Learn about the inspection, testing, and maintenance building owners must complete to stay compliant
Many buildings have a fire department connection (FDC) that allows firefighters to pump water into the building’s fire sprinkler and standpipe systems. If you are a building owner or their designated representative, you are responsible for maintaining this life-saving equipment. And this page serves as a straightforward guide to FDCs and their inspection, testing, and maintenance (ITM).
Note that while you are responsible for FDC maintenance, performing some of these tasks requires a trained fire protection professional. And they may need to be licensed, depending on your local jurisdiction and laws.
Here’s what we cover in this blog:
- Learn about the parts of the FDC and the overall ITM requirements
- Quarterly inspection: Signs, visibility, accessibility
- Quarterly inspection: FDC caps and free of debris
- Quarterly inspection: Swivels, gaskets, and clappers
- Quarterly inspection: Check valve, automatic drain, piping
- 5-year test: Hydrostatic test of the FDC pipe
Throughout this article, we’ll refer to items in NFPA 25: Standard for the Inspection, Testing, and Maintenance of Water-Based Fire Protection Systems (2023 edition), the industry consensus standard published by the National Fire Protection Association (NFPA). We’ll also reference NFPA 13: Standard for the Installation of Sprinkler Systems (2022 edition) for additional details.
QRFS is your resource for FDC parts. Check our catalog for replacement FDC bodies, caps and plugs, identification plates, signs, and swivels with gaskets.
Click here for help finding a qualified sprinkler contractor in your area.
Parts of the FDC and ITM basics
The essential FDC components
To keep a fire department connection up to code, it’s important to know its different parts. FDCs are simple assemblies consisting of two main sections: the actual FDC outlet, located outside the building, and the interior pipe that connects to the standpipe and/or sprinkler system.
The FDC has:
- Caps or plugs to protect the insides of the pipe
- Female hose connections with swivels and gaskets
- Devices called clappers that, similar to check valves, allow water in but not out
- Signage that identifies the FDC
The interior pipe has:
- A check valve that stops water from flowing out of the system through the FDC
- An automatic drain, which prevents water from freezing in the FDC
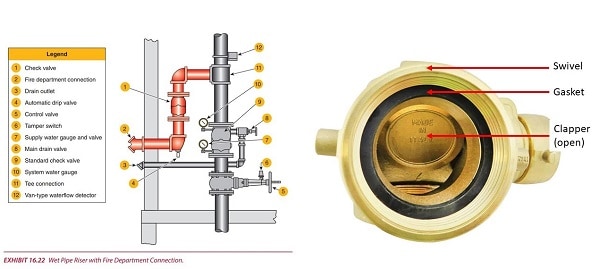
The basics of FDC inspection, testing, and maintenance
The inspection, testing, and maintenance of FDCs are pretty simple. Every quarter, you must inspect every component of the FDC to ensure that it is in place and functional and that it remains visible and accessible. Additionally, a hydrostatic test must be performed on the FDC piping every five years to verify that it can withstand the pump pressure from a fire engine.
Here’s what the standard says explicitly about these tasks and what you must inspect:
From the 2023 Edition of NFPA 25
13.8 Fire Department Connections
13.8.1 Fire department connections shall be inspected quarterly to verify the following:
(1) Fire department connections are visible and accessible
(2) Couplings or swivels are not damaged and rotate smoothly
(3) Plugs or caps are in place and undamaged
(4) Gaskets are in place
(5) Identification signs are in place
(6) Check valve is not leaking
(7) Automatic drain valve is in place and operating properly
(8) Fire department connection clapper(s) is in place and operating properly
(9)* Interior of the connection is inspected for obstructions
(10) Visible piping supplying the fire department connection is undamaged
13.8.5 The piping from the fire department connection to the fire department check valve shall be hydrostatically tested at 150 psi (10 bar) for 2 hours at least once every 5 years.
Quarterly inspection: Visibility and accessibility
As mentioned, NFPA 25 requires a quarterly inspection of the FDCs. The most basic elements of the assessment specified in section 13.8.1 are to check for visibility (including signage) and accessibility. Firefighters can’t use the FDC if they can’t find or get to it! Fortunately, it doesn’t take an expert to visually inspect whether this device is visible or accessible.
NFPA 13 lists (A.16.12.5.7) buildings, fences, posts, shrubbery, landscaping, electrical equipment, and gas lines or meters as potential obstructions. Trash, storage, dumpsters, and parked cars can also block an FDC. Anything that prevents firefighters from quickly spotting and reaching it is a violation.
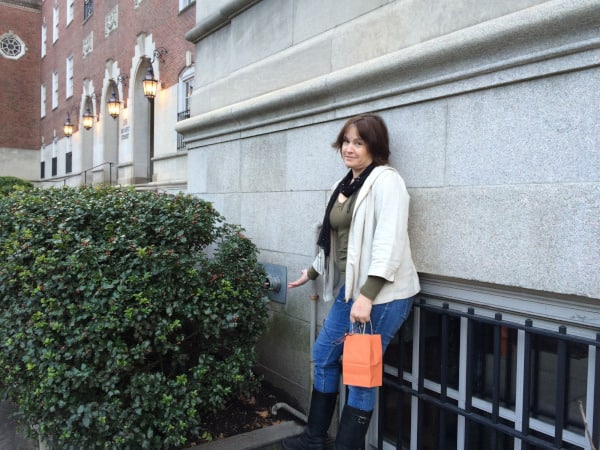
Proper signage is required to improve visibility and provide useful information about the FDC. NFPA 13 says that FDCs should have plates (16.12.5.8) fitted on the pipe with raised or engraved letters at least 1 inch in height. The plate should indicate the type of system the FDC supplies—such as “AUTOSPRK” (automatic fire sprinklers) or “STANDPIPE,” etc. (16.12.5.8).
Additionally, you’ll need a sign indicating the system’s hydraulic demand if that demand exceeds 150 PSI. Learn more about how designers calculate system demand in our previous blog.
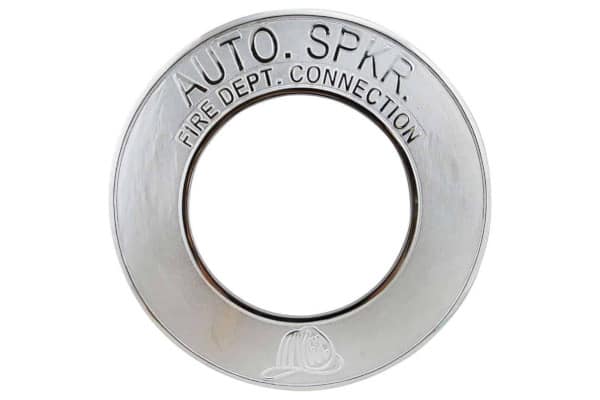
If you have missing FDC signs, make sure to replace them as soon as possible! QRFS offers a wide range of replacement FDC signs and FDC plates.
Quarterly inspection: Caps or plugs should be in place; connections should be free of debris
Every fire department connection should have protective “caps” or “plugs” over the holes where firefighters attach their hoses—two terms are sometimes used interchangeably, though plugs tend to screw in via threads. This equipment prevents dust and debris from entering the fire sprinkler system. If debris does get in, it could lodge in a pipe or an open fire sprinkler, blocking water flow.
Whether it’s because of accidents, theft, or vandalism, FDC caps and plugs can go missing—and a lost one is an infraction. If you discover a cap or plug missing, you must replace it. While inspecting the FDC, also check the connection for any debris and remove it.
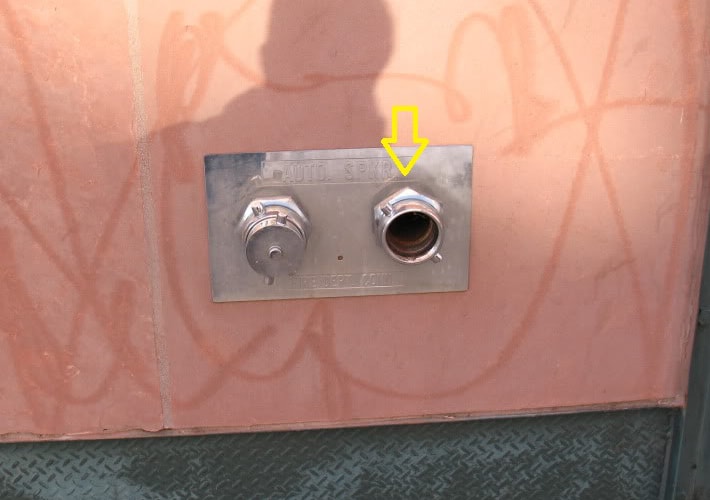
When you shop for replacement FDC caps or plugs, you’ll find three types to choose from: plug and chain models, breakable caps, and locking plugs or caps. Plus, you’ll see that FDC caps (and thus the FDC hose connection) come in different sizes. Here’s how to know which kind you need!
What type of FDC cap is right for you?
- Plug and chain models are the most common out of the three types. These threaded metal plugs screw into the FDC and are affixed with a chain that makes it harder to lose them.
- A breakable cap is made of plastic or aluminum, costs about a quarter of a plug and chain, and is designed to be quickly broken when struck by a firefighter’s tool.
- Locking plugs or caps require a key to remove them to resist theft or tampering. Inspectors may have to coordinate with the fire department to open them. Locking models also let owners inspect the interior parts of FDCs every year instead of every quarter per NFPA 25 (13.8.2).
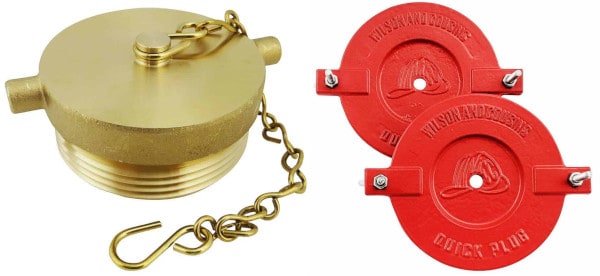
Which type do you need? Fire code leaves that question open-ended. NFPA 13 simply specifies (16.12.3.2) that each FDC has “approved plugs or caps, properly secured and arranged for easy removal by fire departments.”
However, you should check your local ordinances and with your authority having jurisdiction (AHJ). The word “approved” often means that local rules will vary. For example, contact the local fire department before switching to locking caps; they won’t be allowed unless firefighters have the keys!
Learn more about fire marshals and other AHJs, and get some tips on when to contact them.
What size FDC cap or plug (and FDC) do I need?
Fire department connections come in different-sized outlets and thus have different-sized caps, but most will be 2.5 inches (nominal). NFPA 13 says that the default FDC has 2 (“Siamese”) 2.5-inch National Hose threaded swivel fittings (16.12.3.1). However, some jurisdictions designate unique sizes (16.12.3.1.1), such as Phoenix, AZ, San Francisco, CA, and New York, NY.
Beyond the cap or plug size, if you don’t have the right size FDC, you’ll be noncompliant with code, and firefighters won’t be able to connect! Make sure you have the right equipment for your area. Here’s how to do it:
Determine what size FDC cap or plug you need with our quick guide, or get more detail on FDC size and threading with this more in-depth article. To order replacement FDC caps or plugs of various sizes and types, shop our catalog.
Quarterly inspection: The clapper and swivels should move freely; gaskets should be in place
After the caps, the next parts of the FDC to inspect are the swivel, gasket, and clapper.
Swivels should be present, rotate freely, and have a gasket in good condition
Fire department connections have female-threaded hose connections on swivels that allow a connected hose to rotate.
During the inspection, the inspector will check to see 1) if the swivel is present and 2) if it rotates smoothly and freely. If a swivel is missing or stuck, that’s a code violation, and it can be fixed by replacing the swivel. The swivel also has a black gasket that ensures a watertight connection. This must be inspected too—if the gasket is missing or damaged, replace it.
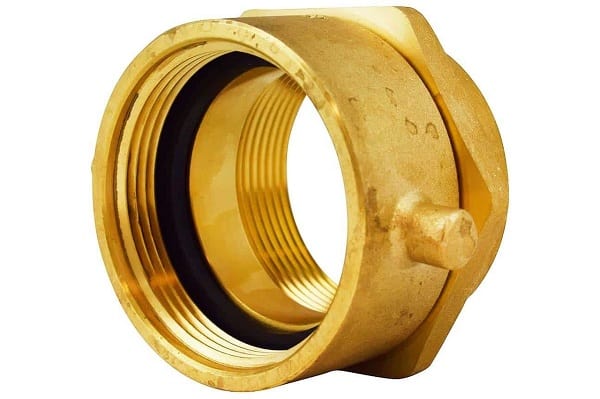
Replacing a damaged or lost swivel is relatively simple. This article will help you select a properly sized swivel and guide you through the replacement.
For replacement swivels and gaskets, check out our catalog.
Clappers should be undamaged and functional
Inside each fire department connection, you’ll find a little spring-loaded door blocking the orifice. This is the clapper. Similar to check valves, clappers are one-way flow devices. The clapper opens when pressure is applied to it, allowing water to enter the FDC. But when pressure and water come from the wrong side of the clapper, it ‘claps’ shut.
This function is necessary because most FDCs have a Siamese connection where two hose connections lead to one supply pipe (NFPA 13: 16.12.3.1). That said, some FDCs in larger buildings have three or more hose connections, whereas only one connection is permitted when the FDC is “piped to a 3 in. (80 mm) or smaller riser (16.12.3.1.3).” The clappers keep water from flowing out of unused connections so that firefighters can employ one or more hoses at a time.
During the inspection, make sure that the clappers open and shut correctly. You should be able to open the clapper by pushing it, and it should automatically close when you release it. If the clappers are broken or missing, they’ll need to be replaced.
Quarterly inspection: Pipe, drain, and check valves should be functional and undamaged
Until now, every part of the quarterly FDC inspection has focused on the most visible parts of the FDC. But NFPA 25 also requires some less-obvious components to be inspected. These items include the FDC supply piping, the FDC check valve, and the automatic drain (if present).
FDC supply pipe should be free from damage and loads
The FDC is connected to the main sprinkler or standpipe system by a length of pipe, and some of it will be in the wall or underground. NFPA 25 doesn’t require or expect a building owner to examine all of this hidden pipe. But any above-ground, accessible pipe must be looked at, and these requirements apply to sections of pipe applicable to sprinkler and standpipe systems.
During the inspection, a qualified building owner or ITM professional checks the pipe for mechanical damage, corrosion, leaks, damaged control valves, missing or damaged support devices, and damaged supervisory signal initiating devices. (NFPA 25: 5.2.2.1 and 6.2.4.1). A professional fire protection contractor must make repairs if you find these issues. Additionally, NFPA 25 states that nothing—no matter how heavy or light—may be hung from or placed on any fire sprinkler pipe, including the FDC pipe (5.2.2.2).
Besides the timing, the quarterly inspection of FDC piping is not substantially different from the annual inspection of sprinkler system piping.
The FDC check valve shouldn’t leak
Positioned between the FDC and the main riser, the FDC check valve keeps water from flowing out of the system. When enough pressure is applied to the check valve from the FDC inlets—such as via a fire department pump truck—the valve opens to let water into the system.
The check valve should be inspected for leaks every quarter. You’ll know it is leaking if water comes out of the FDC when you remove the cap and test the clappers or if water is dripping from the automatic drain.
For more information about check valves, turn to our article on the different roles they play in fire protection. Also, learn about the difference between check valves and backflow preventers.
For replacement parts, check out our check valve catalog. Note that a trained and licensed fire protection professional is needed to replace a check valve.
The automatic drain should be in place and functional
The last quarterly item is inspecting the FDC’s automatic drain if one is required and present. Systems subject to freezing must have an automatic drain valve, also called a ball drip, at the lowest point of the FDC so that any water left in the system will safely drain out instead of freezing. A qualified inspector will verify that the drain valve is in place and functioning correctly.
For replacement ball drip valves, shop our catalog.
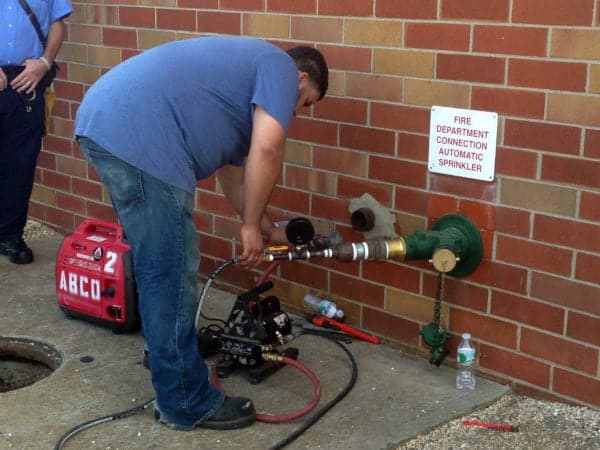
Every 5 years: A hydrostatic test of the FDC pipe
NFPA 25 specifies that the FDC pipe must be hydrostatically tested every five years. A hydrostatic test simulates the water pressure from a fire department’s pump truck. If the system maintains its integrity during the test and doesn’t leak, it passes. An ITM professional or other well-qualified individual must carry out this work.
NFPA 25 specifies (13.8.5) that the pipe between the FDC’s hose connections and the check valve should be hydrostatically tested at 150 PSI for 2 hours at least once every 5 years.
To perform this test, an ITM professional will connect a hydrostatic test pump to the FDC and a fire hydrant. This pump raises the system pressure to 150 PSI, and the individual holds it at this level for two hours while monitoring pressure closely. If the system experiences pressure drops — or leaks or damage are otherwise visible — the piping fails the test.
Check out our article on hydrostatic testing for more details. Note that the FDC test is distinct from the hydrostatic test required for a sprinkler system. The sprinkler system test, which also occurs every 5 years, has a minimum pressure of 200 psi per NFPA 25 6.3.2.1. These tests are conducted separately and the length of pipe should be isolated from the rest of the system before the test.
Maintaining your FDC is important!
Keeping fire protection systems and FDCs up to code can seem complicated, but it’s crucial to maintaining a safe building. And fortunately, NFPA 25’s requirements for inspecting, testing, and maintaining an FDC are pretty straightforward.
Every quarter, inspect each component of the FDC to verify that it’s in place and working. Often these quarterly inspections are done by a fire protection pro and are part of an annual or semi-annual visit. Replace any items that are missing or damaged. And every five years, have a professional perform a hydrostatic test on the FDC piping.
QRFS is your resource for FDC parts. Check our catalog for replacement FDC bodies, caps and plugs, identification plates, signs, and swivels with gaskets.
Click here for help finding a qualified sprinkler contractor in your area.
If you have any questions—or need help finding any FDC or part—give us a call at (888) 361-6662 or email support@qrfs.com.
This blog was originally posted at blog.qrfs.com. If this article helped you, check us out at Facebook.com/QuickResponseFireSupply or on Twitter @QuickResponseFS.
I really appreciate this Blog Topic and all the information and NFPA-25 code references that were compiled here about the Required ITM of Fire Department Connections.
I am a NC State Licensed Fire Sprinkler Inspection Contractor, and this was very useful and informative. I shared it with all of the Inspections/Service Techs. that work for our company. I’d really appreciate more articles about other NFPA-25 related Inspections/Services for Systems and Components such as Standpipes, Private Fire Service Mains (Hydrants), Fire Pumps, etc.
Thank you, Edward!
If I have locking caps on my FDC (Knox) how do I perform the required maintenance, since they are only accessible by the fire dept key?
Morgan — qualified fire protection contractors should also have access to keys that enable them to do necessary work, such as access inlets to inspect them — or they can conduct maintenance in conjunction with the local FD.
You can still conduct quarterly function checks to make sure the couplings are spinning freely along with other visual inspections however, yes the hydrostatic tests, etc. need to be done by a third party since they are KNOX key holders.
Nice Article! Thanks.
Thanks, Ver!
Is any other sprinkler contractors experiencing issues with not being able to flip the FDC check valve for the hydro test. This has become more frequent with our newer customers. They typically have sprinkler systems dating back to the 70′ and 80’s. The FDC check valve is flanged and depending on the age and condition we typically don’t flip the check valve. This is in fear of not being able to get the check valve reinstalled or possibly causing a leak at the flange. Were normally left with recommending the customer to replace/upgrade the existing FDC check valves. Will perform the hydro test prior to the replacement. Does anyone have any recommendations. Thank you.
Aaron — We haven’t heard of this issue, but perhaps other readers may chime in here. Thanks for reading!
Even though the FDC signage is visible,should the apartment building store garbage receptacles and a dumpster in front of the pipes?
Jeffrey — The NFPA rules and other codes mandate FDCs must not only be visible but easily accessible. So, if an apartment building stores stuff in front of or near it, that is a no-no. Firefighters need a clear path the get to the FDC and hook up their hoses. Thanks for reading!
Thank you!!!! Needed this!
You’re welcome!
Can an air test be performed on an FDC for automatic fire sprinkler system which is designed to insure that there
is no leakage from the FDC to the check valve? Air test performed at 25 psi for 15 minutes.
Is this a proper test? If the pressure holds accordingly; then that will insure that there is no leakage from the
swivel inlet area to the check valve.
Les — Hydrostatic tests that pump pressurized water into this pipe section and look for leakage are required at system acceptance, major system revisions, and every 5 years in specific systems (See Chapter 29 of NFPA 13 (2022) and Chapter 6 of NFPA 25 (2023)). We are not aware of any approved “air test.” Thanks for reading.
I am tring to find a bleeder valve box to set around the FDC for the City of Hillsboro, Oregon.
I cannot find anything to match my blue prints and supply house has no idea.
It is a box that surrounds the bottom of the FDC 90 with bleeder valve under 90, the inspecter needs clear view of bleeder valve so that is what the box is for a clear view of 90 and bleeder.
Has anybody dealt with this issue or know where to buy valve box?
Holding up my job and my dirt guys have never dealt with this.
My engineer also has no idea.
Steve — When you reference “bleeder valve,” we think you are referring to the ball-drip valve that sits below an FDC. Unfortunately, we aren’t familiar with a request for a “valve box” in this context. Can you ask whomever created the blueprints/request for clarification?