Switching to nitrogen gas can extend the life of dry sprinkler systems
Dry sprinkler systems may sidestep the cold-weather issues that affect wet sprinkler pipes, but their greater potential to rust from the inside out presents its own challenge. A growing trend toward replacing pressurized air with nitrogen in dry sprinklers may hold the key to stopping corrosion and significantly increasing the lifespan of dry pipes.
In this installment of our series on dry sprinkler systems, we explore why they are more prone to corrosion and how using pressurized nitrogen can prevent it. Stay tuned for future blogs on dry sprinkler testing requirements.
Are you looking to buy components for a building’s sprinkler system? QRFS offers a range of dry sprinkler heads available on special order. Simply give us a call at 888.361.6662 or email support@qrfs.com.
You can also view our in-stock selection of sprinkler gauges, valves, supervisory switches, and other accessories.
Trapped water is the source of dry sprinkler corrosion
For as long as fire sprinklers have existed, corrosion has been a significant issue. But while all systems may experience problems, the corrosion potential dramatically increases in dry sprinklers—and damage can start immediately after a system is installed. That’s because the pressurized air historically used to fill dry pipes makes them the perfect breeding ground for what the fire protection industry refers to as the “corrosion triangle:” the three elements—iron, water, and oxygen—that must be present for electrochemical corrosion to occur.
At the right temperatures, these elements can also cause microbiologically influenced corrosion (MIC) to flourish in sprinkler pipes. MIC bacteria impact metal by causing small nodes called tubercules to form, pitting the pipes, and degrading flow characteristics if loose scale or rust plugs sprinklers and valves.
Specially designed for properties exposed to bitterly cold temperatures, dry sprinklers use pressurized air or nitrogen to keep a dry valve closed, blocking the water supply from entering unheated pipes and freezing. When heat from a fire causes one or more sprinklers to activate, the air pressure drops and the valve opens, releasing the water into the pipes and onto the fire.
But even though dry sprinkler pipes are only supposed to be filled with air during normal operating conditions, it’s nearly impossible to keep them completely dry. The mixture of gases in the air enables condensation to form inside the pipes. And it’s easy for a little water to become trapped during the annual trip test required by NFPA 25: Standard for the Inspection, Testing, and Maintenance of Water-Based Fire Protection Systems, even though drainage is also mandated after the test.
The 2019 edition of NFPA 13: Standard for the Installation of Sprinkler Systems sets specific guidelines for proper pitching of dry sprinkler pipes—at least a ½-inch per 10 feet for branch lines and at least ¼-inch per 10 feet for main lines in non-refrigerated areas, for instance—in a bid to prevent water from pooling inside the pipes (16.10.3).
But when some inevitably do, the water reacts with the oxygen in the air to form the orangey-red rust that eats away at metal pipes, eventually creating holes the size of pins or even pennies.
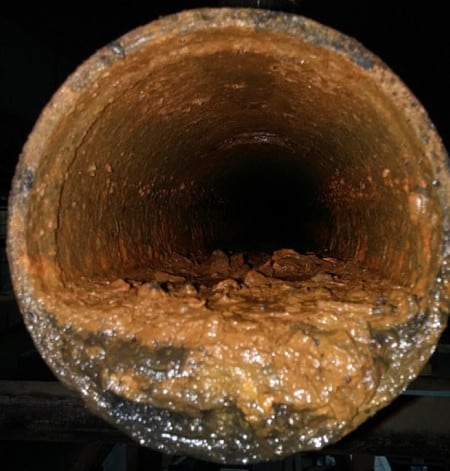
Dry pipe material: black steel vs. galvanized steel
While NFPA 13 (16.3) permits several options for sprinkler piping, including copper and (in some uses) CPVC, dry sprinkler systems are typically installed with galvanized or black steel pipes.
Galvanized steel, the pricier option, features walls that are coated with zinc. Since zinc is more reactive than steel, it’s intended to serve as a sacrificial material that creates a protective layer of scale build-up while protecting the pipe underneath. But concentrated corrosion action around small holes in the zinc may actually cause galvanized pipes to fail faster than black steel, with studies showing that pinhole leaks can form in galvanized steel within two years of installation—and ruptures within four years, according to Potter Corrosion Solutions.
Residential dry systems and those in light-hazard environments can take advantage of a UL-listed chloro-polyvinyl chloride (CPVC) pipe option by Tyco that has little chance of corrosion, but stronger steel pipes are better suited to the larger sprinkler systems required for commercial uses. With the potential to become brittle at low temperatures, CPVC is not a good option in many commercial dry systems. A serious safety hazard can occur if a pipe ruptures and suddenly releases the energy of the pressurized gas.
The impact of corrosion on dry sprinklers
As the tiny holes caused by corrosion cause dry sprinklers to lose pressure, the system’s air compressor kicks in. But if air leaks faster than the compressor can keep up, the system will trip and cause water to flow into the pipes and through the holes—starting as a drip that will eventually start gushing as the holes enlarge.
The 2017 edition of NFPA 25 establishes inspection requirements to spot corrosion that are covered in our previous two blogs:
Guide to Dry Sprinkler Systems: Daily, Weekly, and Monthly Inspections
Guide to Dry Sprinkler Systems: Quarterly, Annual, and Longer Inspections
These inspections aim to catch damage in its earliest stages, before it leads to expensive repairs or property damaged by leaking water—or worse, potentially catastrophic losses if the sprinkler malfunctions during a fire. Corrosion can also impact system hydraulics and reduce the efficiency of fire sprinkler system design.
If corrosion is discovered in time, it’s possible to repair or replace the pieces of failing pipe. But in addition to causing repeated maintenance costs, read this carefully: pinhole leaks in a section of pipe are often a minor symptom of a rotting system hidden within the ceiling.
A Potter Corrosion Solutions report promoted by NFPA asserts that 73 percent of dry sprinkler systems have significant corrosion issues after 12.5 years.
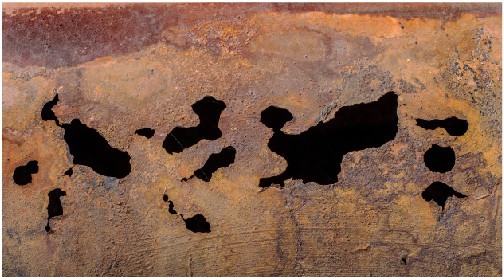
Preventing corrosion in dry sprinklers: the nitrogen solution
A new standard is emerging among building owners and system designers looking to stay ahead of dry sprinkler corrosion: replacing the air supply in a dry sprinkler system with a nitrogen solution.
Nitrogen is an inert gas, meaning it doesn’t undergo the chemical reactions that lead to electrochemical corrosion. When 98 percent nitrogen gas or greater is used to create an oxygen-free atmosphere, oxidation or rust doesn’t occur—extending the lifespan of dry sprinkler pipes an average of 5.3 times longer regardless of whether water is present, according to Potter Corrosion Solutions research.
Since dry systems typically last between 10-15 years, that means stripping oxygen from the pipes and pushing in pure nitrogen can theoretically extend the lifespan of dry sprinklers to roughly 50 to 80 years.
Minimizing corrosion in sprinkler pipes also creates a significant difference in long-term maintenance and replacement costs over the life of a building. Sprinkler Age reports that a nitrogen generator for a 250- to 500-gallon sprinkler system involves upfront costs that average around $10,000.
The average corrosion-induced pipe repair costs between $1,500 and $2,000, which can quickly surpass the cost of switching to a nitrogen-based system if corrosion is an ongoing problem. While the best results are typically achieved by filling new systems with nitrogen, flushing compressed air out of existing systems and replacing it with nitrogen goes a long way toward preserving the integrity of sprinkler pipes.
NFPA 13 permits using air, nitrogen, or other approved gases in dry sprinkler systems but section 5.1.5.2 recommends choosing nitrogen when water supplies and environmental conditions “contribute to unusual corrosive properties.” Nitrogen can be generated onsite or from storage containers sized to provide a reliable supply that covers at least six months of expected maintenance use (A.8.2.6.8.1).
NFPA 13 outlines the following guidelines for using nitrogen in dry systems:
From the 2019 edition of NFPA 13
8.2.6.8 Nitrogen or Other Approved Gas
8.2.6.8.1* Where nitrogen or other approved gas is used, the supply shall be from a reliable source.
8.2.6.8.2 Where stored nitrogen or other approved gas is used, the gas shall be introduced through a pressure regulator and shall be in accordance with 8.2.6.6.
8.2.6.8.3 A low pressure alarm shall be provided on gas storage containers to notify the need for refilling.
8.2.6.8.4* When nitrogen or other approved gas is the only source of gas for pressurizing a system, it shall have a capacity capable of restoring normal gas pressure in the system within 30 minutes.
8.2.6.8.5 The requirements of 8.2.6.8.4 shall not apply in refrigerated spaces maintained below 5° F (-15° C), where normal system air pressure shall be permitted to be restored within 60 minutes.
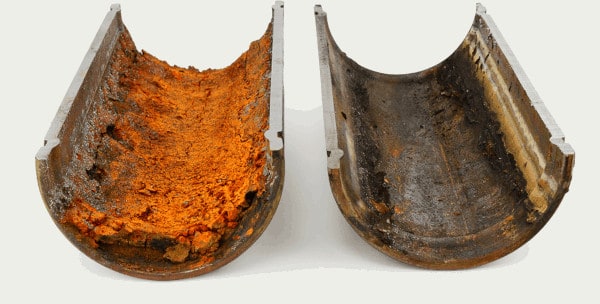
Here’s how nitrogen-based dry sprinklers work
Nitrogen sprinkler systems can be filled by tanks or cylinders of compressed nitrogen, but a nitrogen generator is generally preferred. Many building owners worry about having high-pressure tanks onsite, and they also resist the added headache of monitoring tank levels and scheduling deliveries from an industrial gas supplier.
In contrast, nitrogen generators maintain nitrogen levels within a sprinkler system with lower ongoing costs than nitrogen deliveries. Two types of nitrogen generators are typically used to produce high-purity nitrogen gas onsite by extracting it from the air, which is composed of 78 percent nitrogen gas: membrane nitrogen Generators and pressure swing adsorption (PSA) nitrogen generators.
Membrane nitrogen generators use an attached air compressor that forces air into the generator and through a specialized membrane comprised of thousands of hollow fibers designed to separate pure nitrogen from oxygen and other gases. The walls of each fiber are permeable to gas molecules, but some pass through more easily than others.
The “fast” gases—including oxygen, carbon dioxide, and water vapor±—pass through the fiber walls and are released back into the atmosphere as waste. A high-purity stream of the “slow” gas—nitrogen—flows through the membrane outlet and is captured and stored in a tank connected to the sprinkler system’s air maintenance device, which pipes it to the dry riser.
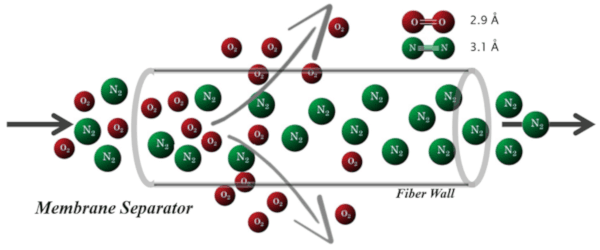
Pressure swing adsorption (PSA) nitrogen generators separate different types of gas under high pressure and then periodically release them with a swing to low pressure. Compressed air is drawn out of the atmosphere and directed into an adsorbent material such as a carbon molecular sieve (CMS). As the air passes over the CMS, the smaller oxygen molecules are adsorbed into the pores while the larger nitrogen molecules pass through unhindered.
There is a hitch: the adsorbent material eventually becomes saturated with oxygen molecules, and separation stops. When that occurs, the adsorber can be “wiped clean” by depressurizing it so the oxygen is released back into the atmosphere.
For this reason, PSA generators are always designed with at least two adsorbers, ensuring that one is always actively producing nitrogen while the other regenerates. But even so, there is a brief period during re-pressurization when no nitrogen is being produced, making a nitrogen buffer tank necessary to maintain constant pressure in the sprinkler system. Switching between the two adsorbers also creates a need for multiple automated control valves, which increases potential points of failure.
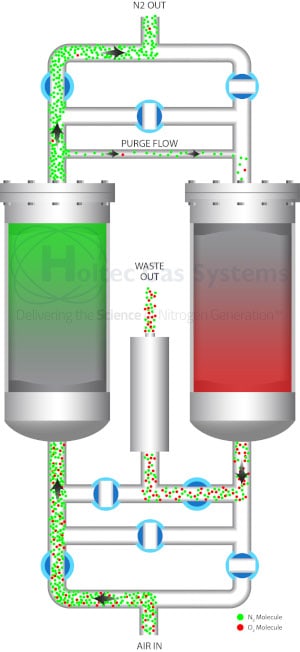
Both types of generators offer the added benefit of helping dry systems dry out over time. The nitrogen produced in the generator is very dry, with a dewpoint of about -71° F. Over several weeks of operation, nitrogen-based dry systems should become completely dry—eliminating two sides of the corrosion triangle.
The size of the sprinkler system and its individual zone capacities determine the size and number of nitrogen generators required.
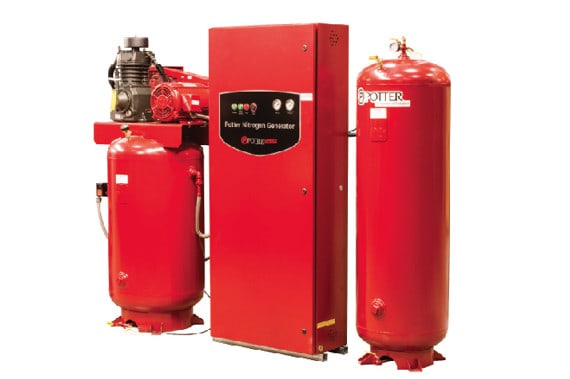
The trend toward nitrogen in dry sprinkler systems
As with any evolving technology, education is key to the widespread adoption of nitrogen-based dry systems. Although knowledge of this solution is growing, many sprinkler contractors aren’t trained in nitrogen generation technology, so they don’t promote it for designing fire protection systems or during service calls.
Internal corrosion of dry sprinkler systems represents a major concern for the fire sprinkler industry. Traditionally, ongoing issues mandate pricey and large-scale replacement of sprinkler pipes and fittings. But replacing corrosive pressurized air with nitrogen can extend the life of existing systems and potentially provide an immediate ROI by reducing the number of service calls.
Stay tuned for the next installments in our review of dry sprinkler systems and their applications, in which we’ll begin to explore testing requirements.
If you’re looking to buy components for your dry pipe sprinkler system, QRFS offers a range of dry sprinkler heads available on special order. Simply give us a call at 888.361.6662 or email support@qrfs.com and we’d be happy to help.
We also stock sprinkler gauges, valves, switches, and other accessories that are applicable in dry systems.
Check out previous installments in the series:
A Guide to Dry Sprinkler Systems, Part 1: System Overview
A Guide to Dry Sprinkler Systems, Part 2: Components and Installation Requirements
A Guide to Dry Sprinkler Systems, Part 3: Installation of Components
A Guide to Dry Sprinkler Systems, Part 5: Daily, Weekly, and Monthly Inspection Requirements
Guide to Dry Sprinkler Systems, Part 6: Quarterly, Annual, and Longer Inspections
Since copper doesn’t rust is nitrogen equally effective in preventing pipe deterioration on a dry sprinkler system?
We don’t know if the two are equally effective, but nitrogen is effective, which is why many dry systems replace air with it to constitute the pressurized gas that holds the dry pipe valve shut. You can read more on that here.
Hello,
What is the point of the bleeders at the end of the dry pipes? Do they actively remove anything or are they there to make sure air is consistently being replaced? There was a closed ball valve that kept it off, so I was trying to figure out why.
Tim — A bleeder valve could be used to relieve excess system/closed network pressure.