The steps to test dry sprinklers and make sure they are up to standards
Fully testing a dry sprinkler system once per year is a routine and important part of a fire safety compliance plan. Dry sprinkler tests ensure that these systems can provide reliable fire protection when temperatures drop below freezing and they prevent expensive property damage.
The dry pipe valve trip testing discussed in detail in our previous blog is generally the first test that comes to mind for annually testing dry sprinklers. But many other parts of a dry sprinkler system require in-depth physical checks once a year. In this installment of our series on dry sprinkler systems, we examine the National Fire Protection Association (NFPA) requirements and best practices for annual testing of many dry sprinkler system parts.
Are you looking to buy components for your building’s sprinkler system? QRFS offers a range of dry sprinkler heads available on special order. Simply give us a call at 888.361.6662 or email support@qrfs.com.
You can also view our in-stock selection of sprinkler gauges, valves, supervisory switches, and other accessories.
Full dry sprinkler system testing is required once a year
Dry sprinkler systems are specially designed to protect properties regularly exposed to freezing temperatures. Unlike wet systems, which risk failure due to water-filled pipes that can freeze and ultimately burst in cold temperatures, dry sprinklers rely on pressurized air or nitrogen to hold back the water supply at a dry pipe valve located in a heated space. When heat from a fire activates a sprinkler head, the compressed air escapes and opens the valve, enabling the water supply to flow through the pipes and onto the fire.
In-depth annual dry sprinkler tests that involve physical checks of all the system’s parts not only confirm that systems are up to standards, but ensure they will perform as expected during a fire. NFPA 25: Standard for the Inspection, Testing, and Maintenance of Water-Based Fire Protection Systems establishes minimum requirements for testing. A dry sprinkler system’s fire pump also requires extensive annual testing that is addressed in detail in previous blogs.
While the standard makes it clear that property owners or their representatives are ultimately responsible for ensuring their sprinkler systems are functioning properly, it recognizes the complexity of the required tests and grants the ability to delegate authority to qualified professionals (The 2017 edition of NFPA 25: 4.1.1). The property owner, however, is charged with keeping careful records of all tests so deteriorating conditions are easily spotted compared to past and future results (4.3).
Keep in mind that the dry sprinkler tests mandated by NFPA 25 are routine, and unusual conditions should prompt additional testing. Consultations with the manufacturer, listing agency, and authority having jurisdiction can help determine the right course of action when more testing is required to uncover the source of a problem.
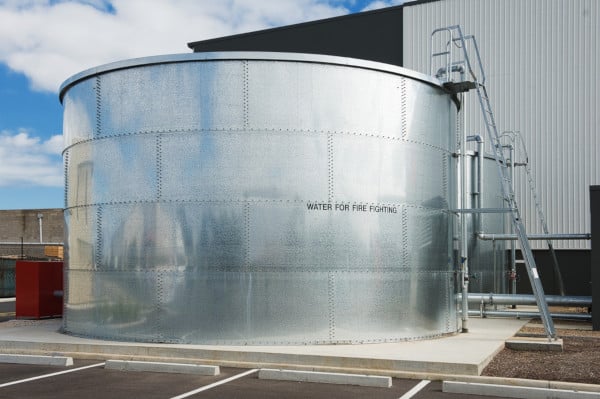
Dry sprinkler tests: water tanks
Water tanks can be used to provide water to dry sprinkler systems when an adequate public or private supply isn’t available. In many cases, a building will require several thousand or hundreds of thousands of gallons to feed its fire protection system. Water tank heating systems, low water temperature signals, and high water temperature limit switches should be tested annually before the heating season begins. The NFPA Handbook provides additional, valuable guidance for annually testing water tank parts.
For some components, such as low-temperature signals and high water temperature limit switches, it might not be possible to test the actual initiating device without draining the tank. In those cases, only the internal circuitry is tested annually, but NFPA recommends that those other components be removed and fully tested when the tank is drained for maintenance or inspection.
Devices that fail their tests must be investigated. Testing should be repeated once the issue is corrected or repaired.
Tank heating system tests
A frozen water supply would render a dry sprinkler system useless during a fire, and even small chunks of ice could cause blockages that prevent water from flowing when it’s needed during an emergency. Tank heating systems must be tested to prevent ice from forming, and low-temperature signal tests aim to ensure that the supervisory switch is able to signal the appropriate monitoring location if water temperatures approach freezing.
From the 2017 edition of NFPA 25
9.3.2 The tank heating system, where provided, shall be tested prior to the heating season to make certain it is in the proper working order.
9.3.3* Low water temperature signals, where provided, shall be tested prior to the heating season.
The manufacturer’s instructions should be followed for testing water tank heating systems.
Normally, testing low water temperature signals would require exposing the switch to a temperature at or below its designated operating temperature, but that’s not usually possible without draining the water tank. Instead, testing of the internal circuitry between the installed switch and monitoring location can be conducted. The manufacturer’s testing instructions should also be followed.
The NFPA 25 Handbook outlines the following steps to test a low-temperature signal:
- Prior to any testing, notify the fire department and alarm monitoring company (as needed), as well as the facility’s representatives, that testing is going to be conducted.
- Check the fire alarm control panel, remote annunciator, or other supervising panel to determine that the low-temperature signal is not currently active on the system.
- Remove the cover plate on the low-temperature supervisory switch, exposing the wiring connection of the unit.
- Disconnect one leg of the wired connection of the low-temperature supervisory switch to simulate an open condition.
- Verify the receipt of a low-temperature supervisory signal at the fire alarm control panel, remote annunciator, or other supervising panel.
- Complete additional testing of the switch as recommended by the manufacturer.
- Reconnect the wiring connection for the low-temperature supervisory switch and reinstall the cover plate.
- Upon completion of all testing, notify the fire department and alarm monitoring company (as needed), as well as the facility representatives and reset the fire alarm system as necessary. You should also verify that initiated signals were so received by the fire department and/or alarm monitoring company.
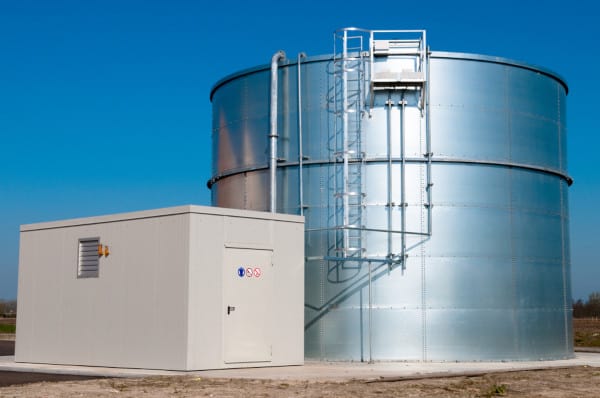
High water temperature limit switch tests
High water temperature limit switch tests are designed to ensure that the water tank’s heating system shuts off if temperatures start to climb too high. Once again, only the circuitry is tested because the switch can’t be accessed without draining the tank. Manufacturer instructions should also be followed.
9.3.4* High water temperature limit switches on tank heating systems, where provided, shall be tested prior to the heating season.
The NFPA 25 Handbook outlines the following steps for testing high-temperature limit switches:
- Prior to any testing, notify the fire department, alarm monitoring company (as needed), and facility representatives that testing is going to be conducted.
- Check the heating system to ensure that it is in operation prior to initiating the test.
- Remove the cover plate on the high-temperature limit switch, exposing the wiring connection of the unit.
- Disconnect one leg of the wired connection of the high-temperature limit switch to simulate an open condition.
- Verify the shutdown of the power or fuel source to the heating system.
- Complete additional testing of the switch as recommended by the manufacturer.
- Reconnect the wiring connection for the high-temperature limit switch and reinstall the cover plate.
- Upon completion of all testing, notify the fire department, alarm monitoring company (as needed), and facility representatives and reset the fire alarm system as necessary. An additional reset of the heating system might be required.
High/low water level signal tests
High/low water level signal testing ensures that appropriate monitoring locations are notified of high and low water conditions in the water tank that could impact sprinkler performance or cause the tank to overflow. As always, manufacturer instructions should also be followed.
9.3.5* High and low water level signals shall be tested annually.
The NFPA 25 Handbook details the following steps:
- Prior to any testing, notify the fire department, alarm monitoring company (as needed), and facility representatives that testing is going to be conducted.
- Check the fire alarm panel, remote annunciator, or other supervising panel to determine that a high/low water level signal is not currently active on the system.
- Note the normal operating water level in the tank.
- For tanks that include a high water level switch, complete steps 5 through 9. Otherwise, skip to Step 10.
- Open the manual fill valve for the tank and monitor the fire alarm panel, remote annunciator, or other supervising panel to verify the initiation and transmission of the high water level signal. Ensure that the signal is initiated before water levels rise more than 12 inches (300 mm) above normal or overflow from the tank, whichever comes first.
- Shut down the manual fill valve.
- Locate a drain connection for the tank and check the surrounding area for any obvious conditions that would prevent water from being discharged safely or cause direct damage to the immediate vicinity. When water is discharged to an area subject to potential freezing conditions, the facility representative should be advised of the potential for icing that could cause injuries.
- Drain water from the tank down to the normal operating level.
- Verify that the high water level signal is restored at the fire alarm panel, remote annunciator, or other supervising panel, resetting as necessary.
- For tanks that include a low water level switch, complete steps 11 through 16. Otherwise, skip to Step 17.
- Shut down the control valve for any automatic fill lines to the tank.
- Locate a drain connection for the tank, and check the surrounding area for any obvious conditions that would prevent water from being discharged safely or cause direct damage to the immediate vicinity. When water is discharged to an area subject to potential freezing conditions, the facility representative should be advised of the potential for icing that could cause injury.
- Initiate drainage of water from the tank. Monitor the fire alarm panel, remote annunciator, or other supervising panel and verify the initiation and transmission of the low water level signal. Ensure that the signal is initiated before water levels drop more than 12 inches (300 mm) below the normal operating water level.
- Shut down the drainage of the tank.
- Open the manual fill valve, or open any control valves that were shut as a part of Step 11 above, and refill to the normal operating water level.
- Verify that the low water level signal is restored at the fire alarm panel, remote annunciator, or other supervising panel, and reset them as necessary.
- Upon completion of all testing, notify the fire department, alarm monitoring company (as needed), and facility representatives, and reset the fire alarm system as necessary. Verify that initiated signals were received by the fire department and/or the alarm monitoring company.
Testing automatic fill valves
Automatic fill valves help ensure reliable fire sprinkler performance by maintaining normal operating water levels in the water tank that supplies the system. Annual testing ensures that the valves refill the tank to the proper level if water levels drop and then shut off. It also tests whether they can be operated through the connected control system and verifies the refill rate. Once again, some manufacturers provide additional testing instructions.
9.5.3* Testing. All automatic tank fill valves shall be tested yearly in accordance with the following:
(1) The valve shall be actuated automatically by lowering the water level in the tank.
(2) The refill rate shall be measured and recorded.
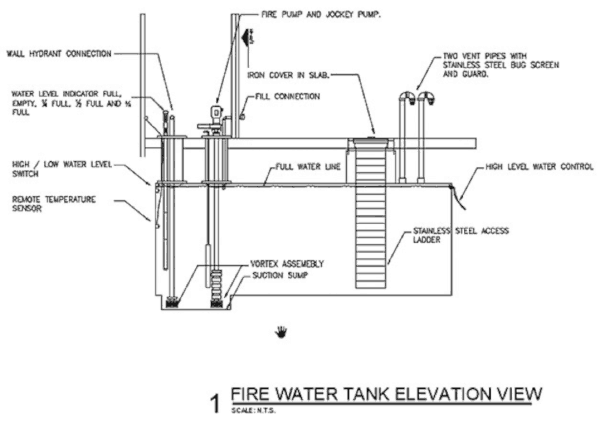
Dry sprinkler tests: supervisory signal devices
Supervisory signal devices (“except valve supervisory switches”) such as water flow alarm and low air pressure alarm devices are simply tested annually according to the manufacturer’s guidance:
From the 2017 edition of NFPA 25
13.2.8.2 Supervisory signal devices shall be tested annually in accordance with the manufacturer’s instructions.
Control valve tests
Control valves control the flow of water in an automatic sprinkler system, so it’s essential that they remain in the proper position and allow water to reach sprinkler heads during a fire. Closed control valves are the leading cause of failure in sprinkler systems. During annual dry sprinkler tests, inspectors exercise all control valves through their full range of motion to ensure there are no obstructions and they are functioning properly.
Spring tests are used to verify that post-indicator-type control valves are fully open. Post indicator valves make it easy to tell whether a hard-to-access valve is opened or closed by offering an accessible post that can not only exercise the valve but also indicates its position.
If the technician believes the valve is fully open, he or she should push the post’s handle in the “open” direction. The handle should move a short distance—about a quarter turn—and then “spring” back when released. This happens when the valve’s gate pulls up tight against the top of its casting and the valve shaft twists slightly. When this spring occurs, it indicates that the valve is fully opened, and the gate is attached to the handle.
If a foreign particle is jamming the gate, the handle is unlikely to spring back. If the gate is loose, the handle will continue to turn in the open direction with little or no resistance.
Before testing a control valve, make sure you have the proper wrench. Using an improper wrench (like a pipe wrench) may damage the operating nut, and using break-over bars and extensions on the wrench can damage the valve or post. If the proper wrench won’t close or open the valve with reasonable force, then maintenance or repairs are needed for the valve to function properly during an emergency.
From the 2017 edition of NFPA 25
13.3.3* Testing.
13.3.3.1 Each control valve shall be operated annually through its full range and returned to its normal position.
13.3.3.2* Post indicator valves shall be opened until spring or torsion is felt in the rod, indicating that the rod has not become detached from the valve.
13.3.3.2.1 This test shall be conducted every time the valve is closed.
13.3.3.3 Post indicator and outside screw and yoke valves shall be backed a one-quarter turn from the fully open position to prevent jamming.
13.3.3.4* A valve status test shall be conducted any time the control valve is closed and reopened at system riser.
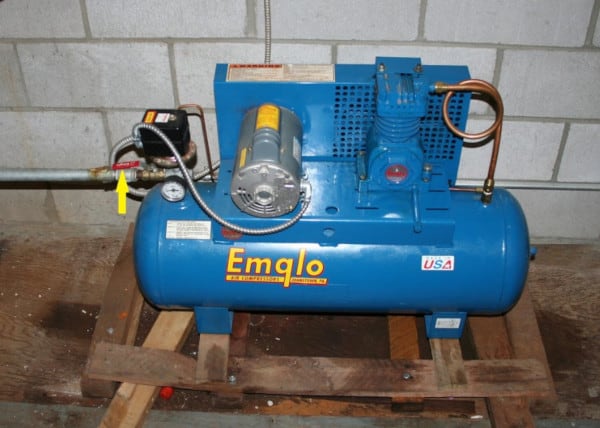
Testing air compressors in dry sprinkler systems
Dry pipe valves must be provided with a reliable air supply at all times that’s capable of restoring normal air pressure to the sprinkler system within 30 minutes (13.4.5.2.2.4). For systems filled with pressurized air, dedicated air compressors are the most common method for achieving this goal. Annual testing is required to ensure that the air compressor is functioning properly—pressurizing the sprinkler piping so the dry pipe valve stays closed until an activated sprinkler head causes the gas to escape.
While nitrogen generators are not specifically mentioned in NFPA 25 testing requirements, the air supply they generate for dry sprinkler systems fall under NFPA guidelines. Thus, nitrogen generators should be tested according to the manufacturer’s instructions to ensure the air supply is up to code and won’t cause the system to accidentally trip. Many property owners are replacing pressurized air with nitrogen in their dry sprinkler systems to reduce the high potential for corrosion caused by oxygen mixing with water and steel sprinkler pipes.
From the 2017 edition of NFPA 25
13.10.3 Testing.
13.10.3.1 Air compressors dedicated to water-based fire protection systems shall be tested annually to verify the following:
(1) Air compressor operates as intended on the proper drop of air pressure in the fire protection system.
(2) Air compressor restores normal air pressure in the fire protection system in the required time frame.
(3) Air compressor does not overheat while running.
Annual backflow preventer testing requirements in dry systems
Backflow preventers stop the stagnant water in a sprinkler system from flowing back into a municipal water supply and causing contamination. But their spring-loaded valves run the risk of failing when they aren’t exercised over long periods of time. Reduced pressure zone backflow preventers are especially susceptible to this problem. The forward flow test was created to ensure that backflow valves function properly.
System design generally dictates how this test is performed. A fire pump’s test header or other connections downstream of the backflow preventer valve can be used to conduct forward flow tests and flow water out of the building. For instance, a bypass around the check valve in the fire department connection line using a normally-closed control valve is a viable option. When flow to a visible drain can’t be accomplished, closed-loop flow is acceptable if a flowmeter or sight glass is also inserted into the system to ensure proper water flow.
During the test, the valve is slowly opened and pitot gauges can be used to test proper flow. The minimum flow rate during the test must equal sprinkler system demand, including hose stream allowance where applicable. If connections don’t permit a full flow test—most likely in older sprinkler systems—tests may be completed at the maximum flow rate that’s possible. When the desired flow is not achieved, further investigations and corrections are warranted.
Read our previous blog to learn more about using pitot gauges to measure pressure and gallons per minute.
From the 2017 edition of NFPA 25
13.7.2 Testing.
13.7.2.1* All backflow preventers installed in fire protection system piping shall be exercised annually by conducting a forward flow test at a minimum flow rate of the system demand.
13.7.2.1.1 Where water rationing is enforced during shortages lasting more than 1 year, an internal inspection of the backflow preventer to ensure the check valves will fully open shall be permitted in lieu of conducting the annual forward flow test.
13.7.2.1.2 The forward flow test shall not be required where annual fire pump testing causes the system flow rate to flow through the backflow preventer device.
13.7.2.2 Where hydrants or inside hose stations are located downstream of the backflow preventer, the forward flow test shall include hose stream demand.
13.7.2.3 Where connections do not permit verification of the forward flow test at the minimum flow rate of system demand, tests shall be conducted at the maximum flow rate possible.
In 2011, performance tests to ensure that backflow is being prevented were deemed outside of NFPA’s scope and removed from its standards. However, backflow remains a significant health concern and many local and state authorities still require the test. Inspectors should consult the authority having jurisdiction for testing requirements.
Watch this video of a forward flow test of a backflow preventer—along with some trouble getting a pressure reading:
Dry sprinkler tests ensure that systems are ready for emergencies
Dry sprinkler systems involve more complex parts and face harsher operating conditions than wet systems, and extra care is needed to keep them functioning properly. Comprehensive annual dry sprinkler tests ensure that they are ready to perform when they’re needed most.
Stay tuned for future blogs covering requirements for annual testing of fire pumps, as well as dry sprinkler system tests that must be performed every three to five years.
If you’re looking to buy components for your dry pipe sprinkler system, QRFS offers a range of dry sprinkler heads available on special order. Simply give us a call at 888.361.6662 or email support@qrfs.com and we’d be happy to help.
We also stock sprinkler gauges, valves, switches, and other accessories that are applicable in dry systems.
This blog was originally posted at blog.qrfs.com. Check us out at Facebook.com/QuickResponseFireSupply or on Twitter @QuickResponseFS.
Check out previous installments in this dry sprinkler system series:
Guide to Dry Sprinkler Systems, Part 1: System Overview
Guide to Dry Sprinkler Systems, Part 2: Components and Installation Requirements
Guide to Dry Sprinkler Systems, Part 4: Installation of Air Compressors and Air Maintenance Devices
Guide to Dry Sprinkler Systems, Part 5: Daily, Weekly and Monthly Inspections
Guide to Dry Sprinkler Systems, Part 6: Quarterly, Annual, and Longer Inspections
Guide to Dry Sprinkler Systems, Part 7: Fighting Corrosion
Guide to Dry Sprinkler Systems, Part 8: Daily, Weekly, and Monthly Testing
Guide to Dry Sprinkler Systems, Part 9: Quarterly and Semiannual Testing
Guide to Dry Sprinkler Systems, Part 10: Trip Testing the Dry Pipe Valve
Hello
We have no city water in our town. So we have several buildings in town with sprinkler systems and a system water supply tank. I witnessed a sprinkler system test recently and was curious is there and rules or regulation against using these tanks, the pump and sprinkler test head for water supply for fire apparatus?
Vincent — Thanks for reaching out. For code questions like this, we recommend submitting your question through QRFS Ask A Pro. Click the link to submit your question with some information about your building or system, and a fire protection professional will provide a detailed answer based on standards and codes. Our pros include AHJs, contractors, engineers, and code experts with 150+ years of combined experience!