Fire inspection software makes it easier than ever to maintain life safety systems
Ignorance is far from bliss when it comes to a facility manager’s duty to keep fire protection systems in working order. Whether they perform mandated inspection, testing, and maintenance (ITM) on their own or hire a contractor to catch deficiencies that could lead to system failure, the ultimate responsibility for ensuring life safety falls on the property owner and designated building personnel. Fire inspection software can ease this burden.
In this blog, we explain the responsibilities of a facility manager when it comes to ITM of fire protection systems. And we show how a new trend toward software—aimed at standpipes, fire alarms, fire sprinklers, fire extinguishers, and other components—is making it easier than ever to maintain life safety systems.
If you’d like to see how fire inspection software works and improves compliance, sign up for a free demo of Inspect Point’s fire protection ITM software.
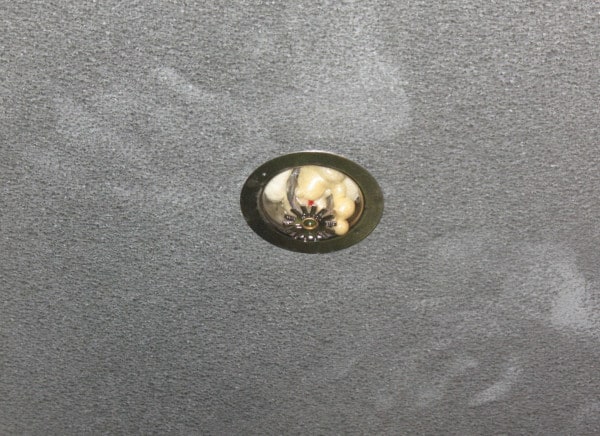
Costs and liabilities soar when a fire protection system is neglected
Fire protection systems are essential equipment for any type of facility—and require extensive maintenance to ensure that they will perform as expected in an emergency. Model fire codes and standards from the National Fire Protection Association (NFPA) outline the responsibilities for conducting ITM of various systems and elements.
For example, the 2017 edition of NFPA 25: Standard for the Installation, Testing, and Maintenance of Water-Based Fire Protection Systems states that ITM work should be carried out by “qualified personnel” (section 4.1.1.2) and permits it to be outsourced to an ITM professional (A.4.1.1). But the main mandate is clear: building owners and their designated representatives are ultimately responsible for the ITM of life safety systems (4.1.1).
Some facilities—usually larger ones, such as a sprawling college campus or a manufacturing plant—decide to take this inspection, testing, and maintenance completely in-house, creating an onsite department that is dedicated to making sure extensive life safety systems work properly.
The focus on keeping systems running stays the same but other priorities may shift slightly. For example, while contractors have to balance thorough inspection, testing, and maintenance with ROI, an on-site ITM department that’s under intense scrutiny has an arguably greater focus on always maintaining 100% compliance that avoids fines, insurance lapses, property damage, shutdowns, and potential legal liabilities:
- It goes without saying that uncontrolled fires imperil life and property and wreak havoc on operations. And there is also the potential cost of uncorrected critical deficiencies and impairments that can lead to building shutdowns or expensive fire watches until fire protection systems are fully restored to service.
- Insurance companies may limit or refuse to cover specific claims if investigations determine that fire protection systems were neglected—or withhold coverage altogether if problems are discovered before an emergency happens and they aren’t quickly corrected.
- The threat of legal liability is a major incentive for sticking to a tight ITM schedule. Property owners can face lawsuits if an uncontrolled fire spreads to adjacent properties. Even more important, facility managers and property owners carry a weighty responsibility to protect the people in their buildings. And if the property’s occupancy includes a residential or educational component, for example—such as dormitories for college campuses—the danger and potential liability soar even higher.
ITM of fire protection systems: what falls under a facility maintenance manager’s responsibilities?
ITM of fire protection systems is an ongoing, rigorous process that requires many different actions over time. Frequencies vary based on the type of system being maintained but typically range from very simple daily checks to intensive annual requirements. In between, there’s a laundry list of other activities that must be carried out and properly recorded—in weekly, monthly, quarterly, semiannual, and multi-year increments.
Even if facility managers don’t perform the activities themselves, they’re charged with ensuring that systems are regularly inspected and tested and meet local codes and regulations. That responsibility requires them to maintain at least a baseline of knowledge on a wide range of complex topics, from operational considerations and testing and inspection requirements to policies and procedures.
Facility managers must also be able to understand how detection, suppression, and notification systems operate; hazard evaluations; freeze protection; requirements for record-keeping; and how to evaluate a system’s design to ensure it continues to meet a building’s occupancy and hazard needs.
NFPA standards and code detail minimum requirements for the inspection, testing, and maintenance of fire protection systems, from fire sprinklers and standpipes to alarms and hydrants. They also outline the robust process that needs to be followed when problems are found, including proper fixes and reporting. AHJs often build upon these guidelines with specific requirements for their areas based on these model fire codes and standards.
Once mandated ITM is completed, the local AHJ reviews the report and enforces the completion of necessary repairs. NFPA lays out general completion timelines, but many jurisdictions also have their own requirements for the timely correction of impairments and/or deficiencies.
For in-depth information about determining what constitutes an impairment, a critical deficiency, or a non-critical deficiency in fire protection systems, read our previous blog: “Standpipe and Fire Sprinkler Inspections: Classifying Deficiencies and Impairments.”

Some tasks – typically the daily, weekly, or monthly ITM requirements—are simple for any qualified facility manager to tackle on their own, while others are more involved and require more expertise and training. Facility managers responsible for larger facilities like universities are often trained to handle all ITM responsibilities, while managers at smaller properties may find it more appropriate to hire an outside contractor.
At most facilities, a hybrid solution is carried out: designated site personnel conduct the simpler inspections or tests on short timelines and an outside contractor is brought in for the more involved requirements that are performed less frequently (such as annually or bi-annually). But even when ITM is contracted to others, the facility manager—and ultimately, the property owner—is responsible for overseeing the work, reviewing reports, and authorizing repairs when needed.
Why inefficient paper ITM inspections can cause deficiencies to remain uncorrected
Here’s where problems kick in: even when dedicated facility managers are more than qualified to perform ITM activities, it’s often far from their only responsibility. After all, managers are a one-stop resource for maintaining every part of a property, from heating and cooling systems to waste disposal to elevators to plumbing. And even particularly large facilities with dedicated fire protection ITM departments still have a massive number of elements to check, test, and correct if something is found to be missing or broken. When a single point of failure can lead to lapsed insurance, a lawsuit, or a non-functioning system, 100% compliance becomes a challenging necessity.
Traditional paper-and-clipboard inspections of fire protection systems consume a significant chunk of time, forcing inspectors to tediously write down their findings, snap separate pictures, and then head back to their office to transcribe the information into a final report. Low-tech improvements like inspection documents that are PDF, Excel, or Word files do little to improve efficiency with no way to quickly insert the data into the report.
Thoroughly documenting inspections is key to proper ITM—and not just for the most obvious reasons of meeting NFPA record requirements, sending reports to the AHJ, and generating a list of issues that need to be corrected. After a fire, proper documentation can also help absolve facility managers of liability when inspections are conducted to determine why a fire occurred, and if any mistakes were made.
“I don’t want to be the facility manager who doesn’t have his ‘i’s dotted,” Chris Jelenewicz, engineering program manager for the Society of Fire Protection Engineers, states in a facilitiesnet report. “They will ask whether you tested the fire alarm in accordance with standards and, if you don’t have documentation, you’ll be in trouble.”
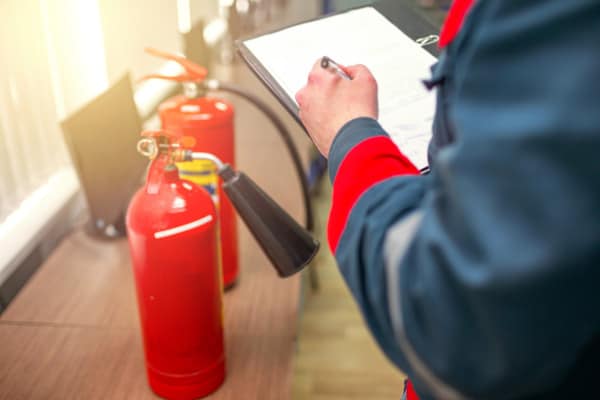
Unfortunately, that means each paper inspection typically generates at least another hour of additional work as individuals spend time uploading files from thumb drives, struggle to decipher scribbled notes, and scan, photocopy, or combine images and handwritten reports into electronic documents.
Even worse, notes and hard copies of paperwork are easily lost or destroyed, making it all too simple to leave something important off of final reports. Paper inspections also force facility managers to dig up old documents to obtain previous inspections results and match those pieces of information together. This time-consuming task can cause subtle downward trends in performance or compliance to be missed if the old reports are missing.
Every day that passes before a critical deficiency or impairment is fixed creates potential life safety risks for the facility and can put property owners afoul of NFPA and local fire code timelines. The same efficiency problems also apply when facility managers hire ITM contractors who rely on paper inspections—often causing days and even weeks to pass before inspection reports and repair proposals are even generated and approved.
Fire inspection software helps facility managers increase efficiency and compliance
Fire inspection software from Inspect Point eliminates the inefficiency of paper inspections and significantly improves compliance. The 100 percent digital interface helps facility managers perform faster, more thorough ITM of fire protection systems—while automating the tedious back-office work of putting reports together. Instead, in-house tasks are thoroughly and instantly documented through the platform to ensure properties comply with current and future NFPA, insurance, and AHJ requirements.
All primary NFPA codes now permit electronic inspection reporting, including NFPA 25:
From the 2017 edition of NFPA 25
4.3.1.1* Records shall be permitted to be stored and accessed electronically.
New technology can be intimidating, and the fire protection industry is sometimes slow to embrace innovations. But performing a digital inspection is simple for any facility manager used to operating a cell phone or mobile tablet. Inspect Point fire inspection software is user-friendly and compatible with iPads and other mobile devices.
It provides a step-by-step process for every ITM activity, requiring users to check off each action to make sure no detail goes unnoticed, no step is missed, and 100 percent compliance is achieved. The software is preloaded with all of the questions, NFPA codes, and standards a facility manager needs to inspect fire protection equipment, including sprinklers, standpipes, alarms, hydrants, extinguishers, and fire pumps.
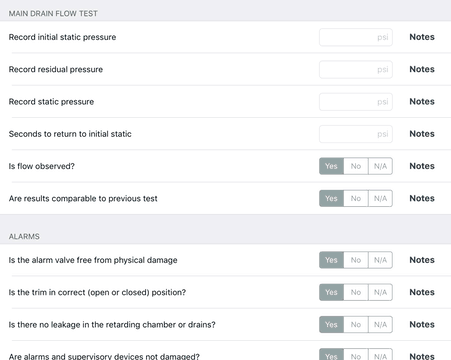
The program can also be customized to ensure compliance with local laws and to decrease inspection time by eliminating items that aren’t relevant to the current frequency, system, asset, and building requirements. The software also places a property’s ITM history at a user’s fingertips, eliminating time-consuming searches for old reports and making it easy to spot concerning trends. The program can even flag equipment that has suffered previous deficiencies and instantly create fire pump performance curves, one of the most tedious and complicated ITM tasks.
Notes and photos taken with the iPad or other mobile device are automatically transferred into reports, so nothing important is omitted. Reports are generated automatically with a single click—freeing up personnel to focus on more important tasks than transcribing handwritten notes. The software also improves safety and compliance by helping facility managers prioritize and keep track of all impairments or deficiencies that are discovered, sending automatic reminders to ensure they are corrected.
Digital ITM software can hasten compliance for facility managers by speeding follow-up on deficiencies and impairments discovered by outside contractors as well. Instead of waiting for administrative staff to generate reports and repair proposals, contractors can use digital inspection programs to produce them while they are still on the job site, followed by obtaining instant approval to start work.
In addition, Inspect Point automatically creates and schedules recurring inspections at the required frequency, reducing the possibility that busy internal departments will accidentally violate fire code requirements or forget to contact an outside ITM company at the right time.
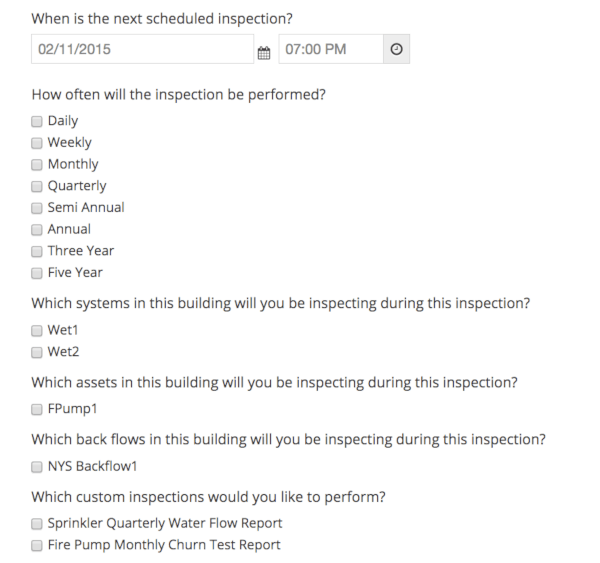
Faster, more reliable ITM with fire inspection software boosts compliance and safety
Properly maintained fire sprinkler systems control 96 percent of the blazes that trigger them. Standpipes, fire extinguishers, hydrants, and other components of a facility’s fire protection system play similarly vital roles in preventing damage and saving lives.
Whether facility managers enlist the help of an ITM contractor or do the work internally, staying code-compliant is a vital responsibility. Fire inspection software helps professionals perform faster, more reliable inspections, testing, and maintenance of fire protection systems—getting the system closer to everyone’s goal of 100% compliance, 100% of the time.
If you’d like a detailed briefing on exactly how fire inspection software works, sign up for a free demo of Inspect Point’s fire protection ITM software.
For more information about Inspect Point or QRFS products, call us at +1 (888) 361-6662 or email support@qrfs.com.
This blog was originally posted at blog.qrfs.com. Check us out at Facebook.com/QuickResponseFireSupply or on Twitter @QuickResponseFS.
Hello, we have multiple resorts, and an in-house fire department. We have thousands of sprinklers, hundreds of fire extinguishers, and hundreds of fire hoses located strategically. I am primarily interested in software that will help our inspection, maintenance, audit, and report writing become more efficient. We perform all but a few inspections with our own personnel, and also do most of our own maintenance. We utilize global standards such as NFPA and it would be helpful to have software that is compatible with these standards. It would be helpful to have a software for ensuring that inspections and maintenance are performed on-schedule. I would be interesting in knowing if your software would be suitable for this.
Best regards, Anthony Betz
Chief Security Officer
Anthony — Inspect Point software comes preloaded with NFPA ITM requirements for sprinklers, standpipes, and more, so it would likely be perfect for your needs. If you visit our landing page and click the “Schedule Your Free Demo” button, we’ll be in touch and get you scheduled to take a guided test run on how it works!
It is good to know that there is now software that thoroughly and instantly documents in-house tasks through the platform to ensure that properties comply with NFPA, insurance, and AHJ requirements. My friend shared with me her frustration on looking for ways to improve their fire protection systems. I will tell her what I found in your post and advise her to look for a provider in our area that offers fire inspection software.