe systems—but any such repairs require further tests
Different types of pipes leak in different ways. Many pipes in underground service consist of lined ductile iron. While this material resists damage from impacts, ductile iron and other metal pipes run the risk of rusting. This is why installers often use plastic pipe which doesn’t corrode but may more easily break.
If investigations uncover corrosion in metal pipes, it’s possible that whole sections will require replacement to make the system fully operational. Failed sections of pipe can be cut out with a saw or, if grooved or flanged couplings are in use, they can be unbolted and uncoupled. The defective section of pipe is removed (with a backhoe, if necessary) and a new section put in place. After that, couplings can connect the new section of pipe to the old one.
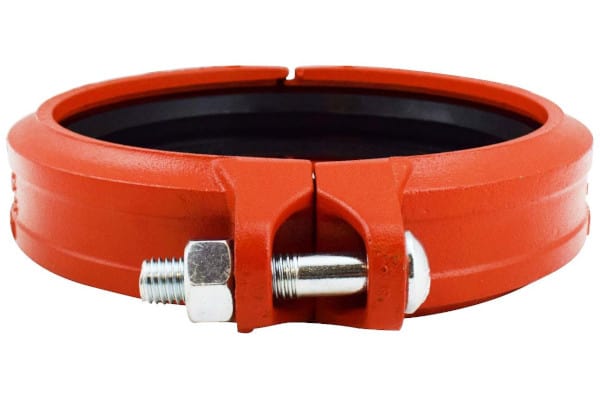
Leaks in copper or plastic pipes can sometimes be repaired with clamps or by tightening or replacing leaking fittings. When that’s not the case, contractors may make use of repair clamps. These clamps use bolts to press a hard, durable exterior around flexible waterproof material, forming a seal around the leaking section of pipe.

After making these repairs, contractors have one final step: ensuring that the restored pipes are clean and durable enough for fire protection service.
From the 2017 edition of NFPA 25
7.5.1 Whenever a component in a private fire service system is adjusted, repaired, reconditioned, or replaced, the action required in Table 7.5.1 shall be performed.
Table 7.5.1 says that any changes to pipes and fittings—including adjustments, repairs, reconditioning, or replacement—should be followed by hydrostatic tests and flushing as prescribed in NFPA 24.
Equipment for pipe replacement can make fixing underground leaks a faster, easier process
Repairing underground pipes is a tough job—but with the right tools and equipment, leaks can be precisely located, and fixes quickly applied. By taking the time to understand what NFPA 25 requires for these repairs, contractors can ensure that these fixes keep pipes in working order for years to come.
This concludes our two-part series on finding and fixing underground leaks in standpipe systems. Check out part one. And if you’ve got a pipe in need of repairs, take a look at the selection of pipe accessories available at QRFS. Our selection of flange packs includes nuts, bolts, and gaskets designed for industrial and fire protection piping. Available in sizes up to 12″, each pack has everything need to form a water-tight seal between two ASME/ANSI Class 150 flanges.
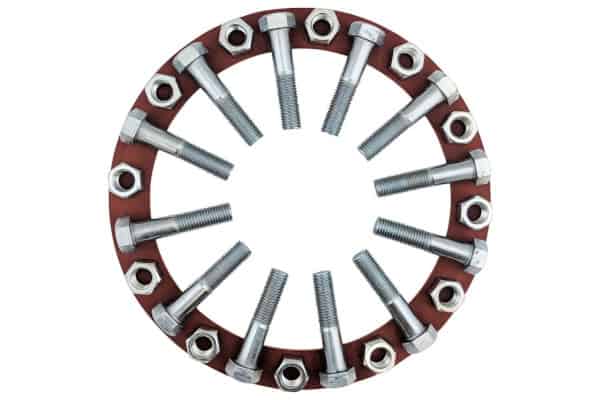
QRFS also carries equipment that establishes whether there is an underground leak in the first place:
- Flow test accessories
- Hydrostatic test pumps
- Air and water pressure gauges
- Pitot gauge kits and parts
Need more information about repairing underground pipes serving standpipe systems? Have questions about our product line or require something that’s not listed online? Call us at +1 (888) 361-6662 or email support@qrfs.com.
This blog was originally posted at blog.qrfs.com. If this article helped you get a better grasp on underground standpipe leaks, check us out at Facebook.com/QuickResponseFireSupply or on Twitter @QuickResponseFS.