The NFPA 25 testing requirements for dry sprinklers at longer intervals
Regularly testing your dry sprinkler system ensures that it’s ready and able to provide automatic fire protection in areas where temperatures drop below freezing. But not every component requires testing every year.
In this installment of our series on dry sprinkler systems, we examine the National Fire Protection Association (NFPA) requirements and best practices for dry sprinkler tests that can stretch longer than a year.
Are you looking to buy components for your building’s sprinkler system? QRFS offers a range of dry sprinkler heads available on special order. Simply give us a call at 888.361.6662 or email support@qrfs.com.
You can also view our in-stock selection of sprinkler gauges, valves, supervisory switches, and other accessories.
Dry sprinkler tests should be performed by qualified professionals
Dry sprinklers sidestep the risk of burst or frozen pipes in freezing temperatures by relying on pressurized air or nitrogen to hold back the water supply at the main valve in a heated space. When heat from a fire activates a sprinkler head, the compressed air escapes, opening the valve and allowing the water to flow through the pipes and onto the fire.
The 2020 edition of NFPA 25: Standard for the Inspection, Testing, and Maintenance of Water-Based Fire Protection Systems establishes a schedule for testing of dry sprinkler systems. While property owners or their representatives are ultimately responsible for ensuring their sprinkler systems are functioning properly, system tests are in-depth and require qualified personnel to physically operate the system or one of its parts to make sure it performs to an acceptable standard.
Multi-year dry sprinkler tests
Dry pipe valve full flow trip tests—every three years
Please refer to Part 10 of our series on dry sprinkler systems, where full flow trip tests are discussed in detail.
Air leakage—every three years
Maintaining proper levels of pressurized air or nitrogen is essential for avoiding accidental trips of dry sprinkler systems. But corrosion can cause holes to form in dry sprinkler pipes that allow the gas to escape. When the air maintenance device can no longer keep up with the leaking air, the dry pipe valve will trip, flooding the system with water and potentially causing pricey property damage. NFPA 25 permits two methods for conducting air leakage tests every three years:
- A pressure test at 40 psi for two hours. The system is pressurized, and the air supply is shut off. To pass the test, the system may lose up to 3 psi (0.2 bar) of air pressure. If more is lost over two hours, the system fails, and air leaks must be detected and addressed.
- A pressure test at normal system pressure for four hours. The air supply source is turned off for four hours. If the low air pressure supervisory alarm activates within this period, air leakage is unacceptable and must be detected and addressed.
From the 2020 edition of NFPA 25
13.4.5.2.9 Dry pipe systems shall be tested once every 3 years for gas leakage, using one of the following test methods:
(1) A gas (air or nitrogen) pressure test at 40 psi (3.2 bar) shall be performed for 2 hours.
(a) The system shall be permitted to lose up to 3 psi (0.2 bar) during the duration of the test.
(b) Gas leaks shall be addressed if the system loses more than 3 psi (0.2 bar) during this test.
(2) With the system at normal system pressure, the gas source (nitrogen supply, compressor, or shop air) shall be shut off for 4 hours. If the low pressure alarm goes off within this period, the leaks shall be addressed.
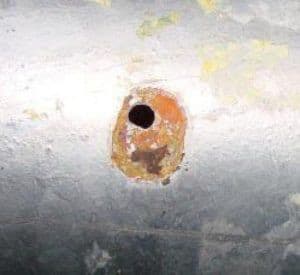
Water tank interiors—every three and five years
Although corrosion is a serious concern for steel water supply storage tanks, the interior can’t be tested while the tank is filled with water. So, when water tanks are drained for inspection and maintenance required by NFPA 25, the standard requires property owners to seize the opportunity to test the interior surface for evidence of corrosion like metal loss and rust, and to ensure that corrosion-resistant coatings remain in place.
NFPA 25 requires inspection of the interior of steel tanks without verifiable corrosion protection every three years (9.2.5.1.1), and the interior of all other tanks to be inspected every five years (9.2.5.1.2).
To aid in the evaluation of test results, the NFPA 25 recommends that the property owner or designated representative stencil the last-known date of interior paint jobs on the exterior of the tank in a conspicuous place. A good option is near one of the tank’s manways at eye level.
Tanks filled with water also prevent comprehensive annual testing of several water tank components, such as low-temperature signals and high water temperature limit switches. NFPA 25 recommends removing and fully testing those parts while the tank is drained for interior inspections.
From the 2020 edition of NFPA 25
9.2.6 Tests During Interior Inspection. Where a drained interior inspection of a steel tank is required by 9.2.5.4, the following tests shall be conducted:
(1) Evaluation of tank coatings shall be made in accordance with the adhesion test of ASTM D3359, Standard Test Methods for Measuring Adhesion by Tape Test, generally referred to as the “cross-hatch test.”
Cross-hatch adhesion tests ensure that corrosion-resistant paint coatings applied to a metal water tank are adhering properly. The test is conducted using pressure-sensitive cross-hatch adhesion tapes, and it is also referred to as a tape adhesion test.
Typically, an inspector uses a razor blade, knife, special cross-hatch cutter, or another sharp cutting tool to etch a lattice pattern through the coating down to the metal substrate. The test area is then brushed diagonally five times in each direction to remove any loose particles.

The special adhesion tape is firmly applied over the test area and removed quickly in a steady motion. Finally, the cross-hatch test area is visually compared to ASTM adhesion standards to determine if the amount of coating lifted off by the test tape signifies a greater problem.
The table below can help inspectors determine if the water tank passed the cross-hatch test:
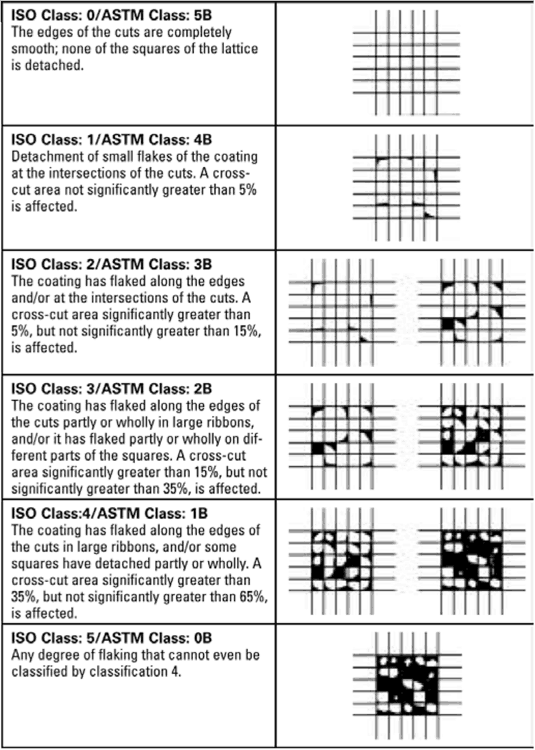
NFPA 25 also requires these tests of water tank interiors:
(2) Dry film thickness measurements shall be taken at random locations to determine the overall coating thickness.
(3) Nondestructive ultrasonic readings shall be taken to evaluate the wall thickness where there is evidence of pitting or corrosion.
(4) Interior surfaces shall be spot wet-sponge tested to detect pinholes, cracks, or other compromises in the coating. Special attention shall be given to sharp edges such as ladder rungs, nuts, and bolts.
(5) Tank bottoms shall be tested for metal loss and/or rust on the underside by use of ultrasonic testing where there is evidence of pitting or corrosion. Removal, visual inspection, and replacement of random floor coupons shall be an acceptable alternative to ultrasonic testing.
(6) Tanks with flat bottoms shall be vacuum-box tested at bottom seams in accordance with test procedures found in NFPA 22. [Standard for Water Tanks for Private Fire Protection]
Vacuum box, or bubble leak, testing is a simple way of spotting leaks in the seams of flat-bottomed tanks. Generally, a detergent solution is applied to a test area, and then a clear vacuum box with an attached compressor is used to create a low-pressure vacuum over the spot. The detergent bubbles over leaks within the pressure envelope, making them easily visible to inspectors.
Watch this video for instructions on how to perform a vacuum box test:
Water tank level indicators—every five years
From the 2020 edition of NFPA 25
9.3.1* Level indicators shall be tested every 5 years for accuracy and freedom of movement.
Water tank level indicators are used to gauge and manage water levels in a tank. It’s important to confirm that the indicator can move freely and isn’t stuck in the wrong position, impacting its performance.
Mercury gauges are often used to indicate water levels on older tanks, but it’s important to note that they are not permitted on new installations due to the health risks associated with the ingestion of mercury vapors and mercury absorption through human skin.
Mercury gauges should not be adjusted until a Material Safety Data Sheet is obtained from the property owner and all precautions are followed. Electronic tank water level indicators should be tested following the manufacturer’s instructions. Listed mercury gauges can be tested every five years as follows (A.9.3.1):
1. Overflow the tank.
2. Referring to the diagram below, close valve F and open test cock D. The mercury should drop quickly into the mercury pot. If it doesn’t, there’s an obstruction that needs to be removed from the pipe or pot between the test cock and gauge glass.
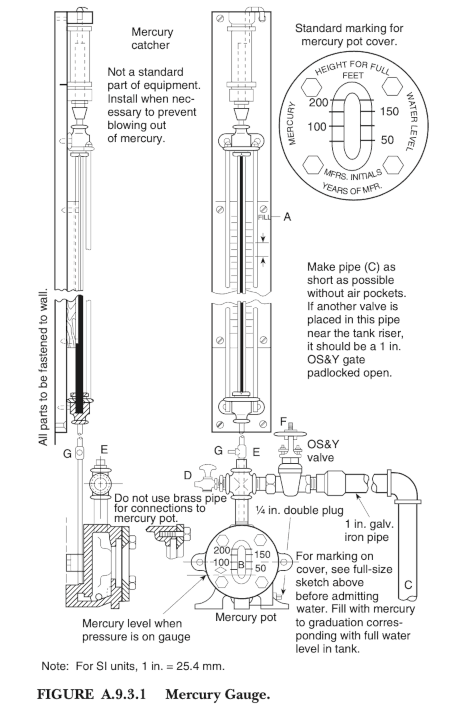
3. If the mercury does lower at once, close cock D and open valve F. If the mercury responds immediately and promptly comes to rest opposite the “full” mark on the gauge board, the indicator is functioning properly.
4. If the mercury column does not respond promptly and indicate the correct reading during the test, there are probably air pockets or obstructions in the water connecting pipe. To remedy this, open cock D; water should flow out forcibly. Allow it to continue to flow until all air is expelled and rusty water from the tank riser appears. Close cock D; the gauge should now read correctly.
If air separates from the water in the 1-inch (25 mm) pipe because it’s enclosed in a buried tile conduit with steam pipes, the air can be removed automatically by installing a ¾-inch (20 mm) air trap at the high point of the piping. This air trap can usually be easily installed in a tee connected by a short piece of pipe at E—with a plug in the top of the tee so mercury can be added in the future (if needed) without removing the trap. If there are inaccessible pockets in the piping—perhaps located below grade or under concrete floors—the air can be removed only through D.
5. If the water doesn’t flow forcibly through cock D in step 4, there is an obstruction that needs to be removed from the outlet of the test cock or from the water pipe between the test cock and the tank riser.
6. If there is water on top of the mercury column in the gauge glass, it will cause inaccurate readings and must be removed. To do so, lower the mercury into the pot as in step 2. Close cock D and remove plug G. Open valve F slowly, causing the mercury to rise slowly and the water above it to drain through plug G. Close valve F quickly when mercury appears at plug G. Be sure to have a receptacle ready to catch any mercury that drains out. Replace plug G and any escaped mercury in the pot.
7. After testing, leave valve F open, except under the following conditions: If it’s necessary to avoid forcing mercury and water into the mercury catcher, the controlling valve F can be closed when filling the tank but should be left open afterward. In cases where the gauge is subjected to a continual fluctuation of pressure, it could be necessary to keep F shut until it needs to be read. Otherwise, it will most likely be necessary to remove water frequently from the top of the mercury column.
Gauges—every five years
The data obtained from dry sprinkler system testing is only as valid as the gauges used for measurement; relying on faulty pressure gauges can produce inaccurate test results. Gauges should be replaced or tested every five years against a calibrated gauge. Damaged gauges—or those not accurate within 3 percent of the full scale—should be immediately recalibrated or replaced. Frankly, most facilities find it easier and more cost-effective to simply replace gauges instead of recalibrating them, given their low cost.
From the 2020 edition of NFPA 25
13.2.5.2 Gauges shall be replaced every 5 years or tested every 5 years by comparison with a calibrated gauge.
13.2.5.3 Gauges not accurate to within 3 percent of the full scale shall be recalibrated or replaced.
Dry sprinkler heads—every 10 years (after 15 years of service)
In our first blog on dry sprinkler testing, QRFS discussed how NFPA requires dry sprinklers to be laboratory tested or replaced every 10 years, which is considerably more often than most other sprinkler systems. NFPA 25 mandates that most types of sprinklers don’t need to be replaced or laboratory tested every 10 years until they have been in service for 50 years (5.3.1.1.1). The frequency changes to every five years after they have been in service for 75 years.
But failure reports in the 1990s and subsequent studies by UL (formerly Underwriters Laboratories) raised concerns about the reliability of dry sprinklers. Those concerns —combined with the extra complexity, harsh environments, and greater potential for corrosion of dry sprinklers—prompted NFPA to significantly shorten dry sprinklers’ testing timeline to ensure they will function properly during a fire.
Since then, manufacturing processes have improved, and UL banned the use of dynamic O-ring water seals in fire sprinklers that were behind many abnormal operations. UL testing found that half of O-ring sealed dry sprinklers have experienced “inhibited operating characteristics” caused by the water seal assembly not releasing as intended. This usually occurs when the rubber seals are impacted by corrosion or minerals, salts, or other contaminants in the water.
The majority of dry sprinklers manufactured between the 1960s and early 2000s contain this O-ring seal, making regular sprinkler testing critically important. Between 2001 and 2007, more than 35 million sprinkler heads—one of the largest replacement programs in the history of the Consumer Product Safety Commission—were recalled and replaced at no charge after O-ring failures were linked to a deadly fire at a nursing home in 2000.
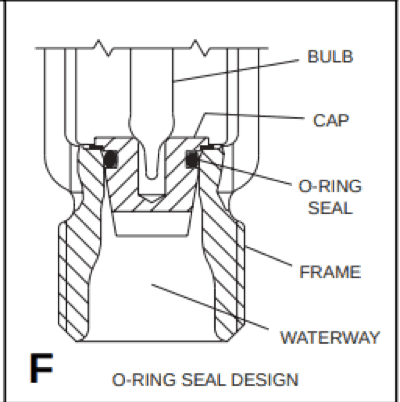
From the 2020 edition of NFPA 25
5.3.1.1.1.6* Dry sprinklers that have been installed for 15 years shall be replaced or representative samples shall be tested and then retested at 10-year intervals.
A.5.3.1.1 Sprinklers should be first given a visual inspection in accordance with 5.2.1.1.1 to determine if replacement is required. Sprinklers that have passed the visual inspection should then be laboratory tested for sensitivity and functionality. The waterway should clear when sensitivity/functionality tested at 5 psi (0.4 bar) or the minimum listed operating pressure for dry sprinklers.
5.3.1.2* A representative sample of sprinklers for testing per 5.3.1.1.1 shall consist of a minimum of not less than four sprinklers or 1 percent of the number of sprinklers per individual sprinkler sample, whichever is greater.
5.3.1.3 Where one sprinkler within a representative sample fails to meet the test requirement, all sprinklers within the area represented by that sample shall be replaced.
Typically, dry sprinkler testing is performed by submitting a random sampling of sprinklers—the greater of four sprinklers or 1 percent of the total number of sprinklers—to a plunge test. Each sprinkler is placed inside a testing apparatus that exposes it to airflow with controlled velocity and temperature. The temperature is considerably higher than the operating temperature of the sprinkler.
The inside of the sprinkler cap is hit with an air pressure of 0.5 psi (0.4 bar), and the amount of time it takes for the fusible element to melt or the glass bulb to break and activate the sprinkler is recorded. When a sprinkler fails to operate in a specified amount of time, it fails the test and all the sprinklers it represents must be replaced.
Property owners: keep records of all dry sprinkler tests
NFPA 25 requires property owners to retain documentation of all dry sprinkler testing for at least one year after the next test, so results can be compared with the current test and used to spot a pattern of deteriorating conditions. Typical records should include—but are not limited to—main drain, fire pump, and supervisory signal device tests, as well as trip tests of the dry pipe valve.
Acceptance test records—conducted after the system was designed and installed to ensure that it will perform as expected—should be retained for the life of the system or its special components (A.4.3.1). Sometimes, special in-depth reports must also be generated for building owners or authorities having jurisdiction after a test, such as after fire pump annual flow tests. Requirements for that report are discussed in part one of our previous blog on fire pump testing.
Computer programs that file test results, compare current and past results, and indicate the need for corrective maintenance and further testing can be used instead of written reports (A.4.3.1.1).
From the 2020 edition of NFPA 25
4.3 Records.
Δ 4.3.1* Records shall be made for all inspections, tests, and
maintenance of the system and its components.
N 4.3.1.1 Records shall be maintained by the property owner.
4.3.1.2* Records shall be permitted to be stored and accessed electronically.
4.3.2 Records shall indicate the following:
(1) The procedure/activity performed (e.g., inspection, test, or maintenance)
(2) The organization that performed the activity
(3) The required frequency of the activity
(4) The results and date of the activity
(5) The name and contact information of the qualified contractor or owner, including lead person for activity
4.3.4 As-built system installation drawings, hydraulic calculations, original acceptance test records, and device manufacturer’s data sheets shall be retained for the life of the system.
4.3.5 Subsequent records shall be retained for a period of 1 year after the next inspection, test, or maintenance of that type required by the standard.
Sample forms for dry sprinkler testing reports are available in the appendix of NFPA 25 or by visiting www.nfpa.org or www.nfsa.org (the National Fire Sprinkler Association’s web site). Commercial insurance carriers and authorities having jurisdiction may also provide additional testing forms.
Dry sprinkler tests are a small price to pay for automatic fire protection in freezing temperatures
The price property owners pay for automatic fire protection in freezing temperatures comes in the form of extra inspection, testing, and maintenance requirements. NFPA 25’s testing guidelines can feel onerous and complex, but they are undeniably the best way to ensure that sprinkler systems won’t fail when they’re needed most.
If you’re looking to buy components for your dry pipe sprinkler system, QRFS offers a range of dry sprinkler heads available on special order. Simply give us a call at 888.361.6662 or email support@qrfs.com and we’d be happy to help.
We also stock sprinkler gauges, valves, switches, and other accessories that are applicable in dry systems.
Check out previous installments in this dry sprinkler system series:
Guide to Dry Sprinkler Systems, Part 1: System Overview
Guide to Dry Sprinkler Systems, Part 2: Components and Installation Requirements
Guide to Dry Sprinkler Systems, Part 4: Installation of Air Compressors and Air Maintenance Devices
Guide to Dry Sprinkler Systems, Part 5: Daily, Weekly, and Monthly Inspections
Guide to Dry Sprinkler Systems, Part 6: Quarterly, Annual, and Longer Inspections
Guide to Dry Sprinkler Systems, Part 7: Fighting Corrosion
Guide to Dry Sprinkler Systems, Part 8: Daily, Weekly, and Monthly Testing
Guide to Dry Sprinkler Systems, Part 9: Quarterly and Semiannual Testing
Guide to Dry Sprinkler Systems, Part 10: Trip Testing the Dry Pipe Valve
Guide to Dry Sprinkler Systems, Part 11: Annual Dry Sprinkler Tests
Does NFPA require dry systems to be flushed and if so, what frequency and scope (just mains or you must include branch lines) what is the acceptable methods of testing?
Thank you,
Scott Edwards
Scott — there are various requirements and procedures for flushing dry sprinkler systems, particularly relating to clearing debris and obstruction investigations, and they are too in-depth to detail here. Please refer to NFPA 25 and Annex D in particular. Thanks for reading!
I live in Minnesota and our church has a dry sprinkler system that was installed in 2015. My question is do we need to test the heads after 10 years of service or 15 years of service? Please help clear up situation. Thank you.
Robert — It depends on the heads in the system, as dry sprinkler systems usually have many non-dry heads and maybe some dry heads. So, you have to figure out what specific types of sprinklers are in the system. Fortunately, even the timelines for initially testing dry heads, which your dry system may or may not have, was extended to 20 years after installation in the latest 2023 edition of NFPA 25. This blog goes over the latest testing timelines for different types of sprinklers, though be sure to check with your local authority having jurisdiction, as they may enforce an older version. Thanks for reading!