Pressure-activated check valves prevent contamination and flooding from water sources used in fire protection systems
A check valve is a device that permits the flow of semisolids, liquids, or gases in only one direction. Check valves, featured in systems ranging from residential plumbing to pharmaceutical production, often rely simply on changes in pressure to manage flows.
In this article, we’ll focus on check valves for fire protection, discussing how they work, the types of check valves, and their benefits in fire sprinkler systems. Additionally, we’ll help you understand what components you should look for when selecting a check valve and discuss how to maintain them.
Already know what you need? Feel free to go straight to our check valve product page and selection of grooved riser check valve trim kits.
How does a check valve for fire protection work?
Each fire sprinkler system needs a dependable source of water for immediate use in a fire emergency. Most systems use some combination of gravity tanks, municipal water supplies, and sometimes fire department connections to provide water to sprinkler heads. But while multiple potential water sources provide an extra layer of reliability to fire protection systems, they can also be problematic: drinkable water might be contaminated by water from a fire hydrant, or dirty water from fire sprinkler pipes might flow through nearby streets and into nearby drains. In many other applications, it’s simply important that water only goes one way for performance reasons. These include protecting equipment such as pumps and filters from backflow damage, stopping drainage in a fire sprinkler system with elevation changes, providing pressure relief in liquid or pneumatic applications, and more.
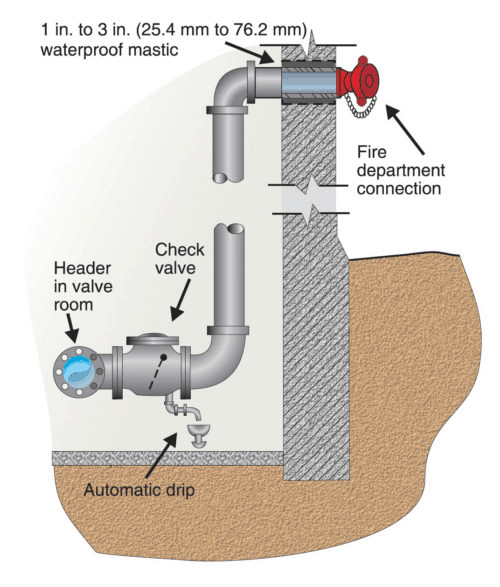
Check valves for fire protection prevent the unwanted reverse flow of water, known as backflow, from occurring. Many check valves feature a hinged clapper with a spring, which keeps the valve closed until the water flowing from some water source opens it. These clappers only open in one direction: when these flows reverse (or very nearly stop), the spring presses the clapper against a rubber seat, forming a water-tight seal.
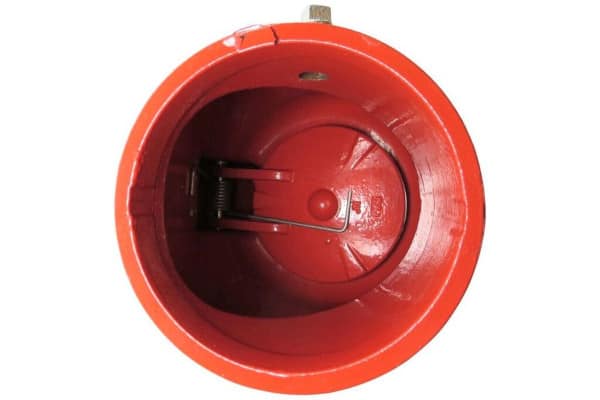
Think of the water on either side of the clapper as the supply side (between the water source and the check valve) and the system side (between the check valve and the rest of the system). When a fire sprinkler head discharges, water is released, decreasing the pressure on the system side. Shortly after, the higher pressures from water stored or pumped from the supply side push open the clapper, and water flows through the system.
How does a check valve for fire protection prevent contamination of potable water?
When multiple water supplies serve the same fire sprinkler system, each must have a check valve.
From the 2022 Edition of NFPA 13
16.9.4.1 Where there is more than one source of water supply, a check valve shall be installed in each connection.
Check valves decide which source actually provides the system with a supply of water at a given moment. When multiple water sources are used simultaneously, only the check valve connected to the highest-pressure water source remains open. Imagine you have a system with three water sources at the following pressure ratings, expressed in pounds per square inch (PSI):
Active Water Sources | Check Valve Status | ||
---|---|---|---|
100 PSI Fire Department Connection (FDC) |
75 PSI Gravity Tank |
50 PSI City Water |
|
FDC, Gravity Tank, & City | Open | Closed | Closed |
Gravity Tank & City Water | Closed | Open | Closed |
City Water Only | Closed | Closed | Open |
(Note: these pressure levels are provided only as illustrations and are not meant to be taken as typical for these water sources.)
When water is supplied from all three sources, only the check valve leading to the fire department connection remains open. Why?
Of these three sources, the FDC delivers the highest water pressure. This supply pressurizes the water on the system side. This increased system-side pressure is greater than the 75 or 50 PSI on the supply side of the check valves connected to the other water sources and, as a result, their clappers close.
To continue with this example, if only the city water and the gravity tank supply water, the check valve to the 75-PSI gravity tank will open, while the city water’s check valve stays closed. Only when all other sources are exhausted or closed does the municipal water supply open the check valve and flow into the system.
What are the types of check valves for fire protection and their benefits?
There are four main types of check valves for fire protection:
- Alarm check valve
- Swing check valve
- Grooved check valve
- Grooved shotgun riser check valve
- Backflow preventers comprising multiple check valves
An alarm check valve consists of a spring, a valve clapper, and an alarm port. The alarm port can be used to direct water to a water motor alarm or an alarm pressure switch used to alert nearby personnel to the system’s activation or send a signal to a fire alarm control panel.
A swing check valve can act as an alarm check valve for a wet-pipe fire sprinkler system, but only when that valve can sound an alarm.
From the 2022 edition of NFPA 13
16.11.3 Waterflow Detection Devices.
16.11.3.1 Wet Pipe Systems.
The alarm apparatus for a wet pipe system shall consist of a listed alarm check valve or other listed waterflow detection alarm device with the necessary attachments required to give an alarm.
Typically, these alarms are sounded by flow switches, which send a signal to local alarms and/or the fire alarm control panel when water flows through system piping.
Grooved check valves are a type of swing check valve for use in systems that have grooved-connecting pipe ends. Many grooved check valves can be used in a vertical or horizontal orientation, allowing them to be used in various configurations with a fire department connection, bypass connection, gravity pressure tank, or pump discharge connection.
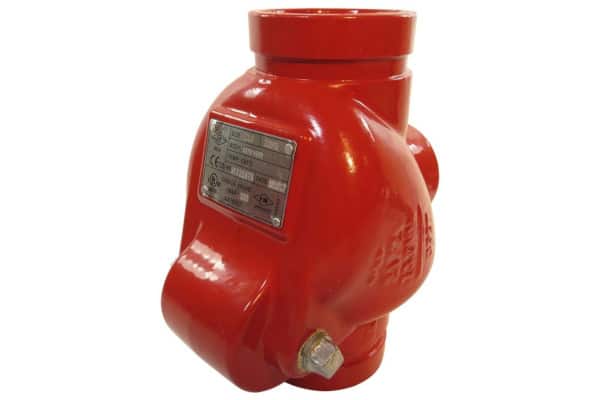
A grooved shotgun riser check valve is similar to a grooved check valve but includes pressure gauges to monitor the supply and system pressure. The shotgun configuration, which uses an electric water flow switch and an alarm bell, is only permitted in situations where a water motor alarm is not required. Shotgun riser check valves offer a more compact and economical alternative to an alarm check valve.
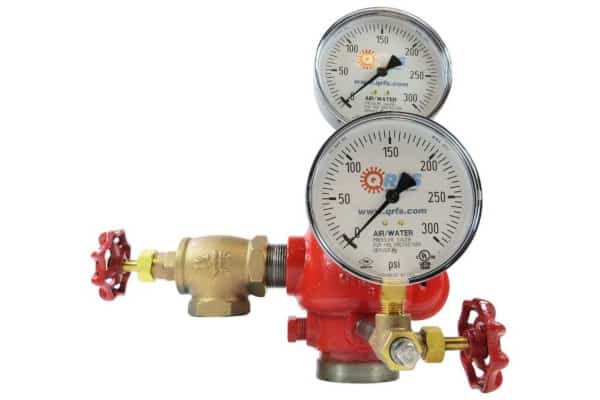
Finally, there are backflow preventers that are explicitly designed to prevent the contamination of water supplies. They use check valves and extra fail-safes to make absolutely sure water flows one way and doesn’t contaminate potable water supplies. You can read more about them in our other blog: “Backflow Preventer vs. Check Valve: What’s the Difference?”
Do check valves require periodic maintenance?
Yes, check valves require periodic inspections and maintenance. For this reason, NFPA 13 warns against burying check valves or positioning them in areas where they will be inaccessible.
From the 2023 Edition of NFPA 25
13.4.2 Check Valves
13.4.2.1 Inspection. Valves shall be inspected internally every 5 years to verify that all of the valve’s components operate correctly.
13.4.2.2 Maintenance. Internal components shall be cleaned, repaired, or replaced as necessary in accordance with the manufacturer’s instructions.
Alarm check valves and system riser check valves require more frequent inspections. Regular inspections help to verify that the clapper functions properly, that the valve seat is in good condition, and that there aren’t any visible signs of corrosion or blockages.
From the 2023 edition of NFPA 25
13.4.1.1* Alarm valves and system riser check valves shall be externally inspected quarterly and shall verify the following:
(1) The gauges indicate normal supply water pressure is being maintained.
(2) The valves and trim are free of physical damage.
(3) All valves are in the appropriate open or closed position.
(4) The retarding chamber or alarm drains are not leaking.
(5) Where applicable, the valve in the connection to the pressure-type contacts or water motor–operated alarm devices are either sealed, locked, or electrically supervised in the open position.
NFPA 25 also requires an inspection of alarm valves’ internal components every five years.
13.4.1.2* Alarm valves and their associated strainers, filters, and restriction orifices shall be inspected internally every 5 years unless tests indicate a greater frequency is necessary.
Maintenance should be performed by following the guidelines set by the manufacturer. Following an inspection, the manufacturer’s guidelines should also be used while returning the system to service.
What’s the best brand of check valve? What should I look for?
Every check valve installed on a fire protection system should be FM-approved and/or UL-listed. Listings certify that a check valve is designed to withstand the conditions it’ll be exposed to while in use. They’re also specifically required by NFPA for check valves on fire sprinkler FDCs and the alarm check valves used with wet-pipe fire sprinkler systems.
From the 2022 edition of NFPA 13
16.11.3 Waterflow Detection Devices.
16.11.3.1 Wet Pipe Systems.
The alarm apparatus for a wet pipe system shall consist of a listed alarm check valve or other listed waterflow detection alarm device with the necessary attachments required to give an alarm.
16.12.6 Valves.
16.12.6.1 A listed check valve shall be installed in each fire department connection and shall be located in an accessible location.
In addition, when you’re purchasing a check valve for fire protection, you should also consider:
- The size and pressure ratings of your fire protection system
- How easy and fast the check valve is to install
- The quality and construction of the valve’s components
QRFS carries UL-listed and FM-approved grooved check valves for pipes ranging from 2 to 6 inches. All of our check valves feature a non-slamming, spring-loaded clapper that forms a water-tight seal against an EPDM synthetic rubber seat. With a durable ductile iron exterior and corrosion-resistant stainless steel clapper, these valves are built to last.
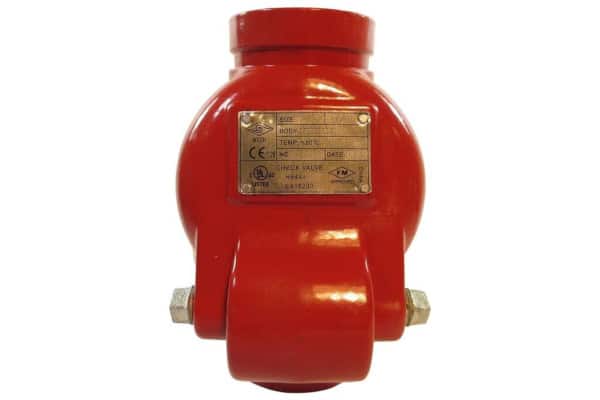
Any of these valves can be installed in a vertical or horizontal orientation. What’s more, each can be used as an alarm check valve with a shotgun riser check valve trim kit, available for every check valve we carry.
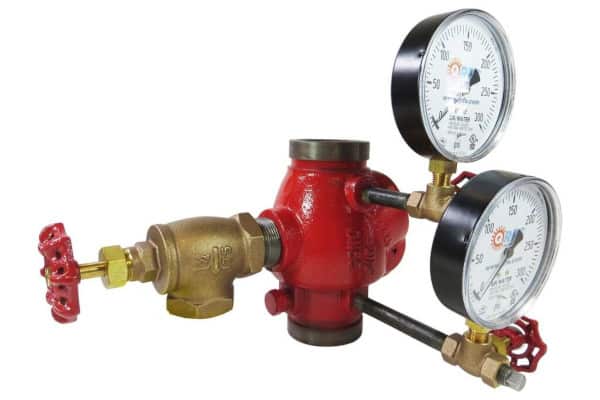
When you make a purchase from QRFS, you receive quality products at our competitive pricing. We begin processing your order the moment we receive it so we can provide you with the fastest standard delivery possible, generally reaching you in 2-3 business days.
View our selection of grooved, inline, and swing check valves, plus our inventory of grooved riser check valve trim kits.
Questions about this article or our grooved check valves? Call us at +1 (888) 361-6662 or email support@qrfs.com.
This blog was originally posted by Jason Hugo and Anna Hartenbach at blog.qrfs.com on October 26, 2017, and updated on January 1, 2019. If this article helped you select the right check valve, check us out at Facebook.com/QuickResponseFireSupply or on Twitter @QuickResponseFS.
Hi
I have a question about collectors piping at spray system fire fighting.
actually, we have a collector at piping with many outlet of it and I want to understand about calculation of them please follow under line:
1-How can I calculate volume of collector pipe according number of outlet of it?
2-How can I calculate length of collector pipe according number of outlet of it?
3-what is min or max length between two outlet pipe from collector?
3-Do we have standards about it that mention calculate collectors for example at NFPA???
Generally I want know about collector piping according standard on the other hand I have searched about it in NFPA13,14,15 but I can’t find that.
Thanks
Yousef, thanks for reaching out. These are complex questions that require in-depth research. We will consider this for a future blog topic!
Regarding check valves linked to a fire system in Australia (Vic) what is the standards on changing them.
I believe they need to be changed between every 5-7 years.
Do you have the standard extract stating this please.
Daniel — Unfortunately, we are not well-versed in Australian fire codes, though they do have a relationship with NFPA model codes and standards. If you would like an interpretation of any replacement rules for check valves in NFPA model documents, you can try our Ask a Fire Pro service; but a local fire protection professional should be able to offer more precise information on enforceable standards in your area of Australia. Thanks for reading!
Talking about Check Valves, What Check valve would be recommended for installing on a 1.5″ drain line before the Drip Cup Assembly on a Dry System? To keep the main drain water from volcanic eruption out of the drip cup and all over the room but yet allow for water from velocity check to drain down the drip cup as well?
Robert — For system application questions like this, you can try our Ask a Fire Pro service. Click the link to submit your question with some information about your building and system, and a fire protection professional will provide an answer based on best practices, standards, and codes. Our pros include AHJs, contractors, engineers, and code experts with 150+ years of combined experience!
where can I find in the code that the check valve needs to be changed on the standpipe FDC
Melissa — we’re aware of conditions-based replacement rules for check valves in FDCs within NFPA 25 — not a universal interval. For example, NFPA 25 (2023 edition) outlines that FDCs must be inspected quarterly (13.8.1) to verify that the “check valve is not leaking” (6), and “check valves “shall be inspected internally every 5 years to verify that all of the valve’s components operate correctly.” (13.8.6 and 13.4.2.1) Thus, there are conditions that warrant replacement. Hope that helps and thanks for reading!
If the standard stated that “check valves shall be listed for fire service”, does that mean the check valve shall be UL listed or FM approved?
Arnold — yes, though UL Listed and FM Approved are only two (albeit perhaps the most common/relevant in the US) listings. If you look at fire sprinkler data sheets, for example, they will also show listings with various European testing organizations, for example.